Die Dauer des Sinterprozesses ist je nach Material, Technik und den spezifischen Anforderungen an das Endprodukt sehr unterschiedlich.Im Allgemeinen kann das Sintern zwischen einigen Millisekunden und über 24 Stunden dauern.Der Prozess selbst kann nur Sekunden dauern, aber die Schritte nach dem Sintern können die Gesamtzeit auf mehrere Stunden verlängern.Faktoren wie Temperatur, Heizrate, Druck, Partikelgröße, Zusammensetzung und die Sinteratmosphäre (z. B. Luft, Vakuum oder Inertgase) spielen eine entscheidende Rolle bei der Bestimmung der Sinterzeit.Hochtemperatursintern kann Materialeigenschaften wie Zugfestigkeit und Kerbschlagarbeit verbessern, erfordert aber auch eine genaue Kontrolle der Sinterumgebung.Bei vielen Anwendungen dauert der Sinterprozess typischerweise zwischen 15 und 20 Stunden, je nach Material und gewünschter Dichte des Endprodukts.
Die wichtigsten Punkte erklärt:
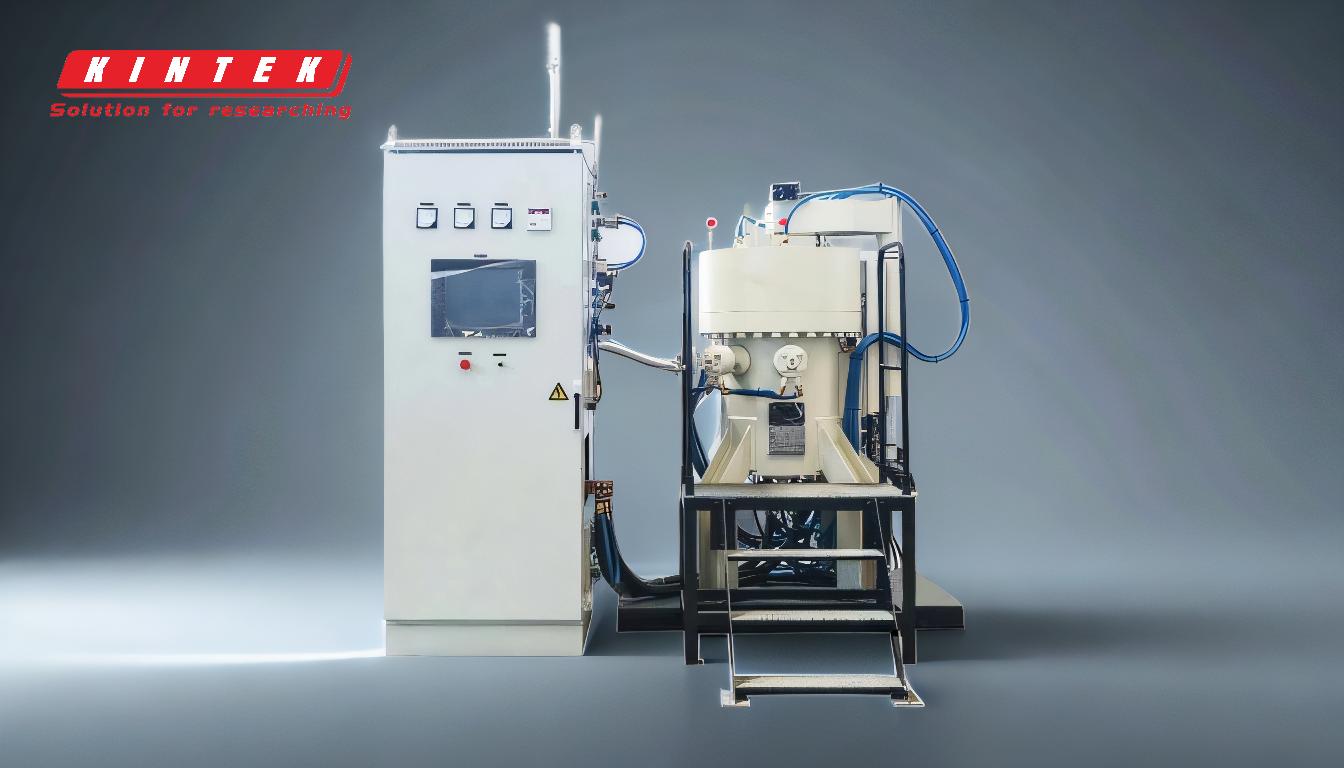
-
Bereich der Sinterzeiten:
- Das Sintern kann zwischen einigen Millisekunden und über 24 Stunden dauern.
- Der Prozess selbst kann nur Sekunden dauern, aber die Schritte nach dem Sintern können die Gesamtzeit auf mehrere Stunden verlängern.
-
Faktoren, die die Sinterzeit beeinflussen:
- Temperatur:Bestimmt die Sinterkinetik und die Materialeigenschaften.Höhere Temperaturen können den Prozess beschleunigen, müssen aber sorgfältig kontrolliert werden, um eine Verschlechterung des Materials zu vermeiden.
- Aufheizrate:Beeinflusst die Verdichtung.Eine schnellere Aufheizrate kann die Sinterzeit verkürzen, kann aber zu einer ungleichmäßigen Verdichtung führen.
- Druck:Verbessert die Umstrukturierung der Partikel und beseitigt die Porosität, was die Sinterzeit verkürzen kann.
- Partikelgröße und -zusammensetzung:Kleinere Partikel und homogene Zusammensetzungen begünstigen eine bessere Verdichtung und können die Sinterzeit verkürzen.
-
Sinter-Atmosphäre:
- Die Atmosphäre (z. B. Luft, Vakuum oder Argon/Stickstoff) kann den Sinterprozess erheblich beeinflussen.Inerte Atmosphären werden häufig verwendet, um Oxidation und andere unerwünschte Reaktionen zu verhindern, die die Sinterzeit und die endgültigen Materialeigenschaften beeinträchtigen können.
-
Anforderungen an Material und Dichte:
- Temperatur und Zeit des Sinterofens hängen vom verwendeten Material und der gewünschten Dichte des Endprodukts ab.Verschiedene Materialien haben unterschiedliche Sinteranforderungen, und das Erreichen höherer Dichten kann längere Sinterzeiten erfordern.
-
Typische Sinterdauern:
- Bei vielen industriellen Anwendungen dauert der Sinterprozess in der Regel zwischen 15 und 20 Stunden.Diese Dauer kann je nach dem spezifischen Material, den gewünschten Eigenschaften und der Art des verwendeten Sinterofens (z. B. Förderband-, Schub- oder Chargenofen) variieren.
-
Sinterung nach der Formgebung:
- Während der anfängliche Sinterprozess schnell abläuft, können die Schritte nach dem Sintern mehrere Stunden dauern.Diese Schritte sind entscheidend für das Erreichen der endgültigen gewünschten Eigenschaften und Abmessungen des gesinterten Teils.
-
Auswirkungen auf die Materialeigenschaften:
- Das Hochtemperatursintern kann die Zugfestigkeit, die Biegewechselfestigkeit und die Kerbschlagarbeit erhöhen.Das Erreichen dieser Eigenschaften erfordert jedoch oft eine genaue Kontrolle der Sinterumgebung und kann die gesamte Sinterzeit verlängern.
Zusammenfassend lässt sich sagen, dass die Sinterzeit sehr variabel ist und von einer Vielzahl von Faktoren abhängt, darunter Materialeigenschaften, gewünschte Ergebnisse und Prozessbedingungen.Das Verständnis dieser Faktoren ist entscheidend für die Optimierung des Sinterprozesses, um die gewünschten Materialeigenschaften effizient zu erreichen.
Zusammenfassende Tabelle:
Faktor | Einfluss auf die Sinterzeit |
---|---|
Temperatur | Höhere Temperaturen beschleunigen die Sinterung, erfordern aber eine genaue Kontrolle, um eine Verschlechterung des Materials zu vermeiden. |
Aufheizrate | Schnelleres Aufheizen verkürzt die Zeit, kann aber zu ungleichmäßiger Verdichtung führen. |
Druck | Verbessert die Umlagerung der Partikel und verkürzt die Sinterzeit. |
Partikelgröße | Kleinere Partikel fördern eine schnellere Verdichtung. |
Sinteratmosphäre | Inerte Gase verhindern die Oxidation, die sich auf die Zeit und die endgültigen Eigenschaften auswirkt. |
Material/Dichte | Dichtere Materialien oder höhere Dichteanforderungen verlängern die Sinterzeit. |
Typische Dauer | 15-20 Stunden für viele industrielle Anwendungen, je nach Material und Ofentyp. |
Benötigen Sie Hilfe bei der Optimierung Ihres Sinterprozesses? Kontaktieren Sie noch heute unsere Experten für maßgeschneiderte Lösungen!