Einführung in das Spark Plasma Sintering (SPS)
Das Spark-Plasma-Sintern (SPS) stellt einen bahnbrechenden Ansatz in der modernen Materialverarbeitung dar und revolutioniert die Art und Weise, wie Materialien gesintert werden. Dieses innovative Verfahren zeichnet sich durch den Einsatz von Gleichstromimpulsen zur schnellen Erhitzung und Sinterung aus und unterscheidet sich damit deutlich von herkömmlichen Techniken. Der einzigartige Prozess von SPS beinhaltet die Erzeugung eines Funkenplasmas durch gepulste Ströme, was die Herstellung von Materialien mit hervorragenden Eigenschaften ermöglicht. In diesem umfassenden Leitfaden werden wir die Feinheiten des SPS-Verfahrens, seine unzähligen Anwendungsmöglichkeiten in verschiedenen Industriezweigen und die beträchtlichen Vorteile, die es gegenüber herkömmlichen Sinterverfahren bietet, näher beleuchten. Begleiten Sie uns, wenn wir das transformative Potenzial von SPS bei der Gestaltung der Zukunft der Materialwissenschaft aufdecken.
Funktionsweise des Spark Plasma Sintering Ofens
Spark Plasma Sintering (SPS), auch bekannt als Pulsed Electric Current Sintering (PECS), Plasma Activated Sintering (PAS) oder Field Assisted Sintering Technology (FAST), ist ein hochentwickeltes Sinterverfahren, das hohe gepulste Gleichströme nutzt, um einen Pulverpressling in einer Matrize/Stanzvorrichtung zu erhitzen. Diese Methode ermöglicht die Anwendung von Druckkräften bis zu 250 kN, mit Transformatorleistungen, die 10 V und Ströme bis zu 10 kA erreichen können. Die gepulsten Gleichstrommuster können mit EIN- und AUS-Segmenten im Bereich von 0 bis 255 ms eingestellt werden, was eine präzise Steuerung des Sinterprozesses ermöglicht.
Das SPS-Verfahren zeichnet sich durch seine schnellen Aufheiz- und Abkühlraten aus, die je nach Werkzeuggröße und -design 1000°C/min bzw. 400°C/min überschreiten können. Durch diese schnellen thermischen Zyklen werden Vergröberungsprozesse bei niedrigen Temperaturen minimiert und die intrinsischen Nanostrukturen bleiben auch nach der vollständigen Verdichtung erhalten. Die Temperatur im SPS-Ofen wird mit einem zentralen Pyrometer überwacht, das auf den Boden einer Bohrung im Oberstempel gerichtet ist und unabhängig von den Eigenschaften oder der Größe der Probe eine genaue Temperaturmessung gewährleistet. Eine zusätzliche Temperaturüberwachung kann mit einem externen Pyrometer und flexiblen Thermoelementen erfolgen, die an verschiedenen Stellen angebracht werden.
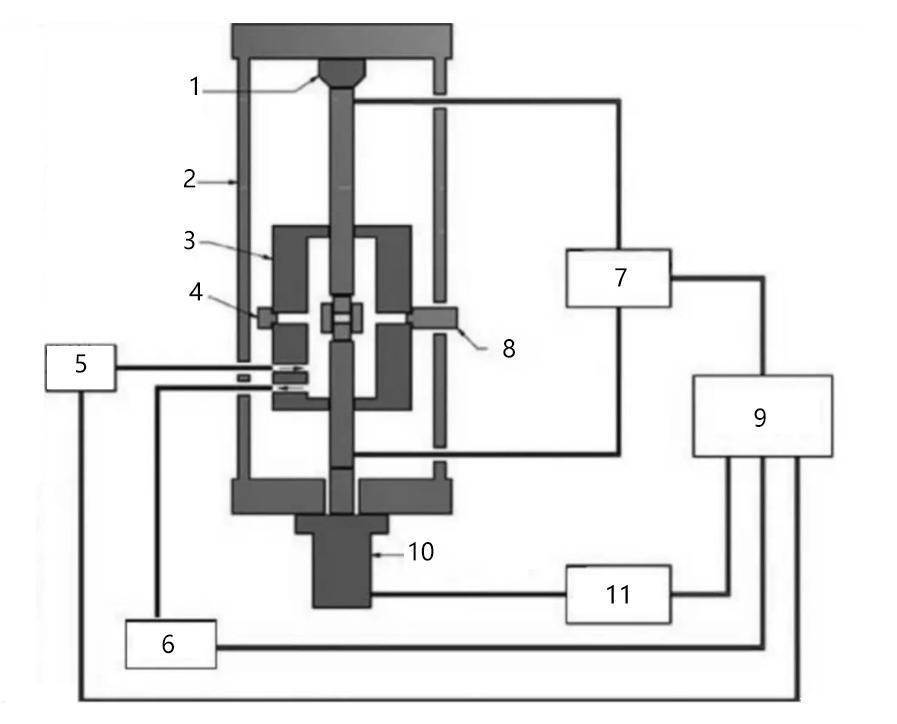
1. Beladeeinheit 2. Beladegestell 3. Vakuumkammer 4. Beobachtungsfenster 5. Inertgas-Kanal 6. Vakuumpumpe 7. Impulsschalter 8. Temperaturmesser 9. Steuerungssystem 10. Hydraulischer Zylinder 11. Hydraulisches System
Zu den wichtigsten Komponenten eines SPS-Ofens gehören die Axialdruckvorrichtung, die wassergekühlte Stempelelektrode und die Vakuumkammer. Die Axialdruckvorrichtung bringt die erforderliche Druckkraft auf, während die wassergekühlten Stempelelektroden dazu beitragen, die während des Prozesses entstehende Wärme zu bewältigen. Die Vakuumkammer, gekoppelt mit einem Atmosphärensteuerungssystem, das zwischen Vakuum- und Argonumgebung umschalten kann, gewährleistet optimale Sinterbedingungen. Die DC-Impulsstromversorgung sowie ein Kühlwassersystem, eine Wegmessung, eine Temperaturmessung und Sicherheitssteuerungseinheiten vervollständigen die SPS-Einrichtung und ermöglichen eine umfassende Prozesssteuerung und Sinterzyklusprogrammierung über eine benutzerfreundliche Touchscreen-Schnittstelle.
Der SPS-Ofen wird in großem Umfang für das Sintern einer breiten Palette von Materialien, einschließlich Keramik, Cermets und Metallen, eingesetzt. Seine technischen Vorteile liegen vor allem in den hohen Aufheiz- und Abkühlraten, die die Prozesszeiten deutlich reduzieren. Der hohe gepulste Strom verbessert nicht nur die Verdichtung in elektrisch leitfähigen Materialien, sondern aktiviert auch mehrere Sintermechanismen wie die Entfernung von Oberflächenoxiden, Elektromigration und Elektroplastizität. Diese Kombination aus mechanischem Druck, elektrischem Feld und thermischem Feld verbessert die Bindung und Verdichtung zwischen den Partikeln erheblich und macht SPS zu einem bevorzugten Verfahren für die Herstellung von Hochleistungswerkstoffen.
Zusammenfassend lässt sich sagen, dass das Spark-Plasma-Sintern ein hocheffizientes und kontrolliertes Verfahren zur Materialverdichtung ist, das schnelle Verarbeitungszeiten und die Fähigkeit zur Erhaltung feiner Mikrostrukturen bietet. Seine Anwendungen erstrecken sich über verschiedene Bereiche, von Hochleistungskeramik bis hin zu metallischen Verbundwerkstoffen, was seine Vielseitigkeit und Bedeutung in der modernen Materialwissenschaft und -technik unterstreicht.
Vorteile des Einsatzes von SPS in der Materialverarbeitung
Das Spark-Plasma-Sintern (SPS) hat den Bereich der Materialverarbeitung revolutioniert, da es gegenüber den herkömmlichen Sintertechniken erhebliche Vorteile bietet. SPS ist ein feldunterstütztes Sinterverfahren, das sowohl Temperatur als auch Druck nutzt, um eine schnelle Verdichtung von Materialien zu erreichen. Diese Methode eignet sich besonders gut für das Sintern einer breiten Palette von Werkstoffen, einschließlich Keramik, Metallen und Verbundwerkstoffen, mit bemerkenswerter Effizienz und Präzision.
Schnelle Sinterraten
Einer der bemerkenswertesten Vorteile von SPS ist die Fähigkeit, schnelle Sinterraten zu erzielen. Herkömmliche Sinterverfahren wie Heißpressen und druckloses Sintern können mehrere Stunden benötigen, um die gewünschte Verdichtung zu erreichen. Im Gegensatz dazu kann SPS Materialien in nur wenigen Minuten verdichten. Ermöglicht wird diese schnelle Sinterung durch die hohen Heizraten, die über 500°C pro Minute betragen können. Das Erreichen einer Temperatur von 1200°C kann beispielsweise mit SPS in nur 4 Minuten erreicht werden, im Vergleich zu 2 bis 4 Stunden bei herkömmlichen Verfahren. Diese Geschwindigkeit steigert nicht nur die Produktivität, sondern senkt auch den Energieverbrauch und die Betriebskosten.
Feinkörnige Sinterung
SPS ermöglicht das Feinkornsintern, das für die Verbesserung der mechanischen und physikalischen Eigenschaften von Sinterwerkstoffen entscheidend ist. Die schnellen Aufheizraten hemmen das Kornwachstum und ermöglichen die Herstellung von Werkstoffen mit kontrollierten Mikrostrukturen. Dies ist besonders vorteilhaft für die Herstellung von nanokristallinen Werkstoffen, bei denen die Beibehaltung kleiner Korngrößen für die Erzielung hervorragender Eigenschaften von entscheidender Bedeutung ist. Das Feinkornsintern verbessert auch die Homogenität der gesinterten Produkte, was zu einer gleichmäßigeren und zuverlässigeren Leistung führt.
Kontrolle von Dichte und Temperaturgradienten
SPS bietet eine ausgezeichnete Kontrolle über die Dichte und die Temperaturgradienten innerhalb der gesinterten Materialien. Dieses Maß an Kontrolle wird durch die gleichzeitige Anwendung von Temperatur und Druck erreicht, was eine präzise Anpassung des Sinterprozesses ermöglicht. Die Steuerung der Dichte ist besonders wichtig für die Herstellung von Materialien mit bestimmten Porositätsgraden oder für die Erzielung einer vollständigen Verdichtung. Darüber hinaus können mit SPS Temperaturgradienten innerhalb der Form erzeugt werden, die das gleichzeitige Sintern von Materialien mit unterschiedlichen Schmelzpunkten ermöglichen. Diese Fähigkeit ist von unschätzbarem Wert für die Herstellung von funktional abgestuften Materialien (FGM), bei denen die Zusammensetzung und die Eigenschaften räumlich variieren.
Effizienz und Kompaktheit von SPS-Öfen
SPS-Öfen sind auf hohe Effizienz und Kompaktheit ausgelegt und eignen sich daher sowohl für Forschungs- als auch für Industrieanwendungen. Die kompakte Bauweise von SPS-Öfen reduziert den Platzbedarf und ermöglicht eine einfache Integration in bestehende Produktionslinien. Darüber hinaus wird die Effizienz von SPS-Öfen durch ihre Fähigkeit, schnelle Aufheiz- und Abkühlraten zu erzielen, erhöht, was zu weiteren Energieeinsparungen und geringeren Betriebskosten beiträgt. Der interne Heizmechanismus, der eine Joule-Erwärmung der Graphitform und des Pulverbriketts beinhaltet, gewährleistet eine gleichmäßige Wärmeverteilung und minimiert den Wärmeverlust, wodurch der Sinterprozess optimiert wird.
Reinigung und Aktivierungssintern
SPS bietet auch einzigartige Vorteile in Bezug auf die Reinigung und das Aktivierungssintern. Das Verfahren kann adsorbierte Gase und Oxidschichten von den Partikeloberflächen entfernen, was zu saubereren Grenzflächen und einer besseren Bindung führt. Dieser Reinigungseffekt in Verbindung mit der Aktivierung der Partikeloberflächen ermöglicht das Sintern von Materialien, die sonst nur schwer zu verarbeiten sind. Diese Fähigkeit erweitert die Palette der Werkstoffe, die mit SPS effektiv gesintert werden können, einschließlich Hochleistungskeramik und Verbundwerkstoffe.
Zusammenfassend lässt sich sagen, dass das Spark-Plasma-Sintern (SPS) eine Vielzahl von Vorteilen bietet, die es zu einer hervorragenden Wahl für die Materialverarbeitung machen. Die schnellen Sinterraten, die Feinkornsinterfähigkeiten, die Dichte- und Temperaturgradientensteuerung, die Effizienz und die Kompaktheit machen es zu einem unschätzbaren Werkzeug sowohl für die Forschung als auch für industrielle Anwendungen. Durch die Nutzung dieser Vorteile erweitert die SPS die Grenzen der Materialwissenschaft und -technik und ermöglicht die Entwicklung innovativer und leistungsstarker Materialien.
Anwendungen von SPS in verschiedenen Branchen
Die Technologie des Spark-Plasma-Sinterns (SPS) hat die Herstellungsprozesse in zahlreichen Branchen revolutioniert und ermöglicht die Entwicklung fortschrittlicher Werkstoffe mit einzigartigen Eigenschaften. SPS ist vor allem für seine Fähigkeit bekannt, schnell und bei relativ niedrigen Temperaturen hochdichte, feinkörnige Materialien herzustellen, was es zu einer bevorzugten Methode für die Synthese von Nanomaterialien, Keramik, Verbundwerkstoffen und medizinischen Implantaten macht.
Nanomaterialien
Eine der wichtigsten Anwendungen der SPS ist die Herstellung von Nanomaterialien. Nanomaterialien weisen aufgrund ihrer geringen Korngröße außergewöhnliche mechanische und physikalische Eigenschaften auf, was ihre Festigkeit und Plastizität erhöht. SPS erleichtert die Synthese dieser Materialien, indem es das Kornwachstum während des Sinterprozesses hemmt. Die schnelle Erhitzung und die kurzen Sinterzeiten, die mit SPS einhergehen, tragen dazu bei, dass die Korngröße im Nanometerbereich erhalten bleibt, was für die Leistung von Nanomaterialien entscheidend ist. Diese Technik eignet sich besonders gut für das Sintern von Pulvern, die durch Methoden wie mechanisches Legieren gewonnen wurden und deren Konsolidierung mit herkömmlichen Methoden oft schwierig ist.
Keramiken und Cermets
SPS wird auch häufig bei der Herstellung von hochdichten, feinkörnigen Keramiken und Cermets eingesetzt. Der einzigartige Heizmechanismus von SPS, bei dem die einzelnen Pulverpartikel und die Poren zwischen ihnen als Wärmequellen fungieren, ermöglicht eine schnelle Verdichtung und eine erhebliche Reduzierung der Sinterzeiten und -temperaturen. Diese Methode ist für die industrielle Produktion sehr vorteilhaft, da sie Energie spart und die Produktionseffizienz verbessert. Die Fähigkeit, Keramiken mit hoher Dichte und feiner Kornstruktur herzustellen, erhöht ihre mechanische Festigkeit und Haltbarkeit, so dass sie sich für verschiedene technische Anwendungen eignen.
Gradienten-Funktionswerkstoffe
Gradientenfunktionswerkstoffe, die eine Gradientenverteilung in bestimmten Richtungen aufweisen, sind ein weiterer Bereich, zu dem die SPS einen wichtigen Beitrag geleistet hat. Herkömmliche Sinterverfahren haben Schwierigkeiten mit den unterschiedlichen Sintertemperaturen, die für jede Schicht in Gradientenwerkstoffen erforderlich sind. SPS hingegen kann diesen Gradienten effektiv steuern und ermöglicht die industrielle Produktion dieser komplexen Materialien. Der kontrollierte Sinterprozess in SPS gewährleistet, dass jede Schicht die gewünschten Eigenschaften erhält, ohne die Integrität der Gesamtstruktur zu beeinträchtigen.
Medizinische Implantate
Im medizinischen Bereich wird SPS zur Herstellung von Implantaten mit maßgeschneiderten mechanischen Eigenschaften und Biokompatibilität eingesetzt. Die Möglichkeit, die Sinterbedingungen genau zu steuern, ermöglicht die Herstellung von Implantaten mit spezifischen mechanischen Eigenschaften, die dem menschlichen Knochen entsprechen, wodurch ihre Funktionalität und Langlebigkeit verbessert wird. Darüber hinaus können mit SPS poröse Strukturen hergestellt werden, die das Einwachsen von Knochen erleichtern und so die Integration von Implantaten in das umgebende Gewebe verbessern.
Verbundwerkstoffe und nanostrukturierte Materialien
SPS spielt eine wichtige Rolle bei der Herstellung von Verbundwerkstoffen und nanostrukturierten Materialien mit verbesserten Eigenschaften wie magnetischen, piezoelektrischen, thermoelektrischen und optischen Merkmalen. Der schnelle Sinterprozess in der SPS trägt dazu bei, die Nanostruktur der Materialien zu erhalten, die für ihre Leistung entscheidend ist. SPS wird beispielsweise zum Sintern von Kohlenstoffnanoröhren verwendet, um Feldelektronenemissionselektroden zu entwickeln, was die Vielseitigkeit des Verfahrens bei der Verarbeitung verschiedener Materialtypen unterstreicht.
Zusammenfassend lässt sich sagen, dass sich das Spark-Plasma-Sintern als vielseitiges und leistungsfähiges Verfahren erwiesen hat, das in verschiedenen Branchen Anwendung findet. Seine Fähigkeit, hochwertige, fortschrittliche Materialien mit einzigartigen Eigenschaften herzustellen, macht es zu einem unverzichtbaren Werkzeug in der modernen Fertigung. Da die Forschung und Entwicklung auf diesem Gebiet weiter voranschreitet, ist zu erwarten, dass sich die potenziellen Anwendungen des SPS noch weiter ausweiten und die Innovation in der Materialwissenschaft und -technik vorantreiben werden.
Fallstudien: Erfolgreiche Implementierungen von SPS
Die Spark Plasma Sintering (SPS)-Technologie hat den Bereich der Materialwissenschaft revolutioniert und ermöglicht das schnelle Sintern und Verdichten einer breiten Palette von Materialien mit verbesserten Eigenschaften. In diesem Abschnitt werden mehrere Fallstudien vorgestellt, die die erfolgreichen Anwendungen von SPS sowohl in der Forschung als auch in der Industrie aufzeigen und die Vielseitigkeit und Effektivität der Technologie demonstrieren.
Materialien zur Energiespeicherung
Eine der wichtigsten Anwendungen von SPS ist die Entwicklung fortschrittlicher Energiespeichermaterialien. SPS wurde zum Beispiel zur Herstellung von Lithium-Ionen-Batterien mit hoher Kapazität und verbesserter Leistung eingesetzt. Durch die präzise Steuerung der Sinterparameter konnten die Forscher Batteriematerialien mit höherer Energiedichte und verbesserter Zykluslebensdauer herstellen. Studien zufolge haben mit SPS hergestellte Lithium-Ionen-Batterien eine um 20 % höhere Energiespeicherkapazität als herkömmliche Verfahren, was sie ideal für den Einsatz in Elektrofahrzeugen und tragbarer Elektronik macht.
Biomedizinische Technik
Im Bereich der Biomedizintechnik hat die SPS bei der Herstellung von porösen Keramiken für die Verabreichung von Medikamenten und Gerüsten für die Gewebezüchtung eine wichtige Rolle gespielt. Diese Materialien erfordern eine genaue Kontrolle ihrer Mikrostruktur, um die Kompatibilität mit biologischen Systemen zu gewährleisten. SPS ermöglicht die Herstellung hochporöser Strukturen mit kontrollierter Porengröße, die für die wirksame Verabreichung von Arzneimitteln und das Wachstum von Geweben entscheidend sind. So wurden beispielsweise mit SPS hergestellte Hydroxylapatitgerüste für das Knochengewebe-Engineering verwendet, die im Vergleich zu herkömmlichen Verfahren eine bessere Biokompatibilität und mechanische Festigkeit aufweisen.
Hochleistungskeramik
SPS wurde auch ausgiebig bei der Herstellung von Hochleistungskeramiken wie Hochtemperatursupraleitern und piezoelektrischen Hochleistungskeramiken eingesetzt. Diese Materialien sind entscheidend für Anwendungen, die von der Energieübertragung bis hin zu Sensoren und Aktoren reichen. SPS ermöglicht die Verdichtung dieser Keramiken bei niedrigeren Temperaturen und in kürzerer Zeit, wobei ihre einzigartigen Eigenschaften erhalten bleiben. So wurde SPS beispielsweise zur Herstellung von Yttrium-Barium-Kupfer-Oxid (YBCO)-Supraleitern mit nahezu theoretischer Dichte eingesetzt, wodurch die Übergangstemperaturen der Supraleiter erheblich verbessert wurden.
Intermetallische Werkstoffe und Verbundwerkstoffe
Die Vielseitigkeit von SPS zeigt sich auch bei der Verarbeitung von Intermetallen und Verbundwerkstoffen. SPS wurde eingesetzt, um fortschrittliche Legierungen mit verbesserten mechanischen, thermischen und elektrischen Eigenschaften herzustellen. So wurde SPS beispielsweise zur Synthese von intermetallischen Titanaluminid (TiAl)-Legierungen eingesetzt, die sich durch eine hervorragende Hochtemperaturfestigkeit und Oxidationsbeständigkeit auszeichnen. Darüber hinaus hat SPS die Herstellung von verstärkten Keramiken und Metallen mit verbesserten mechanischen Eigenschaften ermöglicht, wie z. B. Titanmatrix-Verbundwerkstoffe mit eingebetteten Keramikpartikeln, die zu Werkstoffen mit hoher Festigkeit und Verschleißfestigkeit führen.
Industrielle Anwendungen
In der Industrie wurde SPS für die Herstellung verschiedener Materialien eingesetzt, darunter magnetische Materialien, harte Materialien und Materialien mit Gradientenfunktion. So haben beispielsweise japanische Unternehmen wie Ohta Seiki SPS erfolgreich für die Massenproduktion von 100%igen WC-Superhartstoffen eingesetzt und beliefern damit über 40 Hersteller in Japan und im Ausland. Diese Werkstoffe werden in einem breiten Spektrum von Anwendungen eingesetzt, von Schneidwerkzeugen bis hin zu elektronischen Bauteilen, was die industrielle Skalierbarkeit von SPS unterstreicht.
Schlussfolgerung
Die hier vorgestellten Fallstudien veranschaulichen die breite Anwendbarkeit von SPS in verschiedenen Bereichen, von der Energiespeicherung über die Biomedizintechnik bis hin zu modernen Werkstoffen. Die Fähigkeit von SPS, Materialien bei niedrigeren Temperaturen schnell zu sintern und zu verdichten, in Verbindung mit der präzisen Prozesssteuerung, macht sie zu einem unschätzbaren Werkzeug für Materialwissenschaftler und Ingenieure. Da Forschung und Entwicklung weiter voranschreiten, ist zu erwarten, dass sich die potenziellen Anwendungen von SPS noch weiter ausweiten und ihre Position als führende Technologie in der Materialverarbeitung festigen werden.
Herausforderungen und Überlegungen bei SPS
Die Einführung der Spark Plasma Sintering (SPS)-Technologie ist mit verschiedenen Herausforderungen und Überlegungen verbunden, die Unternehmen angehen müssen, um ihre Vorteile voll auszuschöpfen. Dazu gehören hohe Ausrüstungskosten, komplexe Betriebsabläufe und die Notwendigkeit einer speziellen Ausbildung. Das Verständnis dieser Herausforderungen und die Entwicklung von Strategien zu ihrer Bewältigung sind entscheidend für die erfolgreiche Integration und Nutzung der SPS-Technologie.
Kosten der Ausrüstung
Eines der Haupthindernisse für die Einführung der SPS-Technologie sind die hohen Anfangsinvestitionen, die für die Ausrüstung erforderlich sind. SPS-Systeme sind anspruchsvoll und umfassen fortschrittliche Funktionen wie präzise Temperatur- und Druckregelung, Vakuumsysteme und spezielle Stromversorgungen. Diese Komponenten erhöhen nicht nur die Anfangskosten, sondern erfordern auch eine regelmäßige Wartung und Kalibrierung, um eine optimale Leistung zu gewährleisten.
Betriebliche Komplexität
Der Betrieb von SPS umfasst mehrere Stufen, einschließlich Vakuumerzeugung, Druckanwendung, Widerstandserhitzung und kontrollierte Abkühlung. Jede Stufe erfordert eine sorgfältige Überwachung und Einstellung, um Fehler zu vermeiden und die gewünschten Materialeigenschaften zu gewährleisten. Die Komplexität dieser Vorgänge erfordert ein hohes Maß an technischem Fachwissen und akribischer Aufmerksamkeit für Details, was für Unternehmen ohne vorherige Erfahrung mit fortschrittlichen Sintertechniken eine Herausforderung darstellen kann.
Spezialisierte Ausbildung
Angesichts des technischen Charakters von SPS muss das Personal, das mit dem Betrieb und der Wartung der Anlagen befasst ist, eine spezielle Schulung absolvieren. Diese Schulung sollte nicht nur die grundlegende Bedienung des SPS-Systems abdecken, sondern auch fortgeschrittene Themen wie Prozessoptimierung, Fehlersuche und Sicherheitsprotokolle. Der Kosten- und Zeitaufwand für diese Schulungen kann erheblich sein und die Einführung der SPS-Technologie möglicherweise verzögern.
Strategien zur Überwindung von Herausforderungen
Um diese Herausforderungen zu bewältigen, können Unternehmen verschiedene Strategien anwenden:
-
Investition in qualitativ hochwertige Ausrüstung: Die Anschaffungskosten sind zwar hoch, aber die Investition in zuverlässige, qualitativ hochwertige SPS-Geräte kann die langfristigen Wartungs- und Betriebskosten senken. Die Wahl von Geräten renommierter Hersteller mit starken Support- und Servicenetzwerken kann auch dazu beitragen, Probleme, die während des Betriebs auftreten, zu mindern.
-
Zusammenarbeit und Partnerschaften: Partnerschaften mit Forschungseinrichtungen oder anderen Unternehmen, die Erfahrung mit SPS haben, können wertvolle Erkenntnisse und Unterstützung bieten. Gemeinsame Projekte können dazu beitragen, die für eine erfolgreiche Umsetzung erforderlichen Kosten und Fachkenntnisse zu teilen.
-
Kontinuierliche Schulung und Entwicklung: Durch Investitionen in die kontinuierliche Schulung der Mitarbeiter kann sichergestellt werden, dass sie mit den neuesten Techniken und bewährten Verfahren im Bereich der Betriebsführung auf dem Laufenden bleiben. Dies kann durch Workshops, Online-Kurse und praktische Schulungen erreicht werden.
-
Prozess-Optimierung: Die Entwicklung robuster, gut dokumentierter und standardisierter Prozesse kann dazu beitragen, die Variabilität zu verringern und die Konsistenz der Ergebnisse zu verbessern. Dazu gehören sorgfältige Experimente und Validierungen, um die optimalen Bedingungen für jedes Material und jede Anwendung zu ermitteln.
-
Fokus auf Forschung und Entwicklung: Kontinuierliche Forschungs- und Entwicklungsarbeit kann Unternehmen dabei helfen, bei der SPS-Technologie an der Spitze zu bleiben. Dies kann die Erforschung neuer Materialien, die Optimierung bestehender Prozesse und die Entwicklung innovativer Anwendungen für SPS-produzierte Komponenten beinhalten.
Schlussfolgerung
Die Einführung der SPS-Technologie bringt zwar einige Herausforderungen mit sich, doch können diese mit den richtigen Strategien und Investitionen effektiv gemeistert werden. Durch die Bewältigung der hohen Kosten, der betrieblichen Komplexität und der Schulungsanforderungen können Unternehmen das volle Potenzial von SPS ausschöpfen, was zu bedeutenden Fortschritten in der Materialwissenschaft und Fertigung führt.
Zukünftige Trends beim Spark-Plasma-Sintern
Die Technologie des Spark-Plasma-Sinterns (SPS), die für ihre schnellen Sinterfähigkeiten bei relativ niedrigen Temperaturen bekannt ist, entwickelt sich ständig weiter und bietet bedeutende Fortschritte in Bezug auf Effizienz, Skalierbarkeit und Anwendungsvielfalt. Da die Nachfrage nach neuen Werkstoffen und effizienten Herstellungsverfahren steigt, steht SPS an der Spitze der technologischen Innovation in der Materialwissenschaft.
Verbesserungen der Effizienz
Einer der Hauptschwerpunkte der SPS-Technologie ist die Verbesserung ihrer Effizienz. Herkömmliche Sinterverfahren können zeit- und energieaufwendig sein, während SPS sowohl die Verarbeitungszeit als auch den Energieverbrauch erheblich reduziert. Zukünftige Entwicklungen zielen darauf ab, diese Aspekte durch die Verfeinerung der Pulsstromtechniken und die Verbesserung der Steuerungssysteme von SPS-Geräten weiter zu optimieren. So könnten beispielsweise Fortschritte bei der Stromversorgung und den Steuerungssystemen eine präzisere Temperatur- und Drucksteuerung ermöglichen, was zu effizienteren Sinterprozessen führen würde.
Verbesserungen der Skalierbarkeit
Die Skalierbarkeit ist ein weiterer kritischer Aspekt der SPS-Technologie. Gegenwärtig wird die SPS überwiegend in Laborumgebungen und bei der Produktion in kleinem Maßstab eingesetzt. Um jedoch den Anforderungen der Industrie gerecht zu werden, müssen künftige SPS-Systeme größere Mengen und komplexere Formen verarbeiten können. Die Forscher erforschen neue Formenmaterialien und -konstruktionen, die höheren Drücken und Temperaturen standhalten und die Integrität und Wiederverwendbarkeit der Formen gewährleisten. Darüber hinaus könnte die Integration fortschrittlicher Robotertechnik und Automatisierung in SPS-Anlagen die Produktion größerer und komplizierterer Teile erleichtern und SPS zu einer praktikablen Option für die Großserienfertigung machen.
Ausweitung auf neue Materialarten und Branchen
Die SPS-Technologie wird traditionell für das Sintern von Metallen und Keramiken eingesetzt. Ihre einzigartigen Fähigkeiten bieten jedoch Potenzial für die Ausweitung auf neue Materialtypen und Branchen. Künftige Forschungsarbeiten werden sich wahrscheinlich auf die Anwendung von SPS auf eine breitere Palette von Werkstoffen konzentrieren, darunter Polymere, Verbundwerkstoffe und Nanomaterialien. Diese Ausweitung könnte neue Anwendungen in Sektoren wie Elektronik, Luft- und Raumfahrt und Biomedizintechnik eröffnen, in denen die präzise Steuerung von Materialeigenschaften entscheidend ist.
Ökologischer und wirtschaftlicher Nutzen
Die ökologischen und wirtschaftlichen Vorteile der SPS sind ebenfalls ein wichtiger Faktor für ihre künftige Entwicklung. Der energieeffiziente und abfallarme Produktionsprozess von SPS steht im Einklang mit den globalen Nachhaltigkeitszielen. Da die Industrie zunehmend nach umweltfreundlichen Fertigungslösungen sucht, könnte SPS eine bevorzugte Methode zur Herstellung von Hochleistungsmaterialien werden. Darüber hinaus können die kürzeren Verarbeitungszeiten und die niedrigeren Energiekosten, die mit SPS verbunden sind, zu erheblichen wirtschaftlichen Einsparungen führen, was es zu einer attraktiven Option für Hersteller macht.
Technologische Integration und Kollaboration
Schließlich wird die Zukunft der SPS-Technologie wahrscheinlich eine stärkere Integration mit anderen fortschrittlichen Fertigungstechnologien und die Zusammenarbeit zwischen verschiedenen Bereichen beinhalten. So könnte beispielsweise die Kombination von SPS mit additiven Fertigungsverfahren zur Entwicklung hybrider Fertigungsprozesse führen, die die Stärken beider Technologien nutzen. Darüber hinaus könnte die interdisziplinäre Forschung unter Einbeziehung der Materialwissenschaften, der Elektrotechnik und des Maschinenbaus zu Durchbrüchen beim Verständnis und der Optimierung des SPS-Prozesses führen.
Zusammenfassend lässt sich sagen, dass die Zukunft des Spark-Plasma-Sinterns vielversprechend ist und potenzielle Fortschritte es zu einer effizienteren, skalierbaren und vielseitigen Technologie machen werden. Wenn Forschung und Entwicklung weitergehen, könnte SPS die Art und Weise, wie wir fortschrittliche Materialien herstellen, revolutionieren, zu Innovationen in verschiedenen Branchen beitragen und nachhaltige Fertigungsverfahren fördern.
Schlussfolgerung: Die Rolle der SPS bei der Gestaltung der Materialwissenschaft
Zusammenfassend lässt sich sagen, dass dasSpark-Plasma-Sintern (SPS) Technik als eine transformative Technologie im Bereich der Materialwissenschaft hervor. Seine Fähigkeit, Werkstoffe schnell und feinkörnig zu sintern, sowie seine Effizienz und Vielseitigkeit machen SPS zu einem Eckpfeiler der modernen Materialverarbeitung. Mit Blick auf die Zukunft ist SPS in der Lage, bedeutende Innovationen voranzutreiben, seine Anwendungen in verschiedenen Branchen zu erweitern und den Weg für die Entwicklung fortschrittlicher Hochleistungsmaterialien zu ebnen. Die kontinuierliche Weiterentwicklung und Einführung der SPS-Technologie wird zweifellos die Zukunft der Materialwissenschaft prägen und neue Möglichkeiten und Lösungen für komplexe Materialprobleme bieten.
Kontaktieren Sie uns für eine kostenlose Beratung
Die Produkte und Dienstleistungen von KINTEK LAB SOLUTION werden von Kunden auf der ganzen Welt anerkannt. Unsere Mitarbeiter helfen Ihnen gerne bei allen Fragen weiter. Kontaktieren Sie uns für eine kostenlose Beratung und sprechen Sie mit einem Produktspezialisten, um die am besten geeignete Lösung für Ihre Anwendungsanforderungen zu finden!