Die Kalzinierungstemperatur hat einen erheblichen Einfluss auf die Eigenschaften von Nanopartikeln, einschließlich ihrer Größe, Morphologie, Kristallinität und Oberflächeneigenschaften. Höhere Kalzinierungstemperaturen führen im Allgemeinen zu einer höheren Kristallinität und einer geringeren Oberfläche aufgrund von Partikelagglomeration und Sinterung. Zu hohe Temperaturen können jedoch zu unerwünschten Phasenumwandlungen oder Zersetzungen führen. Optimale Kalzinierungstemperaturen sind entscheidend für die Erzielung der gewünschten Eigenschaften, wie z. B. erhöhte katalytische Aktivität oder verbesserte mechanische Festigkeit, je nach Anwendung. Das Verständnis der Beziehung zwischen Kalzinierungstemperatur und Nanopartikeleigenschaften ist für die maßgeschneiderte Anpassung von Materialien an bestimmte Verwendungszwecke von wesentlicher Bedeutung.
Die wichtigsten Punkte werden erklärt:
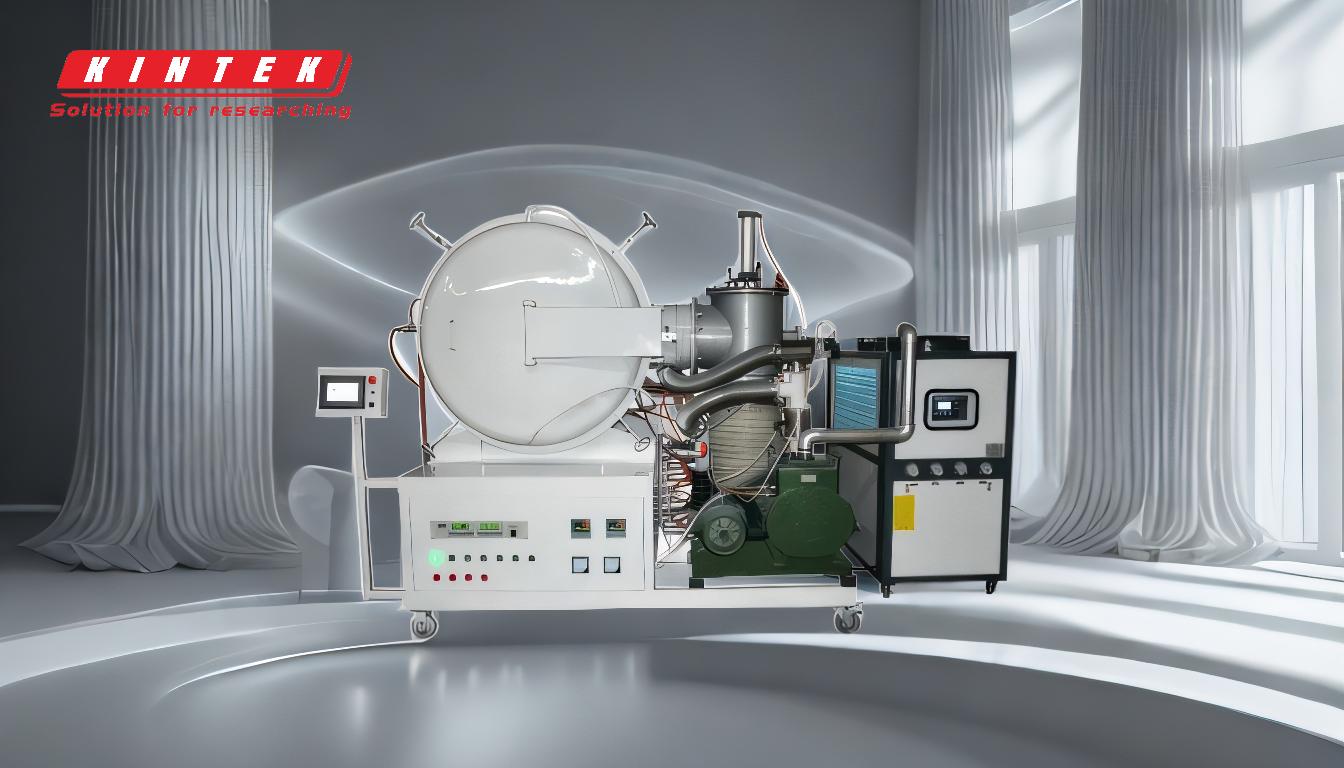
-
Auswirkungen auf Partikelgröße und Agglomeration:
- Höhere Kalzinierungstemperaturen führen häufig zu einer größeren Partikelgröße aufgrund von verstärkter Agglomeration und Sinterung.
- Mit steigender Temperatur neigen die Nanopartikel dazu, miteinander zu verschmelzen, wodurch sich die Oberfläche verkleinert und die Partikelgröße zunimmt.
- Dies kann für Anwendungen, die eine große Oberfläche erfordern, wie Katalyse oder Adsorption, von Nachteil sein.
-
Auswirkungen auf die Kristallinität:
- Das Kalzinieren fördert die Kristallisation, indem es die Energie bereitstellt, die die Atome benötigen, um sich in geordnete Strukturen umzuordnen.
- Höhere Temperaturen verbessern die Kristallinität, was zu definierteren Kristallstrukturen und besseren mechanischen Eigenschaften führt.
- Zu hohe Temperaturen können jedoch zu Phasenumwandlungen oder Zersetzungen führen, wodurch sich die vorgesehenen Eigenschaften des Materials verändern.
-
Oberfläche und Porosität:
- Die Oberfläche nimmt in der Regel mit steigender Kalzinierungstemperatur ab, was auf die Verdichtung der Partikel und den Zusammenbruch der Poren zurückzuführen ist.
- Geringere Oberflächen können die Reaktivität in katalytischen Anwendungen verringern, aber die Stabilität in Hochtemperaturumgebungen verbessern.
- Die Optimierung der Kalzinierungstemperatur ist entscheidend für das Gleichgewicht zwischen Oberfläche und struktureller Integrität.
-
Phasenstabilität und Umwandlung:
- Die Kalzinierungstemperatur kann Phasenumwandlungen bewirken, z. B. die Umwandlung amorpher Materialien in kristalline Phasen oder die Veränderung der Kristallstruktur.
- Bei Metalloxiden zum Beispiel können höhere Temperaturen zur Bildung stabiler Phasen wie Rutil aus Anatas in TiO₂ führen.
- Das Verständnis dieser Umwandlungen ist entscheidend für Anwendungen, die spezifische Phaseneigenschaften erfordern.
-
Thermische und mechanische Eigenschaften:
- Höhere Kalzinierungstemperaturen verbessern in der Regel die thermische Stabilität und die mechanische Festigkeit aufgrund einer verbesserten Kristallinität und geringerer Defekte.
- Zu hohe Temperaturen können jedoch zu Versprödung oder Rissbildung führen und die mechanische Leistung beeinträchtigen.
- Um das gewünschte Gleichgewicht zwischen Festigkeit und Flexibilität zu erreichen, ist die Anpassung der Kalzinierungsbedingungen von entscheidender Bedeutung.
-
Anwendungsspezifische Überlegungen:
- Katalyse: Niedrigere Kalzinierungstemperaturen werden häufig bevorzugt, um eine große Oberfläche und Reaktivität zu erhalten.
- Strukturelle Materialien: Um eine ausreichende mechanische Festigkeit und thermische Stabilität zu erreichen, können höhere Temperaturen erforderlich sein.
- Optische und elektronische Anwendungen: Zur Optimierung von Eigenschaften wie Bandlücke und Leitfähigkeit ist eine genaue Steuerung der Kalzinierungstemperatur erforderlich.
-
Experimentelle Optimierung:
- Forscher verwenden häufig Verfahren wie die thermogravimetrische Analyse (TGA) und die Röntgenbeugung (XRD), um die optimale Kalzinierungstemperatur für ein bestimmtes Material zu ermitteln.
- Es werden systematische Studien durchgeführt, um die Auswirkungen der Temperatur auf Eigenschaften wie Kristallinität, Oberfläche und Phasenzusammensetzung zu bewerten.
Zusammenfassend lässt sich sagen, dass die Kalzinierungstemperatur ein entscheidender Parameter bei der Synthese von Nanopartikeln ist, da sie die Größe, Kristallinität, Oberfläche und Phasenstabilität beeinflusst. Durch die sorgfältige Steuerung dieser Variable können Forscher Nanopartikel für bestimmte Anwendungen maßschneidern und Eigenschaften wie Reaktivität, Festigkeit und thermische Stabilität ausgleichen.
Zusammenfassende Tabelle:
Eigentum | Auswirkung einer höheren Kalzinierungstemperatur | Implikationen für die Anwendung |
---|---|---|
Partikelgröße | Erhöht sich aufgrund von Agglomeration und Sinterung. | Nachteilig bei Bedarf an großer Oberfläche, z. B. in der Katalyse. |
Kristallinität | Verbessert die Kristallinität und damit die mechanischen Eigenschaften. | Günstig für Strukturmaterialien, kann aber bei übermäßigem Einsatz zu einer Verschlechterung der Phasenlage führen. |
Oberfläche und Porosität | Nimmt aufgrund von Verdichtung und Porenkollaps ab. | Reduziert die Reaktivität, verbessert aber die Stabilität in Hochtemperaturumgebungen. |
Phasenstabilität | Löst Phasenumwandlungen aus (z. B. von amorph zu kristallin). | Entscheidend für Anwendungen, die spezifische Phaseneigenschaften erfordern. |
Thermisch und mechanisch | Verbessert die thermische Stabilität und Festigkeit, kann aber bei zu hohen Temperaturen zu Sprödigkeit führen. | Passen Sie die Bedingungen so an, dass ein Gleichgewicht zwischen Kraft und Flexibilität entsteht. |
Anwendungsspezifisch | Unterschiedlich: niedrigere Temperaturen für die Katalyse, höhere für Strukturmaterialien, präzise Steuerung für optische/elektronische Anwendungen. | Optimieren Sie Reaktivität, Festigkeit oder Leitfähigkeit je nach Anwendungsbedarf. |
Benötigen Sie Hilfe bei der Optimierung der Kalzinierungstemperaturen für Ihre Nanopartikelsynthese? Kontaktieren Sie unsere Experten noch heute !