Magnetronsputtern ist eine weit verbreitete Technik zur Dünnschichtabscheidung, die auf der Anwesenheit eines Magnetfelds beruht, um die Effizienz und Effektivität des Prozesses zu steigern. Das Magnetfeld spielt eine entscheidende Rolle dabei, Elektronen in der Nähe der Targetoberfläche einzuschließen, die Plasmadichte zu erhöhen und die Sputterrate zu verbessern. Dies führt zu höheren Abscheidungsraten, besserer Filmqualität und gleichmäßigeren Beschichtungen. Durch das Einfangen von Sekundärelektronen und die Erhöhung der Ionisierung ermöglicht das Magnetfeld den Betrieb des Prozesses bei niedrigeren Drücken, wodurch Kollisionen reduziert und die Gesamteffizienz verbessert werden. Im Folgenden untersuchen wir die Hauptgründe, warum ein Magnetfeld beim Magnetronsputtern unerlässlich ist.
Wichtige Punkte erklärt:
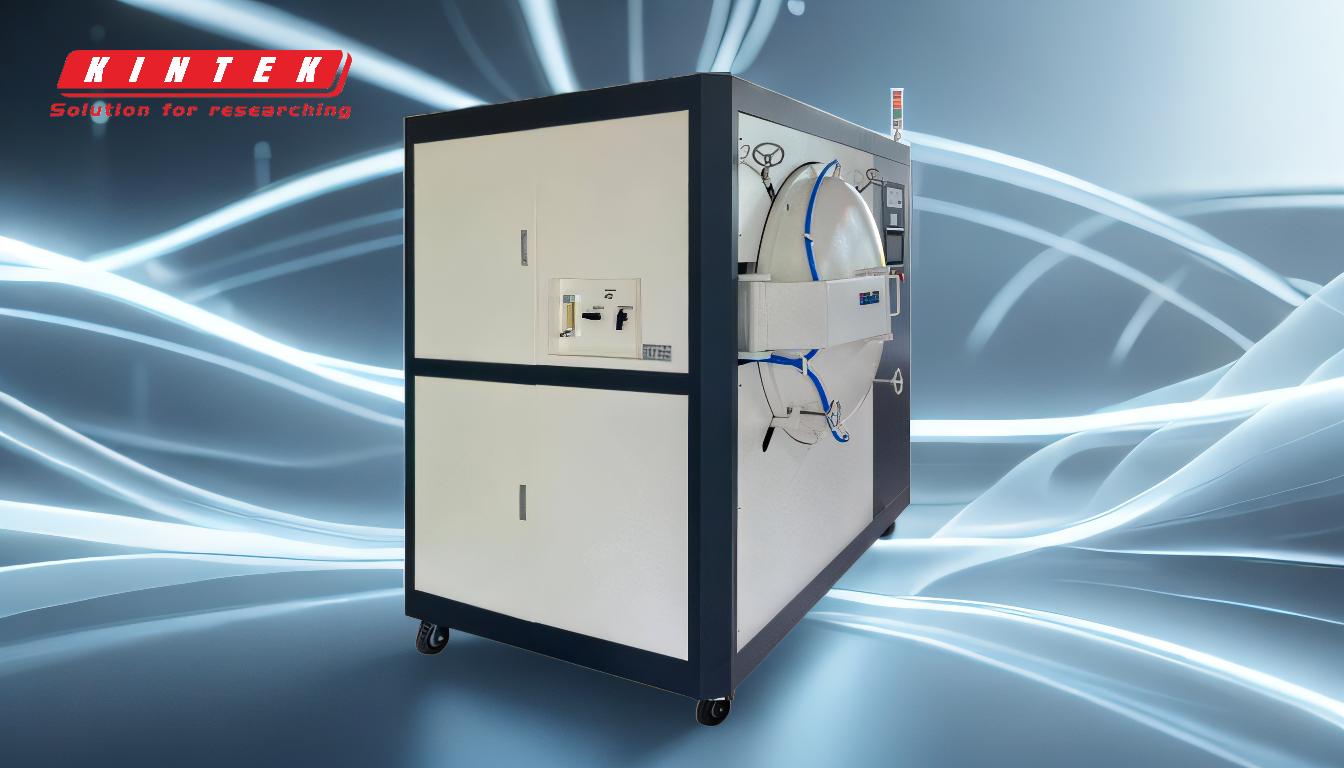
-
Einschluss von Elektronen in der Nähe der Zieloberfläche:
- Das Magnetfeld beim Magnetronsputtern erzeugt einen Grenztunnel, der Sekundärelektronen nahe der Targetoberfläche einfängt. Dieser Einschluss erhöht die Wahrscheinlichkeit von Kollisionen zwischen Elektronen und Argonatomen, was zu höheren Ionisierungsraten führt.
- Indem es die Elektronen in der Nähe des Targets hält, sorgt das Magnetfeld dafür, dass das Plasma dicht und lokalisiert bleibt, was für ein effizientes Sputtern entscheidend ist.
-
Erhöhte Plasmadichte und Ionisierung:
- Die eingefangenen Elektronen ionisieren weitere Argonatome und erzeugen so ein dichteres Plasma in der Nähe des Ziels. Dieses hochdichte Plasma verbessert den Sputterprozess, indem es energiereichere Ionen zum Beschuss des Targetmaterials bereitstellt.
- Höhere Ionisierungsraten führen zu einer effizienteren Energieübertragung auf das Targetmaterial und damit zu schnelleren Sputter- und Abscheidungsraten.
-
Betrieb bei niedrigeren Drücken:
- Durch das Magnetfeld kann das Magnetronsputtern im Vergleich zu herkömmlichen Sputterverfahren bei niedrigeren Drücken betrieben werden. Niedrigere Drücke reduzieren die Anzahl der Kollisionen zwischen gesputterten Atomen und Gasmolekülen in der Kammer und verbessern so die Effizienz des Prozesses.
- Der Betrieb bei niedrigeren Drücken minimiert außerdem die Kontamination und verbessert die Qualität des abgeschiedenen Films.
-
Höhere Sputter- und Abscheidungsraten:
- Die erhöhte Plasmadichte und Ionisierung nahe der Targetoberfläche führen zu höheren Sputterraten. Dies bedeutet, dass in kürzerer Zeit mehr Zielmaterial ausgeworfen und auf dem Substrat abgelagert wird.
- Die Fähigkeit des Magnetfelds, die Sputterrate zu erhöhen, macht das Magnetronsputtern zu einer bevorzugten Methode für Anwendungen, die einen hohen Durchsatz erfordern.
-
Verbesserte Plasmastabilität und Gleichmäßigkeit:
- Das Magnetfeld trägt zur Stabilisierung der Plasmaentladung bei und sorgt für eine gleichmäßige und gleichmäßige Abscheidung auf dem Substrat. Dies ist besonders wichtig, um hochwertige Dünnfilme mit minimalen Defekten zu erzielen.
- Eine gleichmäßige Abscheidung ist für Anwendungen in der Elektronik, Optik und Beschichtung von entscheidender Bedeutung, wo Konsistenz und Präzision von größter Bedeutung sind.
-
Reduzierte Substratschäden:
- Durch die Eingrenzung des Plasmas in der Nähe des Targets verhindert das Magnetfeld einen übermäßigen Ionenbeschuss des Substrats. Dies verringert das Risiko einer Beschädigung des Substrats und stellt sicher, dass der abgeschiedene Film gut haftet, ohne seine strukturelle Integrität zu beeinträchtigen.
-
Vielseitigkeit bei den Stromversorgungsoptionen:
- Magnetron-Sputtersysteme können abhängig vom zu sputternden Material und den gewünschten Filmeigenschaften entweder Gleichstrom (Gleichstrom) oder HF-Stromversorgung (Hochfrequenz) verwenden. Die Rolle des Magnetfelds bleibt bei beiden Typen gleich und gewährleistet eine effiziente Plasmaerzeugung und Sputtern.
- DC-Magnetrons werden typischerweise für leitfähige Materialien verwendet, während RF-Magnetrons für isolierende Materialien geeignet sind.
Zusammenfassend lässt sich sagen, dass das Magnetfeld beim Magnetronsputtern unverzichtbar ist, um ein dichtes, stabiles Plasma nahe der Targetoberfläche zu erzeugen, die Ionisierung zu verbessern und die Gesamteffizienz des Sputterprozesses zu verbessern. Seine Fähigkeit, bei niedrigeren Drücken zu arbeiten, die Abscheidungsraten zu erhöhen und gleichmäßige Beschichtungen zu gewährleisten, macht es zu einem Eckpfeiler moderner Dünnschicht-Abscheidungstechniken.
Übersichtstabelle:
Schlüsselrolle des Magnetfelds | Vorteile |
---|---|
Einschluss von Elektronen | Erhöht die Ionisationsraten und die Plasmadichte in der Nähe der Zieloberfläche. |
Erhöhte Plasmadichte | Verbessert die Sputterraten und die Energieübertragung auf das Targetmaterial. |
Betrieb bei niedrigeren Drücken | Reduziert Kollisionen und Verunreinigungen und verbessert die Filmqualität. |
Höhere Abscheidungsraten | Ermöglicht eine schnellere und effizientere Dünnschichtabscheidung. |
Verbesserte Plasmastabilität | Gewährleistet gleichmäßige und gleichmäßige Beschichtungen für hochwertige Filme. |
Reduzierte Substratschäden | Verhindert übermäßigen Ionenbeschuss und schützt so das Substrat. |
Vielseitigkeit in der Stromversorgung | Unterstützt sowohl Gleichstrom- als auch HF-Stromversorgungen für verschiedene Materialanwendungen. |
Erfahren Sie, wie Magnetronsputtern Ihre Dünnschichtprozesse optimieren kann – Kontaktieren Sie noch heute unsere Experten !