Vakuumbedampfung ist ein hochentwickeltes Verfahren zur Erzeugung dünner Filme auf Substraten durch Abscheiden von Material in einer Vakuumumgebung. Aufgrund ihrer Fähigkeit, hochreine, gleichmäßige und haftende Filme herzustellen, wird diese Methode häufig in Branchen wie Elektronik, Optik und Beschichtungen eingesetzt. Der Prozess umfasst die Erzeugung eines Vakuums zur Beseitigung störender Gase, die Vorbereitung des Substrats, das Verdampfen oder Sputtern des Beschichtungsmaterials und dessen Abscheidung auf dem Substrat. Die Wahl der Abscheidungsmethode, beispielsweise der physikalischen Gasphasenabscheidung (PVD) oder der chemischen Gasphasenabscheidung (CVD), hängt von den gewünschten Filmeigenschaften und Anwendungsanforderungen ab. Das Verfahren gewährleistet eine präzise Kontrolle der Filmdicke, Mikrostruktur und Reinheit und ist daher für fortschrittliche Fertigungs- und Materialwissenschaftsanwendungen unerlässlich.
Wichtige Punkte erklärt:
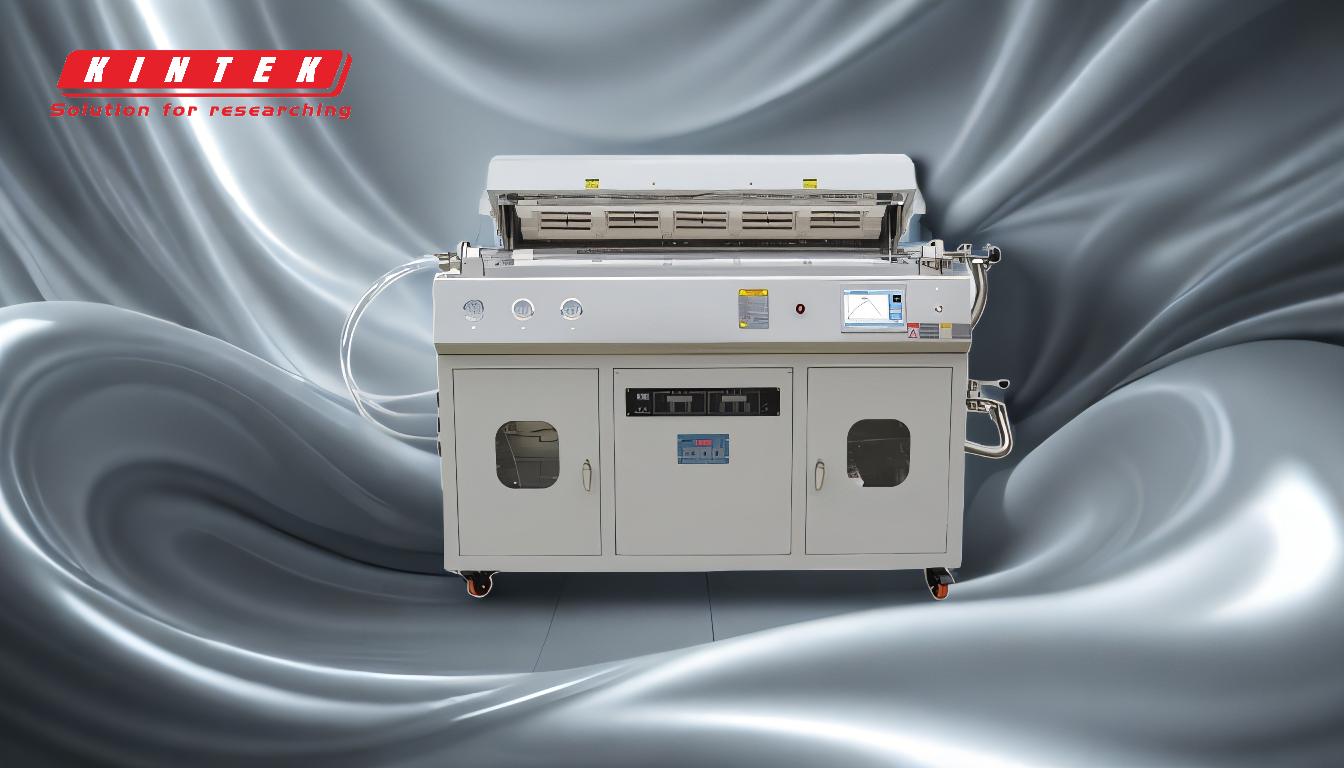
-
Erstellen einer Vakuumumgebung:
- Der erste Schritt bei der Vakuumbedampfung besteht darin, in der Bedampfungskammer ein Vakuum zu erzeugen. Dies geschieht, um Luft und andere Gase zu entfernen, die den Abscheidungsprozess stören könnten. Zum Evakuieren der Kammer wird eine Vakuumpumpe verwendet, um eine kontrollierte Umgebung ohne Verunreinigungen zu gewährleisten. Dieser Schritt ist entscheidend für die Erzielung hochwertiger, gleichmäßiger dünner Filme.
-
Untergrundvorbereitung:
- Vor dem Aufbringen muss der Untergrund gründlich gereinigt und behandelt werden, um eine ordnungsgemäße Haftung des dünnen Films zu gewährleisten. Dies kann chemische Reinigung, Plasmabehandlung oder andere Techniken zur Oberflächenmodifizierung umfassen. Um eine starke Verbindung zwischen Folie und Untergrund zu erreichen, ist eine ordnungsgemäße Untergrundvorbereitung unerlässlich, was sich auf die Haltbarkeit und Leistung der Folie auswirkt.
-
Verdampfen oder Sputtern von Beschichtungsmaterial:
- Das Beschichtungsmaterial wird entweder verdampft oder gesputtert, um einen Dampf zu erzeugen. Beim Verdampfen wird das Material erhitzt, bis es in Dampf übergeht, während beim Sputtern Ionen verwendet werden, um Atome von einem Zielmaterial abzustoßen. Bei beiden Methoden entsteht ein Dampf, der auf dem Substrat abgeschieden werden kann. Die Wahl zwischen Verdampfen und Sputtern hängt von den Materialeigenschaften und den gewünschten Filmeigenschaften ab.
-
Ablagerung von Material auf dem Substrat:
- Das verdampfte Material wird dann auf dem Substrat abgeschieden und bildet einen dünnen Film. Dieser Schritt erfordert eine präzise Steuerung von Parametern wie Temperatur, Druck und Abscheidungsrate, um die Gleichmäßigkeit und Haftung des Films sicherzustellen. Der Abscheidungsprozess kann durch die Ausrichtung des Substrats und die Geometrie der Abscheidungskammer beeinflusst werden.
-
Kühlen und Entlüften des Systems:
- Nach Abschluss der Abscheidung wird das System abgekühlt und die Kammer entlüftet, um wieder Atmosphärendruck zu erreichen. Die Kühlung wird häufig durch die Einführung von Inertgasen wie Argon erreicht, die dazu beitragen, chemische Reaktionen zu verhindern und die Stabilität des abgeschiedenen Films sicherzustellen. Eine ordnungsgemäße Kühlung und Belüftung sind für die Aufrechterhaltung der Integrität des Dünnfilms und die Vorbereitung des Systems auf den nächsten Abscheidungszyklus von entscheidender Bedeutung.
-
Wahl der Abscheidungsmethode:
- Die Auswahl der Abscheidungsmethode (PVD, CVD oder andere) hängt von den spezifischen Anforderungen der Anwendung ab, wie z. B. Filmdicke, Reinheit, Mikrostruktur und Abscheidungsrate. Jede Methode hat ihre Vorteile und Grenzen, und die Wahl wird von Faktoren wie dem abzuscheidenden Material, dem Substrat und den gewünschten Filmeigenschaften beeinflusst.
-
Anwendungen und Bedeutung:
- Vakuumbedampfung ist in verschiedenen Branchen von entscheidender Bedeutung, darunter in der Elektronik (für Halbleitergeräte), in der Optik (für Antireflexbeschichtungen) und in Beschichtungen (für verschleißfeste und dekorative Oberflächen). Die Fähigkeit, qualitativ hochwertige, gleichmäßige dünne Filme mit präziser Kontrolle der Eigenschaften herzustellen, macht diesen Prozess in der modernen Fertigung und Materialwissenschaft unverzichtbar.
Wenn man diese wichtigen Schritte und Überlegungen versteht, kann man die Komplexität und Präzision der Vakuumbedampfung erkennen, die sie zu einem wichtigen Prozess in der modernen Technologie und Industrie macht.
Übersichtstabelle:
Schritt | Beschreibung |
---|---|
1. Ein Vakuum erzeugen | Entfernen Sie Luft und Gase mit einer Vakuumpumpe, um eine kontaminationsfreie Kammer zu gewährleisten. |
2. Untergrundvorbereitung | Reinigen und behandeln Sie den Untergrund, um eine gute Haftung des dünnen Films zu gewährleisten. |
3. Verdampfung/Sputtern | Erhitzen oder ionisieren Sie das Beschichtungsmaterial, um einen Dampf für die Abscheidung zu erzeugen. |
4. Hinterlegung | Tragen Sie das verdampfte Material auf dem Substrat auf, um einen dünnen Film zu bilden. |
5. Kühlung und Belüftung | Kühlen Sie das System ab und entlüften Sie die Kammer, um den abgeschiedenen Film zu stabilisieren. |
6. Abscheidungsmethode | Wählen Sie je nach Anwendungsanforderungen PVD, CVD oder andere Methoden. |
7. Bewerbungen | Wird in der Elektronik, Optik und Beschichtung für hochreine, gleichmäßige Filme verwendet. |
Erfahren Sie, wie Vakuumbedampfung Ihren Herstellungsprozess verbessern kann – Kontaktieren Sie noch heute unsere Experten !