Glühen ist ein kritisches Wärmebehandlungsverfahren, das zur Veränderung der physikalischen und mechanischen Eigenschaften von Werkstoffen, vor allem von Metallen, eingesetzt wird. Es ist unter bestimmten Bedingungen erforderlich, wenn das Material erweicht, dehnbarer gemacht oder von inneren Spannungen befreit werden soll. Dieses Verfahren ist wichtig, um die Bearbeitbarkeit zu verbessern, die Kaltumformung zu erleichtern, die mechanischen oder elektrischen Eigenschaften zu verbessern und die Maßhaltigkeit zu gewährleisten. Besonders nützlich ist das Glühen nach Herstellungsprozessen wie Gießen oder Kaltumformung, wo innere Spannungen und Härte die Leistungsfähigkeit des Materials beeinträchtigen können. Durch Erhitzen des Materials auf seine Rekristallisationstemperatur, Halten auf dieser Temperatur und anschließendes Abkühlen mit kontrollierter Geschwindigkeit trägt das Glühen zu einer gleichmäßigeren und besser verarbeitbaren Struktur bei.
Die wichtigsten Punkte werden erklärt:
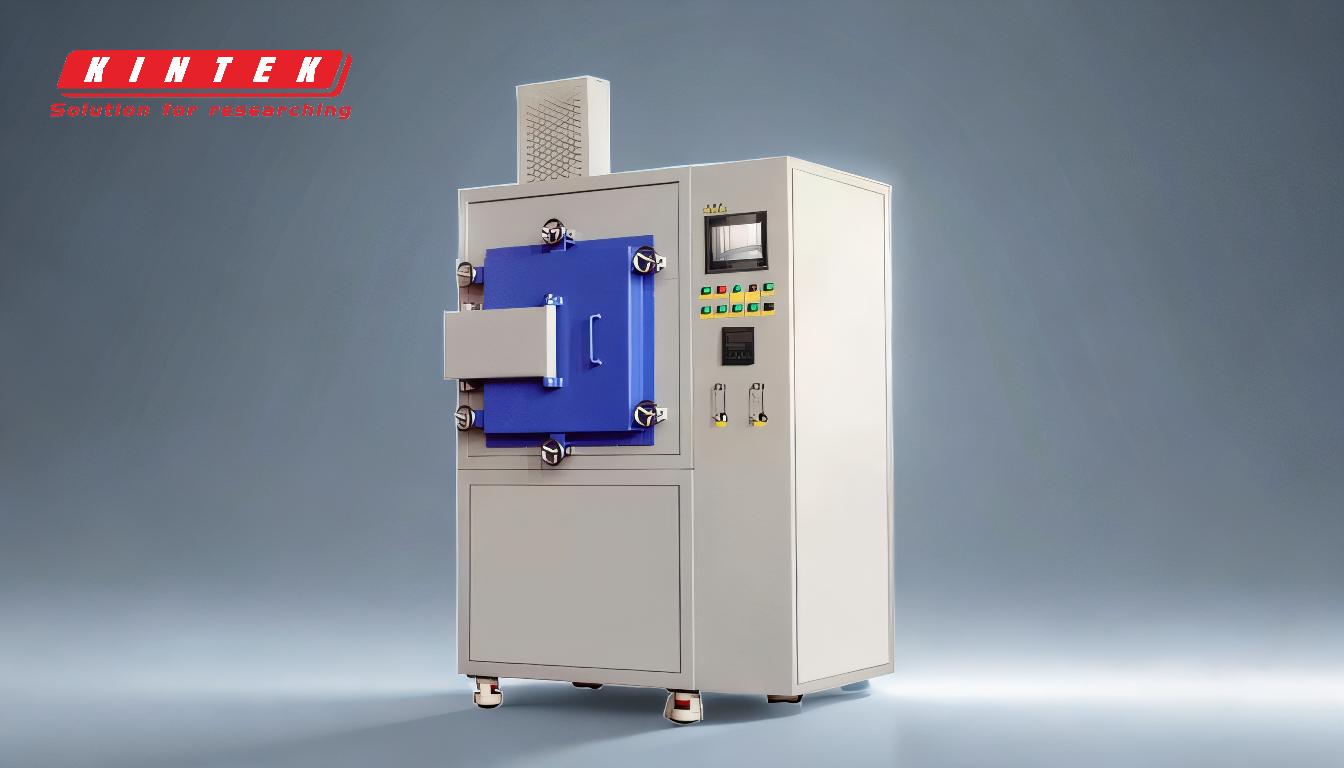
-
Verringerung der Härte und Erhöhung der Duktilität:
- Das Glühen dient in erster Linie dazu, die Härte eines Werkstoffs zu verringern und ihn weicher und dehnbarer zu machen. Dies wird erreicht, indem das Material auf eine bestimmte Temperatur (in der Regel seine Rekristallisationstemperatur) erhitzt und dann langsam abgekühlt wird. Durch diesen Prozess wird die Anzahl der Versetzungen in der Kristallstruktur verringert, was wiederum die Härte verringert und die Zähigkeit erhöht. Dadurch lässt sich das Material leichter bearbeiten, kaltverformen oder formen, ohne dass die Gefahr von Rissen oder Brüchen unter Belastung besteht.
-
Entlastung von inneren Spannungen:
- Bei Fertigungsprozessen wie Gießen, Schweißen oder Kaltverformung können in den Materialien innere Spannungen entstehen. Diese Spannungen können mit der Zeit zu Materialversagen oder Verformung führen. Das Glühen hilft, diese Spannungen abzubauen, indem es dem Material ermöglicht, eine stabilere und gleichmäßigere innere Struktur zu erreichen. Dies ist besonders wichtig für Bauteile, die im Betrieb mechanischen Belastungen oder Temperaturschwankungen ausgesetzt sind.
-
Verbesserung der Bearbeitbarkeit:
- Zu harte Werkstoffe lassen sich nur schwer bearbeiten, was zu erhöhtem Werkzeugverschleiß und schlechter Oberflächengüte führt. Durch das Glühen wird das Material weicher und lässt sich leichter schneiden, bohren oder formen. Dies ist besonders vorteilhaft für Metalle, die umfangreichen Bearbeitungsvorgängen unterzogen werden müssen, da es das Risiko von Werkzeugbrüchen verringert und die Effizienz des Bearbeitungsprozesses verbessert.
-
Erleichterung der Kaltbearbeitung:
- Kaltverformungsverfahren wie Walzen, Ziehen oder Schmieden können die Härte und Festigkeit eines Werkstoffs erheblich erhöhen, machen ihn aber auch spröder. Das Glühen wird häufig zwischen den Kaltverformungsschritten durchgeführt, um die Duktilität wiederherzustellen und die Sprödigkeit zu verringern, so dass eine Weiterverarbeitung ohne Rissgefahr möglich ist. Dies ist entscheidend für die Herstellung komplexer Formen oder dünner Abschnitte, die mehrere Umformstufen erfordern.
-
Verbesserung der mechanischen und elektrischen Eigenschaften:
- Das Glühen kann die mechanischen Eigenschaften eines Werkstoffs, z. B. seine Zugfestigkeit, Zähigkeit und Ermüdungsbeständigkeit, durch Verfeinerung der Kornstruktur verbessern. Bei elektrischen Werkstoffen wie Kupfer oder Aluminium kann das Glühen außerdem die elektrische Leitfähigkeit verbessern, indem es Defekte im Kristallgitter verringert. Dadurch eignet sich das Material besser für Anwendungen, bei denen sowohl die mechanische Festigkeit als auch die elektrische Leistung entscheidend sind.
-
Herstellung einer gleichmäßigen und homogenen Struktur:
- Während der Herstellung können Werkstoffe aufgrund ungleichmäßiger Abkühlung oder mechanischer Verformung ungleichmäßige Mikrostrukturen entwickeln. Das Glühen trägt zur Herstellung einer einheitlicheren und homogeneren inneren Struktur bei, indem es dem Material ermöglicht, zu rekristallisieren und gleichachsige Körner zu bilden. Diese Gleichmäßigkeit verbessert die Gesamtleistung und Zuverlässigkeit des Materials, insbesondere bei Anwendungen, bei denen Beständigkeit entscheidend ist.
-
Wiederherstellung eines "weichen" Zustands des Materials:
- Nach Verfahren wie Kaltverformung oder Wärmebehandlung können Werkstoffe zu hart oder spröde für die weitere Verarbeitung werden. Durch das Glühen wird das Material wieder in einen weicheren Zustand versetzt, so dass weitere Bearbeitungs-, Umformungs- oder Wärmebehandlungsvorgänge leichter durchgeführt werden können. Dies ist besonders wichtig für Werkstoffe, die mehrere Bearbeitungsstufen durchlaufen müssen, um die gewünschten endgültigen Eigenschaften zu erhalten.
-
Dimensionsstabilität:
- Das Glühen kann dazu beitragen, die Dimensionsstabilität eines Materials zu verbessern, indem Eigenspannungen abgebaut werden, die im Laufe der Zeit zu Verformungen oder Verwerfungen führen können. Dies ist besonders wichtig für Präzisionskomponenten, die während ihrer Lebensdauer enge Toleranzen einhalten müssen.
Zusammenfassend lässt sich sagen, dass das Glühen dort erforderlich ist, wo Werkstoffe erweicht, dehnbarer gemacht oder von inneren Spannungen befreit werden sollen. Es ist ein vielseitiges Verfahren, das die Bearbeitbarkeit verbessert, die Kaltumformung erleichtert, die mechanischen und elektrischen Eigenschaften verbessert und die Dimensionsstabilität sicherstellt, was es für verschiedene Anwendungen in der Fertigung und im Maschinenbau unverzichtbar macht.
Zusammenfassende Tabelle:
Die wichtigsten Vorteile des Glühens | Beschreibung |
---|---|
Verringerung der Härte | Erweicht Materialien, macht sie dehnbarer und erleichtert ihre Bearbeitung oder Formgebung. |
Entlastung von inneren Spannungen | Reduziert innere Spannungen, die durch Fertigungsprozesse wie Gießen oder Schweißen entstehen. |
Verbesserte Bearbeitbarkeit | Erleichtert das Schneiden, Bohren oder Formen und reduziert den Werkzeugverschleiß. |
Erleichterung der Kaltbearbeitung | Stellt die Duktilität zwischen den Kaltverformungsphasen wieder her und verhindert Rissbildung. |
Verbesserte mechanische Eigenschaften | Verbessert die Zugfestigkeit, Zähigkeit und Ermüdungsbeständigkeit. |
Gleichmäßiges Gefüge | Erzeugt eine homogene interne Struktur für bessere Konsistenz. |
Wiederherstellung des weichen Zustands | Bereitet die Materialien nach dem Härten für die Weiterverarbeitung vor. |
Dimensionsstabilität | Verringert das Verziehen oder den Verzug und gewährleistet enge Toleranzen. |
Benötigen Sie Glühlösungen für Ihre Materialien? Kontaktieren Sie unsere Experten noch heute um mehr zu erfahren!