Die Abscheidung von Dünnschichten ist ein wichtiger Prozess in verschiedenen Branchen, darunter Halbleiter, Optik und Beschichtungen.Die für die Abscheidung von Dünnschichten verwendeten Methoden lassen sich grob in folgende Kategorien einteilen chemische und physikalische Abscheidungstechniken .Chemische Verfahren beinhalten chemische Reaktionen oder Lösungen zur Bildung dünner Schichten, während physikalische Verfahren auf physikalischen Prozessen wie Verdampfen oder Sputtern beruhen.Gängige chemische Verfahren sind Chemische Gasphasenabscheidung (CVD) , Atomlagenabscheidung (ALD) und Sol-Gel während physikalische Methoden Physikalische Gasphasenabscheidung (PVD) , thermische Verdampfung und Sputtern .Jede Methode hat ihre Vorteile und wird auf der Grundlage der gewünschten Filmeigenschaften, des Substratmaterials und der Anwendungsanforderungen ausgewählt.
Die wichtigsten Punkte erklärt:
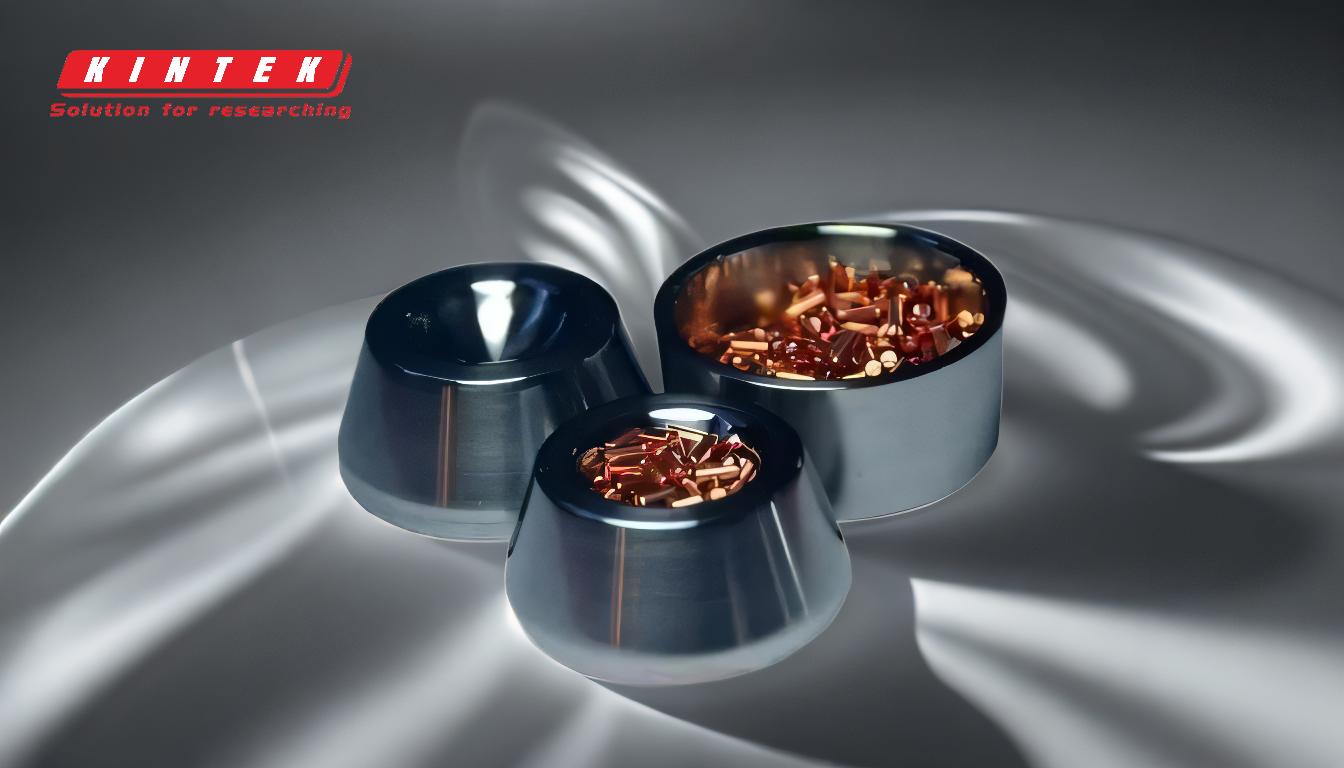
-
Chemische Abscheidungsmethoden
Diese Verfahren beruhen auf chemischen Reaktionen oder Lösungen zur Abscheidung dünner Schichten.Sie sind wegen ihrer Präzision und ihrer Fähigkeit, gleichmäßige Schichten zu erzeugen, weit verbreitet.-
Chemische Gasphasenabscheidung (CVD):
- Chemische Reaktionen zwischen gasförmigen Vorläufersubstanzen zur Bildung eines festen, dünnen Films auf einem Substrat.
- Aufgrund der hohen Präzision und der Fähigkeit, komplexe Materialien abzuscheiden, wird es häufig in der Halbleiterindustrie eingesetzt.
-
Plasma-unterstützte CVD (PECVD):
- Eine Variante der CVD, bei der ein Plasma zur Verbesserung der chemischen Reaktion eingesetzt wird, was die Abscheidung bei niedrigeren Temperaturen ermöglicht.
-
Atomlagenabscheidung (ALD):
- Beschichtet eine Atomschicht nach der anderen und bietet eine außergewöhnliche Kontrolle über Schichtdicke und Gleichmäßigkeit.
- Ideal für Anwendungen, die ultradünne, konforme Beschichtungen erfordern.
-
Sol-Gel, Dip Coating und Spin Coating:
- Bei diesen Verfahren wird eine flüssige Lösung auf das Substrat aufgetragen und anschließend durch Trocknen oder Aushärten verfestigt.
- Sie werden häufig für optische Beschichtungen und kostengünstige Anwendungen eingesetzt.
-
Chemische Gasphasenabscheidung (CVD):
-
Physikalische Abscheidungsmethoden
Bei diesen Verfahren kommen physikalische Prozesse zur Abscheidung dünner Schichten zum Einsatz, z. B. Verdampfen oder Sputtern.Sie sind für die Herstellung hochreiner Schichten bekannt.-
Physikalische Gasphasenabscheidung (PVD):
- Umfasst Techniken wie Sputtern , thermische Verdampfung und Elektronenstrahlverdampfung .
- Beim Sputtern wird ein Zielmaterial mit Ionen beschossen, um Atome auszustoßen, die sich dann auf dem Substrat ablagern.
- Bei der thermischen und der Elektronenstrahlverdampfung wird das Material erhitzt, bis es verdampft, und dann auf dem Substrat kondensiert.
-
Gepulste Laserabscheidung (PLD):
- Mit einem Hochenergielaser wird das Zielmaterial verdampft und ein dünner Film auf dem Substrat gebildet.
- Geeignet für die Abscheidung von komplexen Materialien wie Oxiden und Supraleitern.
-
Molekularstrahlepitaxie (MBE):
- Ein hochpräzises Verfahren zur Herstellung kristalliner Dünnschichten, das häufig bei Halbleiter- und optoelektronischen Anwendungen eingesetzt wird.
-
Physikalische Gasphasenabscheidung (PVD):
-
Vergleich der Methoden
-
Präzision und Gleichmäßigkeit:
- Chemische Verfahren wie CVD und ALD bieten eine überragende Präzision und Gleichmäßigkeit und sind daher ideal für Halbleiter- und Nanotechnologieanwendungen.
- Physikalische Verfahren wie Sputtern und Aufdampfen eignen sich besser für Anwendungen, die hochreine Schichten erfordern.
-
Temperaturanforderungen:
- CVD und ALD erfordern oft hohe Temperaturen, während PECVD und physikalische Verfahren bei niedrigeren Temperaturen arbeiten können.
-
Kosten und Skalierbarkeit:
- Chemische Verfahren wie Sol-Gel und Tauchbeschichtung sind für großtechnische Anwendungen kostengünstig, während physikalische Verfahren wie MBE und PLD zwar teurer sind, aber eine höhere Präzision bieten.
-
Präzision und Gleichmäßigkeit:
-
Anwendungen der Dünnschichtabscheidung
-
Halbleiter:
- CVD und ALD werden häufig für die Abscheidung dünner Schichten in integrierten Schaltkreisen und in der Mikroelektronik verwendet.
-
Optik:
- Sputtern und Aufdampfen werden zur Herstellung von Antireflex- und Reflexionsschichten für Linsen und Spiegel verwendet.
-
Energie:
- Dünne Schichten werden in Solarzellen, Batterien und Brennstoffzellen verwendet, wobei Verfahren wie Sprühpyrolyse und CVD üblich sind.
-
Beschichtungen:
- PVD-Verfahren wie Sputtern und Kohlenstoffbeschichtung werden für verschleißfeste und dekorative Beschichtungen verwendet.
-
Halbleiter:
-
Auswahlkriterien für Beschichtungsmethoden
-
Materialkompatibilität:
- Einige Materialien eignen sich besser für bestimmte Verfahren (z. B. Oxide für PLD, Metalle für Sputtering).
-
Schichtdicke und Gleichmäßigkeit:
- ALD und CVD werden für ultradünne und gleichmäßige Schichten bevorzugt.
-
Empfindlichkeit des Substrats:
- Niedertemperaturverfahren wie PECVD sind ideal für wärmeempfindliche Substrate.
-
Kosten und Durchsatz:
- Für die Großserienproduktion werden kostengünstige Verfahren wie Sol-Gel und Tauchbeschichtung bevorzugt.
-
Materialkompatibilität:
Wenn Sie die Stärken und Grenzen der einzelnen Beschichtungsmethoden kennen, können Sie die für Ihre spezielle Anwendung am besten geeignete Technik auswählen und so optimale Leistung und Kosteneffizienz gewährleisten.
Zusammenfassende Tabelle:
Kategorie | Methoden | Wesentliche Merkmale | Anwendungen |
---|---|---|---|
Chemische Abscheidung | CVD, PECVD, ALD, Sol-Gel, Tauchbeschichtung, Spin-Beschichtung | Hochpräzise, gleichmäßige Beschichtungen, Niedertemperaturoptionen (PECVD) | Halbleiter, optische Beschichtungen, kostengünstige großtechnische Anwendungen |
Physikalische Abscheidung | PVD (Sputtern, thermische Verdampfung, Elektronenstrahlverdampfung), PLD, MBE | Hochreine Beschichtungen, präzise Kontrolle, geeignet für komplexe Materialien | Optik, verschleißfeste Beschichtungen, Halbleiter, Supraleiter |
Benötigen Sie Hilfe bei der Auswahl des richtigen Verfahrens zur Dünnschichtabscheidung für Ihr Projekt? Kontaktieren Sie noch heute unsere Experten !