Das PVD-Verfahren (Physical Vapor Deposition) ist eine hochentwickelte Methode zur Abscheidung dünner Materialschichten auf einem Substrat.Dabei wird ein festes Material in eine Dampfphase umgewandelt, die dann auf ein Substrat aufgebracht wird, um eine dünne, gleichmäßige Schicht zu bilden.Das Verfahren wird in der Regel in einer Vakuumumgebung durchgeführt, um Reinheit und Kontrolle über die Abscheidung zu gewährleisten.PVD wird in verschiedenen Industriezweigen für Anwendungen wie die Verbesserung der Verschleißfestigkeit, die Erhöhung der Korrosionsbeständigkeit und für dekorative Oberflächen eingesetzt.Das Verfahren umfasst mehrere wichtige Schritte, darunter die Verdampfung des Beschichtungsmaterials, die Migration der verdampften Partikel und die Abscheidung auf dem Substrat.
Die wichtigsten Punkte werden erklärt:
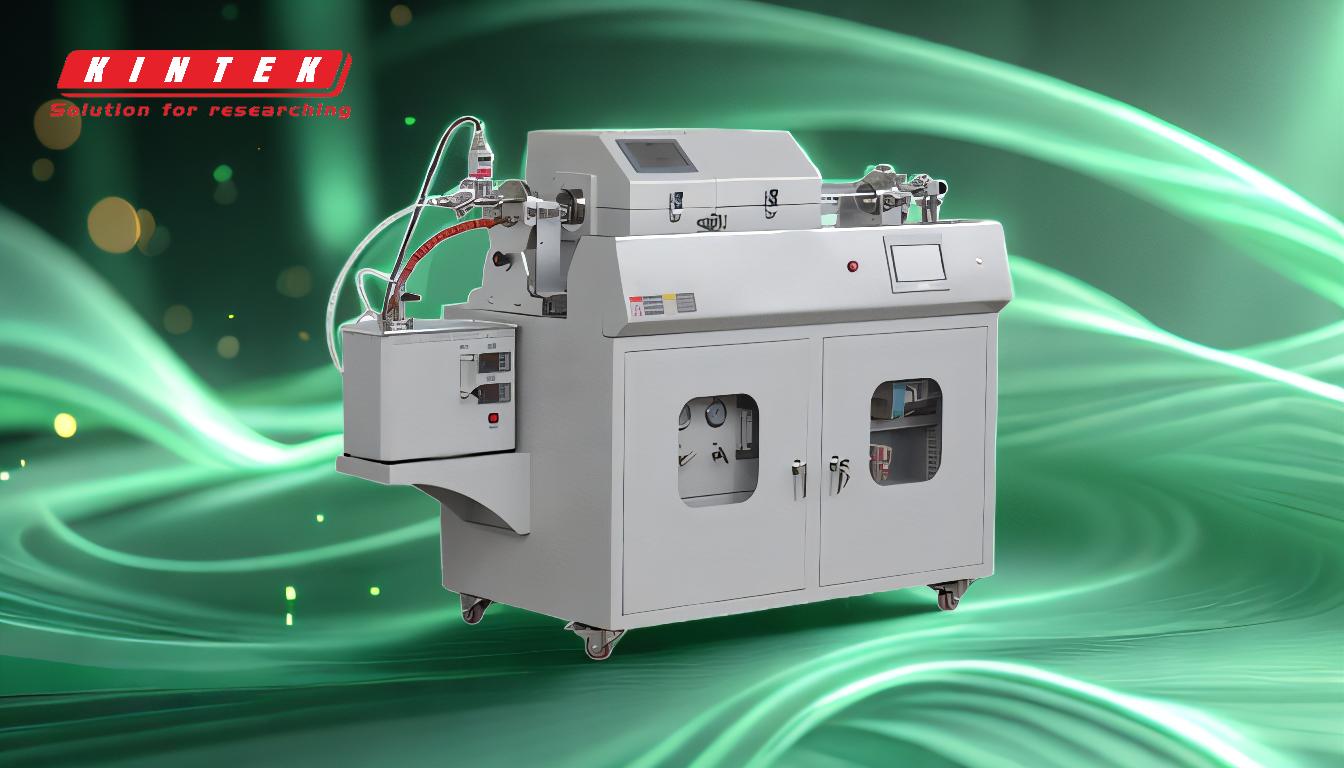
-
Verdampfung von Beschichtungsmaterial:
- Der erste Schritt im PVD-Verfahren ist die Verdampfung des Beschichtungsmaterials.Dies kann durch verschiedene Methoden erreicht werden, darunter Verdampfung, Sputtern oder Laserablation.
- Verdampfung:Das Material wird auf eine hohe Temperatur erhitzt, bis es verdampft.Dies geschieht häufig mit einem Elektronenstrahl oder durch Widerstandserhitzung.
- Sputtern:Das Zielmaterial wird mit hochenergetischen Ionen beschossen, wodurch Atome aus der Oberfläche herausgeschleudert werden und in die Dampfphase übergehen.
- Laserablation:Ein Hochleistungslaser wird verwendet, um das Material direkt zu verdampfen.
-
Migration der verdampften Partikel:
- Sobald sich das Material in der Dampfphase befindet, wandern die Teilchen (Atome, Moleküle oder Ionen) durch die Vakuumkammer.Diese Wanderung wird durch die Vakuumumgebung beeinflusst, die Zusammenstöße mit anderen Teilchen minimiert und eine saubere Abscheidung gewährleistet.
- Während dieser Phase können die verdampften Partikel Reaktionen eingehen, insbesondere wenn reaktive Gase (wie Stickstoff oder Sauerstoff) in die Kammer eingeleitet werden.Bei diesen Reaktionen können sich Verbindungen bilden, die dann auf dem Substrat abgeschieden werden.
-
Ablagerung auf dem Substrat:
- Der letzte Schritt ist die Abscheidung des verdampften Materials auf dem Substrat.Dies geschieht, wenn die verdampften Partikel auf der kühleren Oberfläche des Substrats kondensieren und einen dünnen, gleichmäßigen Film bilden.
- Das Substrat wird in der Regel auf einer im Vergleich zum verdampften Material niedrigeren Temperatur gehalten, was die Kondensation und Haftung der Beschichtung fördert.
- Die Dicke der abgeschiedenen Schicht kann mit Techniken wie der Quarzkristall-Ratenüberwachung, die die Abscheidungsrate misst und bei Bedarf anpasst, genau kontrolliert werden.
-
Einsatz von Plasma und reaktiven Gasen:
- Bei vielen PVD-Verfahren wird Plasma eingesetzt, um den Verdampfungs- und Abscheidungsprozess zu verbessern.Plasma wird durch Ionisierung eines Gases erzeugt, häufig mit einer induktiv gekoppelten Plasmaquelle (ICP).
- Das hochenergetische Plasma kann dazu beitragen, Gasmoleküle in reaktive Spezies zu dissoziieren, die dann mit dem verdampften Material reagieren und Verbindungen bilden können.Dies ist besonders nützlich für die Herstellung harter, verschleißfester Schichten wie Titannitrid (TiN) oder Chromnitrid (CrN).
- Die Einführung reaktiver Gase (z. B. Stickstoff, Sauerstoff) ermöglicht die Bildung von Verbundschichten, die im Vergleich zu reinen Metallschichten bessere Eigenschaften aufweisen können.
-
Vakuumumgebung:
-
Der gesamte PVD-Prozess findet in einer Hochvakuumumgebung statt.Dies ist aus mehreren Gründen entscheidend:
- Reinheit:Das Vakuum minimiert das Vorhandensein von Verunreinigungen und gewährleistet eine saubere Ablagerung.
- Steuerung:Der niedrige Druck ermöglicht eine präzise Steuerung des Abscheidungsprozesses, einschließlich der Geschwindigkeit und Gleichmäßigkeit der Beschichtung.
- Reaktionskontrolle:Die Vakuumumgebung trägt dazu bei, die Reaktionen zwischen dem verdampften Material und den reaktiven Gasen zu kontrollieren, wodurch gleichbleibende Beschichtungseigenschaften gewährleistet werden.
-
Der gesamte PVD-Prozess findet in einer Hochvakuumumgebung statt.Dies ist aus mehreren Gründen entscheidend:
-
Anwendungen von PVD-Beschichtungen:
-
PVD-Beschichtungen werden in einer Vielzahl von Anwendungen eingesetzt, unter anderem:
- Verschleißbeständigkeit:Beschichtungen wie TiN und CrN werden verwendet, um die Verschleißfestigkeit von Schneidwerkzeugen, Formen und anderen Komponenten zu verbessern.
- Korrosionsbeständigkeit:PVD-Beschichtungen können eine Barriere gegen Korrosion bilden und so die Lebensdauer von Komponenten verlängern, die rauen Umgebungen ausgesetzt sind.
- Dekorative Beschichtungen:PVD wird zur Herstellung von dekorativen Beschichtungen mit einer breiten Palette von Farben und Oberflächen verwendet, die häufig in der Unterhaltungselektronik und im Schmuckbereich zu finden sind.
- Optische Beschichtungen:PVD wird verwendet, um dünne Schichten mit bestimmten optischen Eigenschaften abzuscheiden, z. B. Antireflexionsschichten auf Linsen.
-
PVD-Beschichtungen werden in einer Vielzahl von Anwendungen eingesetzt, unter anderem:
Zusammenfassend lässt sich sagen, dass das PVD-Verfahren eine sehr kontrollierte und vielseitige Methode zur Abscheidung dünner Materialschichten auf einem Substrat ist.Es umfasst die Verdampfung des Beschichtungsmaterials, die Migration der verdampften Partikel und die Abscheidung auf dem Substrat, die alle in einer Vakuumumgebung stattfinden.Der Einsatz von Plasma und reaktiven Gasen ermöglicht die Herstellung von Verbundbeschichtungen mit verbesserten Eigenschaften, was PVD zu einer wertvollen Technik für verschiedene industrielle Anwendungen macht.
Zusammenfassende Tabelle:
Wichtige Schritte | Beschreibung |
---|---|
Verdampfung | Das Beschichtungsmaterial wird durch Verdampfen, Sputtern oder Laserablation verdampft. |
Wanderung | Die verdampften Partikel bewegen sich durch ein Vakuum, wodurch Kollisionen minimiert werden. |
Abscheidung | Die Partikel kondensieren auf dem Substrat und bilden einen dünnen, gleichmäßigen Film. |
Plasma und reaktive Gase | Verbessert die Beschichtungseigenschaften, z. B. durch die Bildung von TiN oder CrN zur Erhöhung der Verschleißfestigkeit. |
Vakuumumgebung | Gewährleistet Reinheit, Kontrolle und Reaktionskonsistenz während der Abscheidung. |
Anwendungen | Verschleißfestigkeit, Korrosionsschutz, dekorative Beschichtungen und optische Beschichtungen. |
Entdecken Sie, wie PVD-Beschichtungen Ihre Produkte verbessern können. Kontaktieren Sie unsere Experten noch heute !