Sputtern ist eine weit verbreitete Technik zur Abscheidung von Dünnschichten, die für ihre hohe Reinheit, präzise Kontrolle und Gleichmäßigkeit bekannt ist.Es ist jedoch mit mehreren Nachteilen verbunden, die sich auf die Effizienz, die Kosten und die Eignung für die Anwendung auswirken können.Zu den wichtigsten Nachteilen gehören langsamere Abscheidungsraten, hohe Geräte- und Betriebskosten, Hitzeempfindlichkeit, das Risiko der Filmverunreinigung und die Schwierigkeit, eine gleichmäßige Schichtdicke zu erreichen.Darüber hinaus stößt das Sputtern bei der Materialauswahl, der Prozesssteuerung und der Integration mit anderen Fertigungstechniken an Grenzen.Diese Faktoren machen es weniger ideal für bestimmte Anwendungen, insbesondere für solche, die einen hohen Durchsatz, geringe Kontamination oder komplexe Materialkombinationen erfordern.
Die wichtigsten Punkte werden erklärt:
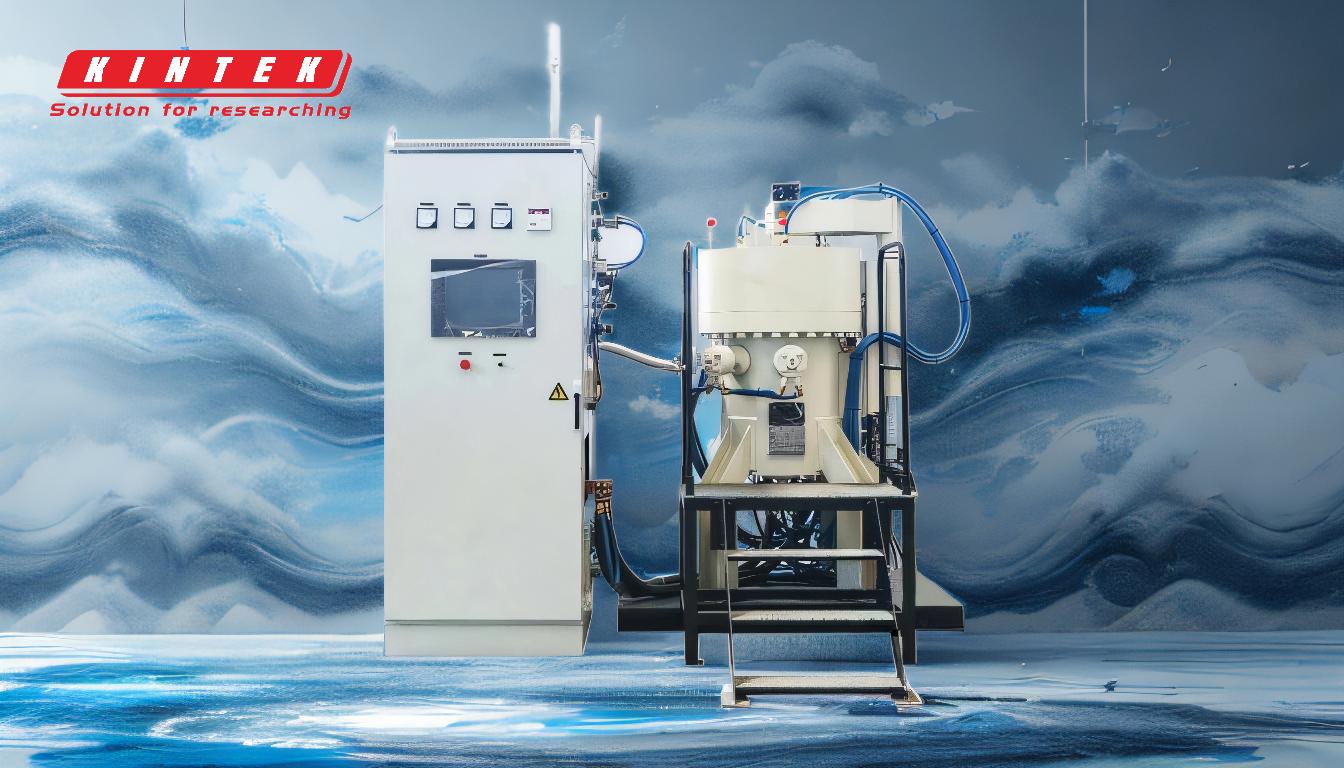
-
Langsamere Abscheidungsraten
- Im Vergleich zu Verfahren wie der thermischen Verdampfung weist das Sputtern in der Regel niedrigere Abscheideraten auf.Dies liegt an der physikalischen Natur des Prozesses, bei dem Atome aus einem Zielmaterial herausgeschleudert und auf einem Substrat abgeschieden werden.Die langsamere Geschwindigkeit kann den Durchsatz begrenzen, so dass sich das Verfahren weniger für die Produktion großer Mengen eignet.
-
Hohe Ausrüstungs- und Betriebskosten
- Sputtering-Systeme sind teuer in der Anschaffung und im Unterhalt.Der Bedarf an hochwertigen Vakuumsystemen, HF- oder DC-Stromquellen und Kühlsystemen erhöht die Gesamtkosten.Darüber hinaus sind Sputtertargets oft kostspielig, und der Materialverbrauch kann ineffizient sein, was die Kosten weiter erhöht.
-
Wärmeempfindlichkeit und Kühlungsanforderungen
- Ein erheblicher Teil der beim Sputtern eingesetzten Energie wird in Wärme umgewandelt, die wirksam abgeführt werden muss, um Schäden am Substrat oder Target zu vermeiden.Es sind Kühlsysteme erforderlich, die jedoch die Produktionsraten verringern und den Energieverbrauch erhöhen können, was wiederum die Betriebskosten in die Höhe treibt.
-
Risiken der Filmkontamination
- Beim Sputtern können Verunreinigungen in die abgeschiedene Schicht gelangen.Verunreinigungen aus dem Targetmaterial oder gasförmige Verunreinigungen im Plasma können aktiviert und in die Schicht eingebaut werden.Dies ist besonders problematisch beim reaktiven Sputtern, wo eine sorgfältige Kontrolle der Gaszusammensetzung erforderlich ist, um eine Vergiftung des Targets zu vermeiden.
-
Herausforderungen bei der Erzielung einer gleichmäßigen Schichtdicke
- Die Verteilung des Beschichtungsflusses beim Sputtern ist oft ungleichmäßig, insbesondere bei großen Substraten oder Targets.Um eine gleichmäßige Schichtdicke zu erreichen, sind unter Umständen bewegliche Vorrichtungen oder komplexe Aufbauten erforderlich, was den Prozess komplexer und teurer macht.
-
Beschränkungen bei der Materialauswahl
- Das Sputtern wird durch die Schmelztemperaturen und Eigenschaften der Zielmaterialien eingeschränkt.Einige Werkstoffe eignen sich aufgrund ihres niedrigen Schmelzpunkts oder anderer physikalischer Eigenschaften nicht für das Sputtern, wodurch die Palette der herstellbaren Beschichtungen eingeschränkt wird.
-
Schwierige Kombination mit Lift-Off-Verfahren
- Das Sputtern lässt sich nur schwer mit Lift-Off-Verfahren kombinieren, die bei der Filmstrukturierung eingesetzt werden.Der diffuse Transport der gesputterten Atome macht eine vollständige Abschattung unmöglich, was zu Verunreinigungen und Schwierigkeiten bei der Herstellung präziser Muster führt.
-
Aktive Kontrolle - eine Herausforderung
- Im Vergleich zu anderen Abscheidungsmethoden wie der gepulsten Laserabscheidung bietet das Sputtern weniger aktive Kontrolle über das schichtweise Wachstum.Dies kann seinen Einsatz bei Anwendungen einschränken, die eine präzise Kontrolle auf atomarer Ebene erfordern.
-
Hohe Betriebsdrücke und Dichtungsprobleme
- Herkömmliche Sputtering-Prozesse arbeiten mit relativ hohen Drücken, was zu Permeation durch Elastomerdichtungen und anderen Problemen im Vakuumsystem führen kann.Diese Probleme können die Qualität und Effizienz des Abscheidungsprozesses beeinträchtigen.
-
Ungleichmäßige Plasmadichte
- Bei großen rechteckigen Kathoden (z.B. >1m) kann es schwierig sein, eine gleichmäßige Plasmadichte zu erreichen, was zu einer ungleichmäßigen Schichtdickenverteilung führt.Dies erfordert zusätzliche technische Lösungen.
-
Ineffiziente Energie
- Der größte Teil der auf das Target auftreffenden Energie wird in Wärme umgewandelt, anstatt für die Abscheidung genutzt zu werden, wodurch das Verfahren im Vergleich zu anderen Techniken weniger energieeffizient ist.
-
Komplikationen beim reaktiven Sputtern
- Beim reaktiven Sputtern ist eine präzise Steuerung der Gaszusammensetzung von entscheidender Bedeutung, um eine Vergiftung des Targets zu vermeiden, bei der die Oberfläche des Targets chemisch verändert wird, was die Abscheidungseffizienz und die Schichtqualität verringert.
Wenn die Käufer von Anlagen und Verbrauchsmaterialien diese Nachteile kennen, können sie fundierte Entscheidungen darüber treffen, ob das Sputtern die richtige Technik für ihre spezifischen Anwendungen ist, und dabei Faktoren wie Kosten, Durchsatz und Materialanforderungen berücksichtigen.
Zusammenfassende Tabelle:
Benachteiligung | Wichtige Details |
---|---|
Langsamere Abscheidungsraten | Geringerer Durchsatz im Vergleich zu Verfahren wie der thermischen Verdampfung. |
Hohe Ausrüstungs- und Betriebskosten | Teure Systeme, Vakuumanforderungen und teure Sputtertargets. |
Wärmeempfindlichkeit | Erfordert Kühlsysteme, was die Produktionsrate verringert und den Energieverbrauch erhöht. |
Risiken der Filmkontamination | Verunreinigungen von Targets oder Plasma können die Filmqualität beeinträchtigen. |
Gleichmäßige Schichtdicke - eine Herausforderung | Ungleichmäßiger Abscheidungsfluss, insbesondere bei großen Substraten. |
Beschränkungen bei der Materialauswahl | Eingeschränkt durch die Eigenschaften des Zielmaterials und die Schmelzpunkte. |
Integration mit Lift-Off-Verfahren | Schwierig zu kombinieren mit präzisen Filmstrukturierungstechniken. |
Aktive Kontrolle - Herausforderungen | Weniger präzises schichtweises Wachstum im Vergleich zu anderen Methoden. |
Hohe Betriebsdrücke | Kann zu Problemen mit dem Vakuumsystem und mit der Abdichtung führen. |
Ungleichmäßige Plasmadichte | Bei großen Kathoden ist es schwierig, eine gleichmäßige Plasmadichte zu erreichen. |
Ineffiziente Energie | Die meiste Energie wird in Wärme umgewandelt, nicht in Abscheidung. |
Komplikationen beim reaktiven Sputtern | Erfordert eine präzise Gassteuerung, um eine Vergiftung des Targets zu vermeiden. |
Benötigen Sie Hilfe bei der Entscheidung, ob Sputtern das Richtige für Ihre Anwendung ist? Kontaktieren Sie noch heute unsere Experten für eine maßgeschneiderte Beratung!