Das Sintern von Eisen ist ein wichtiger Prozess in der Metallurgie, bei dem Eisenerzpartikel auf hohe Temperaturen erhitzt werden, um ein kohäsives Material mit geringer Porosität zu bilden.Der Temperaturbereich für das Sintern von Eisen liegt normalerweise zwischen 1250-1350 °C was hoch genug ist, um die Partikelbindung durch Diffusion zu erleichtern, aber unter dem Schmelzpunkt von Eisen bleibt, um eine Verflüssigung zu vermeiden.Dieser Prozess wird in einem Sinterofen Der Sinterprozess umfasst mehrere Phasen, darunter die Zusammensetzung, die Verdichtung, die Erwärmung und die Abkühlung.Der Sinterprozess umfasst mehrere Phasen, einschließlich Zusammensetzung, Verdichtung, Erhitzung und Abkühlung, die jeweils sorgfältig kontrolliert werden, um optimale Ergebnisse zu erzielen.
Die wichtigsten Punkte erklärt:
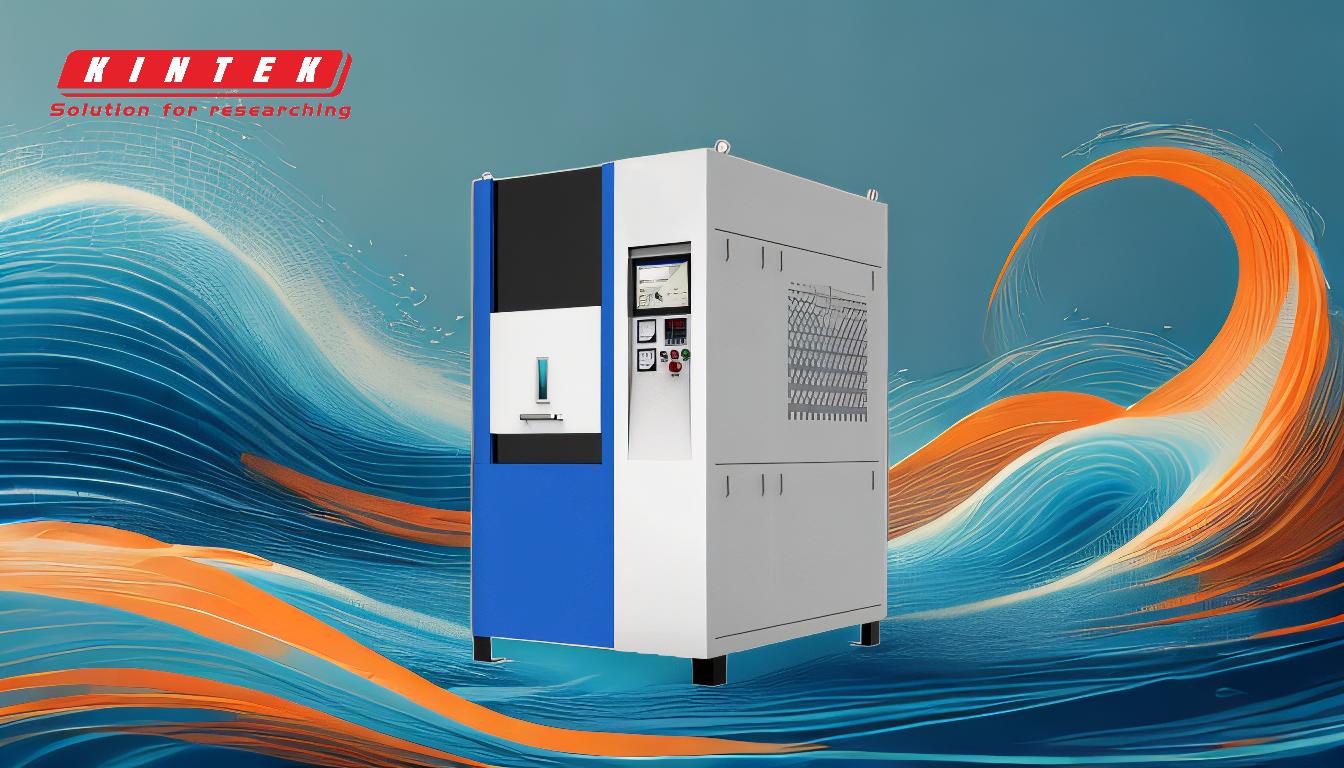
-
Temperaturbereich für das Sintern von Eisen
- Die Temperatur für das Sintern von Eisen liegt normalerweise zwischen 1250-1350 °C .
- Dieser Bereich wurde gewählt, weil er eine ausreichende Diffusion der Atome über die Partikelgrenzen hinweg ermöglicht, so dass sich die Partikel verbinden und eine kohäsive Struktur bilden können.
- Die Temperatur muss unter dem Schmelzpunkt von Eisen bleiben, um eine vollständige Verflüssigung zu verhindern, die den Sinterprozess stören würde.
-
Die Rolle der Temperatur bei der Sinterung
- Die Temperatur ist ein entscheidender Faktor beim Sintern, da sie sich direkt auf die Diffusionsmechanismen auswirkt, z. B. die Korngrenzendiffusion und die Massendiffusion.
- Hohe Temperaturen fördern die Bewegung von Atomen, was zur Bildung von "Nasen" zwischen den Partikeln führt, die für die Verdichtung und Festigkeit wesentlich sind.
- Übermäßig hohe Temperaturen oder lange Heizzeiten können jedoch zu Defekten wie Anbrennen oder verminderten Produkteigenschaften führen.
-
Stadien des Sinterprozesses
- Zusammensetzung:Die Rohstoffe, einschließlich Eisenerz und Kupplungsmittel, werden zu einem einheitlichen Gemisch vermischt.
- Komprimierung:Das Pulver wird mit kontrolliertem Druck in die gewünschte Form gepresst, um Hohlräume zu beseitigen und Gleichmäßigkeit zu gewährleisten.
- Erhitzen:Das verdichtete Material wird in einem Sinterofen auf die erforderliche Temperatur, bei der sich die Partikel durch Diffusion verbinden.
- Kühlung:Das gesinterte Produkt wird abgekühlt und verfestigt sich zu einer starren und kohäsiven Struktur.
-
Die Bedeutung der Temperaturkontrolle
- Die Temperaturkontrolle ist entscheidend, um die gewünschten Eigenschaften des Sinterprodukts wie Dichte, Porosität, Festigkeit und Härte zu erreichen.
- Schwankungen bei der Temperatur oder der Erhitzungszeit können sich erheblich auf die Qualität des Endprodukts auswirken.So können beispielsweise niedrige Temperaturen zu einer unvollständigen Sinterung führen, während zu hohe Temperaturen Defekte verursachen können.
-
Faktoren, die die Sintertemperatur beeinflussen
- Die spezifische Temperatur und die Heizzeit hängen von Faktoren wie der Art des Eisenerzes, der Partikelgröße, der Materialzusammensetzung und der gewünschten Dichte des Endprodukts ab.
- Auch die Sinterumgebung, einschließlich der atmosphärischen Bedingungen im Ofen, spielt eine entscheidende Rolle bei der Bestimmung der optimalen Temperatur.
-
Einfluss der Sintertemperatur auf die Produkteigenschaften
- Porosität und Dichte:Höhere Sintertemperaturen verringern im Allgemeinen die Porosität und erhöhen die Dichte, was zu einem festeren und haltbareren Produkt führt.
- Festigkeit und Härte:Eine ordnungsgemäße Temperaturkontrolle gewährleistet, dass das Sinterprodukt die gewünschten mechanischen Eigenschaften erhält, ohne seine strukturelle Integrität zu beeinträchtigen.
- Defekte:Eine unzureichende Temperaturkontrolle kann zu Problemen wie unvollständiger Sinterung, Verbrennung oder verschlechterten Eigenschaften führen.
-
Anwendungen des Sinterns in der Metallurgie
- Das Sintern ist bei der Herstellung von Eisen- und Stahlerzeugnissen weit verbreitet, wo es die Festigkeit, Haltbarkeit und Leistung des Materials verbessert.
- Das Verfahren wird auch in anderen Industriezweigen angewandt, z. B. in der Keramik- und Pulvermetallurgie, wo eine kontrollierte Erwärmung für die Erzielung bestimmter Materialeigenschaften unerlässlich ist.
Zusammenfassend lässt sich sagen, dass die Temperatur beim Sintern von Eisen sorgfältig kontrolliert wird, und zwar im Bereich von 1250-1350 °C um eine optimale Partikelbindung und Materialeigenschaften zu gewährleisten.Der Prozess umfasst mehrere Stufen, von denen jede einzelne entscheidend für die Qualität des Endprodukts ist.Die Temperaturregelung spielt zusammen mit Faktoren wie Partikelgröße und Materialzusammensetzung eine entscheidende Rolle für den Erfolg des Sinterprozesses.
Zusammenfassende Tabelle:
Hauptaspekt | Einzelheiten |
---|---|
Temperaturbereich | 1250-1350 °C |
Zweck | Erleichtert die Partikelbindung durch Diffusion ohne Verflüssigung |
Stadien der Sinterung | Zusammensetzung, Verdichtung, Erwärmung, Abkühlung |
Kritische Faktoren | Temperaturkontrolle, Partikelgröße, Materialzusammensetzung |
Auswirkungen auf das Produkt | Dichte, Porosität, Festigkeit, Härte und Fehlervermeidung |
Anwendungen | Eisen- und Stahlproduktion, Keramik, Pulvermetallurgie |
Stellen Sie sicher, dass Ihr Sinterprozess optimale Ergebnisse erzielt - Kontaktieren Sie noch heute unsere Experten für maßgeschneiderte Lösungen!