Das CVD-Beschichtungsverfahren (Chemical Vapor Deposition) ist ein hochentwickeltes Verfahren, bei dem harte Materialschichten durch eine chemische Gasphasenreaktion auf ein Substrat aufgebracht werden. Bei diesem Verfahren werden flüchtige Vorläufergase in eine Reaktionskammer eingeleitet, in der Regel unter Vakuum, und die Kammer auf hohe Temperaturen (etwa 1000 °C) erhitzt, um die Reaktion zu aktivieren. Die Vorläufergase zersetzen sich oder reagieren mit der Substratoberfläche und bilden eine dünne, dauerhafte Beschichtung mit hervorragender Haftung. Das Verfahren ist äußerst vielseitig und eignet sich für die Beschichtung komplexer Geometrien, einschließlich Gewinden, Sacklöchern und Innenflächen. Es erfordert jedoch hohe Temperaturen und eine sorgfältige Kontrolle der Umgebungsbedingungen, was die Art der beschichtbaren Grundmaterialien einschränken kann. Das CVD-Verfahren wird häufig in Branchen eingesetzt, die Hochleistungsbeschichtungen benötigen, wie z. B. in der Luft- und Raumfahrt, der Automobilindustrie und der Werkzeugherstellung.
Die wichtigsten Punkte erklärt:
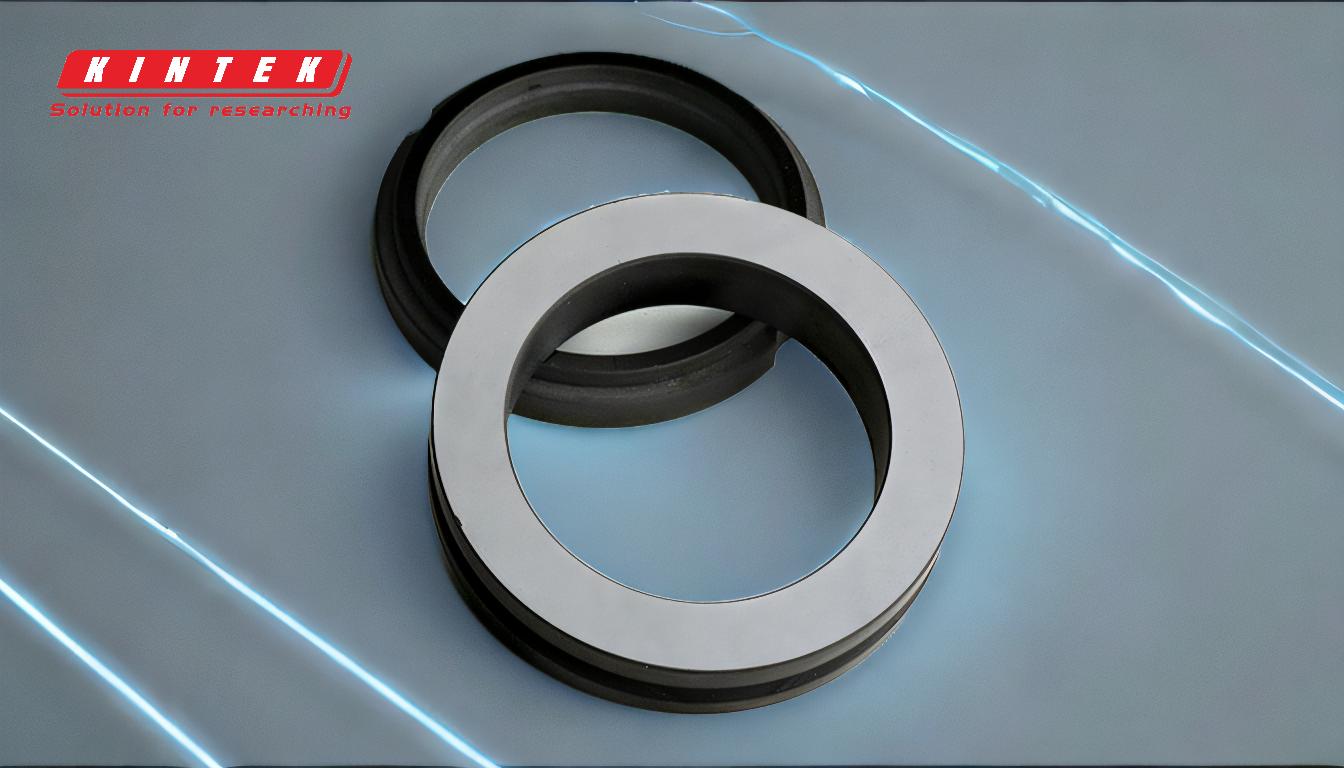
-
Definition und Zweck der CVD-Beschichtung
- Die CVD-Beschichtung ist ein chemisches Gasphasenverfahren, mit dem harte, dauerhafte Materialschichten auf ein Substrat aufgebracht werden.
- Mit diesem Verfahren lassen sich Beschichtungen mit hoher Haftfestigkeit herstellen, die sich für Anwendungen eignen, die Verschleißfestigkeit, Korrosionsschutz und thermische Stabilität erfordern.
-
Schlüsselkomponenten des CVD-Verfahrens
- Vorläufer-Gase: Flüchtige Chemikalien, die reagieren oder sich zersetzen, um die gewünschte Beschichtung zu bilden.
- Reaktionskammer: Eine vakuumversiegelte Umgebung, in der die chemischen Reaktionen stattfinden.
- Substrat: Das zu beschichtende Material, das sauber und frei von Verunreinigungen sein muss.
- Wärmequelle: Liefert die für die Aktivierung der chemischen Reaktionen erforderliche Energie, in der Regel bei Temperaturen um 1000 °C.
-
Schritte im CVD-Beschichtungsprozess
Das CVD-Verfahren kann in vier Hauptschritte unterteilt werden:-
Schritt 1: Einleitung der Reaktanten
- Gasförmige Ausgangsstoffe und Inertgase werden in die Reaktionskammer eingeleitet, in der sich das Substrat befindet.
-
Schritt 2: Aktivierung der Reaktanten
- Die Kammer wird erhitzt und der Druck wird reduziert, um die chemischen Reaktionen zu aktivieren. Die Ausgangsstoffe können durch thermische Energie, Plasma oder Katalysatoren aktiviert werden.
-
Schritt 3: Oberflächenreaktion und Abscheidung
- Die aktivierten Vorläufer reagieren mit der Substratoberfläche und bilden eine dünne Schicht des gewünschten Materials.
-
Schritt 4: Beseitigung von Nebenprodukten
- Die gasförmigen Nebenprodukte werden aus der Kammer abgesaugt, um Verunreinigungen und Umweltbelastungen zu vermeiden.
-
Schritt 1: Einleitung der Reaktanten
-
Vorteile der CVD-Beschichtung
- Gleichmäßige Bedeckung: Mit CVD können komplexe Geometrien beschichtet werden, darunter Innenflächen, Gewinde und Sacklöcher.
- Hervorragende Adhäsion: Die Beschichtung ist chemisch mit dem Substrat verbunden, was eine ausgezeichnete Haltbarkeit gewährleistet.
- Vielseitigkeit: Geeignet für eine Vielzahl von Werkstoffen und Anwendungen, einschließlich Schneidwerkzeugen, Halbleitern und Komponenten für die Luft- und Raumfahrt.
-
Beschränkungen der CVD-Beschichtung
- Hohe Temperaturen: Das Verfahren erfordert hohe Temperaturen, was die Art der zu beschichtenden Grundmaterialien einschränken kann.
- Reaktivitätseinschränkungen: Einige Materialien können ungünstig mit den Vorläufergasen oder dem Beschichtungsverfahren reagieren.
- Umweltaspekte: Um Umweltverschmutzung zu vermeiden, ist eine ordnungsgemäße Handhabung und Entsorgung der gasförmigen Nebenprodukte erforderlich.
-
Anwendungen der CVD-Beschichtung
- Werkzeugherstellung: CVD-Beschichtungen werden häufig eingesetzt, um die Leistung und Lebensdauer von Schneidwerkzeugen, Bohrern und Einsätzen zu verbessern.
- Luft- und Raumfahrt und Automobilindustrie: Beschichtungen bieten Verschleißfestigkeit, Wärmeschutz und Korrosionsbeständigkeit für kritische Komponenten.
- Halbleiter: CVD wird für die Abscheidung dünner Schichten für elektronische und optoelektronische Geräte verwendet.
-
Vergleich mit PVD (Physikalische Abscheidung aus der Gasphase)
- Temperatur: CVD arbeitet bei höheren Temperaturen als PVD, was seine Anwendbarkeit auf bestimmte Materialien einschränken kann.
- Bedeckung: Im Gegensatz zu PVD kann CVD alle Bereiche eines Teils beschichten, auch komplexe Geometrien.
- Haftung: CVD-Beschichtungen weisen aufgrund des chemischen Bindungsprozesses in der Regel eine stärkere Haftung auf.
-
Umwelt- und Sicherheitsaspekte
- Das CVD-Verfahren erfordert einen sorgfältigen Umgang mit Vorläufergasen und Nebenprodukten, um die Sicherheit zu gewährleisten und die Umweltauswirkungen zu minimieren.
- Richtige Belüftung, Abgasbehandlung und die Einhaltung von Sicherheitsprotokollen sind unerlässlich.
Durch das Verständnis des CVD-Beschichtungsprozesses können Käufer von Anlagen und Verbrauchsmaterialien fundierte Entscheidungen über die Eignung für ihre spezifischen Anwendungen treffen und dabei Faktoren wie Materialverträglichkeit, Leistungsanforderungen und Umweltauswirkungen berücksichtigen.
Zusammenfassende Tabelle:
Aspekt | Einzelheiten |
---|---|
Verfahren | Chemische Gasphasenreaktion zur Abscheidung harter Materialschichten. |
Wichtige Komponenten | Vorläufergase, Reaktionskammer, Substrat, Wärmequelle. |
Schritte | 1. Einleitung der Reaktanten 2. Aktivierung 3. Oberflächenreaktion 4. Entfernung des Nebenprodukts. |
Vorteile | Gleichmäßige Abdeckung, hervorragende Haftung, Vielseitigkeit. |
Beschränkungen | Hohe Temperaturen, eingeschränkte Reaktivität, Umweltprobleme. |
Anwendungen | Werkzeugbau, Luft- und Raumfahrt, Automobilbau, Halbleiterindustrie. |
Vergleich mit PVD | Höhere Temperaturen, bessere Abdeckung, stärkere Haftung. |
Sicherheitsaspekte | Richtige Handhabung von Gasen, Belüftung und Abgasbehandlung erforderlich. |
Entdecken Sie, wie die CVD-Beschichtung die Leistung Ihrer Produkte verbessern kann. Kontaktieren Sie unsere Experten noch heute !