Wenn Keramik, insbesondere Ton, in einem Ofen gebrannt wird, durchlaufen der Kohlenstoff und die organischen Verbindungen, die sie enthalten, einen Prozess, der als Oxidation bezeichnet wird, bei dem sie verbrennen.Diese Verbrennung ist unerlässlich, um Fehler im Endprodukt zu vermeiden, wie etwa Aufblähungen oder Verfärbungen, die auftreten können, wenn der Kohlenstoff nicht vollständig entfernt wird.Bei diesem Verfahren wird das Material auf hohe Temperaturen erhitzt, in der Regel zwischen 500°C und 900°C, wobei der Kohlenstoff mit Sauerstoff reagiert und Kohlendioxid und andere Gase bildet, die dann aus dem Ofen abgeleitet werden.Nach dem Brennen wird das Material abgekühlt und weiterverarbeitet, häufig durch Mahlen und Pelletieren, bevor es für den Transport verpackt wird.
Die wichtigsten Punkte werden erklärt:
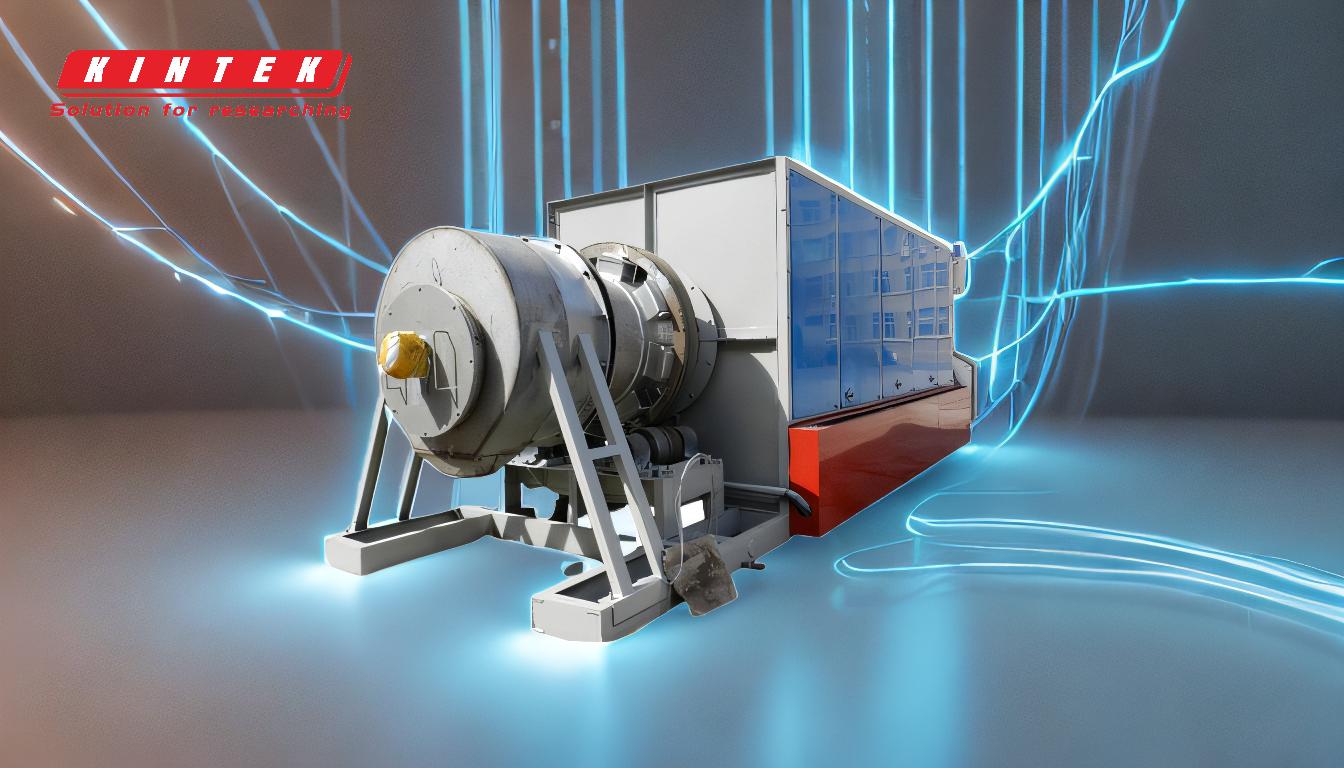
-
Das Vorhandensein von Kohlenstoff in Keramik:
- Keramische Materialien, insbesondere Ton, enthalten von Natur aus Kohlenstoff und organische Verbindungen.Diese können aus der Zersetzung von pflanzlichen und tierischen Stoffen in dem Boden stammen, in dem der Ton gebildet wird.
-
Die Notwendigkeit, Kohlenstoff zu verbrennen:
- Während des Brennvorgangs im Ofen ist es wichtig, den Kohlenstoff und die organischen Verbindungen zu verbrennen.Werden diese nicht entfernt, können sie Defekte in den keramischen Erzeugnissen verursachen, wie Aufblähungen, schwarze Kerne oder Verfärbungen, die die strukturelle Integrität und die ästhetische Qualität des Endprodukts beeinträchtigen.
-
Oxidationsprozess:
- Das Abbrennen des Kohlenstoffs erfolgt durch einen Oxidationsprozess.Dabei wird das keramische Material auf Temperaturen zwischen 500°C und 900°C erhitzt.Bei diesen Temperaturen reagiert der Kohlenstoff mit dem Sauerstoff in der Ofenatmosphäre und bildet Kohlendioxid (CO₂) und andere gasförmige Nebenprodukte.
- Der Oxidationsprozess wird sorgfältig kontrolliert, um eine vollständige Verbrennung der kohlenstoffhaltigen Materialien zu gewährleisten.Bei unzureichender Oxidation können Kohlenstoffreste zurückbleiben, die zu den oben genannten Mängeln führen.
-
Komplikationen beim Brennen:
- Die Verbrennung von Kohlenstoff und organischen Verbindungen kann während des Brennvorgangs zu Komplikationen führen.Dazu gehört die Freisetzung von Gasen, die bei unzureichender Entlüftung zu Aufblähungen oder Nadellöchern im Keramikkörper führen können.Außerdem kann eine schnelle Oxidation zu einem thermischen Schock führen, der die Keramikstücke sprengen kann.
-
Verarbeitung nach dem Brennen:
- Nach dem Ausbrennen des Kohlenstoffs und dem Brennen der Keramik wird das Material abgekühlt.Dieser Abkühlungsprozess muss kontrolliert werden, um thermische Spannungen zu vermeiden, die zu Rissen führen könnten.
- Nach dem Abkühlen kann das Material weiterverarbeitet werden, z. B. durch Mahlen, um die gewünschte Partikelgröße zu erreichen, durch Pelletieren, um die Handhabung zu erleichtern, und durch Verpacken für den Transport.Auf diese Weise wird sichergestellt, dass das Material für die nächste Verwendung oder für den Vertrieb bereit ist.
-
Die Bedeutung der Temperaturkontrolle:
- Die Temperatur, bei der die Kohle abbrennt, ist entscheidend.Ist die Ofentemperatur zu niedrig, verbrennt der Kohlenstoff möglicherweise nicht vollständig, was zu Defekten führt.Umgekehrt kann eine zu hohe Temperatur andere Probleme verursachen, wie z. B. einen Überbrand, der die Keramikstruktur schwächen kann.
- Die Betreiber von Brennöfen müssen die Temperatur während des gesamten Brennvorgangs sorgfältig überwachen und steuern, um optimale Ergebnisse zu erzielen.
-
Umweltaspekte:
- Die Freisetzung von Kohlendioxid und anderen Gasen während des Brennvorgangs hat Auswirkungen auf die Umwelt.Moderne Brennöfen sind häufig mit Systemen ausgestattet, die diese Emissionen auffangen und behandeln, um ihre Umweltauswirkungen zu minimieren.
- Die effiziente Verbrennung von Kohlenstoff trägt auch dazu bei, den gesamten Kohlenstoff-Fußabdruck des Keramikherstellungsprozesses zu verringern.
Zusammenfassend lässt sich sagen, dass das Abbrennen von Kohlenstoff in einem Brennofen ein kritischer Schritt im keramischen Herstellungsprozess ist.Es handelt sich um einen sorgfältig kontrollierten Oxidationsprozess, der die vollständige Entfernung des Kohlenstoffs und der organischen Verbindungen gewährleistet und dadurch Mängel im Endprodukt verhindert.Eine ordnungsgemäße Temperaturregelung, Entlüftung und Nachbearbeitung sind für die Herstellung hochwertiger Keramik unerlässlich.Darüber hinaus spielen Umweltaspekte eine Rolle bei der Beherrschung der während dieses Prozesses entstehenden Emissionen.
Zusammenfassende Tabelle:
Hauptaspekt | Einzelheiten |
---|---|
Vorhandensein von Kohlenstoff | Keramik, insbesondere Ton, enthält Kohlenstoff aus zersetztem organischem Material. |
Notwendigkeit der Verbrennung von Kohlenstoff | Verhindert Defekte wie Aufblähung, Verfärbung und schwarze Kernbildung. |
Oxidationsprozess | Kohlenstoff reagiert mit Sauerstoff bei 500°C-900°C und bildet CO₂, das die Verbrennung sicherstellt. |
Komplikationen beim Brennen | Die Freisetzung von Gas kann zu Blähungen oder Rissen führen, wenn es nicht richtig entlüftet wird. |
Verarbeitung nach der Verbrennung | Kühlung, Zerkleinerung, Pelletierung und Verpackung sorgen für die Fertigstellung des Materials. |
Temperaturkontrolle | Entscheidend, um Unter- oder Überbrennen zu vermeiden, was die Keramik schwächen kann. |
Auswirkungen auf die Umwelt | Die Emissionen werden kontrolliert, um den Kohlenstoff-Fußabdruck der Keramikproduktion zu reduzieren. |
Sichern Sie sich hochwertige Keramik mit fachkundigen Brennlösungen. Kontaktieren Sie uns noch heute für weitere Informationen!