Die physikalische Gasphasenabscheidung (PVD) ist eine weit verbreitete Technik zur Abscheidung dünner Materialschichten auf ein Substrat.Das Verfahren wird in der Regel aus mehreren entscheidenden Gründen in einer Vakuumumgebung durchgeführt.Ein Vakuum verringert die Dichte der Atome in der Kammer, wodurch sich die mittlere freie Weglänge der Atome erhöht, so dass sie längere Strecken ohne Zusammenstöße zurücklegen können.Diese Umgebung minimiert auch die Verunreinigung durch Gase und sorgt für hochwertige, reine Filme.Darüber hinaus ermöglicht ein Vakuum hohe thermische Verdampfungsraten und verhindert unerwünschte chemische Reaktionen zwischen dem Material und atmosphärischen Gasen, die die Eigenschaften der Folie beeinträchtigen könnten.Die kontrollierte Vakuumumgebung ist für Anwendungen wie die Mikrochip-Herstellung unerlässlich, wo selbst geringe Verunreinigungen zu erheblichen Mängeln führen können.
Die wichtigsten Punkte werden erklärt:
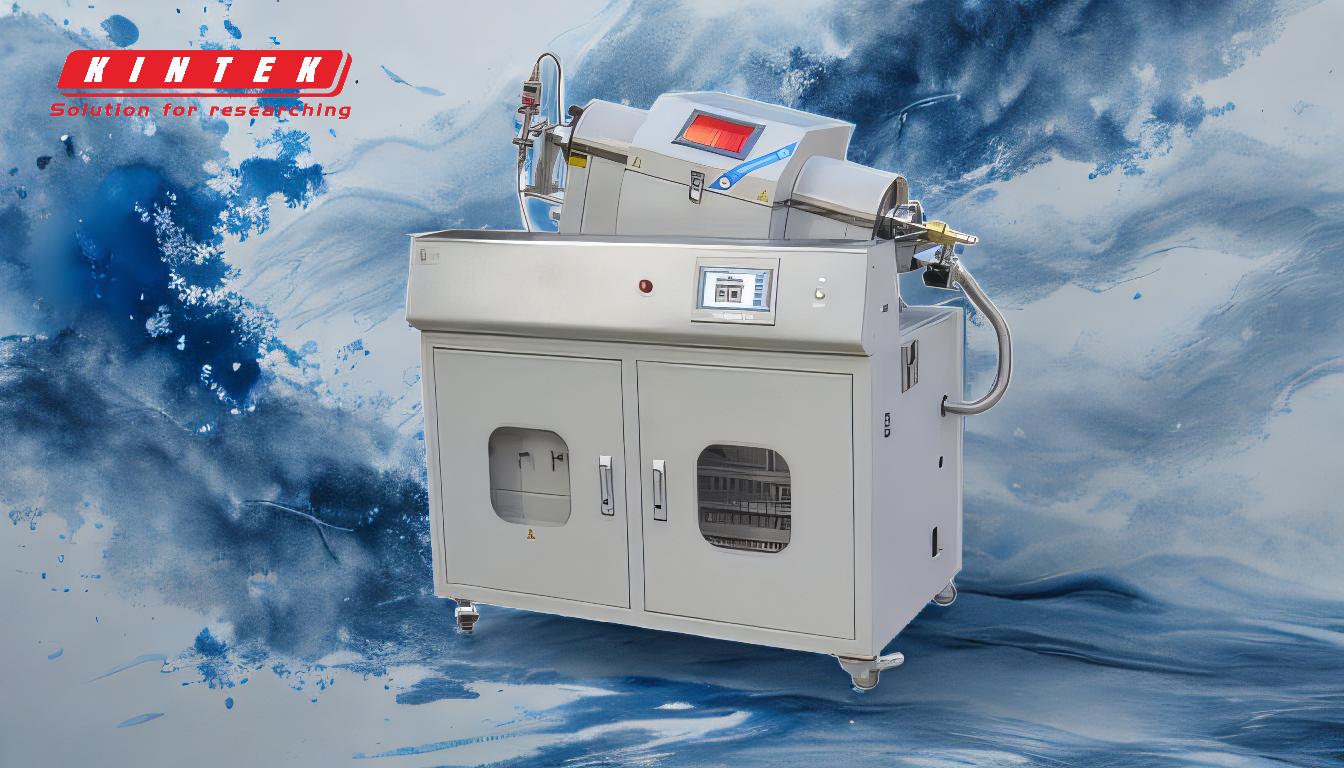
-
Erhöhte mittlere freie Weglänge von Atomen:
- Im Vakuum ist die Dichte der Atome deutlich geringer, was die mittlere freie Weglänge erhöht - die durchschnittliche Entfernung, die ein Atom zurücklegen kann, bevor es mit einem anderen Atom oder Molekül zusammenstößt.Dies ist beim PVD-Verfahren von entscheidender Bedeutung, da sich das verdampfte Material ungehindert von der Quelle zum Substrat bewegen kann, was eine gleichmäßige Abscheidung und hochwertige dünne Schichten gewährleistet.
-
Minimierung der gasförmigen Verunreinigung:
- In einer Vakuumumgebung wird das Vorhandensein unerwünschter Atome und Moleküle wie Sauerstoff, Feuchtigkeit und anderer reaktiver Gase drastisch reduziert.Diese Verunreinigungen können mit dem verdampften Material reagieren und dessen Eigenschaften verändern oder Defekte in der abgeschiedenen Schicht verursachen.Durch die Aufrechterhaltung eines hohen Vakuums sorgt PVD für eine saubere und kontrollierte Umgebung, was besonders wichtig für Anwendungen wie die Mikrochip-Herstellung ist, wo selbst Spuren von Verunreinigungen erhebliche Probleme verursachen können.
-
Hohe thermische Verdampfungsrate:
- Die Vakuumumgebung ermöglicht eine hohe thermische Verdampfungsrate, indem der Druck in der Kammer reduziert wird.Dadurch kann das Material bei niedrigeren Temperaturen verdampfen, was für die Beschichtung von Materialien mit hohem Schmelzpunkt von Vorteil ist.Das Fehlen von Luft oder anderen Gasen sorgt außerdem dafür, dass das verdampfte Material das Substrat mit minimalem Energieverlust erreicht, was zu einem effizienteren und effektiveren Abscheidungsprozess führt.
-
Vermeidung von unerwünschten chemischen Reaktionen:
- Im Vakuum werden die reaktiven Elemente der Luft, wie Sauerstoff, Kohlendioxid und Wasserstoff, entfernt.Dies verhindert unerwünschte chemische Reaktionen zwischen dem verdampften Material und diesen Elementen, die andernfalls die Oberflächeneigenschaften der abgeschiedenen Schicht verändern könnten.So könnten beispielsweise Reaktionen mit Sauerstoff zur Bildung von Oxiden führen, was bei bestimmten Anwendungen unerwünscht sein könnte.
-
Kontrollierter und wiederholbarer Abscheidungsprozess:
- Ein Vakuum bietet eine kontrollierte Umgebung, die für gleichbleibende und wiederholbare Ergebnisse bei der PVD-Beschichtung unerlässlich ist.Durch die Aufrechterhaltung eines bestimmten Vakuumniveaus können die Prozessparameter genau gesteuert werden, wodurch sichergestellt wird, dass bei jedem Abscheidungszyklus die gleichen Bedingungen herrschen.Dies ist entscheidend für industrielle Anwendungen, bei denen Beständigkeit und Zuverlässigkeit von größter Bedeutung sind.
-
Verbesserte Haftung und Filmqualität:
- Das Fehlen von Luft oder anderen Flüssigkeiten im Vakuum sorgt dafür, dass das verdampfte Material das Substrat mit mehr Energie erreicht, was zu einer besseren Haftung und einem gleichmäßigeren Film führt.Dies ist besonders wichtig für Anwendungen, die starke, haltbare Beschichtungen erfordern, wie z. B. bei der Herstellung von CDs, DVDs und anderen optischen Medien.
-
Flexibilität bei Beschichtungsarten:
- Während PVD in der Regel zur Abscheidung von Metallen und Legierungen ohne chemische Reaktionen verwendet wird, ermöglicht die Vakuumumgebung auch die Zufuhr reaktiver Gase, falls dies gewünscht wird.So kann zum Beispiel Sauerstoff zugeführt werden, um Oxidschichten zu erzeugen, was die Flexibilität bei den Beschichtungsarten erhöht, die mit PVD hergestellt werden können.
Zusammenfassend lässt sich sagen, dass die PVD-Beschichtung im Vakuum unerlässlich ist, um hochwertige, kontaminationsfreie Dünnschichten mit präziser Kontrolle über den Beschichtungsprozess zu erhalten.Die Vakuumumgebung erhöht nicht nur die Effizienz und Effektivität des Prozesses, sondern stellt auch sicher, dass das Endprodukt die strengen Anforderungen verschiedener industrieller Anwendungen erfüllt.Weitere Informationen über verwandte Verfahren finden Sie unter Chemische Gasphasenabscheidung durch Mikrowellenplasma .
Zusammenfassende Tabelle :
Hauptgrund | Erläuterung |
---|---|
Erhöhter mittlerer freier Weg | Ermöglicht den Atomen, sich ungehindert fortzubewegen, was eine gleichmäßige Abscheidung und qualitativ hochwertige Schichten gewährleistet. |
Minimierung der gasförmigen Verunreinigung | Reduziert reaktive Gase wie Sauerstoff und Feuchtigkeit und verhindert so Defekte in der Folie. |
Hohe thermische Verdampfungsrate | Ermöglicht die Verdampfung bei niedrigeren Temperaturen und verbessert so die Effizienz und Wirksamkeit. |
Verhinderung von chemischen Reaktionen | Verhindert unerwünschte Reaktionen mit atmosphärischen Gasen und bewahrt die Folieneigenschaften. |
Kontrollierter und wiederholbarer Prozess | Gewährleistet gleichbleibende Ergebnisse durch Aufrechterhaltung bestimmter Vakuumwerte. |
Bessere Haftung und Filmqualität | Verbessert die Energieübertragung, was zu besserer Haftung und gleichmäßigen Beschichtungen führt. |
Flexibilität bei Beschichtungsarten | Ermöglicht die Einführung reaktiver Gase für verschiedene Beschichtungsoptionen. |
Erfahren Sie mehr darüber, wie PVD in einem Vakuum Ihre Prozesse verbessern kann. Kontaktieren Sie unsere Experten noch heute !