Die Wahl der Frequenz bei der induktiven Erwärmung wird von mehreren Schlüsselfaktoren beeinflusst, darunter die Materialeigenschaften, die Größe und Dicke des Werkstücks, die gewünschte Erwärmungstiefe, der Wirkungsgrad und die spezifischen Anwendungsanforderungen.Höhere Frequenzen eignen sich für kleinere, dünnere Materialien und geringe Erwärmungstiefen, während niedrigere Frequenzen besser für größere, dickere Materialien geeignet sind, die eine tiefere Erwärmung erfordern.Der Materialwiderstand, die Stromversorgungskapazität und das Design der Induktoren spielen ebenfalls eine entscheidende Rolle.Darüber hinaus müssen Kostenerwägungen und Prozessanforderungen, wie z. B. die Notwendigkeit von Rühreffekten oder Rauschunterdrückung, berücksichtigt werden, um die Leistung und Kosteneffizienz des Systems zu optimieren.
Die wichtigsten Punkte erklärt:
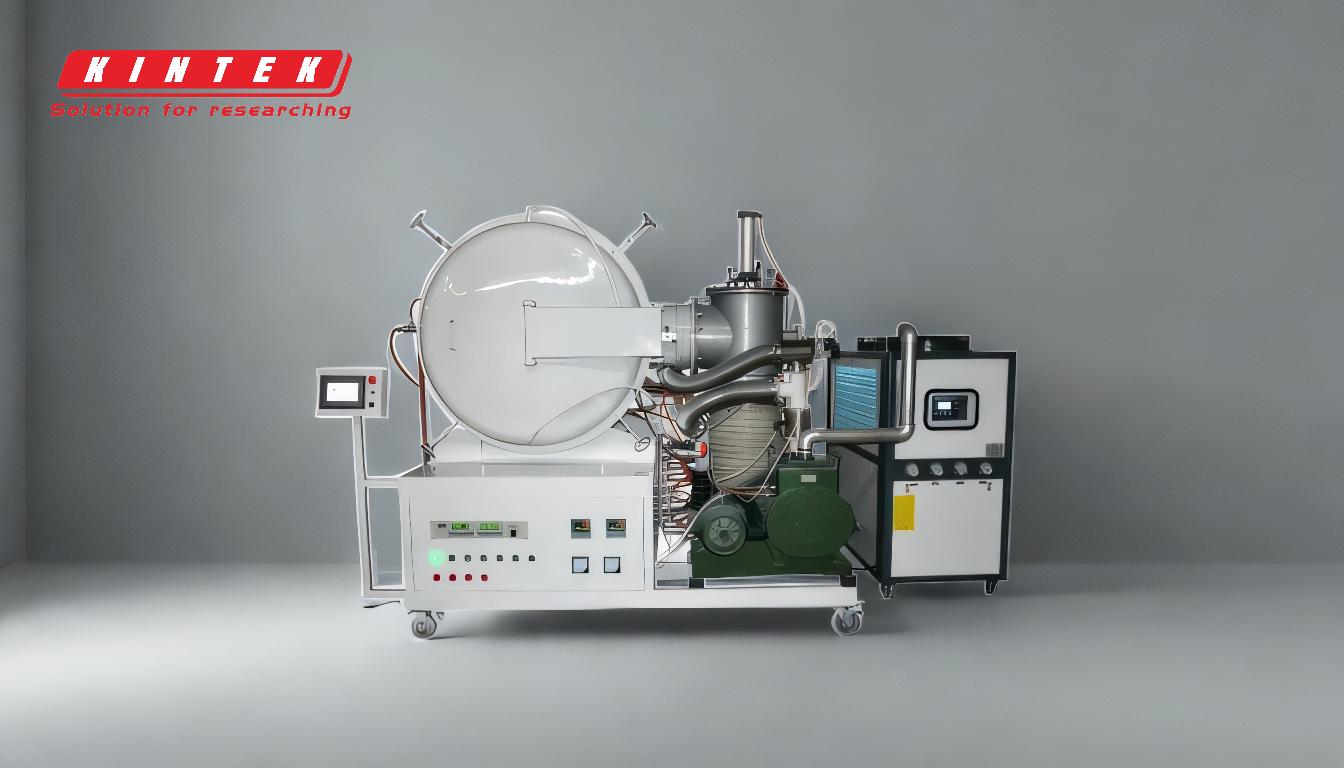
-
Materialeigenschaften:
- Art des Materials:Die Induktionserwärmung wird in der Regel für Metalle und leitende Materialien verwendet.Die Wahl der Frequenz hängt vom spezifischen Widerstand und den magnetischen Eigenschaften des Materials ab.Materialien mit höherem Widerstand erwärmen sich schneller und erfordern möglicherweise niedrigere Frequenzen.
- Widerstandswert:Materialien mit höherem Widerstand erzeugen mehr Wärme, wenn sie mit Wechselstrom beaufschlagt werden, was sich auf die Wahl der Frequenz auswirkt.
-
Größe und Dicke des Werkstücks:
- Kleine und dünne Materialien:Diese erhitzen sich schneller und sind besser für höhere Frequenzen geeignet, die eine geringere Erhitzungstiefe bieten.
- Große und dicke Materialien:Diese benötigen niedrigere Frequenzen, um eine tiefere Wärmedurchdringung zu erreichen.
-
Gewünschte Erwärmungstiefe:
- Höhere Frequenzen:Geringere Erwärmungstiefe, daher ideal für Oberflächenerwärmung oder dünne Materialien.
- Niedrigere Frequenzen:Bietet eine tiefere Wärmedurchdringung, geeignet für dickere Materialien oder Anwendungen, die eine gleichmäßige Erwärmung des gesamten Werkstücks erfordern.
-
Wirkungsgrad und Stromversorgungskapazität:
- Wirkungsgrad:Der Wirkungsgrad des Induktionserwärmungssystems hängt von der Frequenz, den Materialeigenschaften und der Konstruktion des Induktors ab.Höhere Frequenzen können für bestimmte Anwendungen einen besseren Wirkungsgrad bieten.
- Kapazität der Stromversorgung:Die Stromversorgung muss die spezifische Wärme des Materials, seine Masse, den erforderlichen Temperaturanstieg und den Wärmeverlust berücksichtigen.Bei größeren Temperaturschwankungen kann eine höhere Leistung erforderlich sein.
-
Induktor-Design:
- Spulen- und Kondensatorkonfiguration:Das Design der Induktionsspule und des Kompensationskondensators kann angepasst werden, um die Frequenz für bestimmte Anwendungen zu optimieren, z. B. um einen gewünschten Rühreffekt zu erzielen oder das Arbeitsgeräusch zu reduzieren.
-
Anwendungsspezifische Anforderungen:
- Rührender Effekt:Bestimmte Anwendungen, wie z. B. das Induktionsschmelzen, können bestimmte Frequenzen erfordern, um den gewünschten Rühreffekt im geschmolzenen Material zu erzielen.
- Geräuschreduzierung:Niedrigere Frequenzen können gewählt werden, um die Arbeitsgeräusche in bestimmten Umgebungen zu reduzieren.
-
Kostenüberlegungen:
- Anschaffungskosten:Bei der Auswahl des Frequenzbandes sollte das Budget des Kunden berücksichtigt werden.Hochfrequenzgeräte mit niedriger Leistung und Ultra-Audio-Geräte mit höherer Leistung können ähnliche Erwärmungseffekte für bestimmte Werkstücke bieten, allerdings zu unterschiedlichen Kosten.
- Betriebskosten:Die Betriebseffizienz und der Energieverbrauch des Systems sollten gegen die Anschaffungskosten abgewogen werden.
-
Anforderungen an den Prozess:
- Temperaturschwankungen:Der Grad der für die Anwendung erforderlichen Temperaturschwankungen beeinflusst die Wahl der Frequenz.Um größere Temperaturbereiche zu erreichen, kann mehr Leistung eingesetzt werden.
- Wärmeverlust:Faktoren wie Wärmeleitung, Konvektion und Strahlung müssen berücksichtigt werden, um den Wärmeverlust zu minimieren und den Erwärmungsprozess zu optimieren.
Durch eine sorgfältige Bewertung dieser Faktoren kann man die am besten geeignete Frequenz für ein Induktionserwärmungssystem auswählen und so eine optimale Leistung, Effizienz und Kosteneffizienz für die jeweilige Anwendung sicherstellen.
Zusammenfassende Tabelle:
Faktor | Beschreibung |
---|---|
Materialeigenschaften | Widerstand und magnetische Eigenschaften bestimmen die Frequenzwahl. |
Größe/Stärke des Werkstücks | Bei kleineren, dünneren Materialien werden höhere Frequenzen verwendet, bei größeren, dickeren Materialien niedrigere. |
Erhitzungstiefe | Höhere Frequenzen für eine flache Erwärmung; niedrigere Frequenzen für eine tiefere Durchdringung. |
Wirkungsgrad | Die Frequenz beeinflusst die Systemeffizienz je nach Material und Induktionsdesign. |
Induktor-Design | Spulen- und Kondensatorkonfigurationen optimieren die Frequenz für bestimmte Anwendungen. |
Anforderungen an die Anwendung | Rütteleffekte, Geräuschreduzierung und Temperaturschwankungen beeinflussen die Frequenz. |
Kostenüberlegungen | Bringen Sie die Anschaffungs- und Betriebskosten mit den Leistungsanforderungen ins Gleichgewicht. |
Benötigen Sie Hilfe bei der Auswahl der richtigen Frequenz für Ihr Induktionserwärmungssystem? Kontaktieren Sie noch heute unsere Experten für maßgeschneiderte Lösungen!