Die Plasmaabscheidung, insbesondere bei Verfahren wie der plasmaunterstützten chemischen Gasphasenabscheidung (PECVD), erfolgt bei wesentlich niedrigeren Temperaturen als die herkömmliche chemische Gasphasenabscheidung (CVD).Während für die CVD-Beschichtung in der Regel Temperaturen um 1000 °C erforderlich sind, können mit der Plasmabeschichtung ähnliche Ergebnisse bei viel niedrigeren Temperaturen, oft zwischen 200 und 400 °C, erzielt werden.Dies liegt daran, dass das Plasma die notwendige Energie für die Aktivierung chemischer Reaktionen liefert, ohne sich ausschließlich auf thermische Energie zu verlassen.Der niedrigere Temperaturbereich ist vorteilhaft für Substrate, die hohen Temperaturen nicht standhalten können, wie z. B. Polymere oder bestimmte Metalle.Außerdem ermöglicht der Einsatz von Plasma eine bessere Kontrolle der Schichteigenschaften und verringert die thermische Belastung, die bei Hochtemperaturverfahren wie CVD häufig auftritt.
Die wichtigsten Punkte erklärt:
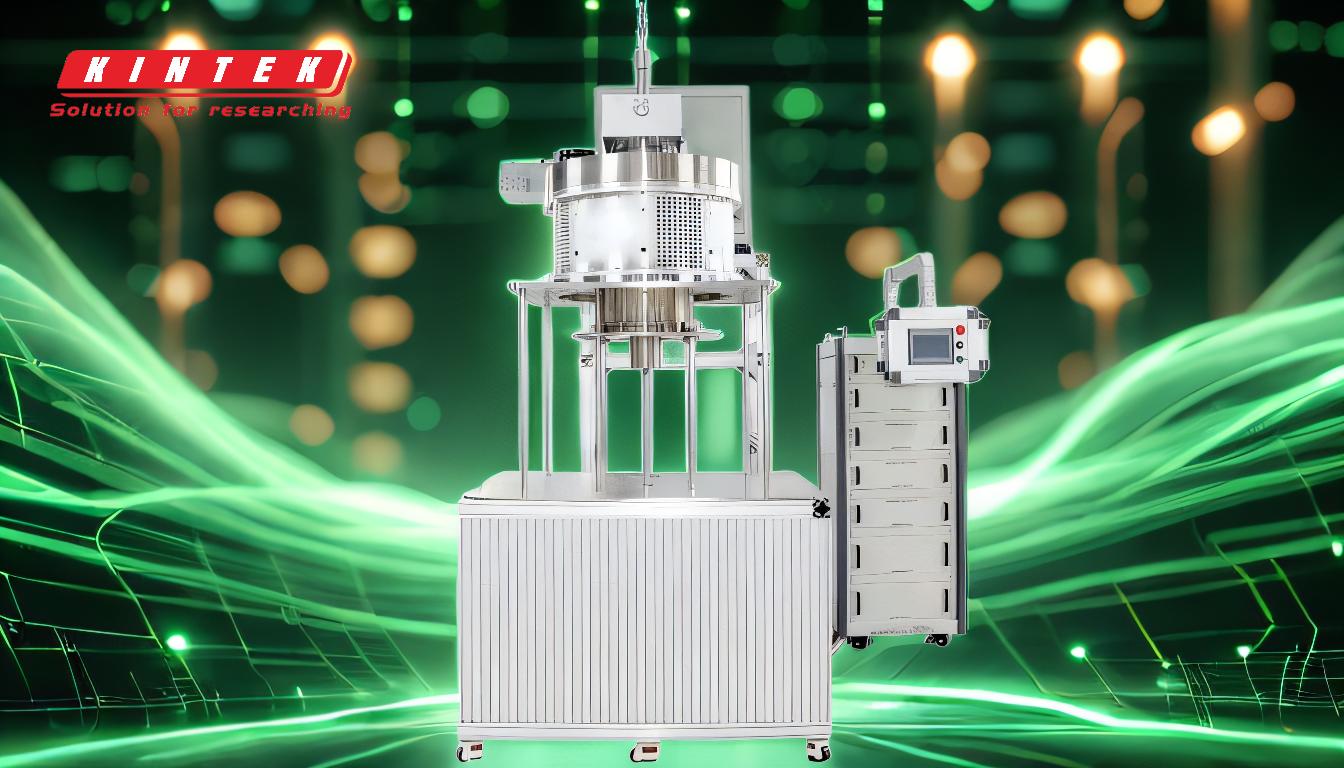
-
Temperaturbereich bei der Plasmabeschichtung:
- Die Plasmabeschichtung, einschließlich PECVD, erfolgt in der Regel bei Temperaturen zwischen 200 und 400 °C.Dies ist deutlich niedriger als die 1000 °C, die für die traditionelle chemischen Gasphasenabscheidung (CVD).
- Die niedrigere Temperatur wird dadurch erreicht, dass die für die chemischen Reaktionen benötigte Energie durch ein Plasma bereitgestellt wird und nicht allein durch thermische Energie.
-
Vorteile der niedrigeren Temperaturen:
- Kompatibilität der Substrate:Viele Substrate, z. B. Polymere und bestimmte Metalle, vertragen die für die CVD erforderlichen hohen Temperaturen nicht.Mit der Plasmabeschichtung können diese Materialien ohne Beschädigung beschichtet werden.
- Reduzierte thermische Belastung:Hohe Temperaturen können aufgrund von Unterschieden in der Wärmeausdehnung zwischen dem Substrat und der abgeschiedenen Schicht zu thermischen Spannungen führen.Niedrigere Temperaturen bei der Plasmabeschichtung minimieren dieses Problem und führen zu einer besseren Schichthaftung und weniger Defekten.
-
Vergleich mit CVD:
- Temperatur:CVD-Prozesse erfordern in der Regel Temperaturen um 1000°C, was weit über dem Temperaturbereich von 200-400°C bei der Plasmabeschichtung liegt.
- Energiequelle:Bei der CVD werden die chemischen Reaktionen durch thermische Energie angetrieben, während bei der Plasmabeschichtung die Energie durch das Plasma bereitgestellt wird, was niedrigere Temperaturen ermöglicht.
- Anwendungen:Der niedrigere Temperaturbereich der Plasmabeschichtung macht sie für ein breiteres Spektrum von Anwendungen geeignet, auch für solche mit temperaturempfindlichen Materialien.
-
Erwägungen zur thermischen Belastung:
- Bei der CVD-Beschichtung sind thermische Spannungen ein großes Problem, insbesondere während der Abkühlphase nach der Abscheidung.Die unterschiedlichen Wärmeausdehnungskoeffizienten von Substrat und Schicht können zu Rissen oder Delamination führen.
- Die Plasmabeschichtung verringert das Risiko thermischer Spannungen, da sie bei niedrigeren Temperaturen durchgeführt wird, was den Unterschied im Wärmeausdehnungskoeffizienten minimiert und zu stabileren Schichten führt.
-
Prozesskontrolle und Filmeigenschaften:
- Der Einsatz von Plasma in Abscheidungsprozessen ermöglicht eine bessere Kontrolle der Schichteigenschaften wie Dicke, Gleichmäßigkeit und Zusammensetzung.
- Die niedrigeren Temperaturen ermöglichen auch eine präzisere Kontrolle über den Abscheidungsprozess, wodurch die Wahrscheinlichkeit unerwünschter Nebenreaktionen oder einer Schädigung des Substrats verringert wird.
Zusammenfassend lässt sich sagen, dass die Plasmaabscheidung eine Alternative zu herkömmlichen CVD-Verfahren mit niedrigeren Temperaturen darstellt und sich daher für eine breitere Palette von Materialien und Anwendungen eignet.Die Verwendung von Plasma als Energiequelle ermöglicht eine präzise Steuerung des Abscheidungsprozesses, was zu hochwertigen Schichten mit minimaler thermischer Belastung führt.Dies macht die Plasmabeschichtung zu einer attraktiven Option für Branchen, die Beschichtungen auf temperaturempfindlichen Substraten benötigen.
Zusammenfassende Tabelle:
Aspekt | Plasma-Beschichtung | Traditionelle CVD |
---|---|---|
Temperaturbereich | 200-400°C | ~1000°C |
Energiequelle | Plasma | Thermische Energie |
Kompatibilität der Substrate | Polymere, Metalle | Begrenzt durch hohe Temperaturen |
Thermische Belastung | Minimal | Hohes Risiko |
Anwendungen | Breite, empfindliche Materialien | Hochtemperatur-Materialien |
Erfahren Sie, wie die Plasmabeschichtung Ihren Materialbeschichtungsprozess verbessern kann. Kontaktieren Sie unsere Experten noch heute !