Die Temperatur einer Lötverbindung hängt von der Art des verwendeten Zusatzmetalls und den zu verbindenden Materialien ab. Das Hartlöten erfolgt typischerweise bei Temperaturen über 840 °F (450 °C), aber unterhalb des Schmelzpunkts der Grundmetalle. Die genaue Temperatur wird durch den Schmelzbereich des Zusatzwerkstoffes bestimmt, der je nach Grundwerkstoff und gewünschter Verbindungsfestigkeit gewählt wird. Beispielsweise erfordern Füllmetalle auf Silberbasis möglicherweise Temperaturen zwischen 620 °C (1145 °F) und 815 °C (1500 °F), während Füllmetalle auf Kupferbasis möglicherweise höhere Temperaturen erfordern, etwa 1093 °C (2000 °F). Die richtige Temperaturkontrolle sorgt für eine starke, dauerhafte Verbindung, ohne die Grundmaterialien zu beschädigen.
Wichtige Punkte erklärt:
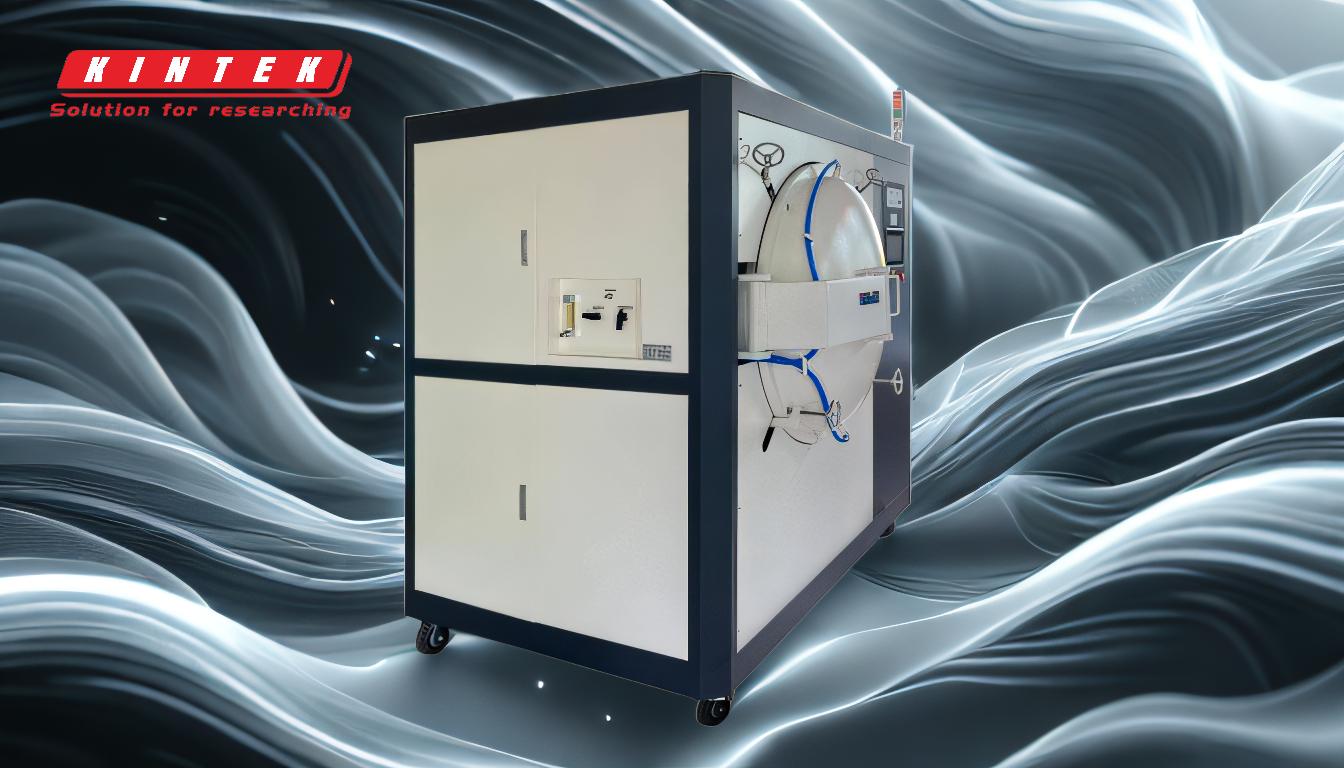
-
Definition der Löttemperatur:
- Beim Hartlöten wird ein Füllmetall auf seinen Schmelzpunkt erhitzt, der durch Kapillarwirkung in die Verbindung fließt. Die Temperatur muss hoch genug sein, um den Füllstoff zu schmelzen, aber niedrig genug, um ein Schmelzen der Grundmetalle zu vermeiden. Dies stellt die Integrität der Verbindung und der zu verbindenden Materialien sicher.
-
Typischer Löttemperaturbereich:
- Das Löten erfolgt im Allgemeinen zwischen 840 °F (450 °C) und 2200 °F (1204 °C), abhängig vom Zusatzmetall und den Grundmaterialien. Die meisten Lötprozesse liegen im Bereich von 1100 °F (593 °C) bis 1500 °F (815 °C).
-
Faktoren, die die Löttemperatur beeinflussen:
- Zusammensetzung des Zusatzmetalls: Unterschiedliche Zusatzmetalle haben unterschiedliche Schmelzpunkte. Beispielsweise schmelzen Füllstoffe auf Silberbasis bei niedrigeren Temperaturen (1145 °F bis 1500 °F), während Füllstoffe auf Kupferbasis höhere Temperaturen erfordern (ca. 2000 °F).
- Grundmaterialien: Die thermischen Eigenschaften der Grundmaterialien, wie z. B. deren Schmelzpunkte und Wärmeleitfähigkeit, beeinflussen die erforderliche Löttemperatur.
- Gemeinsames Design und Anwendung: Auch die Komplexität der Verbindung und der Verwendungszweck des gelöteten Bauteils können Einfluss auf die Temperaturwahl haben.
-
Gängige Zusatzmetalle und ihre Temperaturbereiche:
- Füllstoffe auf Silberbasis: Diese sind aufgrund ihrer niedrigeren Schmelzpunkte (1145 °F bis 1500 °F) beliebt und werden häufig in HLK-, Sanitär- und Elektroanwendungen verwendet.
- Füllstoffe auf Kupferbasis: Diese werden für hochfeste Verbindungen verwendet, erfordern höhere Temperaturen (ca. 2000 °F) und sind in Industrie- und Automobilanwendungen üblich.
- Füllstoffe auf Aluminiumbasis: Diese werden zum Verbinden von Aluminium und seinen Legierungen verwendet und erfordern typischerweise Temperaturen zwischen 1050 °F (566 °C) und 1180 °F (638 °C).
-
Bedeutung der Temperaturkontrolle:
- Eine präzise Temperaturkontrolle ist entscheidend, um sicherzustellen, dass das Zusatzmetall richtig fließt und eine starke Verbindung bildet. Überhitzung kann die Grundmaterialien beschädigen, während unzureichende Hitze zu einer unvollständigen Verbindung führen kann.
-
Erhitzungsmethoden zum Hartlöten:
- Brennerlöten: Verwendet eine Flamme zum Erhitzen der Verbindung, geeignet für kleine oder lokale Anwendungen.
- Ofenlöten: Verwendet eine kontrollierte Umgebung zur gleichmäßigen Erwärmung der Verbindung, ideal für die Massenproduktion oder komplexe Baugruppen.
- Induktionslöten: Nutzt elektromagnetische Induktion, um die Verbindung schnell und effizient zu erwärmen, häufig bei hochpräzisen Anwendungen eingesetzt.
-
Überlegungen nach dem Hartlöten:
- Nach dem Löten sollte die Verbindung langsam abkühlen, um thermische Spannungen und Risse zu vermeiden. Um sicherzustellen, dass die Verbindung den Qualitätsstandards entspricht, sind außerdem eine ordnungsgemäße Reinigung und Inspektion erforderlich.
Wenn Sie diese Schlüsselpunkte verstehen, können Sie die geeignete Löttemperatur und -methode für Ihre spezifische Anwendung auswählen und so eine starke und zuverlässige Verbindung gewährleisten.
Übersichtstabelle:
Faktor | Einzelheiten |
---|---|
Typischer Lötbereich | 840 °F (450 °C) bis 2200 °F (1204 °C) |
Arten von Zusatzwerkstoffen | Silberbasiert (1145°F–1500°F), Kupferbasiert (~2000°F), Aluminiumbasiert (1050°F–1180°F) |
Heizmethoden | Fackel, Ofen, Induktion |
Wichtige Überlegungen | Grundmaterialeigenschaften, Verbindungsdesign und präzise Temperaturkontrolle |
Benötigen Sie Hilfe bei der Auswahl der richtigen Löttemperatur für Ihre Anwendung? Kontaktieren Sie noch heute unsere Experten!