Das Induktionslöten ist ein hocheffizientes und präzises Verfahren zum Verbinden von Metallen mit Hilfe von durch elektromagnetische Induktion erzeugter Wärme.Die Dauer des Prozesses hängt von mehreren Faktoren ab, darunter die zu verbindenden Werkstoffe, die Größe und Geometrie der Bauteile, die Art des verwendeten Zusatzwerkstoffs und die Leistung des Induktionserwärmungssystems.Im Allgemeinen kann das Induktionslöten zwischen einigen Sekunden und mehreren Minuten dauern.Das Verfahren ist schneller als herkömmliche Lötverfahren, da die Erwärmung lokal erfolgt, wodurch die Wärmeeinflusszonen minimiert und die Gesamtzykluszeiten verkürzt werden.Die richtige Einstellung und die Optimierung der Parameter sind entscheidend, um gleichbleibende und hochwertige Ergebnisse zu erzielen.
Die wichtigsten Punkte werden erklärt:
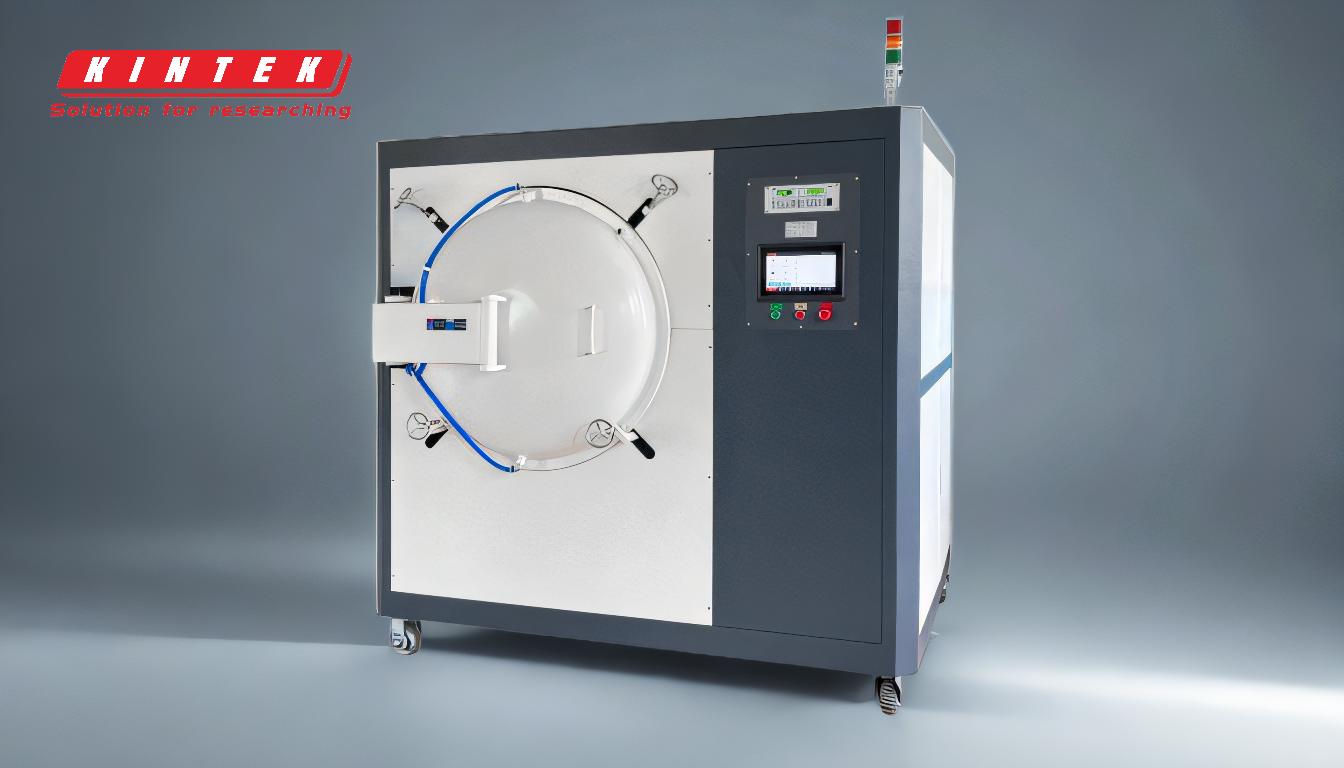
-
Faktoren, die die Induktionslötdauer beeinflussen
- Materialeigenschaften:Die Wärmeleitfähigkeit und der Schmelzpunkt der Grundmetalle und des Zusatzwerkstoffs beeinflussen die Erhitzungszeit erheblich.Materialien mit hoher Wärmeleitfähigkeit, wie z. B. Kupfer, erwärmen sich schneller als solche mit geringerer Leitfähigkeit, wie z. B. Edelstahl.
- Bauteilgröße und -geometrie:Größere oder komplexere Teile benötigen mehr Zeit für eine gleichmäßige Erwärmung.Dünne Abschnitte erhitzen sich schneller als dicke Abschnitte, und gleichmäßige Geometrien lassen sich leichter erhitzen als unregelmäßige Formen.
- Eigenschaften der Schweißzusatzwerkstoffe:Der Schmelzpunkt und die Fließeigenschaften des Zusatzwerkstoffs beeinflussen die Lötzeit.Zusatzwerkstoffe mit niedrigeren Schmelzpunkten verkürzen die Gesamtzykluszeit.
- Induktionserwärmung Leistung:Induktionssysteme mit höherer Leistung können die Wärme schneller erzeugen und so die Gesamtlötdauer verkürzen.Eine zu hohe Leistung muss jedoch vermieden werden, um eine Überhitzung oder Beschädigung der Bauteile zu vermeiden.
-
Typische Zeitspanne beim Induktionslöten
- Induktionslöten ist im Allgemeinen viel schneller als traditionelle Verfahren wie Brenner- oder Ofenlöten.
- Bei kleinen Bauteilen kann der Prozess nur 5 bis 10 Sekunden .
- Mittelgroße Teile benötigen möglicherweise 30 Sekunden bis 2 Minuten .
- Größere oder komplexere Baugruppen können 2 bis 5 Minuten oder länger, je nach den oben genannten Faktoren.
-
Vorteile des Induktionslötens in Bezug auf die Zeiteffizienz
- Lokalisierte Erwärmung:Beim Induktionslöten wird nur der Bereich erwärmt, in dem sich die Verbindung befindet, wodurch die Gesamterwärmungszeit verkürzt und der Energieverbrauch minimiert wird.
- Schnelle Erwärmungsraten:Das elektromagnetische Induktionsverfahren erzeugt die Wärme direkt im Werkstück und ermöglicht so eine schnellere Erwärmung im Vergleich zu externen Erwärmungsmethoden.
- Reduzierte Zykluszeiten:Die Möglichkeit, die Erwärmungs- und Abkühlungszyklen präzise zu steuern, gewährleistet eine effiziente Produktion, insbesondere in der Großserienfertigung.
-
Optimierung der Induktionslötdauer
- Richtiges Spulendesign:Die Induktionsspule muss an die Geometrie des Werkstücks angepasst werden, um eine gleichmäßige und effiziente Erwärmung zu gewährleisten.
- Abstimmung der Parameter:Die Einstellung von Parametern wie Leistung, Frequenz und Heizzeit ist wichtig, um optimale Ergebnisse ohne Über- oder Unterhitzung zu erzielen.
- Vor dem Einsetzen des Zusatzwerkstoffs:Die korrekte Positionierung des Schweißzusatzes vor dem Erhitzen gewährleistet ein gleichmäßiges Schmelzen und Fließen und reduziert die Notwendigkeit längerer Heizzeiten.
-
Anwendungen und Beispiele
- Autoindustrie:Induktionslöten wird zum Fügen von Bauteilen wie Wärmetauschern und Getriebeteilen verwendet, bei denen schnelle Zykluszeiten für die Großserienproduktion entscheidend sind.
- Elektronik:Kleine Bauteile wie Steckverbinder und Klemmen werden oft in Sekundenschnelle durch Induktionserwärmung gelötet.
- Luft- und Raumfahrt:Komplexe Baugruppen mit strengen Qualitätsanforderungen profitieren von der Präzision und Schnelligkeit des Induktionslötens.
-
Vergleich mit anderen Lötverfahren
- Brennerlöten:In der Regel langsamer und weniger gleichmäßig aufgrund der manuellen Steuerung und der breiteren Wärmeverteilung.
- Hartlöten im Ofen:Es eignet sich für große Chargen, erfordert jedoch häufig längere Erwärmungs- und Abkühlungszyklen, was es für kleine oder mittelgroße Teile weniger zeitsparend macht.
- Induktionslöten:Bietet die beste Kombination aus Geschwindigkeit, Präzision und Wiederholbarkeit und ist damit ideal für moderne Fertigungsumgebungen.
Zusammenfassend lässt sich sagen, dass das Induktionslöten ein vielseitiges und zeitsparendes Verfahren ist, das auf spezifische Anwendungsanforderungen zugeschnitten werden kann.Durch das Verständnis und die Optimierung der Faktoren, die die Lötzeit beeinflussen, können Hersteller qualitativ hochwertige Verbindungen mit minimalen Zykluszeiten erzielen, was die Produktivität erhöht und die Kosten senkt.
Zusammenfassende Tabelle:
Faktor | Einfluss auf die Lötzeit |
---|---|
Materialeigenschaften | Hohe Wärmeleitfähigkeit (z. B. Kupfer) erwärmt sich schneller als geringe Leitfähigkeit (z. B. Stahl). |
Bauteilgröße/Geometrie | Größere oder komplexe Teile brauchen länger; dünne Abschnitte erhitzen sich schneller als dicke. |
Schweißzusatzwerkstoff | Schweißzusatzwerkstoffe mit niedrigerem Schmelzpunkt reduzieren die Zykluszeit. |
Leistung der Induktionserwärmung | Systeme mit höherer Leistung erwärmen schneller, erfordern aber eine sorgfältige Kontrolle, um Schäden zu vermeiden. |
Typischer Zeitbereich | Kleine Teile: 5-10 Sekunden; Mittlere Teile: 30 Sekunden-2 Minuten; Große Teile: 2-5 Minuten oder mehr. |
Optimieren Sie Ihren Induktionslötprozess für schnellere, qualitativ hochwertige Ergebnisse - Kontaktieren Sie noch heute unsere Experten !