Spark Plasma Sintering (SPS), auch bekannt als Field Assisted Sintering Technique (FAST) oder Direct Current Sintering (DCS), ist ein fortschrittliches Sinterverfahren, das Druck und ein elektrisches Feld kombiniert, um eine schnelle Verdichtung von keramischen und metallischen Pulvern zu erreichen. Bei diesem Verfahren wird ein gepulster Gleichstrom an das Pulver oder den Grünling angelegt, wodurch ein Plasma, eine Joule-Erwärmung und Elektromigrationseffekte entstehen. Diese Effekte führen zu örtlich begrenzten hohen Temperaturen, Oberflächenaktivierung und schneller Partikelbindung, wodurch in kurzer Zeit Materialien mit hoher Dichte entstehen. Trotz des Namens weisen Forschungsergebnisse darauf hin, dass die Plasmaerzeugung nicht der primäre Mechanismus ist, aber das Verfahren bietet dennoch Vorteile wie niedrigere Sintertemperaturen, kürzere Verarbeitungszeiten und Energieeffizienz.
Die wichtigsten Punkte werden erklärt:
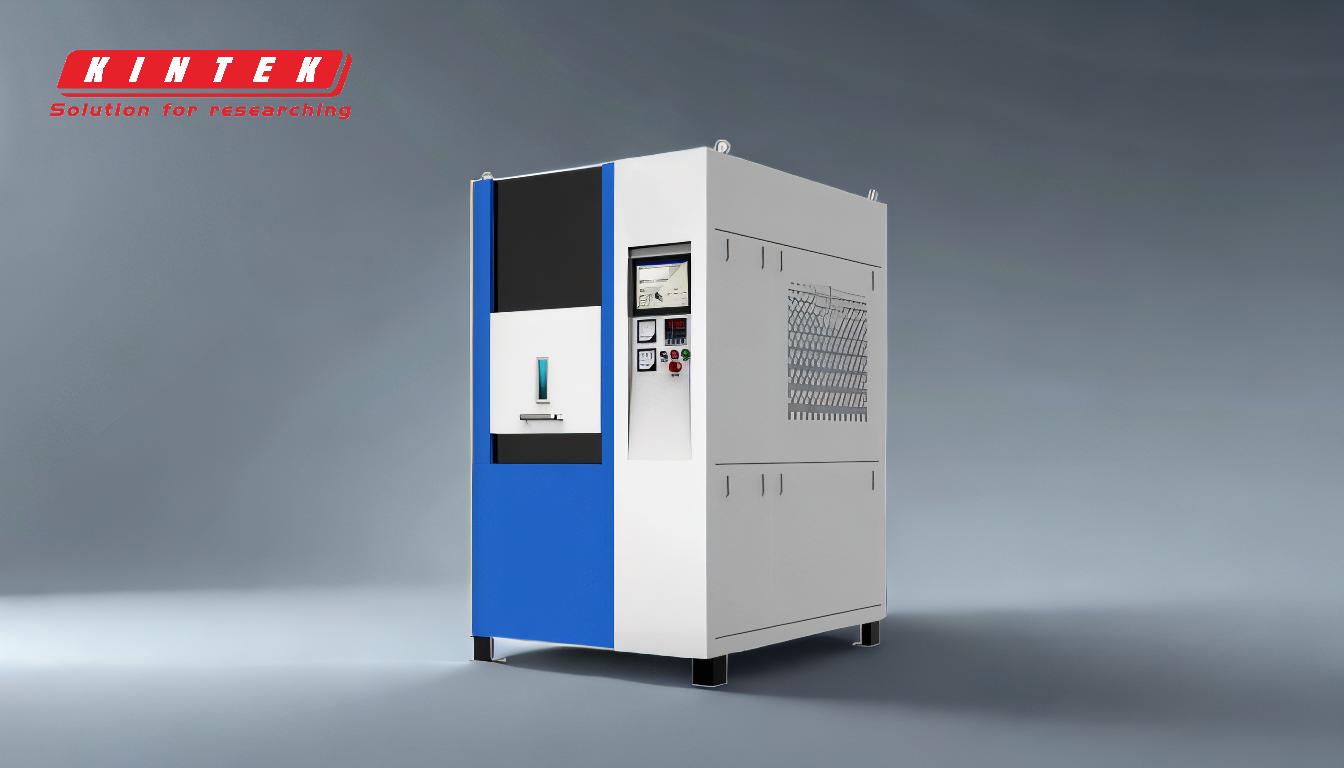
-
Anwendung von gepulstem Gleichstrom (DC):
- Bei SPS wird ein gepulster Gleichstrom direkt auf das Pulver oder den Grünling aufgebracht. Dieser Strom erzeugt lokal hohe Temperaturen und ein Plasma zwischen den Partikeln, was eine schnelle Sinterung ermöglicht.
- Der gepulste Charakter des Stroms ermöglicht eine präzise Steuerung der Aufheiz- und Abkühlraten, so dass das Verfahren in kurzer Zeit eine hohe Verdichtung erreicht.
-
Erzeugung von Plasma und Joule-Erwärmung:
- Der gepulste Strom erzeugt ein Funkenplasma zwischen den Partikeln, das Temperaturen von bis zu 10.000°C (18.032°F) erreicht. Diese hohe Temperatur führt zur Oberflächenaktivierung, zum Schmelzen und zur Bindung der Partikel.
- Die Joule-Erwärmung, die durch den Widerstand des Materials gegenüber dem elektrischen Strom verursacht wird, trägt ebenfalls zur schnellen Erwärmung und Verdichtung des Pulvers bei.
-
Oberflächenaktivierung und Partikelbindung:
- Die durch den gepulsten Strom erzeugten hohen Temperaturen führen dazu, dass die Oberflächen der Partikel schmelzen und "Necks" bilden, d. h. erste Bindungen zwischen den Partikeln. Im Laufe der Zeit entwickeln sich diese Nasen zu festeren Verbindungen, wodurch sich die Gesamtdichte des Materials erhöht.
- Das Verfahren hilft auch bei der Entfernung von Oberflächenverunreinigungen durch Oxidation oder Verdampfung, was zu saubereren und festeren Partikelbindungen führt.
-
Integration von Druck und elektrischem Feld:
- SPS kombiniert die Anwendung von mechanischem Druck mit dem elektrischen Feld, das durch den gepulsten Strom erzeugt wird. Diese Kombination verbessert den Verdichtungsprozess durch Verringerung der Partikellücken und Förderung der Oberflächendiffusion.
- Der während des Sinterns ausgeübte Druck trägt zur Verfestigung der Partikel bei, während das elektrische Feld zur schnellen Erwärmung und Aktivierung der Partikeloberflächen beiträgt.
-
Vorteile von SPS:
- Niedrigere Sintertemperaturen: SPS ermöglicht das Sintern bei Temperaturen, die mehrere hundert Grad niedriger sind als bei herkömmlichen Sinterverfahren, wodurch der Energieverbrauch gesenkt und die thermische Belastung des Materials minimiert wird.
- Kurze Verarbeitungszeit: Die schnellen Aufheiz- und Abkühlraten sowie die kurzen Haltezeiten ermöglichen es, den Prozess in einem Bruchteil der Zeit abzuschließen, die bei herkömmlichen Sinterverfahren benötigt wird.
- Hohe Verdichtung: SPS kann Materialdichten von über 99 % erreichen und eignet sich daher für die Herstellung von Hochleistungskeramiken und -metallen.
- Energieeffizienz und Umweltfreundlichkeit: Das Verfahren ist im Vergleich zum herkömmlichen Sintern energieeffizienter und erzeugt weniger Abfall, was es zu einer umweltfreundlichen Option macht.
-
Mechanismen der Verdichtung:
- Entladungsstoßdruck: Der gepulste Strom erzeugt einen Entladungsstoßdruck, der dazu beiträgt, die Lücken zwischen den Partikeln zu verringern und die Verdichtung zu fördern.
- Elektromigration und Elektroplastizität: Diese durch das elektrische Feld hervorgerufenen Effekte erhöhen die Mobilität von Atomen und Defekten, was eine schnellere Diffusion und Bindung der Partikel ermöglicht.
- Oberflächendiffusion und Grenzdefektdiffusion: Die hohen Temperaturen und das elektrische Feld fördern die Oberflächendiffusion und die Bewegung von Defekten an den Partikelgrenzen, was zu einer schnellen Verdichtung führt.
-
Missverständnisse und alternative Bezeichnungen:
- Trotz des Namens hat die Forschung gezeigt, dass die Erzeugung eines Plasmas nicht der primäre Mechanismus bei SPS ist. Dies hat zur Annahme alternativer Namen wie Field Assisted Sintering Technique (FAST), Electric Field Assisted Sintering (EFAS) und Direct Current Sintering (DCS) geführt.
- Das Verfahren lässt sich genauer als eine Kombination aus elektrisch feldunterstütztem Sintern und Heißpressen beschreiben, bei der das elektrische Feld den Sinterprozess unterstützt, ohne notwendigerweise ein Plasma zu erzeugen.
-
Anwendungen von SPS:
- SPS wird in großem Umfang bei der Herstellung von Hochleistungskeramik, Metallen und Verbundwerkstoffen eingesetzt. Es ist besonders nützlich für Materialien, die eine hohe Dichte, eine feine Kornstruktur und verbesserte mechanische Eigenschaften erfordern.
- Das Verfahren wird auch bei der Entwicklung von Nanomaterialien eingesetzt, bei denen eine genaue Kontrolle der Sinterbedingungen für das Erreichen der gewünschten Materialeigenschaften entscheidend ist.
Zusammenfassend lässt sich sagen, dass das Spark-Plasma-Sintern ein hocheffizientes und vielseitiges Sinterverfahren ist, das die kombinierten Effekte von gepulstem elektrischem Strom, Druck und Joule-Erwärmung nutzt, um eine schnelle Verdichtung von Materialien zu erreichen. Seine Fähigkeit, Materialien mit hoher Dichte bei niedrigeren Temperaturen und in kürzerer Zeit herzustellen, macht es zu einem wertvollen Werkzeug für die Entwicklung fortschrittlicher Materialien.
Zusammenfassende Tabelle:
Wichtige Aspekte | Einzelheiten |
---|---|
Verfahren | Kombiniert gepulsten Gleichstrom, Druck und elektrische Felder zum Sintern. |
Temperaturbereich | Bis zu 10.000°C (18.032°F) für örtliche Erwärmung. |
Verdichtung | Erzielt eine Materialdichte von über 99%. |
Vorteile | Niedrigere Sintertemperaturen, kurze Verarbeitungszeiten, Energieeffizienz. |
Anwendungen | Hochleistungskeramiken, Metalle, Verbundwerkstoffe und Nanomaterialien. |
Erfahren Sie, wie Spark Plasma Sintering Ihre Materialproduktion revolutionieren kann. Kontaktieren Sie unsere Experten noch heute !