Der Aufkohlungsprozess ist eine Wärmebehandlungsmethode, mit der die Oberflächenhärte und Verschleißfestigkeit von kohlenstoffarmem Stahl erhöht und gleichzeitig ein duktiler und zäher Kern erhalten bleibt. Dies wird erreicht, indem Kohlenstoff bei hohen Temperaturen, typischerweise unterhalb seines Schmelzpunkts, in einer kohlenstoffreichen Umgebung in die Oberflächenschicht des Metalls diffundiert. Dabei wird der Stahl in einem Ofen erhitzt, kohlenstoffreichen Elementen wie Propangas ausgesetzt und der Kohlenstoff in die Oberfläche diffundieren gelassen. Nach dem Aufkohlen wird der Stahl oft in Öl abgeschreckt, um die Oberfläche zu härten, was zu einer harten Außenschicht und einem weicheren, formbareren Kern führt. Diese Methode wird häufig in Branchen eingesetzt, die langlebige und verschleißfeste Komponenten erfordern, beispielsweise im Automobil- und Maschinenbau.
Wichtige Punkte erklärt:
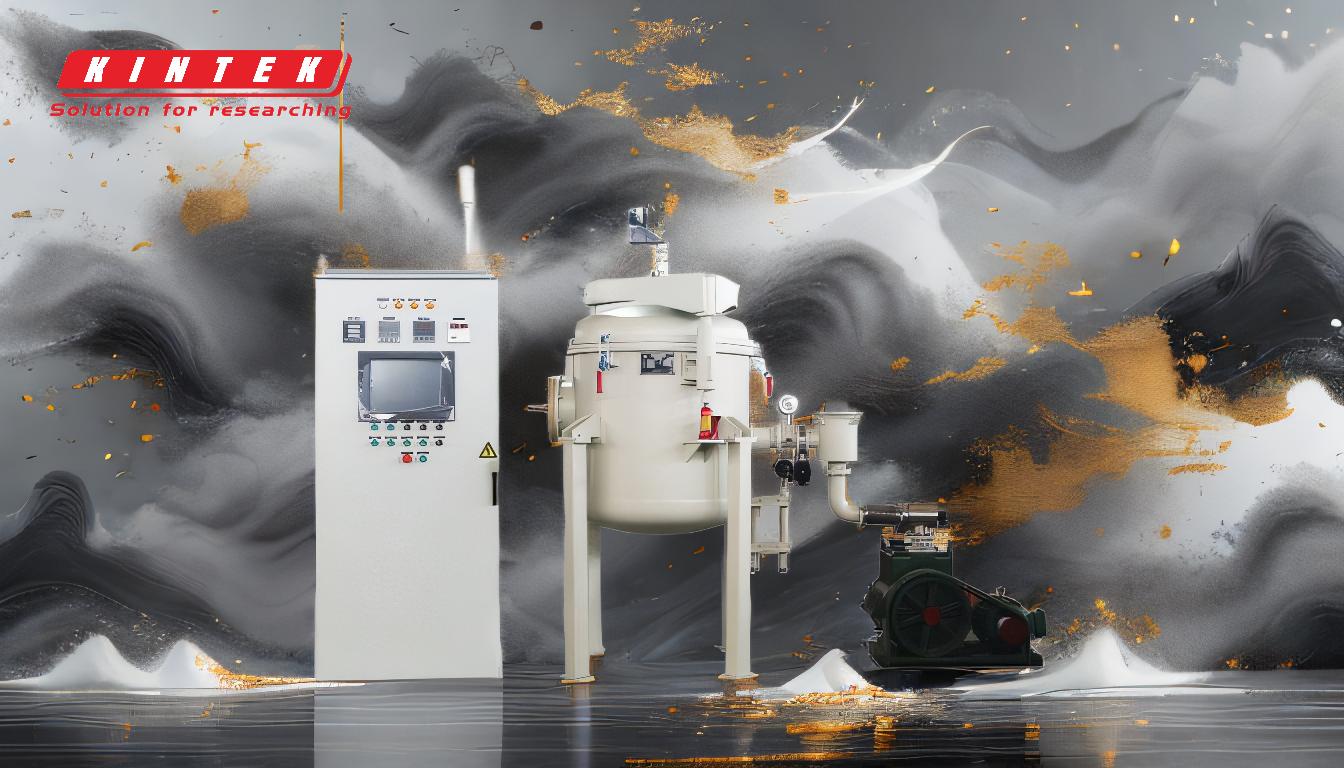
-
Zweck des Aufkohlens:
- Aufkohlen wird hauptsächlich zur Erhöhung der Oberflächenhärte und der Verschleißfestigkeit von kohlenstoffarmen Stählen eingesetzt.
- Dies wird durch die Anreicherung der Oberflächenschicht mit Kohlenstoff erreicht, was die Härtbarkeit verbessert und gleichzeitig die Duktilität und Zähigkeit des Kerns beibehält.
- Diese doppelte Eigenschaft ist für Komponenten, die sowohl Oberflächenhaltbarkeit als auch innere Festigkeit erfordern, wie z. B. Zahnräder, Wellen und Lager, von entscheidender Bedeutung.
-
Prozessübersicht:
- Der Stahl wird in einem Ofen auf eine Temperatur unterhalb seines Schmelzpunkts erhitzt, typischerweise zwischen 850 °C und 950 °C.
- Anschließend wird es einer kohlenstoffreichen Umgebung wie Propangas, Methan oder einer endothermen Atmosphäre ausgesetzt.
- Die Kohlenstoffatome diffundieren in die Stahloberfläche und bilden eine kohlenstoffreiche Schicht.
-
Schritte beim Aufkohlen:
- Schritt 1: Vorbereitung: Das Stahlteil wird gereinigt und in einen Ofen gelegt.
- Schritt 2: Erhitzen: Der Ofen wird auf die gewünschte Temperatur erhitzt und sorgt so für eine gleichmäßige Wärmeverteilung.
- Schritt 3: Kohlenstoffeinführung: Ein kohlenstoffreiches Gas (z. B. Propan) wird in den Ofen eingeleitet.
- Schritt 4: Kohlenstoffdiffusion: Durch die Hitze zerfällt das Gas und setzt Kohlenstoffatome frei, die in die Stahloberfläche diffundieren.
- Schritt 5: Abschrecken: Nach dem Aufkohlen wird der Stahl in Öl oder einem anderen Medium schnell abgekühlt (abgeschreckt), um die Oberfläche zu härten.
-
Arten der Aufkohlung:
- Gasaufkohlung: Verwendet kohlenstoffreiche Gase wie Propan oder Methan in einem Ofen mit kontrollierter Atmosphäre.
- Vakuumaufkohlung: Wird in einem Vakuumofen durchgeführt, um die Oxidation zu minimieren und die Kohlenstoffdiffusion zu verbessern.
- Flüssigaufkohlung: Dabei wird der Stahl in ein kohlenstoffreiches Flüssigkeitsbad, beispielsweise geschmolzenes Salz, getaucht.
- Packaufkohlung: Der Stahl wird in ein kohlenstoffreiches Material (z. B. Holzkohle) verpackt und in einem verschlossenen Behälter erhitzt.
-
Vorteile des Aufkohlens:
- Oberflächenhärte: Die mit Kohlenstoff angereicherte Oberfläche erhält eine hohe Verschleiß- und Abriebfestigkeit.
- Kernfestigkeit: Der Kern bleibt weich und duktil und bietet Schlagfestigkeit.
- Präzise Kontrolle: Härtetiefe (typischerweise 0,020″ bis 0,050″) und Kohlenstoffkonzentration können präzise gesteuert werden.
- Vielseitigkeit: Geeignet für eine Vielzahl von kohlenstoffarmen Stahllegierungen und komplexen Geometrien.
-
Anwendungen von aufgekohltem Stahl:
- Automobilindustrie: Wird für Zahnräder, Kurbelwellen und Nockenwellen verwendet, um die Haltbarkeit zu erhöhen.
- Maschinen: Wird auf Komponenten wie Lager, Rollen und Schneidwerkzeuge angewendet, um die Verschleißfestigkeit zu verbessern.
- Luft- und Raumfahrt: Wird in Teilen verwendet, die ein hohes Verhältnis von Festigkeit zu Gewicht und Ermüdungsbeständigkeit erfordern.
-
Überlegungen zu Geräten und Verbrauchsmaterialien:
- Ofenauswahl: Wählen Sie Öfen mit präziser Temperaturregelung und gleichmäßiger Wärmeverteilung.
- Kohlenstoffquellen: Verwenden Sie hochwertige kohlenstoffreiche Gase oder Materialien, um konsistente Ergebnisse zu gewährleisten.
- Abschreckmedium: Wählen Sie je nach Stahltyp und gewünschter Härte geeignete Abschrecköle oder -flüssigkeiten aus.
- Maskierungsmaterialien: Verwenden Sie kohlenstoffhemmende Farben oder Beschichtungen, um Bereiche zu schützen, die nicht aufgekohlt werden sollen.
-
Vorteile gegenüber anderen Wärmebehandlungsmethoden:
- Das Aufkohlen sorgt im Vergleich zu Methoden wie Flammhärten oder Induktionshärten für eine tiefere und gleichmäßigere Einsatzhärtung.
- Es ist kostengünstig für die Großserienfertigung und eignet sich für komplexe Teile.
Durch das Verständnis des Aufkohlungsprozesses können Gerätekäufer fundierte Entscheidungen über die Arten von Öfen, Gasen und Verbrauchsmaterialien treffen, die erforderlich sind, um optimale Ergebnisse für ihre spezifischen Anwendungen zu erzielen.
Übersichtstabelle:
Aspekt | Einzelheiten |
---|---|
Zweck | Erhöht die Oberflächenhärte und Verschleißfestigkeit bei gleichzeitiger Beibehaltung der Kernzähigkeit. |
Prozesstemperatur | 850 °C bis 950 °C, unterhalb des Schmelzpunkts des Stahls. |
Kohlenstoffquellen | Propan, Methan, endotherme Atmosphäre, geschmolzenes Salz oder Holzkohle. |
Wichtige Schritte | Vorbereitung, Erhitzen, Kohlenstoffeinbringung, Diffusion und Abschrecken. |
Typen | Gas-, Vakuum-, Flüssigkeits- und Packungsaufkohlung. |
Vorteile | Oberflächenhärte, Kernzähigkeit, Präzisionskontrolle und Vielseitigkeit. |
Anwendungen | Automobilgetriebe, Maschinenlager, Luft- und Raumfahrtkomponenten. |
Sind Sie bereit, Ihre Stahlkomponenten durch Aufkohlen zu verbessern? Kontaktieren Sie noch heute unsere Experten für maßgeschneiderte Lösungen!