Die Sprühpyrolyse ist zwar eine vielseitige und weit verbreitete Technik zur Herstellung von feinen Pulvern und dünnen Filmen, hat jedoch mehrere Nachteile, die ihre Anwendung und Effizienz einschränken können.Zu diesen Nachteilen gehören hohe Betriebs- und Investitionskosten, technische Herausforderungen im Zusammenhang mit der Wärmeübertragung und der Reaktorkonstruktion, die Erzeugung schädlicher Nebenprodukte und Schwierigkeiten bei der Skalierung der Technologie für reale Anwendungen.Darüber hinaus erfordert das Verfahren häufig ausgeklügelte Überwachungs- und Luftreinigungssysteme, um die Umweltvorschriften zu erfüllen, was die Komplexität und die Kosten weiter erhöht.Im Folgenden gehen wir auf diese Nachteile im Detail ein.
Die wichtigsten Punkte werden erklärt:
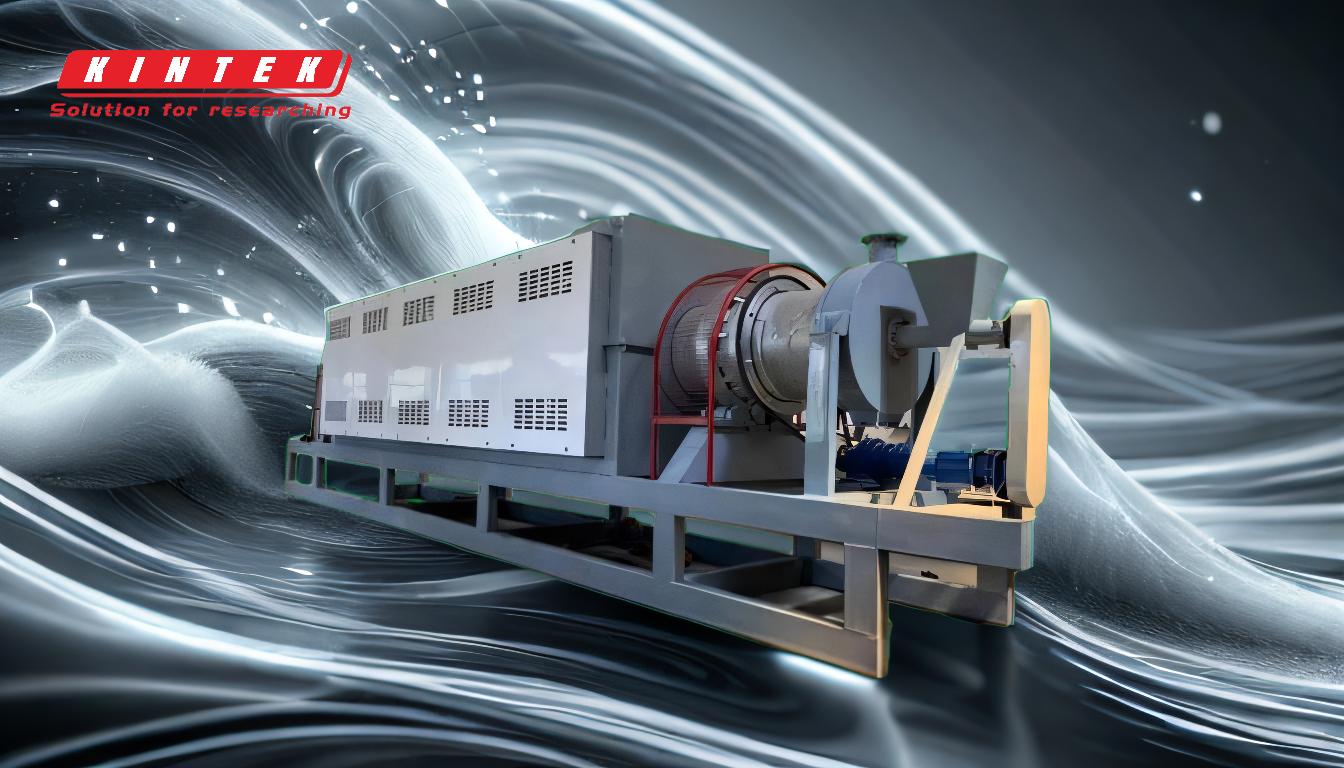
-
Hohe Betriebs- und Investitionskosten:
- Die Sprühpyrolyse erfordert komplexe Anlagen und Verfahren, deren Einrichtung und Wartung teuer sein kann.Der Bedarf an hochreinen Ausgangsstoffen, präzisen Kontrollsystemen und energieintensiven Heizmechanismen trägt zu den Gesamtkosten bei.
- Das Verfahren erfordert häufig eine Luftreinigungsanlage zur Behandlung der Rauchgase, was die Betriebskosten weiter in die Höhe treibt.Die Einhaltung von Umweltvorschriften, z. B. der EU-Luftreinhaltungsnormen, kann die Kosten weiter in die Höhe treiben, da fortschrittliche Rauchgasreinigungssysteme erforderlich sind.
-
Technische Herausforderungen bei der Wärmeübertragung und Reaktorkonstruktion:
- Bei der Sprühpyrolyse ist es eine große Herausforderung, eine effiziente Wärmeübertragung in feste Biomassepartikel zu erreichen.Das Verfahren erfordert oft hohe Heizraten, die nur schwer konstant erreicht werden können.
- Die Reaktorkonstruktion muss optimiert werden, um eine gleichmäßige Wärmeverteilung zu gewährleisten und heiße Stellen oder kalte Zonen zu vermeiden, die zu unvollständiger Pyrolyse oder ungleichmäßiger Produktqualität führen können.Dies kann die Verwendung fester Wärmeträger, heißer Gasströme oder eines indirekten Wärmeaustauschs über Reaktorwände oder eingebaute Rohre/Platten beinhalten.
-
Produktion von schädlichen Nebenprodukten:
- Bei der thermischen Zersetzung von Materialien während der Sprühpyrolyse können schädliche Chemikalien und unerwünschte Nebenprodukte entstehen.Diese Stoffe müssen aus dem Rauchgas entfernt werden, um die Umweltvorschriften einzuhalten, was den Prozess zusätzlich kompliziert macht.
- Die entstehende Asche enthält oft einen hohen Anteil an Schwermetallen und wird als gefährlicher Abfall eingestuft, der ordnungsgemäß entsorgt werden muss.Dies erhöht nicht nur die Betriebskosten, sondern birgt auch Umwelt- und Sicherheitsrisiken.
-
Variabilität der Futtermittel-Ausgangserzeugnisse:
- Die Leistung der Sprühpyrolyse kann in hohem Maße von der Qualität und Konsistenz des Ausgangsmaterials abhängen.Schwankungen im Ausgangsmaterial, z. B. in Bezug auf Feuchtigkeitsgehalt, Partikelgröße und chemische Zusammensetzung, können zu einer uneinheitlichen Produktqualität und zu Ineffizienzen im Prozess führen.
- Um diese Schwankungen auszugleichen, sind oft ausgeklügelte Überwachungs- und automatische Anpassungssysteme erforderlich, was die Komplexität und die Kosten des Prozesses weiter erhöht.
-
Schwierigkeiten bei der Skalierung für Anwendungen in der realen Welt:
- Während die Sprühpyrolyse im Labor- und Pilotmaßstab erfolgreich demonstriert wurde, bleibt die Skalierung der Technologie für industrielle Anwendungen eine große Herausforderung.Faktoren wie Reaktorkonstruktion, Wärmeübertragungseffizienz und Rohstofflogistik werden in größerem Maßstab immer komplexer.
- Die Variabilität der realen Ausgangsmaterialien und die Notwendigkeit robuster, skalierbarer Systeme haben die weltweite Verbreitung und Zuverlässigkeit der Sprühpyrolyse für großtechnische Anwendungen eingeschränkt.
-
Ökologische und regulatorische Herausforderungen:
- Die Erzeugung schädlicher Nebenprodukte und die Notwendigkeit einer Rauchgasbehandlung machen die Sprühpyrolyse zu einem technisch anspruchsvollen Verfahren.Die Einhaltung strenger Umweltvorschriften, z. B. zur Luftqualität und Abfallentsorgung, kann sowohl schwierig als auch kostspielig sein.
- Die Entsorgung gefährlicher Abfälle, wie schwermetallhaltiger Asche, erfordert eine spezielle Handhabung und Behandlung, was den betrieblichen Aufwand weiter erhöht.
Zusammenfassend lässt sich sagen, dass die Sprühpyrolyse zwar eine Reihe von Vorteilen bietet, wie z. B. die Möglichkeit, feine Pulver und dünne Filme mit kontrollierten Eigenschaften herzustellen, dass aber auch ihre Nachteile - wie hohe Kosten, technische Herausforderungen, schädliche Nebenprodukte und Probleme bei der Skalierbarkeit - sorgfältig berücksichtigt werden müssen.Diese Faktoren können die Anwendbarkeit in bestimmten Kontexten einschränken und erfordern kontinuierliche Forschung und Entwicklung, um diese Herausforderungen zu überwinden.
Zusammenfassende Tabelle:
Benachteiligung | Wichtige Details |
---|---|
Hohe Betriebs- und Investitionskosten | Komplexe Ausrüstung, hochreine Ausgangsstoffe und Luftreinigung erhöhen die Kosten. |
Technische Herausforderungen | Ineffiziente Wärmeübertragung und komplizierte Reaktorkonstruktion. |
Schädliche Nebenprodukte | Erzeugt schädliche Chemikalien und schwermetallhaltige Asche. |
Variabilität der Ausgangsstoffe | Eine uneinheitliche Qualität der Ausgangsstoffe beeinträchtigt die Einheitlichkeit des Produkts. |
Schwierigkeiten bei der Skalierung | Herausforderungen beim Reaktordesign und der Rohstofflogistik im industriellen Maßstab. |
Umwelt- und Regulierungsfragen | Die Einhaltung strenger Vorschriften erhöht die Komplexität und die Kosten. |
Benötigen Sie Hilfe bei der Bewältigung der Herausforderungen der Sprühpyrolyse? Kontaktieren Sie noch heute unsere Experten für maßgeschneiderte Lösungen!