Vakuumgießen und Spritzgießen sind zwei unterschiedliche Fertigungsverfahren zur Herstellung von Kunststoff- oder Harzteilen, die jeweils ihre eigenen Vorteile, Einschränkungen und Anwendungen haben. Das Vakuumgießen ist ein Niederdruckverfahren, das sich ideal für die Herstellung von Prototypen und Kleinserien eignet und eine hohe Detailgenauigkeit sowie eine große Materialvielfalt bietet. Das Spritzgießen hingegen ist ein Hochdruckverfahren, das sich für die Massenproduktion eignet und hohe Präzision, Wiederholbarkeit und Kosteneffizienz in großem Maßstab bietet. Die Wahl zwischen den beiden Verfahren hängt von Faktoren wie Produktionsvolumen, Materialanforderungen, Budget und der gewünschten Teilequalität ab. Im Folgenden werden die wichtigsten Unterschiede zwischen diesen Verfahren im Detail erläutert.
Die wichtigsten Punkte werden erklärt:
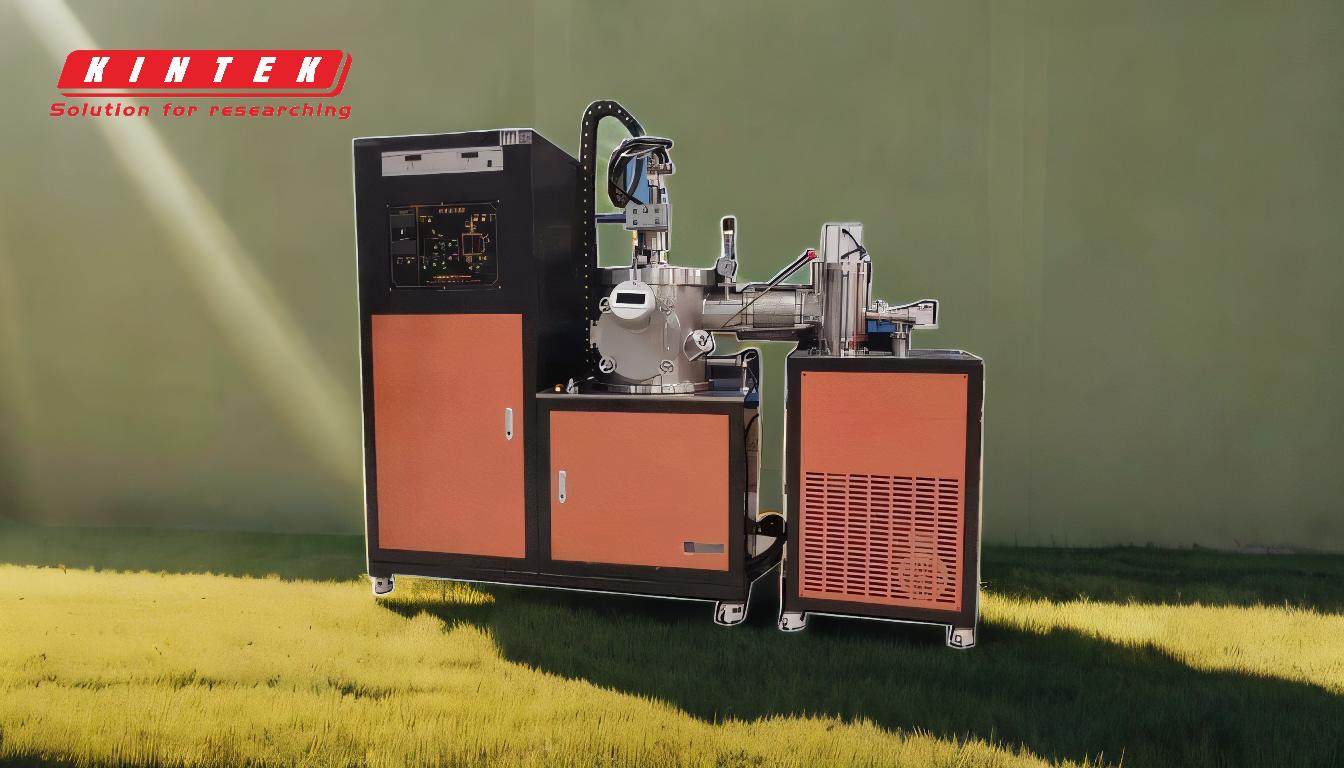
-
Mechanismus des Prozesses:
-
Vakuumgießen:
- Verwendet eine Silikonform, die nach einem (oft 3D-gedruckten) Urmodell erstellt wird.
- Flüssiges Harz wird in die Form gegossen, und ein Vakuum wird angelegt, um Luftblasen zu entfernen und eine glatte und detaillierte Oberfläche zu gewährleisten.
- Die Form wird dann in einem Ofen ausgehärtet, um das Harz zu verfestigen.
-
Spritzgießen:
- Bei diesem Verfahren wird geschmolzener Kunststoff oder Harz unter hohem Druck in eine Stahl- oder Aluminiumform gespritzt.
- Das Material kühlt ab und verfestigt sich in der Form, woraufhin das Teil ausgeworfen wird.
- Dieser Prozess ist hochgradig automatisiert und wiederholbar.
-
Vakuumgießen:
-
Produktionsvolumen:
-
Vakuumgießen:
- Am besten geeignet für kleine bis mittlere Produktionsmengen (typischerweise 10-50 Teile pro Form).
- Silikonformen zersetzen sich mit der Zeit, wodurch die Anzahl der herstellbaren Teile begrenzt ist.
-
Spritzgießen:
- Konzipiert für die Großserienproduktion (Tausende bis Millionen von Teilen).
- Metallformen sind langlebig und können zahlreiche Zyklen ohne nennenswerten Verschleiß überstehen.
-
Vakuumgießen:
-
Material-Optionen:
-
Vakuumgießen:
- Bietet eine breite Palette von Polyurethanharzen an, die verschiedene technische Kunststoffe nachahmen können (z. B. ABS, PP, PC).
- Beschränkt auf Materialien, die bei relativ niedrigen Temperaturen ausgehärtet werden können.
-
Spritzgießen:
- Kompatibel mit einer breiten Palette von Thermoplasten und einigen duroplastischen Materialien.
- Kann Hochleistungsmaterialien wie PEEK, Nylon und Polycarbonat verarbeiten.
-
Vakuumgießen:
-
Kostenüberlegungen:
-
Vakuumgießen:
- Geringere Anschaffungskosten durch kostengünstige Silikonformen.
- Höhere Stückkosten bei größeren Produktionsläufen aufgrund von Formverschleiß und manueller Arbeit.
-
Spritzgießen:
- Hohe Vorlaufkosten für die Werkzeugherstellung (Metallformen).
- Geringere Stückkosten bei Großserienfertigung durch Automatisierung und Materialeffizienz.
-
Vakuumgießen:
-
Qualität und Präzision der Teile:
-
Vakuumgießen:
- Produziert Teile mit ausgezeichneter Oberflächengüte und feinen Details.
- Leichte Abweichungen können aufgrund manueller Prozesse und der Flexibilität der Formen auftreten.
-
Spritzgießen:
- Liefert hohe Präzision und Konsistenz über alle Teile hinweg.
- Ideal für komplexe Geometrien und enge Toleranzen.
-
Vakuumgießen:
-
Vorlaufzeit:
-
Vakuumgießen:
- Kürzere Vorlaufzeit für die Formherstellung (in der Regel 1-2 Wochen).
- Geeignet für Rapid Prototyping und Projekte mit kurzer Durchlaufzeit.
-
Spritzgießen:
- Längere Vorlaufzeit für den Entwurf und die Herstellung von Formen (mehrere Wochen bis Monate).
- Wirtschaftlich nur bei Großserienproduktion.
-
Vakuumgießen:
-
Anwendungen:
-
Vakuumgießen:
- Ideal für das Prototyping, die Funktionsprüfung und die Produktion von Kleinserien.
- Sie werden häufig in Branchen wie der Automobilindustrie, der Unterhaltungselektronik und der Medizintechnik eingesetzt.
-
Spritzgießen:
- Am besten geeignet für die Massenproduktion von Konsumgütern, Automobilkomponenten und Industrieteilen.
- Weit verbreitet in Industrien, die eine hohe und gleichmäßige Leistung erfordern.
-
Vakuumgießen:
-
Auswirkungen auf die Umwelt:
-
Vakuumgießen:
- Erzeugt im Vergleich zum Spritzgießen weniger Abfall.
- Silikonformen sind nicht recycelbar, aber das Verfahren verbraucht weniger Energie.
-
Spritzgießen:
- Kann erheblichen Materialabfall verursachen (z. B. Angüsse und Kufen).
- Energieintensiv aufgrund von Hochdruckmaschinen und Heizbedarf.
-
Vakuumgießen:
Durch das Verständnis dieser Hauptunterschiede können Hersteller und Konstrukteure fundierte Entscheidungen darüber treffen, welches Verfahren am besten für ihre spezifischen Anforderungen geeignet ist, wobei Faktoren wie Kosten, Volumen, Material und Teilequalität berücksichtigt werden.
Zusammenfassende Tabelle:
Aspekt | Vakuumgießen | Spritzgießen |
---|---|---|
Mechanismus des Prozesses | Verwendung von Silikonformen, Vakuum entfernt Luftblasen, Harz härtet im Ofen aus. | Geschmolzener Kunststoff, der unter hohem Druck in Metallformen gespritzt wird. |
Produktionsvolumen | Gering bis mittel (10-50 Teile pro Form). | Hohe Stückzahlen (Tausende bis Millionen von Teilen). |
Material-Optionen | Polyurethanharze, die technische Kunststoffe nachahmen. | Große Auswahl an Thermoplasten und Hochleistungswerkstoffen (z. B. PEEK). |
Kostenüberlegungen | Niedrigere Anfangskosten, höhere Stückkosten bei größeren Auflagen. | Hohe Vorlaufkosten für Werkzeuge, niedrigere Stückkosten für die Massenproduktion. |
Teil Qualität | Ausgezeichnete Oberflächengüte, leichte Abweichungen durch manuelle Bearbeitung. | Hohe Präzision, Konsistenz und enge Toleranzen. |
Vorlaufzeit | Kürzer (1-2 Wochen für die Erstellung der Form). | Länger (mehrere Wochen bis Monate für die Herstellung von Formen). |
Anwendungen | Prototyping, Funktionsprüfung, Kleinserienfertigung. | Massenproduktion von Konsumgütern, Automobil- und Industrieteilen. |
Auswirkungen auf die Umwelt | Weniger Abfall, weniger Energieverbrauch, Silikonformen nicht recycelbar. | Erheblicher Materialabfall, energieintensiver Prozess. |
Sind Sie noch unsicher, welches Verfahren für Ihr Projekt am besten geeignet ist? Kontaktieren Sie unsere Experten noch heute für eine persönliche Beratung!