Reaktives Sputtern ist ein spezielles Verfahren zur Abscheidung von Dünnschichten, bei dem ein reaktives Gas, z. B. Sauerstoff oder Stickstoff, in eine Sputterkammer eingeleitet wird.Dieses Gas reagiert chemisch mit den gesputterten Atomen eines Zielmaterials und bildet Verbindungen wie Oxide oder Nitride, die dann als Dünnschicht auf einem Substrat abgeschieden werden.Dieses Verfahren ermöglicht eine genaue Kontrolle über die Zusammensetzung und die Eigenschaften des Films und ist daher für Anwendungen wie die Herstellung von Sperrschichten, optischen Beschichtungen und Halbleiterbauelementen unerlässlich.Das Verfahren erfordert eine sorgfältige Steuerung von Parametern wie Gasdurchsatz, Partialdruck und Plasmabedingungen, um die gewünschte Stöchiometrie und Filmeigenschaften zu erreichen.
Die wichtigsten Punkte werden erklärt:
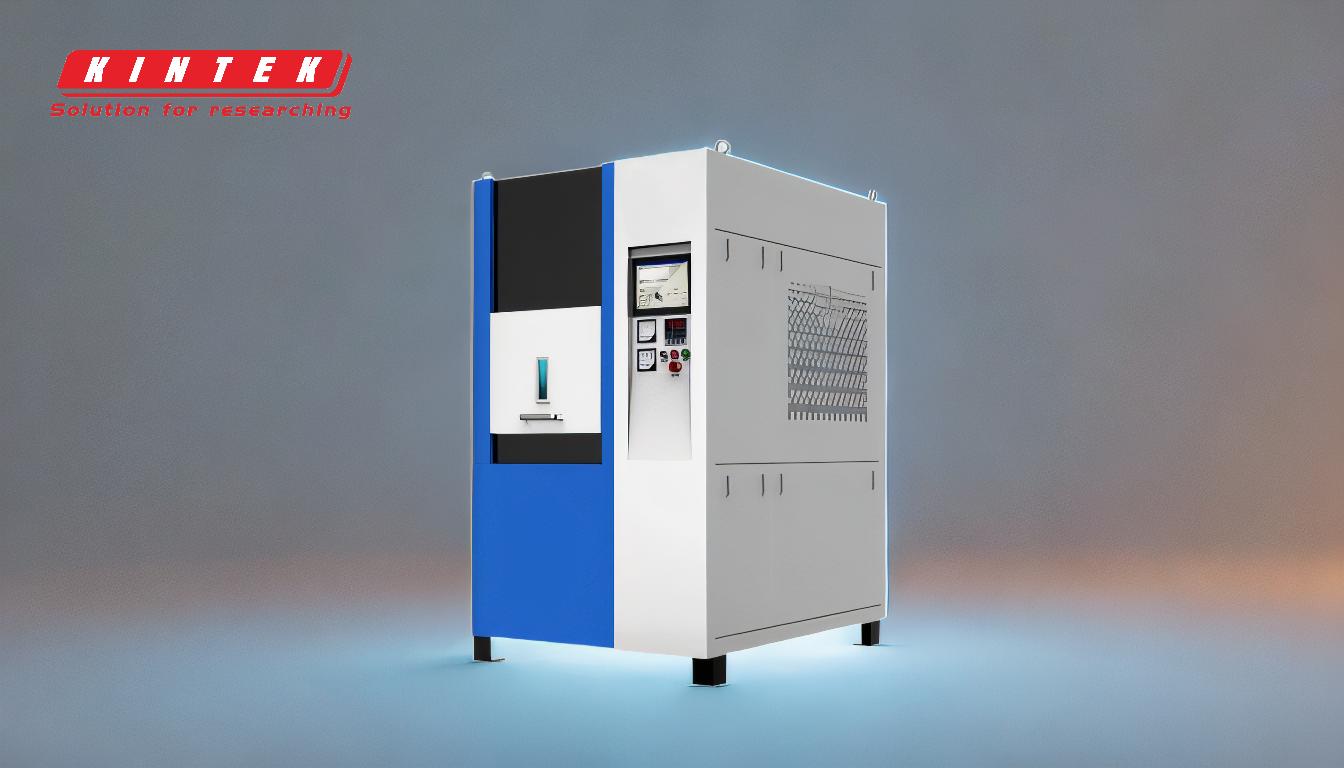
-
Definition des reaktiven Sputterns:
- Das reaktive Sputtern ist eine Variante des Plasmasputterverfahrens, das zur Abscheidung dünner Schichten auf Substraten verwendet wird.
- Dabei wird ein reaktives Gas (z. B. Sauerstoff, Stickstoff) in die Sputterkammer eingeleitet, wo es chemisch mit den gesputterten Atomen des Zielmaterials reagiert.
- Die dabei entstehenden Reaktionsprodukte bilden eine Verbindung (z. B. Titannitrid, Siliziumoxid), die als dünner Film auf dem Substrat abgeschieden wird.
-
Schlüsselkomponenten des Verfahrens:
- Ziel Material:In der Regel ein elementares Material (z. B. Titan, Silizium), das zerstäubt wird, um Atome in der Kammer freizusetzen.
- Reaktives Gas:Ein Gas wie Sauerstoff oder Stickstoff, das mit den gesputterten Atomen reagiert und eine Verbindung bildet.
- Inertes Gas:Häufig Argon, das zur Erzeugung des Plasmas verwendet wird, das das Zielmaterial zerstäubt.
- Substrat:Die Oberfläche, auf der die dünne Schicht abgeschieden wird.
-
Mechanismus der chemischen Reaktion:
- Die gesputterten Atome des Zielmaterials stoßen mit den reaktiven Gasmolekülen im Plasma zusammen.
- Es kommt zu einer chemischen Reaktion, bei der eine neue Verbindung entsteht (z. B. Titannitrid oder Siliziumoxid).
- Diese Verbindung wird dann als dünner Film auf dem Substrat abgeschieden.
-
Kontrolle der Filmeigenschaften:
- Stöchiometrie:Die Zusammensetzung des Films kann durch Anpassung des Verhältnisses von reaktivem Gas zu Inertgas gesteuert werden.
- Struktur des Films:Parameter wie Gasflussraten, Partialdrücke und Plasmabedingungen beeinflussen die Struktur und die Eigenschaften des Films.
- Funktionelle Eigenschaften:Das Verfahren ermöglicht die Optimierung von Eigenschaften wie Spannung, Brechungsindex und elektrische Leitfähigkeit.
-
Herausforderungen und Überlegungen:
- Hysterese-Verhalten:Die Einführung eines reaktiven Gases kann den Prozess verkomplizieren und zu einem nichtlinearen Verhalten bei den Abscheideraten und der Stöchiometrie führen.
- Kontrolle der Parameter:Um die gewünschten Schichteigenschaften zu erreichen, müssen Gasdurchsatz, Partialdruck und Plasmabedingungen genauestens gesteuert werden.
- Ziel Erosion:Das Berg-Modell wird häufig verwendet, um die Auswirkungen reaktiver Gase auf die Targeterosion und die Abscheideraten abzuschätzen.
-
Anwendungen des reaktiven Sputterns:
- Barriereschichten:Wird bei der Halbleiterherstellung verwendet, um dünne Schichten zu erzeugen, die die Diffusion von Materialien verhindern.
- Optische Beschichtungen:Herstellung von Filmen mit spezifischen Brechungsindizes für Anwendungen wie Antireflexionsbeschichtungen.
- Halbleiterbauelemente:Ermöglicht die Abscheidung von präzisen Dünnschichten für elektronische Bauteile.
-
Varianten des reaktiven Sputterns:
- DC Reaktives Sputtern:Verwendung von Gleichstrom zur Erzeugung des Plasmas.
- HF (Hochfrequenz) Reaktives Sputtern:Verwendung von Hochfrequenz-Wechselstrom, häufig für isolierende Materialien.
Durch eine sorgfältige Steuerung des reaktiven Sputterprozesses können Hersteller dünne Schichten mit maßgeschneiderten Eigenschaften für eine breite Palette industrieller und technischer Anwendungen herstellen.
Zusammenfassende Tabelle:
Aspekt | Einzelheiten |
---|---|
Definition | Ein Verfahren zur Abscheidung von Dünnschichten unter Verwendung reaktiver Gase zur Bildung von Verbindungen. |
Hauptbestandteile | Zielmaterial, reaktives Gas (z. B. Sauerstoff, Stickstoff), Inertgas, Substrat. |
Anwendungen | Barriereschichten, optische Beschichtungen, Halbleiterbauelemente. |
Herausforderungen | Hystereseverhalten, präzise Parametersteuerung, Zielerosion. |
Varianten | DC Reaktive Zerstäubung, HF Reaktive Zerstäubung. |
Entdecken Sie, wie reaktives Sputtern Ihren Fertigungsprozess verbessern kann. Kontaktieren Sie noch heute unsere Experten für maßgeschneiderte Lösungen!