Nach dem Sintern erfährt das Material erhebliche mikrostrukturelle Veränderungen, die seine physikalischen und mechanischen Eigenschaften direkt beeinflussen.Der Prozess führt zur Verschmelzung der Partikel, zur Verringerung der Porosität und zur Bildung einer dichten, festen Struktur.Diese Veränderungen verbessern Eigenschaften wie Festigkeit, Haltbarkeit, Wärmeleitfähigkeit und elektrische Leitfähigkeit.Je nach Material und Sinterbedingungen kann das Endprodukt auch eine verbesserte Transluzenz aufweisen.Das Ergebnis ist ein Material mit maßgeschneiderten Eigenschaften für bestimmte Anwendungen, die durch eine sorgfältige Kontrolle der Parameter des Sinterprozesses erreicht werden.
Die wichtigsten Punkte werden erklärt:
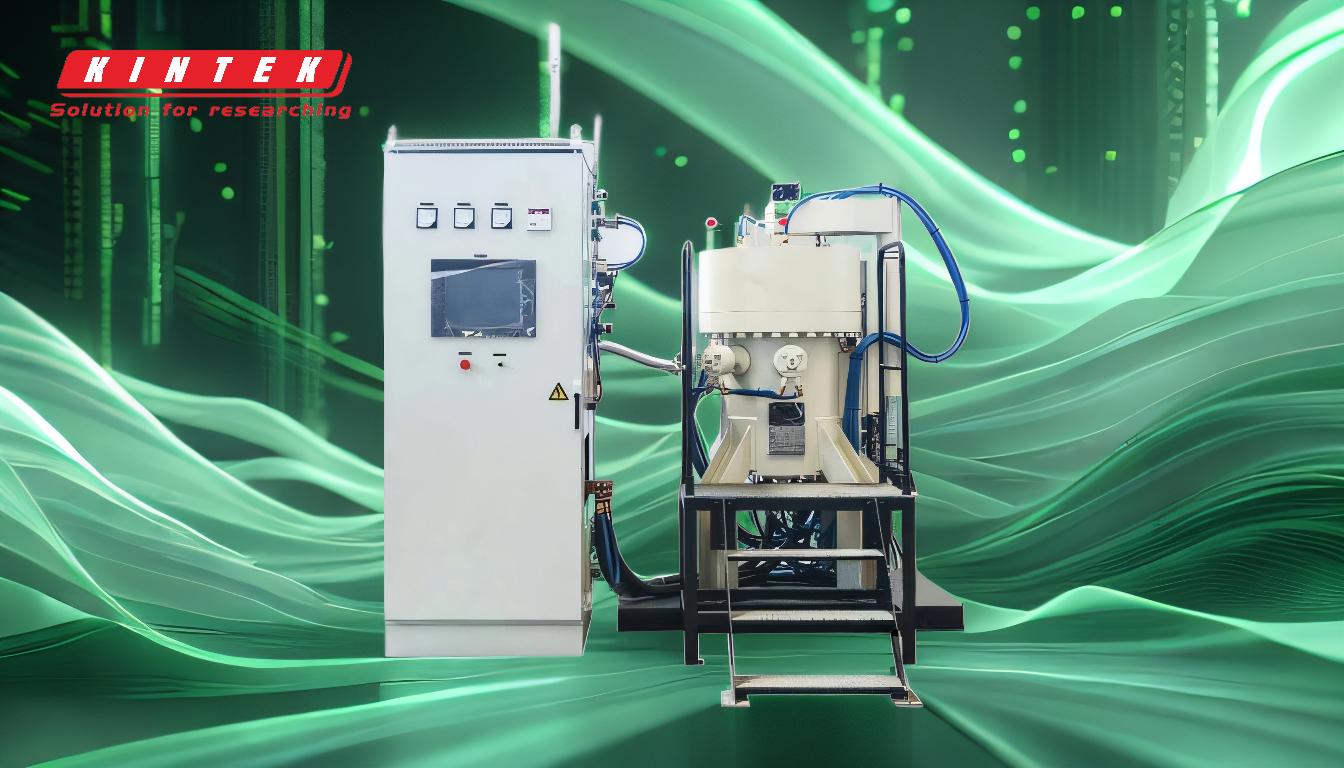
-
Mikrostrukturelle Veränderungen:
- Korngröße und Wachstum: Das Sintern führt zu einem Wachstum der Körner im Material.Wenn die Partikel miteinander verschmelzen, verschwinden die Grenzen zwischen ihnen, was zu einer größeren Korngröße führt.Dieses Kornwachstum kann sich auf die mechanischen Eigenschaften des Materials auswirken, z. B. auf die Festigkeit und Zähigkeit.
- Porengröße und -verteilung: Durch den Sinterprozess wird die Porosität des Materials verringert, indem Poren geschlossen und Hohlräume beseitigt werden.Diese Verdichtung verbessert die Dichte des Materials und kann Eigenschaften wie Festigkeit und Wärmeleitfähigkeit verbessern.
- Form und Verteilung der Korngrenzen: Die Form und die Verteilung der Korngrenzen werden während des Sinterns verändert.Diese Veränderungen können sich auf die Verformungsbeständigkeit des Materials und seine allgemeine Haltbarkeit auswirken.
-
Physikalische und chemische Veränderungen:
- Verdampfung flüchtiger Bestandteile: Während des Sinterns werden Wasser, organische Stoffe oder adsorbierte Gase aus dem Material entfernt.Dieser Reinigungsprozess ist entscheidend für die Herstellung eines dichten und homogenen Endprodukts.
- Reduktion von Oberflächenoxiden: Die Oberflächenoxide auf den Pulverpartikeln werden reduziert, was eine bessere Bindung zwischen den Partikeln ermöglicht und die Gesamtintegrität des Materials verbessert.
- Materialwanderung und Rekristallisation: Atome wandern über Partikelgrenzen hinweg, was zur Rekristallisation und zur Bildung neuer kristalliner Strukturen führt.Dieser Prozess trägt zur Verdichtung und Festigkeit des Materials bei.
-
Verbesserung der Materialeigenschaften:
- Festigkeit und Dauerhaftigkeit: Die Verringerung der Porosität und die Bildung einer dichten Mikrostruktur erhöhen die Festigkeit und Haltbarkeit des Materials erheblich.Dadurch eignet sich das gesinterte Material für Anwendungen, die eine hohe mechanische Leistung erfordern.
- Thermische und elektrische Leitfähigkeit: Durch den Verdichtungsprozess wird die thermische und elektrische Leitfähigkeit des Materials verbessert, indem die Anzahl der isolierenden Hohlräume verringert und die Verbindung zwischen den Körnern verbessert wird.
- Transluzenz: Bei einigen Werkstoffen kann das Sintern zu einer erhöhten Transluzenz führen, was bei Anwendungen wie Dentalkeramik oder optischen Komponenten wünschenswert ist.
-
Letzte Phase der Sinterung:
- Bindung der verbleibenden Poren: In der letzten Phase des Sinterns werden alle verbleibenden offenen Risse oder Poren mit flüssigen oder bindenden Zusätzen gefüllt.Auf diese Weise wird sichergestellt, dass das Material vollständig dicht und frei von Fehlern ist, was zu einem hochwertigen Endprodukt führt.
- Bildung einer festen Masse: Das Material wird größtenteils fest, mit einer einheitlichen Mikrostruktur, die die gewünschten Eigenschaften für die vorgesehene Anwendung aufweist.
-
Anwendungen und Implikationen:
- Maßgeschneiderte Materialeigenschaften: Durch die Steuerung der Parameter des Sinterprozesses können die Hersteller die Eigenschaften des Materials auf die spezifischen Anforderungen der Anwendung abstimmen.Dazu gehört die Anpassung von Temperatur, Druck und Dauer des Sinterns, um die gewünschte Mikrostruktur und die gewünschten Eigenschaften zu erreichen.
- Vielseitigkeit in den Anwendungen: Gesinterte Werkstoffe werden in einer Vielzahl von Branchen eingesetzt, unter anderem in der Automobilindustrie, der Luft- und Raumfahrt, der Elektronik und der Medizintechnik.Die durch das Sintern erzielten verbesserten Eigenschaften machen diese Materialien ideal für Hochleistungsanwendungen.
Zusammenfassend lässt sich sagen, dass die Phase nach dem Sintern durch erhebliche mikrostrukturelle Veränderungen gekennzeichnet ist, die die physikalischen und mechanischen Eigenschaften des Materials verbessern.Das Verfahren führt zu einem dichten, festen Gefüge mit verbesserter Festigkeit, Haltbarkeit und Leitfähigkeit und eignet sich damit für eine Vielzahl von Hochleistungsanwendungen.
Zusammenfassende Tabelle:
Wichtigste Änderungen | Auswirkungen auf die Materialeigenschaften |
---|---|
Korngröße und Wachstum | Größere Körner verbessern Festigkeit und Zähigkeit. |
Porengröße und -verteilung | Eine geringere Porosität erhöht die Dichte, Festigkeit und thermische/elektrische Leitfähigkeit. |
Veränderungen der Korngrenzen | Veränderte Korngrenzen verbessern die Haltbarkeit und den Widerstand gegen Verformung. |
Verdampfung von flüchtigen Bestandteilen | Entfernt Verunreinigungen und sorgt für ein dichtes und homogenes Gefüge. |
Rekristallisation | Bildet neue kristalline Strukturen, die die Verdichtung und Festigkeit erhöhen. |
Transluzenz | Erhöht sich bei einigen Materialien, ideal für Dentalkeramiken oder optische Komponenten. |
Endverdichtung | Bindet die verbleibenden Poren und schafft eine fehlerfreie, feste Masse mit maßgeschneiderten Eigenschaften. |
Erschließen Sie das Potenzial von Sinterwerkstoffen für Ihre Anwendungen. Kontaktieren Sie unsere Experten noch heute !