Das Sputtering-Verfahren bei der Magnetron-Beschichtung ist eine Technik der physikalischen Gasphasenabscheidung (PVD), mit der dünne Schichten auf Substraten erzeugt werden.Dabei wird ein Magnetfeld eingesetzt, um die Ionisierung eines Inertgases, in der Regel Argon, zu verstärken, das dann zum Beschuss eines Zielmaterials verwendet wird.Durch den Beschuss werden Atome aus dem Target herausgeschleudert, die sich dann auf einem Substrat ablagern und einen dünnen Film bilden.Das Verfahren ist hochgradig kontrolliert und umfasst Vakuumbedingungen, präzise Temperatureinstellungen und die Anwendung hoher Spannungen zur Erzeugung des Plasmas.Diese Methode ist in der Industrie für die Beschichtung von Materialien weit verbreitet, da sie qualitativ hochwertige, gleichmäßige Schichten erzeugt.
Die wichtigsten Punkte werden erklärt:
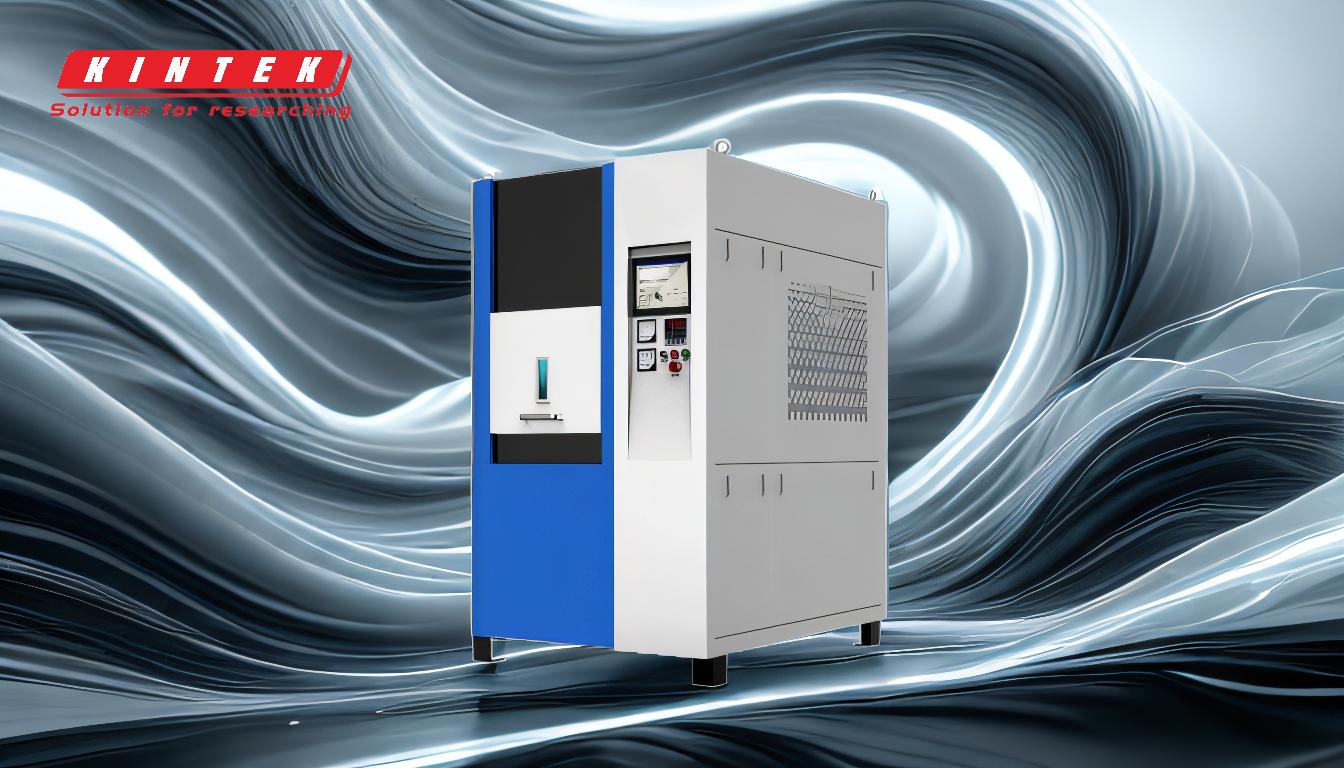
-
Einführung von Inertgas:
- Argon-Gasfluss: Das Verfahren beginnt mit der Einleitung eines Inertgases, in der Regel Argon, in die Vakuumkammer.Dieses Gas wird gewählt, weil es chemisch inert ist und nicht mit dem Zielmaterial oder dem Substrat reagiert.
-
Erzeugung von Plasma:
- Hochspannungsanwendung: Es wird eine Hochspannung angelegt, um in der Kammer ein Plasma zu erzeugen.Dieses Plasma besteht aus Argon-Ionen, freien Elektronen und neutralen Argon-Atomen.
- Einfluss des Magnetfeldes: Das von den Magnetanordnungen (Magnetron) erzeugte Magnetfeld schließt die Elektronen in der Nähe der Targetoberfläche ein, wodurch sich die Ionisierungsrate des Argongases erhöht und die Dichte des Plasmas gesteigert wird.
-
Ionenbombardierung und Sputtern:
- Ionenbeschleunigung: Die positiv geladenen Argon-Ionen werden aufgrund des elektrischen Feldes auf das negativ geladene Target beschleunigt.
- Energieübertragung: Wenn diese Ionen mit dem Target zusammenstoßen, übertragen sie ihre kinetische Energie auf die Targetatome.Wenn die übertragene Energie die Bindungsenergie der Target-Atome übersteigt, werden sie von der Target-Oberfläche ausgestoßen.
-
Abscheidung von gesputterten Atomen:
- Atomauswurf: Die ausgestoßenen Zielatome sind neutral und wandern durch die Vakuumkammer.
- Filmbildung: Diese Atome landen schließlich auf dem Substrat, wo sie kondensieren und einen dünnen Film bilden.Die Gleichmäßigkeit und Qualität der Schicht wird durch Faktoren wie den Einfallswinkel, die Energie der gesputterten Atome und die Substrattemperatur beeinflusst.
-
Die Rolle der Sekundärelektronen:
- Elektronenemission: Während des Ionenbeschusses werden Sekundärelektronen von der Oberfläche des Targets emittiert.Diese Elektronen werden durch das Magnetfeld eingefangen und tragen zur Aufrechterhaltung des Plasmas bei, indem sie weitere Argonatome ionisieren.
-
Prozesskontrollparameter:
- Vakuumbedingungen: In der Kammer herrscht ein Hochvakuum (etwa 1 Pa), um Verunreinigungen zu minimieren und eine saubere Beschichtungsumgebung zu gewährleisten.
- Temperaturregelung: Das Substrat und die Kammer können je nach Material auf bestimmte Temperaturen (150 - 750°C) aufgeheizt werden, um die Schichthaftung und -qualität zu verbessern.
- Stromversorgung: Ein Gleichstromnetzteil wird verwendet, um die erforderliche Hochspannung (3-5 kV) an das Target anzulegen, die für die Ionisierung von Argon und den Sputterprozess entscheidend ist.
-
Vorteile des Magnetronsputterns:
- Hohe Abscheideraten: Das Magnetfeld erhöht die Ionisationseffizienz, was zu höheren Sputtering-Raten führt.
- Gleichmäßige Beschichtungen: Das Verfahren ermöglicht die Abscheidung gleichmäßiger und dichter Schichten, die für Anwendungen, die eine präzise Dicke und hochwertige Oberflächen erfordern, unerlässlich sind.
- Vielseitigkeit: Das Magnetronsputtern kann für eine Vielzahl von Materialien eingesetzt werden, darunter Metalle, Legierungen und Keramiken, was es zu einer vielseitigen Technik für verschiedene industrielle Anwendungen macht.
Wenn man diese Kernpunkte versteht, kann man die Komplexität und Präzision des Magnetron-Sputterverfahrens nachvollziehen, das für die Herstellung von Hochleistungsbeschichtungen in Branchen wie Halbleiter, Optik und dekorative Oberflächen unerlässlich ist.
Zusammenfassende Tabelle:
Schritt | Beschreibung |
---|---|
Einleitung von Inertgas | Zur Ionisierung wird Argongas in die Vakuumkammer eingeleitet. |
Erzeugung eines Plasmas | Hochspannung erzeugt Plasma; das Magnetfeld verstärkt die Ionisierung. |
Ionenbombardement | Argon-Ionen beschießen das Target und schleudern Atome zur Abscheidung aus. |
Filmbildung | Die gesputterten Atome lagern sich auf dem Substrat ab und bilden einen dünnen Film. |
Sekundäre Elektronen | Die Elektronen halten das Plasma aufrecht, indem sie weitere Argonatome ionisieren. |
Kontrollierte Parameter | Vakuum, Temperatur und Hochspannung gewährleisten Präzision und Qualität. |
Vorteile | Hohe Abscheideraten, gleichmäßige Beschichtungen und Materialvielfalt. |
Entdecken Sie, wie Magnetronsputtern Ihre Beschichtungsprozesse verbessern kann. Kontaktieren Sie uns noch heute !