Das PVD-Sputterverfahren ist eine weit verbreitete Technik zur Abscheidung dünner Schichten, bei der Atome oder Moleküle durch den Beschuss mit hochenergetischen Ionen, in der Regel Argon-Ionen, aus einem Zielmaterial ausgestoßen werden.Diese ausgestoßenen Atome wandern durch eine Vakuumkammer und kondensieren auf einem Substrat, um eine dünne, gleichmäßige Schicht zu bilden.Der Prozess beginnt mit der Erzeugung eines Plasmas, das Argon-Ionen und Elektronen enthält.Diese Ionen werden in Richtung des Zielmaterials beschleunigt, wodurch Atome abgesputtert werden.Die gesputterten Atome wandern dann durch die Kammer und lagern sich auf dem Substrat ab, so dass ein dünner Film entsteht.Dieses Verfahren lässt sich sehr gut steuern und wird in verschiedenen Branchen eingesetzt, z. B. in der Halbleiterindustrie, der Optik und bei dekorativen Beschichtungen.
Die wichtigsten Punkte werden erklärt:
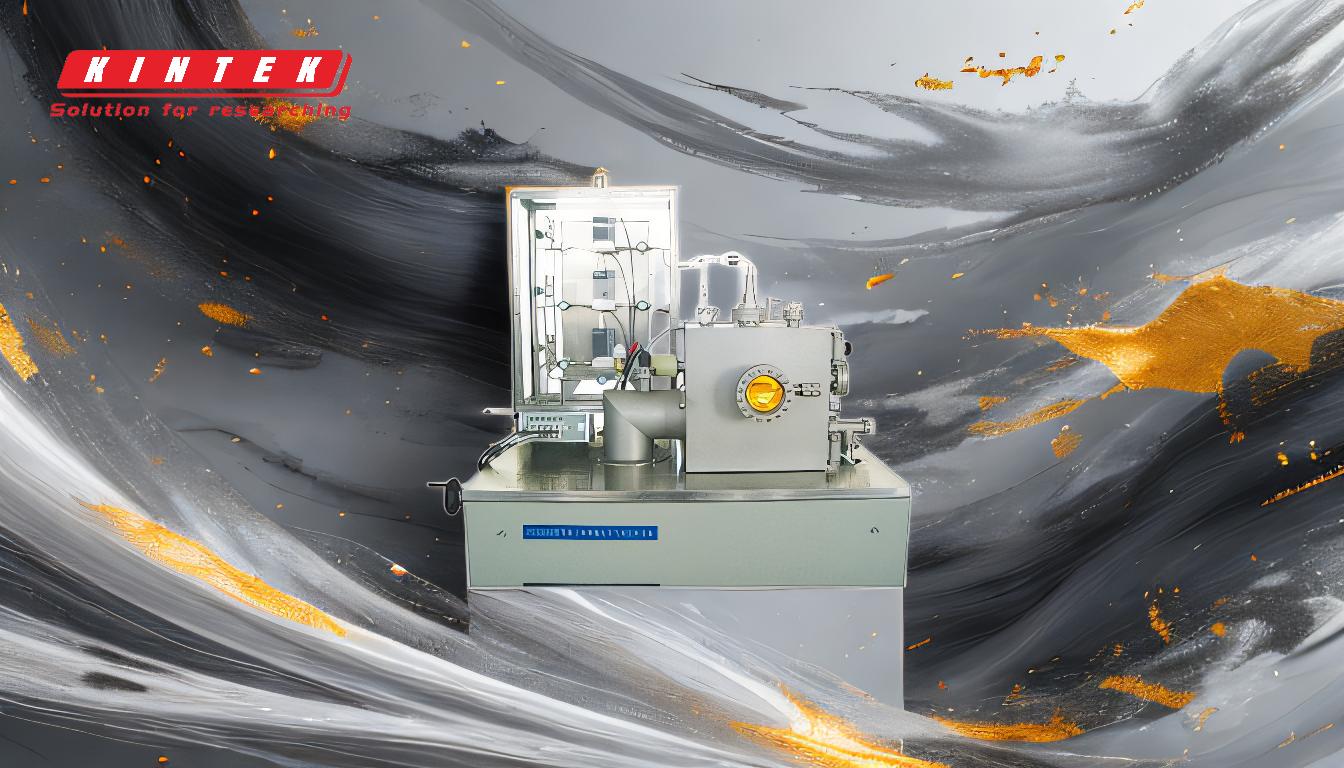
-
Einführung in die PVD-Sputtertechnik:
- PVD-Sputtern (Physical Vapor Deposition) ist ein Verfahren zur Abscheidung dünner Materialschichten auf einem Substrat.
- Es handelt sich um eine vakuumbasierte Technik, bei der Atome oder Moleküle aus einem Zielmaterial herausgeschleudert werden und sich auf einem Substrat ablagern.
-
Erzeugung von Plasma:
- Das Verfahren beginnt mit der Erzeugung eines Plasmas in einer Vakuumkammer.
- Das Plasma wird durch Ionisierung eines Gases, in der Regel Argon, erzeugt, wodurch ein Gemisch aus Argon-Ionen und Elektronen entsteht.
- Dieses Plasma ist für den Sputterprozess unerlässlich, da es die hochenergetischen Ionen liefert, die für den Beschuss des Zielmaterials benötigt werden.
-
Bombardierung des Zielmaterials:
- Hochenergetische Argon-Ionen aus dem Plasma werden in Richtung des Zielmaterials beschleunigt.
- Wenn diese Ionen auf das Target treffen, übertragen sie ihre Energie auf die Atome des Targetmaterials.
- Dieser Energietransfer führt dazu, dass Atome oder Moleküle von der Oberfläche des Targets abgestoßen werden, ein Vorgang, der als Sputtern bezeichnet wird.
-
Transport von gesputterten Atomen:
- Die ausgestoßenen Atome oder Moleküle bewegen sich durch die Vakuumkammer.
- Die Vakuumumgebung sorgt dafür, dass sich die gesputterten Atome in einer geraden Linie bewegen, ohne mit Gasmolekülen zusammenzustoßen, die andernfalls ihre Bahn verändern und die Qualität der abgeschiedenen Schicht beeinträchtigen könnten.
-
Abscheidung auf dem Substrat:
- Die gesputterten Atome erreichen schließlich das Substrat, wo sie kondensieren und einen dünnen Film bilden.
- Das Substrat wird in der Regel gegenüber dem Zielmaterial positioniert, um eine gleichmäßige Abscheidung zu gewährleisten.
- Die Dicke und die Eigenschaften der Schicht können durch die Einstellung von Parametern wie der dem Plasma zugeführten Leistung, dem Druck in der Kammer und dem Abstand zwischen Target und Substrat gesteuert werden.
-
Vorteile des PVD-Sputterns:
- Präzision:Das Verfahren ermöglicht eine genaue Kontrolle über die Dicke und Zusammensetzung der abgeschiedenen Schicht.
- Vielseitigkeit:Es kann zur Abscheidung einer Vielzahl von Materialien verwendet werden, darunter Metalle, Legierungen und Keramiken.
- Gleichmäßigkeit:Die Vakuumumgebung und die kontrollierten Parameter gewährleisten eine gleichmäßige und konsistente Schichtabscheidung.
- Haftung:Der hochenergetische Prozess führt zu einer starken Haftung der Schicht auf dem Substrat.
-
Anwendungen des PVD-Sputterns:
- Halbleiter:Wird bei der Herstellung von integrierten Schaltkreisen und anderen elektronischen Komponenten verwendet.
- Optik:Wird bei der Herstellung von Antireflexionsbeschichtungen, Spiegeln und optischen Filtern verwendet.
- Dekorative Beschichtungen:Zur Herstellung haltbarer und ästhetisch ansprechender Beschichtungen auf Konsumgütern.
- Harte Beschichtungen:Anwendung bei Werkzeugen und Komponenten zur Verbesserung der Verschleißfestigkeit und Haltbarkeit.
-
Herausforderungen und Überlegungen:
- Kosten:Die für das PVD-Sputtern erforderliche Ausrüstung und Vakuumumgebung kann teuer sein.
- Komplexität:Das Verfahren erfordert eine präzise Kontrolle verschiedener Parameter, die komplex sein kann und qualifiziertes Personal erfordert.
- Grenzen des Materials:Obwohl sie vielseitig sind, können nicht alle Materialien einfach gesputtert werden, und einige erfordern spezielle Bedingungen oder Ziele.
Zusammenfassend lässt sich sagen, dass das PVD-Sputtern ein hochgradig kontrolliertes und vielseitiges Verfahren zur Abscheidung von Dünnschichten ist, bei dem Atome aus einem Zielmaterial durch Ionenbeschuss mit hoher Energie ausgestoßen werden.Das Verfahren wird aufgrund seiner Präzision, Gleichmäßigkeit und der Fähigkeit, eine breite Palette von Materialien abzuscheiden, in verschiedenen Branchen eingesetzt.Es bringt jedoch auch Herausforderungen wie Kosten und Komplexität mit sich, die bei der Auswahl dieses Verfahrens für bestimmte Anwendungen berücksichtigt werden müssen.
Zusammenfassende Tabelle:
Aspekt | Einzelheiten |
---|---|
Prozess-Übersicht | Ausstoß von Atomen aus einem Zielmaterial durch hochenergetischen Ionenbeschuss. |
Wichtigste Schritte | Plasmaerzeugung, Beschuss des Ziels, Atomtransport und Schichtabscheidung. |
Vorteile | Präzision, Vielseitigkeit, Gleichmäßigkeit und starke Haftung. |
Anwendungen | Halbleiter, Optik, dekorative Beschichtungen und harte Beschichtungen. |
Herausforderungen | Hohe Kosten, komplexe Prozesse und Materialbeschränkungen. |
Entdecken Sie, wie das PVD-Sputtern Ihren Fertigungsprozess verbessern kann. Kontaktieren Sie unsere Experten noch heute !