Vakuum spielt eine entscheidende Rolle bei Dünnschichtbeschichtungsverfahren wie der physikalischen Gasphasenabscheidung (PVD) und der Elektronenstrahlabscheidung (E-Beam), da es eine Umgebung schafft, die Verunreinigungen minimiert, den Materialtransport verbessert und eine hochwertige Schichtbildung gewährleistet.Ein Vakuum reduziert die Dichte der Gasmoleküle, so dass das verdampfte Material längere Strecken ohne Zusammenstöße zurücklegen kann, was die gerichtete Abscheidung und die Reinheit der Schichten verbessert.Außerdem werden unerwünschte chemische Reaktionen und Verunreinigungen durch Umgebungsgase verhindert, was eine starke Haftung und hochwertige dünne Schichten gewährleistet.Die Vakuumumgebung ist für die Erzielung der gewünschten Schichteigenschaften wie Gleichmäßigkeit, Reinheit und Haftung von entscheidender Bedeutung und daher für Dünnschichtbeschichtungsprozesse unverzichtbar.
Die wichtigsten Punkte erklärt:
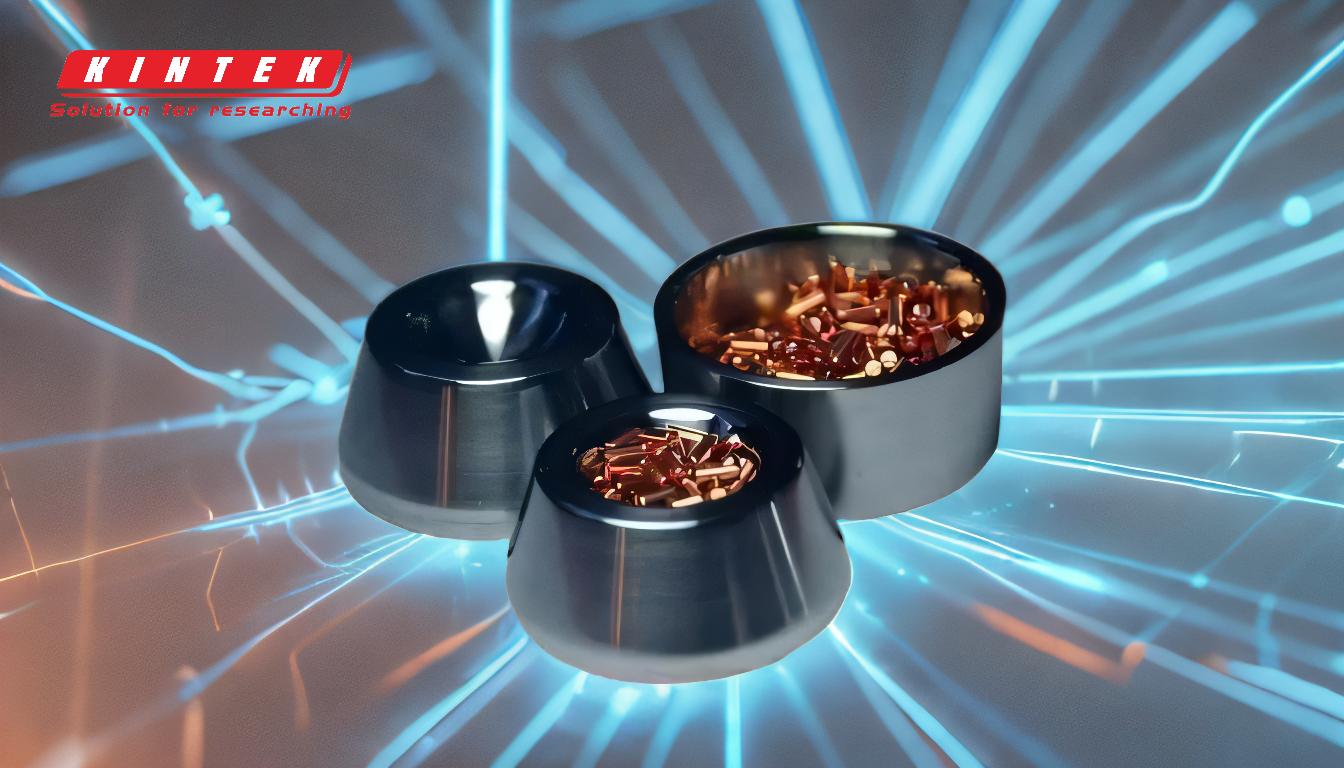
-
Minimierung der Kontamination:
- Eine Vakuumumgebung reduziert das Vorhandensein von unerwünschten Gasen wie Sauerstoff, Stickstoff und Kohlendioxid, die mit dem Filmmaterial reagieren oder Defekte verursachen können.
- Durch die Aufrechterhaltung eines hohen Vakuums (in der Regel weniger als 10^-5 Torr) minimiert das System die Verunreinigung durch Hintergrundgase und gewährleistet so hochreine Dünnschichten.
-
Erhöhung der mittleren freien Weglänge:
- Im Vakuum vergrößert sich die mittlere freie Weglänge von verdampften Atomen oder Molekülen erheblich.Bei 10^-5 Torr beträgt die mittlere freie Weglänge zum Beispiel etwa 1 Meter.
- Dadurch kann sich das verdampfte Material in einer geraden Linie zum Substrat bewegen, ohne mit Gasmolekülen zu kollidieren, was eine effiziente und gerichtete Abscheidung gewährleistet.
-
Verbesserung der Filmqualität:
- Eine Vakuumumgebung gewährleistet, dass das verdampfte Material gleichmäßig auf dem Substrat kondensiert, was zu hochwertigen dünnen Schichten mit hervorragender Haftung und Gleichmäßigkeit führt.
- Es verhindert die Bildung von Defekten, die durch Zusammenstöße von Gasmolekülen oder chemische Reaktionen entstehen und die strukturelle Integrität des Films schwächen können.
-
Kontrolle der Zusammensetzung von Gasen und Dämpfen:
- Ein Vakuum ermöglicht eine präzise Kontrolle der Zusammensetzung von Gasen und Dämpfen in der Prozesskammer, was für die Erzielung bestimmter Filmeigenschaften entscheidend ist.
- Diese Kontrolle ist für Verfahren wie das reaktive Sputtern, bei dem die Zufuhr reaktiver Gase sorgfältig gesteuert werden muss, unerlässlich.
-
Reduzierung der Partikeldichte:
- Durch die Verringerung der Partikeldichte in der Kammer sorgt das Vakuum dafür, dass das verdampfte Material die vorherrschende Spezies ist, wodurch die Wahrscheinlichkeit, dass Verunreinigungen in den Film gelangen, verringert wird.
- Dies ist besonders wichtig bei Anwendungen, die ultrareine Filme erfordern, wie z. B. bei der Halbleiterherstellung.
-
Unterstützt hohe thermische Verdampfungsraten:
- Eine Vakuumumgebung erleichtert hohe thermische Verdampfungsraten, indem sie den Energieverlust der verdampften Atome aufgrund von Zusammenstößen mit Gasmolekülen verringert.
- Dies ist entscheidend für Prozesse wie die Widerstandsverdampfung, bei denen hohe Verdampfungsraten für eine effiziente Abscheidung erforderlich sind.
-
Verhinderung chemischer Reaktionen:
- Ein Vakuum minimiert die Anwesenheit reaktiver Gase und verhindert unerwünschte chemische Reaktionen zwischen dem Folienmaterial und den Umgebungsgasen.
- Dies ist besonders wichtig für Materialien, die stark mit Sauerstoff oder Stickstoff reagieren, um sicherzustellen, dass die Folie ihre gewünschten Eigenschaften beibehält.
-
Ultrahochvakuum für fortschrittliche Anwendungen:
- Für fortschrittliche Anwendungen sind Ultrahochvakuum-Bedingungen (10^-9 Torr oder weniger) erforderlich, um Spurengase zu eliminieren, die Defekte verursachen können.
- UHV-Umgebungen sind entscheidend für die Herstellung fehlerfreier Dünnschichten in Hochpräzisionsbranchen wie Optik und Mikroelektronik.
Zusammenfassend lässt sich sagen, dass ein Vakuum bei der Beschichtung von Dünnschichten von entscheidender Bedeutung ist, da es eine saubere, kontrollierte Umgebung gewährleistet, die den Materialtransport verbessert, Verunreinigungen minimiert und die Bildung hochwertiger, einheitlicher und haftender Dünnschichten ermöglicht.Diese Vorteile sind entscheidend für die Erfüllung der strengen Anforderungen moderner Anwendungen in Branchen wie der Halbleiterindustrie, der Optik und der Luft- und Raumfahrt.
Zusammenfassende Tabelle:
Hauptnutzen | Erläuterung |
---|---|
Minimierung der Kontamination | Reduziert unerwünschte Gase und gewährleistet hochreine dünne Schichten. |
Vergrößerung des mittleren freien Wegs | Ermöglicht es dem verdampften Material, längere Strecken ohne Kollisionen zurückzulegen. |
Verbessert die Filmqualität | Sorgt für gleichmäßige Kondensation und starke Haftung dünner Filme. |
Kontrolle der Gaszusammensetzung | Ermöglicht die präzise Steuerung von Gasen für bestimmte Filmeigenschaften. |
Reduzierung der Partikeldichte | Verringert den Einbau von Verunreinigungen, was für hochreine Filme entscheidend ist. |
Unterstützt hohe Verdampfung | Ermöglicht hohe thermische Verdampfungsraten für eine effiziente Abscheidung. |
Verhinderung von chemischen Reaktionen | Minimiert reaktive Gase und bewahrt die Folieneigenschaften. |
Erreichen von Ultra-Hochvakuum | Eliminiert Spurengase für defektfreie Schichten in modernen Anwendungen. |
Erfahren Sie, wie die Vakuumtechnologie Ihre Dünnschicht-Beschichtungsprozesse verbessern kann. Kontaktieren Sie unsere Experten noch heute !