Die Abscheidung dünner Schichten ist ein wichtiger Prozess in der Materialwissenschaft und -technik, mit dem dünne Materialschichten auf einem Substrat erzeugt werden.Die Techniken für die Dünnschichtabscheidung lassen sich grob in zwei Haupttypen einteilen: Physikalische Gasphasenabscheidung (PVD) und Chemische Gasphasenabscheidung (CVD) .Diese Verfahren werden in verschiedene Untertechniken unterteilt, die jeweils eigene Mechanismen und Anwendungen haben.Bei PVD-Verfahren wird das Material physikalisch von einer Quelle auf ein Substrat übertragen, in der Regel in einer Vakuumumgebung, während CVD-Verfahren auf chemischen Reaktionen beruhen, um das Material auf das Substrat aufzubringen.Darüber hinaus gibt es andere Verfahren wie Atomlagenabscheidung (ALD) , Sprüh-Pyrolyse und Spin-Beschichtung bieten spezielle Verfahren zur präzisen Kontrolle von Schichtdicke und Eigenschaften.Das Verständnis dieser Techniken ist für die Auswahl der geeigneten Methode auf der Grundlage der gewünschten Filmeigenschaften und der Anwendungsanforderungen unerlässlich.
Die wichtigsten Punkte werden erklärt:
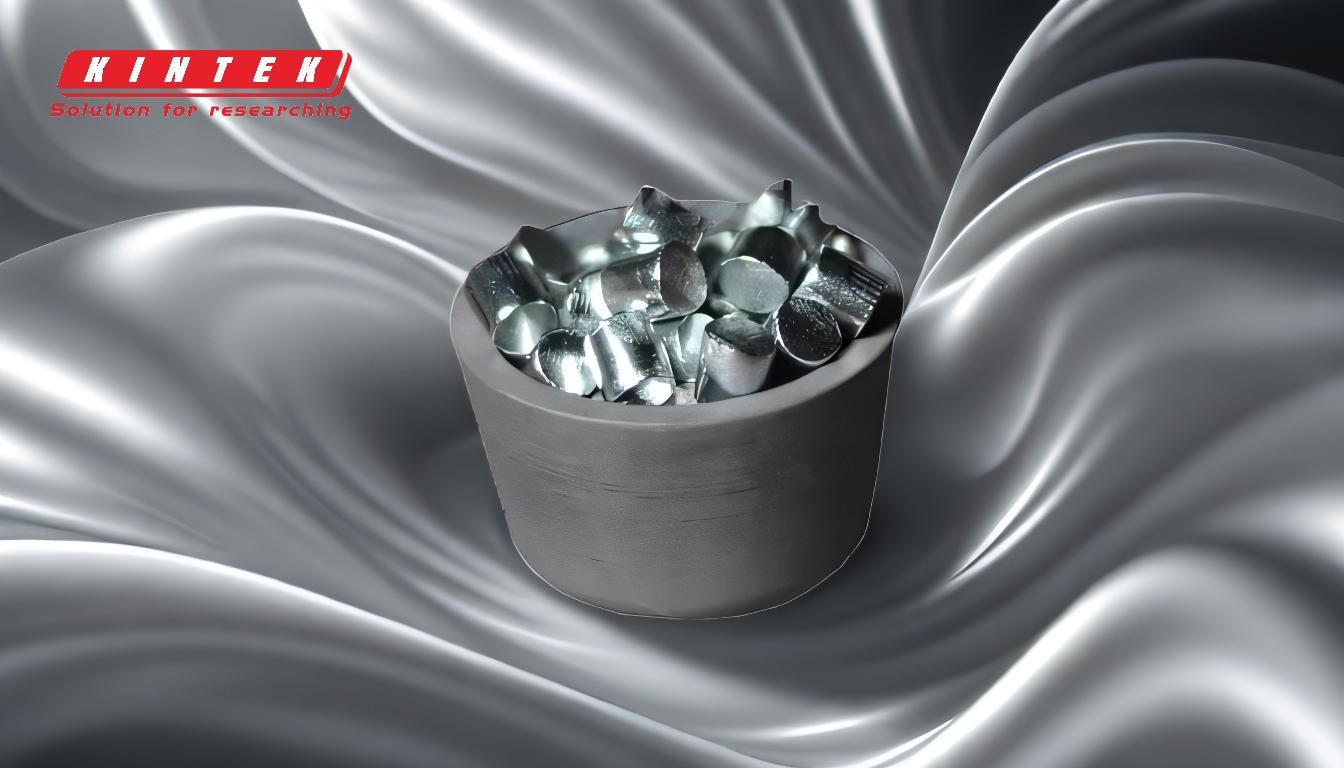
-
Physikalische Gasphasenabscheidung (PVD)
- Definition:Bei der PVD wird das Material physikalisch von einer Quelle auf ein Substrat übertragen, in der Regel in einer Vakuumumgebung.
-
Verfahren:
- Verdunstung:Das Material wird erhitzt, bis es verdampft und dann auf dem Substrat kondensiert.Zu den Techniken gehören die thermische Verdampfung und die Elektronenstrahlverdampfung.
- Sputtern:Durch Beschuss mit hochenergetischen Ionen werden Atome aus einem festen Zielmaterial herausgeschleudert, die sich dann auf dem Substrat ablagern.Gängige Verfahren sind Magnetronsputtern und Ionenstrahlsputtern.
- Gepulste Laserabscheidung (PLD):Ein Hochleistungslaser trägt Material von einem Ziel ab, wodurch eine Plasmastrahlung entsteht, die sich auf dem Substrat ablagert.
- Molekularstrahlepitaxie (MBE):Ein hochgradig kontrolliertes Verfahren, bei dem Strahlen von Atomen oder Molekülen auf das Substrat gerichtet werden, um epitaktische Schichten Schicht für Schicht zu erzeugen.
- Anwendungen:PVD ist weit verbreitet in der Halbleiterherstellung, bei optischen Beschichtungen und dekorativen Veredelungen.
-
Chemische Gasphasenabscheidung (CVD)
- Definition:Bei der CVD werden durch chemische Reaktionen hochreine dünne Schichten hergestellt.Vorläufergase reagieren auf der Substratoberfläche und bilden das gewünschte Material.
-
Verfahren:
- Thermische CVD:Das Substrat wird auf hohe Temperaturen erhitzt, um die chemische Reaktion zu erleichtern.
- Plasma-unterstütztes CVD (PECVD):Durch den Einsatz von Plasma wird die Reaktionstemperatur gesenkt, so dass das Verfahren auch für temperaturempfindliche Substrate geeignet ist.
- Atomlagenabscheidung (ALD):Ein spezielles CVD-Verfahren, bei dem die Schichten atomweise abgeschieden werden, was eine außergewöhnliche Kontrolle über Dicke und Gleichmäßigkeit ermöglicht.
- Metallorganische CVD (MOCVD):Verwendet metallorganische Vorstufen zur Abscheidung von Verbindungshalbleitern, die häufig bei der Herstellung von LEDs und Laserdioden verwendet werden.
- Anwendungen:CVD ist unerlässlich für die Herstellung hochwertiger Schichten in der Mikroelektronik, bei Solarzellen und Schutzschichten.
-
Andere Abscheidungstechniken
- Spin-Beschichtung:Ein flüssiger Vorläufer wird auf ein Substrat aufgetragen, das dann mit hoher Geschwindigkeit geschleudert wird, um das Material gleichmäßig zu verteilen.Dieses Verfahren wird üblicherweise zur Herstellung gleichmäßiger Polymerfilme verwendet.
- Tauchbeschichtung:Das Substrat wird in ein flüssiges Vorprodukt getaucht und dann mit kontrollierter Geschwindigkeit herausgezogen, wobei ein dünner Film auf der Oberfläche zurückbleibt.
- Sprühpyrolyse:Eine Lösung, die das gewünschte Material enthält, wird auf ein erhitztes Substrat gesprüht, wo es sich zersetzt und einen dünnen Film bildet.
- Sol-Gel:Ein nasschemisches Verfahren, bei dem eine Lösung (Sol) in einen gelartigen Zustand übergeht, der dann getrocknet und gesintert wird, um einen dünnen Film zu bilden.
- Galvanik:Ein elektrochemisches Verfahren, bei dem Metallionen reduziert und auf einem leitfähigen Substrat abgeschieden werden.
-
Faktoren, die die Auswahl der Technik beeinflussen
- Filmdicke und Gleichmäßigkeit:Verfahren wie ALD und Spin-Coating bieten eine präzise Kontrolle der Schichtdicke, während PVD und CVD besser für dickere Schichten geeignet sind.
- Substratmaterial und Temperaturempfindlichkeit:PECVD und ALD sind ideal für temperaturempfindliche Substrate, während thermisches CVD und PVD höhere Temperaturen erfordern.
- Materialkompatibilität:Bestimmte Materialien eignen sich besser für bestimmte Techniken, z. B. Metalle für Sputtering und Halbleiter für MOCVD.
- Anforderungen an die Anwendung:Der Verwendungszweck der Dünnschicht (z. B. optisch, elektronisch oder als Schutzschicht) bestimmt die Wahl der Abscheidungsmethode.
-
Aufkommende Trends in der Dünnschichtabscheidung
- Hybride Techniken:Kombination von PVD- und CVD-Verfahren, um die Vorteile beider Verfahren zu nutzen.
- Nanostrukturierte Filme:Fortgeschrittene Techniken wie ALD und MBE ermöglichen die Herstellung von Schichten im Nanomaßstab.
- Nachhaltigkeit:Entwicklung umweltfreundlicher Ausgangsstoffe und energieeffizienter Verfahren zur Verringerung der Umweltauswirkungen.
Durch das Verständnis dieser Techniken und ihrer jeweiligen Vorteile können die Käufer von Geräten und Verbrauchsmaterialien fundierte Entscheidungen bei der Auswahl der geeigneten Methode für ihre spezifische Anwendung treffen.
Zusammenfassende Tabelle:
Kategorie | Techniken | Anwendungen |
---|---|---|
Physikalische Gasphasenabscheidung (PVD) | Aufdampfen, Sputtern, PLD, MBE | Halbleiterherstellung, optische Beschichtungen, dekorative Veredelungen |
Chemische Gasphasenabscheidung (CVD) | Thermische CVD, PECVD, ALD, MOCVD | Mikroelektronik, Solarzellen, Schutzschichten |
Andere Techniken | Spin Coating, Dip Coating, Sprühpyrolyse, Sol-Gel, Galvanik | Polymerfilme, nanostrukturierte Filme, umweltfreundliche Verfahren |
Benötigen Sie Hilfe bei der Auswahl der richtigen Dünnschichtabscheidungstechnik? Kontaktieren Sie noch heute unsere Experten !