Das Schmieden ist ein wichtiges Fertigungsverfahren in der Automobilindustrie, mit dem starke, haltbare und leistungsstarke Komponenten hergestellt werden.Dabei wird Metall durch örtlich begrenzte Druckkräfte geformt, normalerweise mit Hämmern, Pressen oder Gesenken.Die Automobilindustrie setzt verschiedene Schmiedeverfahren ein, um Teile wie Kurbelwellen, Pleuelstangen, Zahnräder und Aufhängungskomponenten herzustellen.Jedes Schmiedeverfahren bietet einzigartige Vorteile in Bezug auf Präzision, Materialeigenschaften und Produktionseffizienz.Ein Verständnis der verschiedenen Arten von Schmiedeverfahren hilft den Herstellern bei der Auswahl des am besten geeigneten Verfahrens für bestimmte Automobilanwendungen.
Die wichtigsten Punkte erklärt:
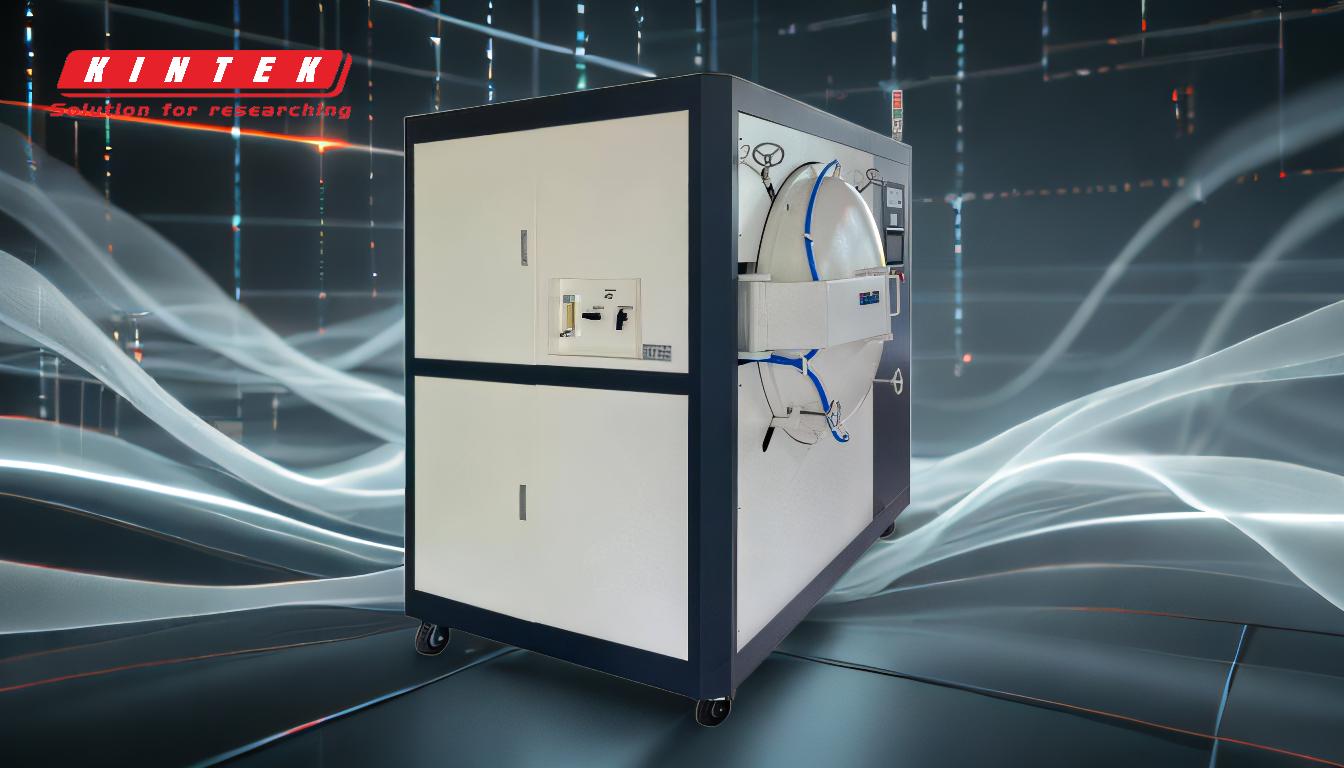
-
Freiformschmieden
- Beschreibung:Beim Freiformschmieden, das auch als Freiformschmieden bezeichnet wird, wird Metall zwischen flachen oder einfach geformten Gesenken verformt.Das Werkstück ist nicht vollständig umschlossen, so dass es in Form und Größe flexibel ist.
- Anwendungen:Wird für große, einfach geformte Bauteile wie Wellen, Ringe und Zylinder in der Automobilindustrie verwendet.
-
Vorteile:
- Geeignet für große Teile.
- Ermöglicht eine individuelle Gestaltung und Flexibilität.
- Verbessert die Materialfestigkeit und die Kornstruktur.
- Beschränkungen:Weniger präzise im Vergleich zum Gesenkschmieden, erfordert zusätzliche Bearbeitung für die endgültigen Abmessungen.
-
Gesenkschmieden (Gesenkschmieden)
- Beschreibung:Beim Gesenkschmieden wird das Metall zwischen zwei oder mehr Gesenken verdichtet, die ein vorgeschnittenes Profil des gewünschten Teils enthalten.Das Material fließt in die Hohlräume der Gesenke, um die endgültige Form zu erhalten.
- Anwendungen:Wird häufig für die Herstellung komplexer Automobilteile wie Zahnräder, Kurbelwellen und Pleuelstangen verwendet.
-
Vorteile:
- Hohe Präzision und Maßhaltigkeit.
- Minimaler Materialabfall.
- Hervorragende mechanische Eigenschaften aufgrund des kontrollierten Kornflusses.
- Beschränkungen:Höhere Werkzeugkosten und Beschränkung auf kleinere bis mittelgroße Teile.
-
Walzschmieden
- Beschreibung:Beim Walzschmieden wird das Metall zwischen zwei rotierenden Walzen mit geformten Rillen hindurchgeführt.Die Walzen komprimieren und formen das Metall, während es durchläuft.
- Anwendungen:Zur Herstellung von langen, konischen Bauteilen wie Achsen, Hebeln und Blattfedern in Fahrzeugen.
-
Vorteile:
- Effizient für lange Teile mit gleichmäßigem Querschnitt.
- Reduziert den Materialabfall und verbessert die Oberflächengüte.
- Beschränkungen:Begrenzt auf Teile mit einfachen Geometrien und erfordert eine spezielle Ausrüstung.
-
Stauchschmieden
- Beschreibung:Beim Stauchschmieden wird der Durchmesser eines Metallwerkstücks durch Komprimierung seiner Länge vergrößert.Dieses Verfahren wird in der Regel mit horizontalen oder vertikalen Pressen durchgeführt.
- Anwendungen:Ideal für die Herstellung von Schraubenköpfen, Ventilen und anderen Komponenten mit vergrößerten Enden.
-
Vorteile:
- Erhöht die Festigkeit und Dichte des Materials.
- Geeignet für die Großserienproduktion.
- Beschränkungen:Begrenzt auf Teile mit örtlich begrenzten Vergrößerungen und erfordert eine genaue Kontrolle des Materialflusses.
-
Isothermisches Schmieden
- Beschreibung:Isothermes Schmieden wird bei konstanter Temperatur durchgeführt, wobei in der Regel beheizte Gesenke verwendet werden, um die Temperatur des Werkstücks während des gesamten Prozesses aufrechtzuerhalten.
- Anwendungen:Für Hochleistungskomponenten wie Turbinenschaufeln und Teile für die Luft- und Raumfahrt, aber auch für spezielle Anwendungen in der Automobilindustrie.
-
Vorteile:
- Erzeugt Teile mit hervorragenden mechanischen Eigenschaften.
- Reduziert Eigenspannungen und verbessert die Maßhaltigkeit.
- Beschränkungen:Hohe Ausrüstungs- und Energiekosten, daher weniger verbreitet für Standardteile in der Automobilindustrie.
-
Präzisionsschmieden
- Beschreibung:Das Präzisionsschmieden ist ein endkonturnahes Verfahren, das Teile mit minimalen Bearbeitungsanforderungen herstellt.Dabei werden hochpräzise Werkzeuge verwendet, um enge Toleranzen zu erreichen.
- Anwendungen:Geeignet für kritische Automobilkomponenten wie Zahnräder, Getriebeteile und Lenkungsteile.
-
Vorteile:
- Reduziert den Materialabfall und die Bearbeitungszeit.
- Verbessert die Festigkeit und Ermüdungsbeständigkeit der Teile.
- Beschränkungen:Hohe anfängliche Werkzeugkosten und fortschrittliche Ausrüstung erforderlich.
-
Kaltschmieden
- Beschreibung:Das Kaltschmieden erfolgt bei oder nahe der Raumtemperatur, wobei das Metall mit Hilfe von Hochdruckwerkzeugen geformt wird.
- Anwendungen:Wird häufig für die Herstellung von Verbindungselementen, Bolzen und kleinen Automobilteilen verwendet.
-
Vorteile:
- Verbessert die Materialfestigkeit und Oberflächengüte.
- Kostengünstig für die Großserienproduktion.
- Beschränkungen:Begrenzt auf kleinere Teile und erfordert Hochdruckanlagen.
-
Warmumformung
- Beschreibung:Beim Warmschmieden wird das Metall über seine Rekristallisationstemperatur erhitzt, um es formbarer zu machen.Das erhitzte Metall wird dann mit Hilfe von Gesenken oder Pressen geformt.
- Anwendungen:Weit verbreitet für die Herstellung großer Automobilteile wie Kurbelwellen, Pleuelstangen und Aufhängungskomponenten.
-
Vorteile:
- Ermöglicht komplexe Formen und große Teile.
- Verbessert die Duktilität des Materials und verringert den Verformungswiderstand.
- Beschränkungen:Höherer Energieverbrauch und die Gefahr von Oxidation oder Verzunderung.
Jedes Schmiedeverfahren bietet unterschiedliche Vorteile und wird auf der Grundlage der spezifischen Anforderungen des herzustellenden Automobilteils ausgewählt.Faktoren wie die Komplexität des Teils, die Materialeigenschaften, das Produktionsvolumen und Kostenüberlegungen spielen eine entscheidende Rolle bei der Auswahl des geeigneten Schmiedeverfahrens.Durch den Einsatz dieser Verfahren kann die Automobilindustrie hochwertige, langlebige und zuverlässige Komponenten herstellen, die den Anforderungen moderner Fahrzeuge gerecht werden.
Zusammenfassende Tabelle:
Schmiedeprozess | Beschreibung | Anwendungen | Vorteile | Beschränkungen |
---|---|---|---|---|
Freiformschmieden | Verformt Metall zwischen flachen oder einfach geformten Gesenken. | Große, einfach geformte Komponenten wie Wellen, Ringe und Zylinder. | Geeignet für große Teile, anpassbar, erhöht die Materialfestigkeit. | Weniger präzise, erfordert zusätzliche Bearbeitung. |
Gesenkschmieden | Pressen von Metall zwischen Gesenken mit vorgeschnittenen Profilen. | Komplexe Teile wie Zahnräder, Kurbelwellen und Pleuelstangen. | Hohe Präzision, minimaler Ausschuss, hervorragende mechanische Eigenschaften. | Höhere Werkzeugkosten, beschränkt auf kleinere bis mittelgroße Teile. |
Walzschmieden | Verformt Metall zwischen rotierenden Walzen mit Rillen. | Lange, verjüngte Komponenten wie Achsen, Hebel und Blattfedern. | Effizient für lange Teile, reduziert den Abfall, verbessert die Oberflächengüte. | Begrenzt auf einfache Geometrien, erfordert spezielle Ausrüstung. |
Stauchschmieden | Vergrößert den Durchmesser durch Komprimierung der Länge. | Zum Verschrauben von Köpfen, Ventilen und Komponenten mit vergrößerten Enden. | Erhöht die Festigkeit und Dichte, geeignet für die Großserienproduktion. | Begrenzt auf örtlich begrenzte Vergrößerungen, erfordert präzise Kontrolle. |
Isothermisches Schmieden | Wird bei konstanter Temperatur mit beheizten Gesenken durchgeführt. | Hochleistungskomponenten wie Turbinenschaufeln und Teile für die Luft- und Raumfahrt. | Hervorragende mechanische Eigenschaften, reduziert Eigenspannungen. | Hohe Ausrüstungs- und Energiekosten, weniger üblich für Standardteile in der Automobilindustrie. |
Präzisionsschmieden | Nahezu endkonturnahes Verfahren mit minimaler Bearbeitung. | Kritische Komponenten wie Zahnräder, Getriebeteile und Lenkungsteile. | Reduziert Abfall und Bearbeitungszeit, erhöht die Festigkeit und Ermüdungsbeständigkeit. | Hohe Werkzeugkosten, erfordert moderne Ausrüstung. |
Kaltumformung | Verformt Metall bei oder nahe Raumtemperatur mit Hilfe von Hochdruckwerkzeugen. | Befestigungselemente, Bolzen und kleine Automobilkomponenten. | Verbessert Festigkeit und Oberflächengüte, kosteneffektiv bei hohen Stückzahlen. | Begrenzt auf kleinere Teile, erfordert Hochdruckausrüstung. |
Warmumformung | Erhitzt Metall über die Rekristallisationstemperatur für die Formgebung. | Große Teile wie Kurbelwellen, Pleuelstangen und Aufhängungskomponenten. | Ermöglicht komplexe Formen, verbessert die Duktilität, verringert den Verformungswiderstand. | Höherer Energieverbrauch, Gefahr von Oxidation oder Verzunderung. |
Benötigen Sie Hilfe bei der Auswahl des richtigen Schmiedeverfahrens für Ihre Automobilkomponenten? Kontaktieren Sie noch heute unsere Experten für maßgeschneiderte Lösungen!