Vakuumumgebungen sind bei der Abscheidung von Dünnschichten unerlässlich, um qualitativ hochwertige, kontaminationsfreie Schichten zu gewährleisten.Das Fehlen von Luft und anderen Gasen im Vakuum verhindert Oxidation, Verunreinigung und unerwünschte chemische Reaktionen, die für die Erzielung präziser Schichteigenschaften entscheidend sind.Außerdem ermöglichen die Vakuumbedingungen eine bessere Kontrolle der Abscheidungsparameter wie Temperatur und Druck, was zu gleichmäßigen und fehlerfreien dünnen Schichten führt.Der Einsatz eines Vakuum-Reinigungsofens verbessert den Prozess durch die Aufrechterhaltung einer sauberen und kontrollierten Umgebung, die die Integrität der abgeschiedenen Materialien gewährleistet.
Die wichtigsten Punkte werden erklärt:
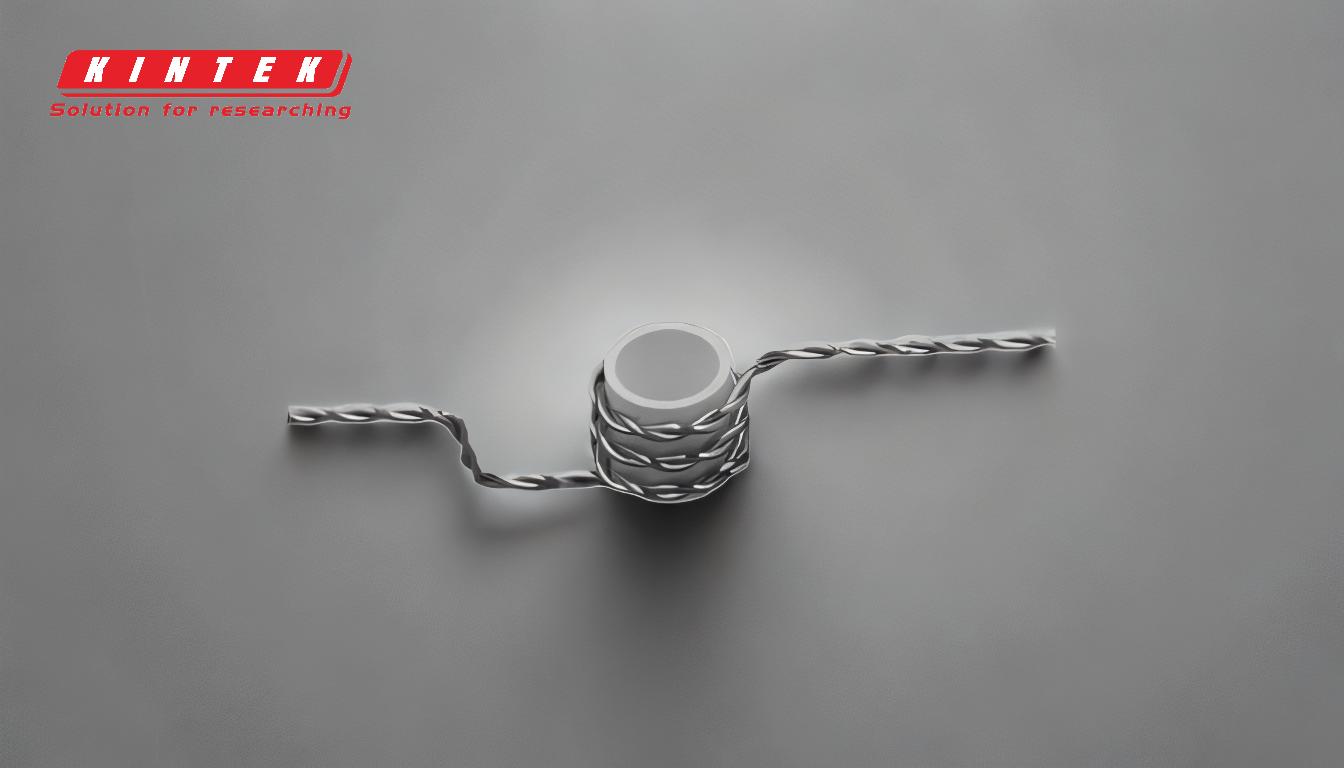
-
Verhinderung von Oxidation und Kontamination:
- In einer Vakuumumgebung wird durch das Fehlen von Luft und anderen Gasen das Risiko von Oxidation und Kontamination ausgeschlossen.Dies ist von entscheidender Bedeutung für Materialien, die mit Sauerstoff oder anderen atmosphärischen Gasen sehr reaktiv sind.
- So können beispielsweise Metalle wie Aluminium oder Titan in Gegenwart von Luft leicht oxidieren, was zu einer Verschlechterung der Schichtqualität führt.Ein Vakuum sorgt dafür, dass diese Materialien während der Abscheidung rein und unverändert bleiben.
-
Kontrolle über Abscheidungsparameter:
- Vakuumbedingungen ermöglichen eine präzise Steuerung von Temperatur und Druck, die für die Herstellung gleichmäßiger dünner Schichten entscheidend sind.
- Im Vakuum erhöht sich die mittlere freie Weglänge der Partikel, was eine kontrolliertere und gezieltere Abscheidung ermöglicht.Dies führt zu Schichten mit weniger Defekten und besserer Haftung auf dem Substrat.
-
Verbesserte Materialintegrität:
- Ein Vakuumofen verhindert die Materialzersetzung durch Aufrechterhaltung einer Niederdruck- oder Vakuumumgebung.Dies ist besonders wichtig für Prozesse wie Sintern, Glühen und Wärmebehandlung, bei denen die Unversehrtheit des Materials von größter Bedeutung ist.
- Bei der Herstellung von Halbleitern zum Beispiel können schon geringe Verunreinigungen zum Ausfall der Geräte führen.Ein Vakuum sorgt dafür, dass die Materialien nicht verunreinigt werden und ihre gewünschten Eigenschaften beibehalten.
-
Vorteile für die Umwelt:
- Vakuumöfen, einschließlich Vakuum-Reinigungsöfen arbeiten ohne die Emission von Abgasen oder Wasser, was sie umweltfreundlich macht.
- Dies trägt nicht nur zur Aufrechterhaltung einer guten atmosphärischen Umgebung bei, sondern verringert auch die Notwendigkeit, drei Abfälle (Abgas, Abwasser und feste Abfälle) zu behandeln, wodurch der Druck auf die Luftverschmutzungsbehandlung verringert wird.
-
Angleichung an moderne Umweltstandards:
- Der Einsatz der Vakuumtechnologie bei der Dünnschichtabscheidung steht im Einklang mit den Umweltstandards der modernen sozialen Industrialisierung.
- Durch die Verringerung von Emissionen und Abfällen tragen Vakuumöfen zu nachhaltigen Fertigungsverfahren bei, die in der heutigen umweltbewussten Welt immer wichtiger werden.
Zusammenfassend lässt sich sagen, dass die Notwendigkeit eines Vakuums bei der Dünnschichtabscheidung aus der Notwendigkeit resultiert, Verunreinigungen zu vermeiden, die Abscheidungsparameter zu kontrollieren, die Materialintegrität aufrechtzuerhalten und die Umweltstandards zu erfüllen.Die Verwendung eines Vakuum-Reinigungsofens verbessert diese Vorteile noch, indem er eine saubere und kontrollierte Umgebung gewährleistet, was ihn zu einem unverzichtbaren Werkzeug in modernen Dünnschichtabscheidungsprozessen macht.
Zusammenfassende Tabelle:
Die wichtigsten Vorteile des Vakuums bei der Dünnschichtabscheidung |
---|
Verhindert Oxidation und Verunreinigung |
- Eliminiert Luft und Gase, um Materialverschlechterung zu vermeiden. |
Präzise Kontrolle über die Abscheidungsparameter |
- Ermöglicht gleichmäßige Temperatur und Druck für fehlerfreie Schichten. |
Erhält die Integrität des Materials |
- Gewährleistet, dass die Materialien für Prozesse wie Sintern und Glühen nicht kontaminiert werden. |
Vorteile für die Umwelt |
- Keine Abgas- oder Wasseremissionen, was den Nachhaltigkeitsstandards entspricht. |
Entspricht den modernen Umweltstandards |
- Reduziert Emissionen und Abfall und unterstützt eine umweltfreundliche Produktion. |
Optimieren Sie Ihren Dünnschicht-Beschichtungsprozess mit einem Vakuum-Reinigungsofen. Kontaktieren Sie uns noch heute um mehr zu erfahren!