Die Wärmebehandlung von Metallen ist ein weit verbreitetes Verfahren zur Verbesserung der mechanischen Eigenschaften wie Härte, Festigkeit und Zähigkeit.Sie ist jedoch mit mehreren Nachteilen verbunden, die sich auf die Leistung, die Kosten und die Eignung des Materials für die Anwendung auswirken können.Zu diesen Nachteilen gehören mögliche Verformungen oder Verwerfungen, Eigenspannungen, geringere Duktilität, erhöhte Sprödigkeit und höhere Kosten für Energieverbrauch und Ausrüstung.Außerdem kann eine unsachgemäße Wärmebehandlung zu uneinheitlichen Ergebnissen führen, so dass eine sorgfältige Kontrolle des Prozesses unerlässlich ist.Im Folgenden gehen wir auf diese Nachteile im Detail ein, um ein umfassendes Verständnis für die mit der Wärmebehandlung verbundenen Herausforderungen zu vermitteln.
Die wichtigsten Punkte erklärt:
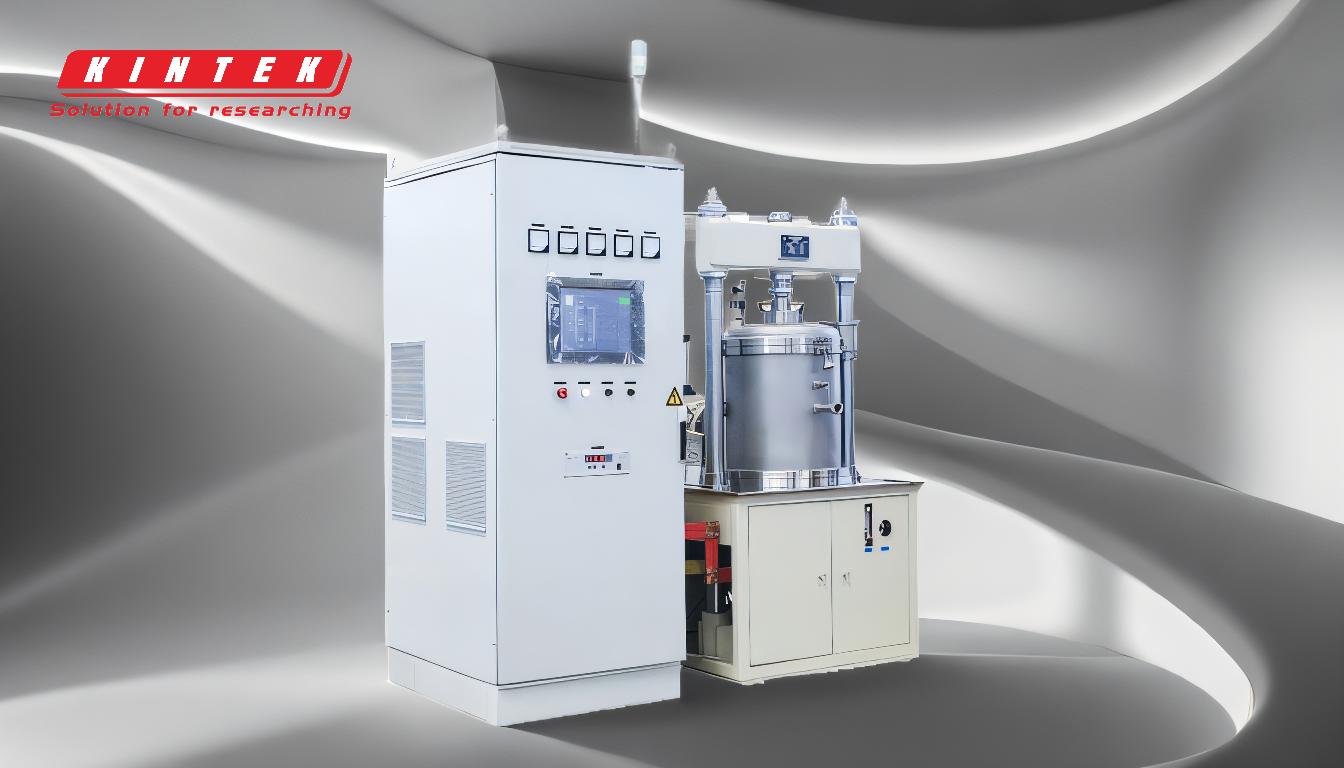
-
Verformung und Verziehen
- Während der Wärmebehandlung unterliegen Metalle erheblichen Temperaturschwankungen, die eine ungleichmäßige Ausdehnung und Kontraktion verursachen können.Dies führt häufig zu einer Verformung oder einem Verziehen des Materials.
- Dünne oder komplex geformte Bauteile sind für diese Probleme besonders anfällig, da ihnen die strukturelle Integrität fehlt, um thermischen Spannungen standzuhalten.
- Verformungen können Teile unbrauchbar machen, so dass zusätzliche Bearbeitungen oder sogar die Verschrottung erforderlich werden, was Kosten und Ausschuss erhöht.
-
Eigenspannungen
- Eine schnelle Abkühlung, wie z. B. das Abschrecken, kann zu Eigenspannungen im Metall führen.Diese Spannungen entstehen, weil die äußeren Schichten schneller abkühlen als die inneren, wodurch innere Spannungen entstehen.
- Eigenspannungen können die strukturelle Integrität des Materials beeinträchtigen und zu einem vorzeitigen Versagen unter Last oder während des Betriebs führen.
- Um dieses Problem zu entschärfen, sind unter Umständen Entspannungsbehandlungen erforderlich, die den Prozess um zusätzliche Schritte und Kosten erweitern.
-
Verminderte Duktilität und erhöhte Sprödigkeit
- Eine Wärmebehandlung kann zwar die Härte und Festigkeit erhöhen, verringert aber häufig die Duktilität und macht das Material spröder.
- Spröde Werkstoffe neigen bei Stößen oder Belastungen zu Rissen oder Brüchen, was ihre Eignung für Anwendungen, die Zähigkeit erfordern, einschränkt.
- Wird beispielsweise ein Stahlbauteil zu stark gehärtet, kann es zu spröde für den Einsatz in stark beanspruchten Umgebungen wie der Automobil- oder Luftfahrtindustrie werden.
-
Energieverbrauch und Umweltauswirkungen
- Wärmebehandlungsverfahren wie Glühen, Abschrecken und Anlassen erfordern einen erheblichen Energieaufwand, um hohe Temperaturen zu erreichen und zu halten.
- Dieser hohe Energieverbrauch trägt zu höheren Betriebskosten und einer größeren CO2-Bilanz bei, wodurch die Wärmebehandlung weniger umweltfreundlich ist.
- Die Industrie sucht zunehmend nach alternativen Methoden zur Verringerung des Energieverbrauchs und der Umweltbelastung.
-
Kosten für Ausrüstung und Wartung
- Für die Wärmebehandlung sind spezielle Anlagen wie Öfen, Abschreckbecken und Anlassöfen erforderlich, deren Anschaffung und Wartung teuer sein kann.
- Um gleichbleibende Ergebnisse zu gewährleisten, ist eine regelmäßige Wartung erforderlich, was die Gesamtkosten des Prozesses erhöht.
- Für kleine Hersteller kann es schwierig sein, die Investition in eine solche Ausrüstung zu rechtfertigen.
-
Uneinheitliche Ergebnisse durch unsachgemäße Kontrolle
- Die Wärmebehandlung ist ein hochsensibler Prozess, der eine präzise Steuerung von Temperatur, Abkühlgeschwindigkeit und Zeit erfordert.
- Schwankungen bei diesen Parametern können zu uneinheitlichen Ergebnissen führen, z. B. zu ungleichmäßiger Härte oder unvollständiger Umwandlung des Gefüges.
- Um zuverlässige Ergebnisse zu erzielen, sind geschulte Bediener und fortschrittliche Überwachungssysteme erforderlich, was die Kosten weiter erhöht.
-
Materialspezifische Beschränkungen
- Nicht alle Metalle sprechen gut auf eine Wärmebehandlung an.Einige Legierungen erreichen beispielsweise nicht die gewünschten Eigenschaften oder erfordern extrem spezielle Bedingungen.
- Bestimmte Werkstoffe wie Aluminium oder Titan haben besondere Anforderungen an die Wärmebehandlung, die den Prozess komplizieren und seine Wirksamkeit einschränken können.
- Dies schränkt die Vielseitigkeit der Wärmebehandlung als universelle Lösung zur Verbesserung der Metalleigenschaften ein.
-
Möglichkeit der Oberflächenoxidation und Entkohlung
- Bei hohen Temperaturen kann es zu einer Oberflächenoxidation kommen, die zur Bildung von Zunder oder Oxidschichten auf dem Metall führt.
- Entkohlung, also der Verlust von Kohlenstoff an der Stahloberfläche, kann während der Wärmebehandlung auftreten und die Oberflächenhärte und -festigkeit verringern.
- Um die gewünschten Oberflächeneigenschaften wiederherzustellen, sind oft zusätzliche Nachbearbeitungsprozesse wie Schleifen oder Beschichten erforderlich.
-
Zeitaufwändiger Prozess
- Die Wärmebehandlung ist kein schneller Prozess.Je nach Art der Behandlung und des Materials kann es Stunden oder sogar Tage dauern, bis sie abgeschlossen ist.
- Diese längere Bearbeitungszeit kann Produktionspläne verzögern und die Vorlaufzeiten verlängern, was sich auf die Gesamteffizienz auswirkt.
- Für Branchen, die eine schnelle Bearbeitung benötigen, sind alternative Methoden möglicherweise besser geeignet.
-
Gesundheits- und Sicherheitsrisiken
- Bei der Wärmebehandlung wird mit hohen Temperaturen, brennbaren Materialien (z. B. Abschreckölen) und potenziell gefährlichen Gasen gearbeitet.
- Die Bediener müssen strenge Sicherheitsprotokolle befolgen, um Unfälle wie Verbrennungen, Brände oder den Kontakt mit giftigen Dämpfen zu vermeiden.
- Die Gewährleistung einer sicheren Arbeitsumgebung erhöht die Komplexität und die Kosten des Prozesses.
Wenn Hersteller und Ingenieure diese Nachteile kennen, können sie fundierte Entscheidungen darüber treffen, ob die Wärmebehandlung die richtige Wahl für ihre spezifische Anwendung ist.Sie bietet zwar erhebliche Vorteile, doch müssen die mit dem Verfahren verbundenen Herausforderungen sorgfältig gegen die gewünschten Ergebnisse abgewogen werden.
Zusammenfassende Tabelle:
Benachteiligung | Wesentliche Auswirkungen |
---|---|
Verformung und Verwerfung | Ungleichmäßige Expansion/Kontraktion, insbesondere bei dünnen oder komplexen Teilen. |
Eigenspannungen | Innere Spannungen durch schnelle Abkühlung, die zu vorzeitigem Versagen führen. |
Verminderte Duktilität | Erhöhte Sprödigkeit, wodurch die Materialien anfällig für Risse werden. |
Verbrauch von Energie | Ein hoher Energieverbrauch erhöht die Kosten und die Umweltbelastung. |
Kosten der Ausrüstung | Teure Öfen, Abschreckbehälter und Wartung. |
Inkonsistente Ergebnisse | Eine unsachgemäße Kontrolle führt zu ungleichmäßiger Härte oder unvollständigen Umwandlungen. |
Werkstoffspezifische Beschränkungen | Nicht alle Metalle sprechen gut auf eine Wärmebehandlung an. |
Oxidation der Oberfläche | Zunderbildung und Entkohlung verringern die Oberflächenhärte. |
Zeitaufwendig | Lange Bearbeitungszeiten verzögern die Produktionspläne. |
Gesundheits- und Sicherheitsrisiken | Hohe Temperaturen, brennbare Materialien und gefährliche Gase bergen Risiken. |
Brauchen Sie Hilfe bei der Entscheidung, ob eine Wärmebehandlung für Ihre Anwendung geeignet ist? Kontaktieren Sie noch heute unsere Experten für eine maßgeschneiderte Beratung!