Die Toleranzen beim Lasersintern sind entscheidend für die Präzision und Qualität von 3D-gedruckten Teilen.Bei diesem Verfahren wird pulverförmiges Material Schicht für Schicht mit einem Laser verschmolzen. Für Anwendungen, die eine hohe Genauigkeit erfordern, sind enge Toleranzen unerlässlich.Auf der Grundlage der vorliegenden Referenz können maßgeschneiderte Sintertechniken Toleranzen innerhalb eines Mikrometers für Linearität und Konzentrizität erreichen.Dieses Präzisionsniveau lässt sich durch eine fortschrittliche Steuerung der Laserparameter, der Materialeigenschaften und der Prozessoptimierung erreichen.
Die wichtigsten Punkte werden erklärt:
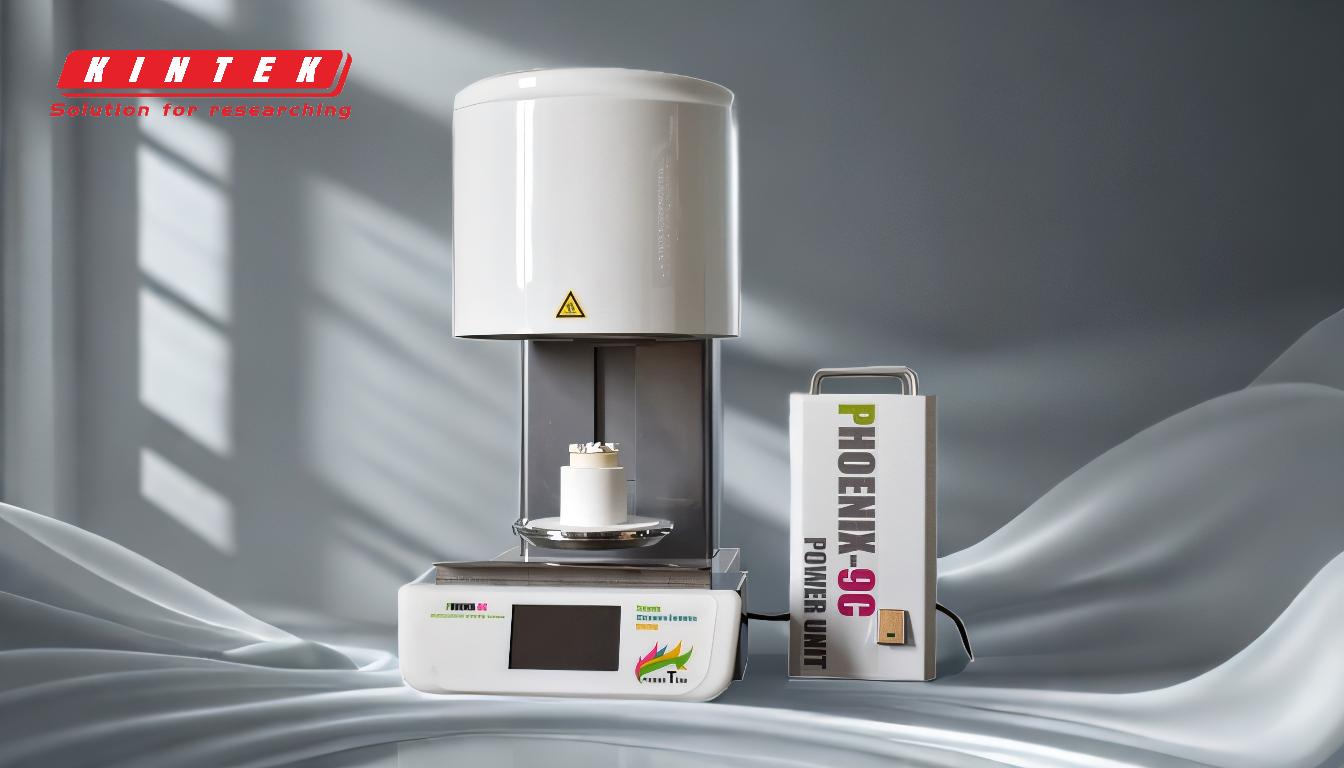
-
Definition von Toleranzen beim Laser-Sintern:
- Toleranzen bezeichnen die zulässige Abweichung von einer bestimmten Abmessung oder Geometrie in einem gefertigten Teil.
- Beim Lasersintern werden die Toleranzen durch Faktoren wie Laserleistung, Scangeschwindigkeit, Schichtdicke und Materialeigenschaften beeinflusst.
-
Erreichen von Toleranzen innerhalb eines Mikron:
- Die Referenz besagt, dass maßgeschneiderte Sintertechniken Linearität und Konzentrizität innerhalb eines Mikrometers gewährleisten können.
-
Dieses Maß an Präzision wird erreicht durch:
- Fortschrittliche Lasersteuerung:Präzise Steuerung von Laserleistung und Scangeschwindigkeit zur Minimierung von Abweichungen.
- Material-Optimierung:Verwendung von Materialien mit gleichmäßiger Partikelgröße und -verteilung, um eine gleichmäßige Sinterung zu gewährleisten.
- Überwachung des Prozesses:Echtzeitüberwachung und -anpassung des Sinterprozesses zur Einhaltung enger Toleranzen.
-
Faktoren, die die Toleranzen beeinflussen:
- Laser-Parameter:Die Intensität, der Fokus und das Abtastmuster des Lasers haben einen erheblichen Einfluss auf die Genauigkeit des gesinterten Teils.
- Schichtdicke:Dünnere Schichten ermöglichen im Allgemeinen eine höhere Präzision, können aber die Bauzeit verlängern.
- Materialeigenschaften:Die Wärmeleitfähigkeit, der Schmelzpunkt und die Partikelgröße des Materials beeinflussen die Sinterfähigkeit und die endgültige Maßgenauigkeit.
- Kalibrierung der Maschine:Die regelmäßige Kalibrierung der Lasersintermaschine ist für eine gleichbleibende Leistung unerlässlich.
-
Anwendungen, die enge Toleranzen erfordern:
- Medizinische Geräte:Komponenten wie Implantate und chirurgische Werkzeuge erfordern eine hohe Präzision, um die richtige Passform und Funktion zu gewährleisten.
- Luft- und Raumfahrt:Teile für Luft- und Raumfahrzeuge müssen strenge Toleranzen einhalten, um Sicherheit und Leistung zu gewährleisten.
- Mikroelektronik:Kleine, komplizierte Komponenten für elektronische Geräte erfordern oft Toleranzen von wenigen Mikrometern.
-
Herausforderungen bei der Aufrechterhaltung von Toleranzen:
- Thermische Verzerrung:Die beim Sintern entstehende Hitze kann dazu führen, dass sich die Teile verziehen oder verformen, was die Maßhaltigkeit beeinträchtigt.
- Schrumpfung des Materials:Einige Materialien schrumpfen beim Abkühlen, was bei der Konstruktion und dem Sinterprozess berücksichtigt werden muss.
- Oberflächengüte:Das Erreichen einer glatten Oberfläche bei gleichzeitiger Einhaltung enger Toleranzen kann eine Herausforderung sein.
-
Strategien zur Verbesserung der Toleranzen:
- Prozess-Optimierung:Feinabstimmung der Laserparameter und Sinterstrategien zur Minimierung von Abweichungen.
- Nachbearbeitung:Um die gewünschten Toleranzen und Oberflächengüten zu erreichen, können Techniken wie Bearbeitung oder Polieren eingesetzt werden.
- Entwurf für additive Fertigung (DfAM):Entwurf von Teilen unter Berücksichtigung von Sintertoleranzen, wie z. B. die Berücksichtigung von Schrumpfung oder Verzug.
Zusammenfassend lässt sich sagen, dass beim Lasersintern durch fortschrittliche Techniken und eine sorgfältige Kontrolle der Prozessparameter Toleranzen innerhalb eines Mikrometers für Linearität und Konzentrizität erreicht werden können.Die Einhaltung solch enger Toleranzen erfordert jedoch eine Kombination aus optimierten Materialien, präziser Lasersteuerung und gründlicher Prozessüberwachung.Diese Toleranzen sind für hochpräzise Anwendungen in Branchen wie der Medizin, der Luft- und Raumfahrt und der Mikroelektronik unerlässlich.
Zusammenfassende Tabelle:
Hauptaspekt | Einzelheiten |
---|---|
Toleranz Definition | Zulässige Abweichung von den angegebenen Maßen bei lasergesinterten Teilen. |
Erreichen von 1-Mikrometer-Präzision | Fortschrittliche Lasersteuerung, Materialoptimierung und Prozessüberwachung in Echtzeit. |
Beeinflussende Faktoren | Laserparameter, Schichtdicke, Materialeigenschaften und Maschinenkalibrierung. |
Anwendungen | Medizinische Geräte, Luft- und Raumfahrt und Mikroelektronik. |
Herausforderungen | Thermischer Verzug, Materialschrumpfung und Oberflächengüte. |
Verbesserungs-Strategien | Prozessoptimierung, Nachbearbeitung und Design for Additive Manufacturing (DfAM). |
Sie benötigen Präzisions-Lasersintern für Ihr Projekt? Kontaktieren Sie noch heute unsere Experten um mehr zu erfahren!