Der Vakuumglühprozess ist eine spezielle Wärmebehandlungsmethode, die in einer Vakuumumgebung durchgeführt wird, um die Eigenschaften von Metallen und Legierungen zu verbessern. Dabei wird das Material auf eine bestimmte Temperatur erhitzt, dort gehalten, um strukturelle Veränderungen zu ermöglichen, und dann langsam abgekühlt. Dieser Prozess wird in einem Vakuumglühofen durchgeführt, der eine kontaminationsfreie Umgebung, eine präzise Temperaturkontrolle und eine gleichmäßige Erwärmung gewährleistet. Die Vakuumumgebung verhindert Oxidation und andere chemische Reaktionen, was zu einer höheren Reinheit und verbesserten mechanischen Eigenschaften des behandelten Materials führt. Vakuumglühen wird häufig in Branchen eingesetzt, die hochwertige Materialien erfordern, beispielsweise in der Luft- und Raumfahrt, der Elektronik und der Herstellung medizinischer Geräte.
Wichtige Punkte erklärt:
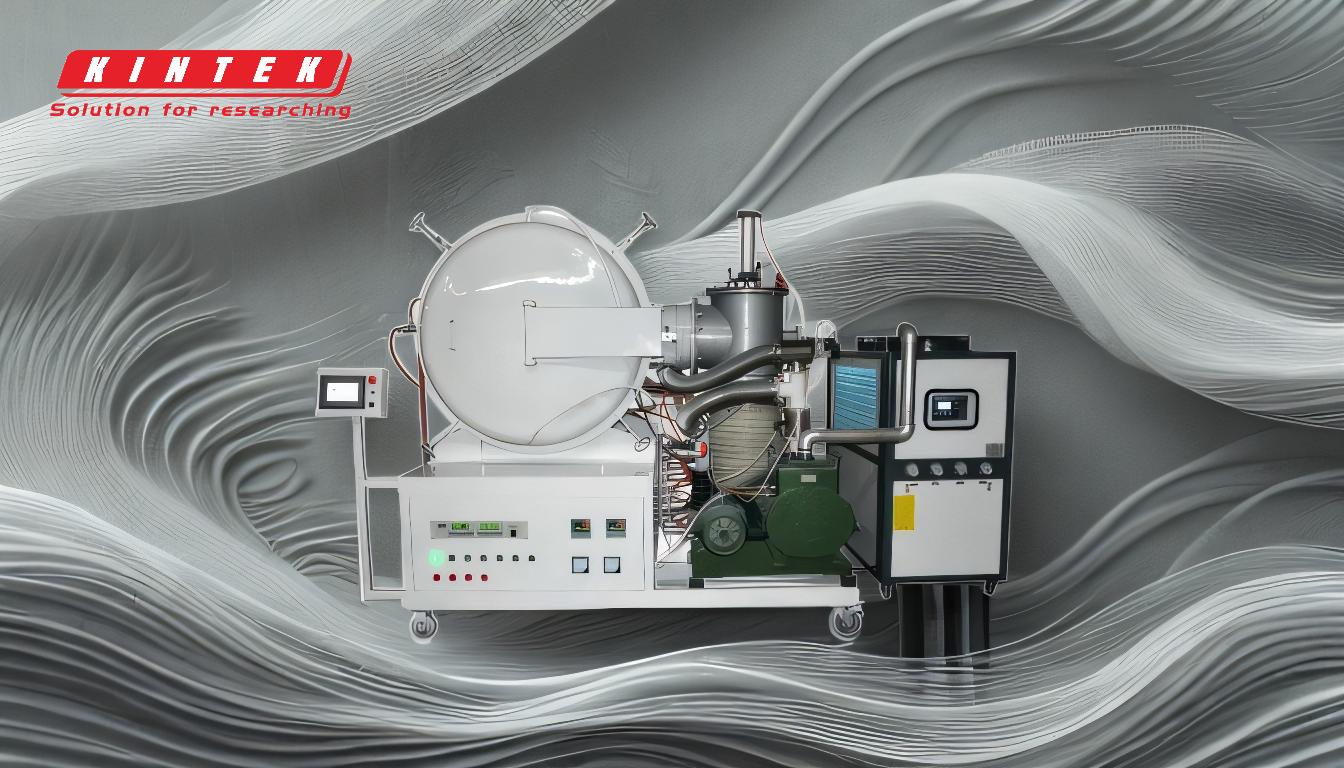
-
Was ist Vakuumglühen?
- Vakuumglühen ist ein Wärmebehandlungsprozess, bei dem Materialien in einer Vakuumumgebung auf eine bestimmte Temperatur erhitzt, auf dieser Temperatur gehalten und dann langsam abgekühlt werden. Dieser Prozess verbessert die Duktilität des Materials, baut innere Spannungen ab und verbessert seine mechanischen oder elektrischen Eigenschaften. Die Vakuumumgebung verhindert Oxidation und Kontamination und sorgt so für ein hochreines Endprodukt.
-
Rolle des Vakuumglühofens:
- Der Vakuumglühofen ist die Kernausrüstung, die in diesem Prozess verwendet wird. Es sorgt für eine kontrollierte Umgebung mit gleichmäßiger Erwärmung und präziser Temperaturregulierung. Der Ofen umfasst typischerweise eine Vakuumkammer, Heizelemente und Kühlsysteme. Die Vakuumumgebung eliminiert das Vorhandensein von Sauerstoff und anderen reaktiven Gasen, verhindert Oxidation und gewährleistet einen sauberen, kontaminationsfreien Prozess.
-
Wichtige Schritte im Vakuumglühprozess:
- Heizung: Das Material wird auf eine Temperatur erhitzt, die über seinem Rekristallisationspunkt, aber unter seinem Schmelzpunkt liegt. Dadurch wird die kristalline Struktur flüssig und Defekte können sich selbst reparieren.
- Einweichen: Das Material wird für eine bestimmte Zeit auf der Zieltemperatur gehalten, um eine gleichmäßige Erwärmung und Strukturveränderung zu gewährleisten.
- Kühlung: Das Material wird entweder im Ofen oder unter Verwendung von Inertgas langsam abgekühlt, um die gewünschte Kristallstruktur und die gewünschten Eigenschaften zu erreichen.
-
Vorteile des Vakuumglühens:
- Kontaminationsfreie Umgebung: Das Vakuum verhindert Oxidation und andere chemische Reaktionen, was zu einer höheren Reinheit führt.
- Präzise Temperaturregelung: Eine gleichmäßige Erwärmung sorgt für gleichbleibende Materialeigenschaften.
- Verbesserte Materialeigenschaften: Verbesserte Duktilität, geringere innere Spannungen und bessere mechanische oder elektrische Eigenschaften.
- Schnellkühloptionen: Inertgas-Abschrecksysteme ermöglichen eine schnellere Abkühlung und verkürzen so die Prozesszykluszeiten.
-
Anwendungen des Vakuumglühens:
-
Vakuumglühen wird in Branchen eingesetzt, die hochwertige Materialien mit präzisen Eigenschaften benötigen, wie zum Beispiel:
- Luft- und Raumfahrt: Für Komponenten, die eine hohe Festigkeit und Ermüdungsbeständigkeit erfordern.
- Elektronik: Für Halbleitermaterialien und leitfähige Legierungen.
- Medizinische Geräte: Für Implantate und chirurgische Instrumente, die Biokompatibilität und Korrosionsbeständigkeit erfordern.
- Werkzeuge: Zur Verbesserung der Haltbarkeit und Leistung von Schneidwerkzeugen und Matrizen.
-
Vakuumglühen wird in Branchen eingesetzt, die hochwertige Materialien mit präzisen Eigenschaften benötigen, wie zum Beispiel:
-
Vergleich mit anderen Glühmethoden:
- Im Gegensatz zu herkömmlichen Glühmethoden, die in Luft- oder Schutzgasatmosphären durchgeführt werden, bietet das Vakuumglühen eine bessere Kontrolle über die Umgebung. Dies führt zu weniger Verunreinigungen, besseren Oberflächengüten und gleichmäßigeren Materialeigenschaften. Die Abwesenheit von Sauerstoff und anderen reaktiven Gasen eliminiert das Risiko einer Oxidation und Entkohlung.
-
Bedeutung der Kühlung beim Vakuumglühen:
- Die Kühlung ist ein entscheidender Schritt im Vakuumglühprozess. Durch langsames Abkühlen entwickelt das Material eine duktilere und gleichmäßigere Kristallstruktur. In einigen Fällen wird eine schnelle Abkühlung (Abschrecken) mit Inertgasen eingesetzt, um bestimmte Materialeigenschaften, wie beispielsweise eine erhöhte Härte, zu erreichen.
Durch die Nutzung der Fähigkeiten eines Vakuumglühofen können Hersteller überlegene Materialeigenschaften erreichen und so sicherstellen, dass ihre Produkte den strengen Anforderungen moderner Industrien entsprechen.
Übersichtstabelle:
Aspekt | Einzelheiten |
---|---|
Definition | Wärmebehandlung im Vakuum zur Verbesserung der Materialeigenschaften. |
Schlüsselausrüstung | Vakuum-Glühofen für kontaminationsfreies, präzises Erhitzen. |
Prozessschritte | Erhitzen, Einweichen und langsames Abkühlen in einer Vakuumumgebung. |
Vorteile | Kontaminationsfrei, präzise Temperaturregelung, verbesserte Materialqualität. |
Anwendungen | Luft- und Raumfahrt, Elektronik, medizinische Geräte und Werkzeugindustrie. |
Kühlbedeutung | Entscheidend für das Erreichen der gewünschten Kristallstruktur und Eigenschaften. |
Erfahren Sie, wie Vakuumglühen Ihre Materialqualität verbessern kann – Kontaktieren Sie noch heute unsere Experten !