Beim Aufkohlen handelt es sich um einen Wärmebehandlungsprozess, der den Kohlenstoffgehalt auf der Oberfläche von kohlenstoffarmem Stahl erhöht und so dessen Härte und Verschleißfestigkeit erhöht, während gleichzeitig ein duktiler Kern erhalten bleibt. Der beim Aufkohlen zugesetzte Kohlenstoffgehalt liegt typischerweise zwischen 0,8 % und 1,2 %, abhängig von der Stahlsorte und Prozessparametern wie Temperatur und Zeit. Dieses Verfahren wird häufig zur Herstellung von Komponenten verwendet, die eine harte Außenseite für Haltbarkeit und eine robuste Innenseite für Flexibilität erfordern, wie z. B. Zahnräder, Wellen und Befestigungselemente.
Wichtige Punkte erklärt:
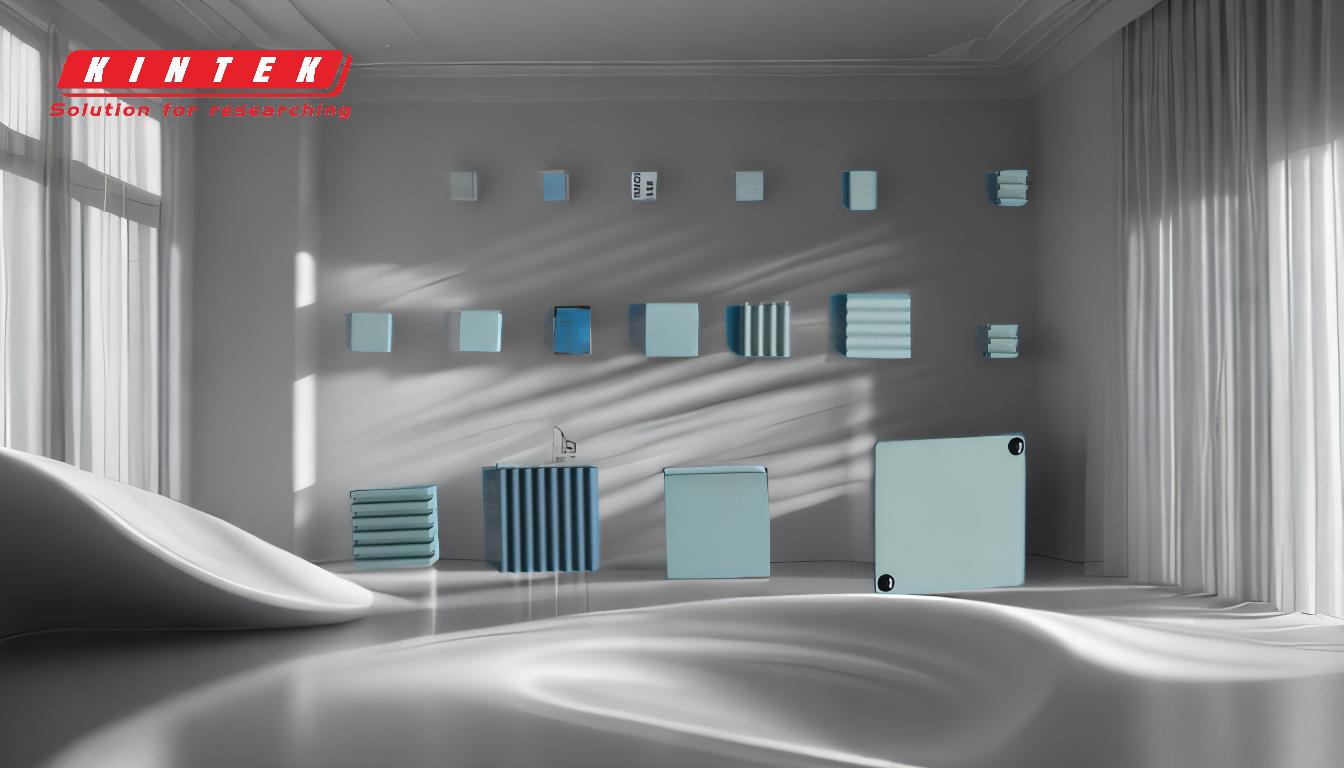
-
Definition und Zweck des Aufkohlens:
- Beim Aufkohlen handelt es sich um einen Einsatzhärtungsprozess, bei dem Kohlenstoff in die Oberfläche von kohlenstoffarmem Stahl diffundiert wird, um dessen Härte und Verschleißfestigkeit zu erhöhen.
- Mit dem Verfahren werden Teile mit einer harten Außenschicht und einem weichen, duktilen Kern hergestellt, was sie ideal für Anwendungen macht, die sowohl Haltbarkeit als auch Flexibilität erfordern.
-
Kohlenstoffgehalt beim Aufkohlen:
- Der beim Aufkohlen der Stahloberfläche hinzugefügte Kohlenstoffgehalt liegt typischerweise zwischen 0,8 % und 1,2 % .
- Dieser Bereich wird durch die bestimmt Diagramm des Eisen-Kohlenstoff-Gleichgewichts , was das optimale Kohlenstoffpotenzial zum Erreichen der gewünschten Härte und Mikrostruktur vorgibt.
-
Faktoren, die den Kohlenstoffgehalt beeinflussen:
- Temperatur: Höhere Temperaturen erhöhen die Diffusionsrate von Kohlenstoff in den Stahl und ermöglichen so eine stärkere Kohlenstoffabsorption.
- Zeit: Längere Aufkohlungszeiten führen zu größeren Härtetiefen und einem höheren Kohlenstoffgehalt in der Oberflächenschicht.
- Stahltyp: Der Grundkohlenstoffgehalt des Stahls und seine Legierungselemente beeinflussen den endgültigen Kohlenstoffgehalt und die Härte.
-
Prozessmechanismus:
- Der Stahl wird in einer kohlenstoffreichen Umgebung, beispielsweise einem kohlenstoffhaltigen Gas oder festen Medium, auf Temperaturen unterhalb seines Schmelzpunkts erhitzt.
- Kohlenstoffatome diffundieren in die Stahloberfläche, verändern deren Kornstruktur und erhöhen die Härte.
- Nach dem Aufkohlen wird der Stahl in Öl oder einem anderen Medium abgeschreckt, um die gehärtete Oberflächenschicht zu fixieren.
-
Anwendungen aufgekohlter Teile:
- Zur Herstellung wird üblicherweise Aufkohlen eingesetzt Zahnräder, Wellen, Befestigungselemente und Werkzeuge die eine Kombination aus Oberflächenhärte und Kernzähigkeit erfordern.
- Das Verfahren ist ideal für Bauteile, die hohem Verschleiß, Abrieb oder Ermüdung ausgesetzt sind.
-
Typische Gehäusetiefen:
- Die Tiefe der gehärteten Schicht (Verstärkungstiefe) liegt typischerweise im Bereich von 0,020″ bis 0,050″ , abhängig von der Anwendung und den Prozessparametern.
- Größere Einsatztiefen werden durch längere Aufkohlungszeiten und höhere Temperaturen erreicht.
-
Vergleich mit Carbonitrieren:
- Während sich das Aufkohlen ausschließlich auf die Zugabe von Kohlenstoff konzentriert, Karbonitrieren führt sowohl Kohlenstoff als auch Stickstoff in den Stahl ein.
- Carbonitrieren wird verwendet, wenn eine Durchhärtung erforderlich ist, um zusätzliche Festigkeit und Verschleißfestigkeit zu gewährleisten.
-
Vorteile des Aufkohlens:
- Verbesserte Verschleißfestigkeit: Die harte Oberflächenschicht widersteht Abrieb und Verschleiß.
- Erhöhte Ermüdungsfestigkeit: Das Verfahren erhöht die Widerstandsfähigkeit des Stahls gegenüber zyklischen Belastungen.
- Duktiler Kern: Die weiche Innenseite sorgt dafür, dass das Teil flexibel und bruchsicher bleibt.
Durch das Verständnis des Kohlenstoffgehalts und der Prozessparameter des Aufkohlens können Hersteller die Behandlung so anpassen, dass sie spezifische Leistungsanforderungen für ihre Komponenten erfüllt. Dies macht das Aufkohlen zu einem vielseitigen und unverzichtbaren Prozess bei der Herstellung langlebiger mechanischer Teile.
Übersichtstabelle:
Aspekt | Einzelheiten |
---|---|
Kohlenstoffgehalt | 0,8 % bis 1,2 % (Oberflächenschicht) |
Prozesstemperatur | Unterhalb des Schmelzpunkts, typischerweise 850 °C bis 950 °C |
Gehäusetiefe | 0,020″ bis 0,050″ (einstellbar mit Zeit und Temperatur) |
Anwendungen | Zahnräder, Wellen, Befestigungselemente, Werkzeuge |
Vorteile | Verbesserte Verschleißfestigkeit, erhöhte Dauerfestigkeit, duktiler Kern |
Vergleich | Aufkohlen vs. Carbonitrieren: Nur Kohlenstoff vs. Zugabe von Kohlenstoff + Stickstoff |
Entdecken Sie, wie Aufkohlen Ihre Stahlkomponenten optimieren kann – Kontaktieren Sie noch heute unsere Experten für maßgeschneiderte Lösungen!