Das Vakuumgießen ist zwar ein vielseitiges und weit verbreitetes Herstellungsverfahren, hat jedoch einige Einschränkungen, die sich auf seine Effizienz, die Kosten und die Qualität des Endprodukts auswirken können. Diese Einschränkungen ergeben sich aus den Materialeigenschaften, den Prozessbeschränkungen und den betrieblichen Herausforderungen. Zu den Hauptproblemen gehören Schwund und Porosität in Gussbauteilen, die hohen Kosten und der Verschleiß von Formmaterialien, zeitintensive Abkühlungsprozesse, Schwierigkeiten bei der Einhaltung enger Maßtoleranzen und Ineffizienzen im Ofenbetrieb. All diese Faktoren können die mechanischen Eigenschaften, die Zuverlässigkeit und die wirtschaftliche Rentabilität von Vakuumgussteilen beeinträchtigen.
Die wichtigsten Punkte werden erklärt:
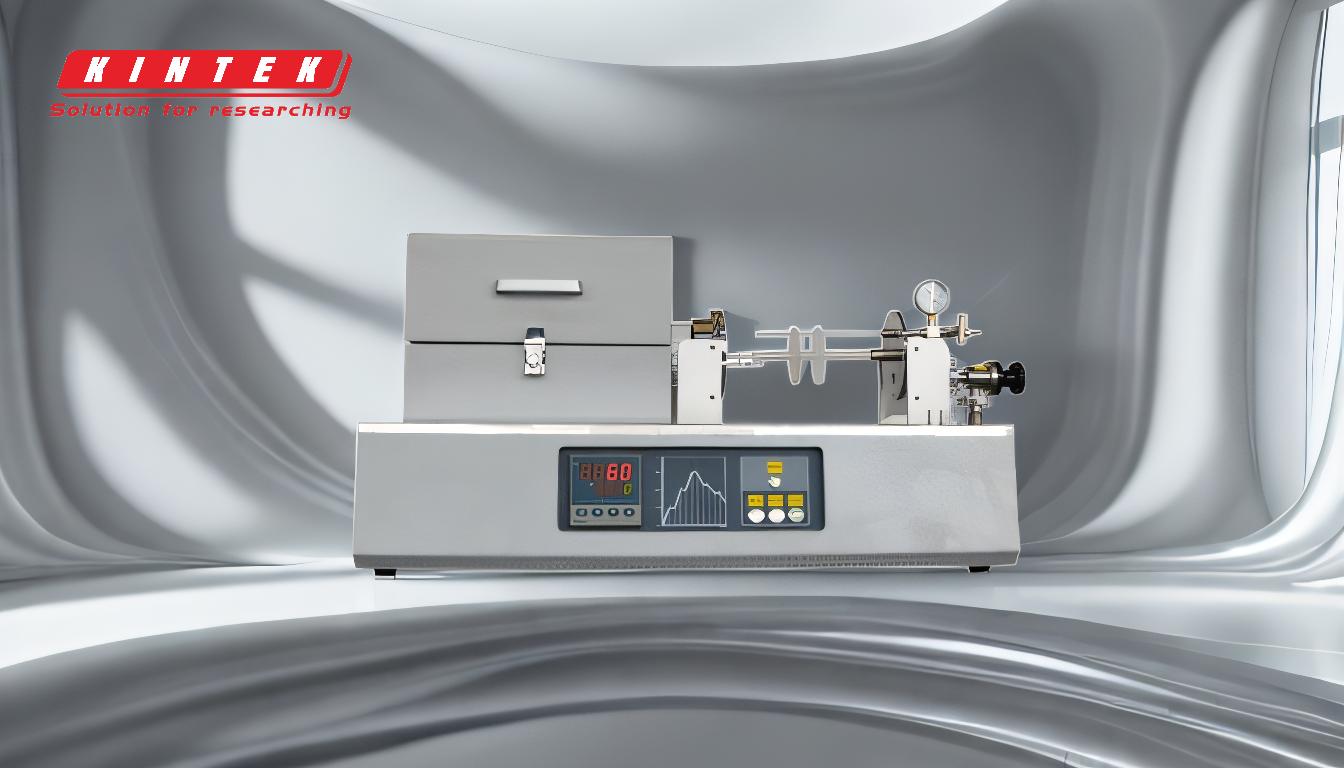
-
Schrumpfung und Porosität in Gussbauteilen:
- Erläuterung: Bei der Erstarrung von Metall im Vakuumguss ist die Schrumpfung eine inhärente Eigenschaft, die zu Defekten wie Restschrumpfung oder Gasporosität führen kann. Diese Defekte können die mechanischen Eigenschaften der Gussteile beeinträchtigen, insbesondere ihre Schlagfestigkeit und Ermüdungseigenschaften.
- Auswirkungen: Diese Einschränkung ist kritisch bei Anwendungen, die eine hohe Zuverlässigkeit und Leistung erfordern, wie z. B. bei Bauteilen für die Luft- und Raumfahrt. Das Vorhandensein von Porosität kann auch zusätzliche Qualitätskontrollmaßnahmen und Nachbearbeitungen erforderlich machen, um die Integrität der Gussteile zu gewährleisten.
-
Herausforderungen bei Formwerkstoffen:
- Erläuterung: Das Vakuum-Heißpressverfahren, eine gängige Technik beim Vakuumgießen, ist häufig mit hohen Temperaturen und reaktiven Umgebungen verbunden, die Formwerkstoffe zersetzen können. Dies führt zu erheblichen Formverlusten und erfordert den Einsatz hochwertiger, oft teurer Formwerkstoffe, die diesen rauen Bedingungen standhalten können.
- Auswirkungen: Der Bedarf an haltbaren Formenmaterialien erhöht die Gesamtkosten des Gießverfahrens. Außerdem kann die Abnutzung der Formen dazu führen, dass sie häufiger ausgetauscht werden müssen, was die Kosten weiter in die Höhe treibt und möglicherweise zu Verzögerungen in der Produktion führt.
-
Zeitintensiver Abkühlungsprozess:
- Erläuterung: Der Abkühlungsprozess beim Vakuumgießen ist von Natur aus langsam, um sicherzustellen, dass das Metall gleichmäßig erstarrt und Fehler minimiert werden. Diese langsame Abkühlung kann einen Engpass im Herstellungsprozess darstellen, insbesondere wenn schnelle Produktionszyklen erforderlich sind.
- Auswirkungen: Die verlängerten Abkühlzeiten können zu längeren Vorlaufzeiten und einem geringeren Durchsatz führen, was sich auf die Gesamteffizienz und Kostenwirksamkeit des Fertigungsprozesses auswirkt.
-
Schwierigkeit, enge Maßtoleranzen einzuhalten:
- Erläuterung: Das Erreichen präziser Maßtoleranzen beim Vakuumgießen kann aufgrund der Art des Gießprozesses und des Verhaltens der Werkstoffe während der Erstarrung eine Herausforderung darstellen. Schwankungen in den Abkühlungsraten und Materialeigenschaften können zu Abweichungen von den gewünschten Abmessungen führen.
- Auswirkungen: Diese Einschränkung kann zusätzliche Bearbeitungs- oder Endbearbeitungsprozesse erfordern, um die erforderlichen Spezifikationen zu erreichen, was die Kosten und die Komplexität der Produktion erhöht. Dies ist besonders problematisch in Branchen, in denen Präzision von größter Bedeutung ist, wie z. B. bei medizinischen Geräten oder in der Feinmechanik.
-
Ineffizienzen beim Betrieb von Öfen:
- Erläuterung: Moderne Vakuumgießöfen müssen oft gekippt und die Formen häufig gewechselt werden, was zu Materialverlusten und längeren Fertigungszeiten führen kann. Diese betrieblichen Ineffizienzen können in der Großserienproduktion einen erheblichen Nachteil darstellen.
- Auswirkungen: Die Notwendigkeit des ständigen Kippens und Wechselns von Formen verlangsamt nicht nur den Produktionsprozess, sondern erhöht auch das Risiko von Fehlern und Unstimmigkeiten. Dies kann zu höheren Ausschussraten und einer geringeren Gesamtproduktivität führen.
Zusammenfassend lässt sich sagen, dass das Vakuumgießen zwar zahlreiche Vorteile bietet, darunter die Möglichkeit, komplexe Formen und hochwertige Oberflächen herzustellen, aber auch seine Grenzen hat. Diese Einschränkungen - von Materialschwund und Formverschleiß bis hin zu betrieblichen Ineffizienzen - müssen sorgfältig gehandhabt werden, um die wirtschaftliche und funktionale Tragfähigkeit des Gießverfahrens zu gewährleisten. Die Hersteller müssen diese Faktoren gegen die spezifischen Anforderungen ihrer Anwendungen abwägen, um die Eignung des Vakuumgießens für ihre Bedürfnisse zu bestimmen.
Zusammenfassende Tabelle:
Begrenzung | Erläuterung | Auswirkungen |
---|---|---|
Schrumpfung und Porosität | Die inhärente Schrumpfung während der Erstarrung verursacht Defekte wie Porosität. | Beeinträchtigt die mechanischen Eigenschaften, erfordert zusätzliche Qualitätskontrollen und Nachbearbeitungen. |
Hohe Kosten und Abnutzung von Formmaterialien | Hohe Temperaturen zersetzen die Formen und erfordern teure, haltbare Materialien. | Erhöht die Kosten und verzögert die Produktion aufgrund des häufigen Austauschs von Formen. |
Zeitintensiver Abkühlungsprozess | Die langsame Abkühlung gewährleistet eine gleichmäßige Erstarrung, verzögert aber die Produktion. | Reduziert den Durchsatz und die Effizienz, was zu längeren Vorlaufzeiten führt. |
Schwierigkeit bei Maßtoleranzen | Schwankungen bei den Abkühlungsraten und den Materialeigenschaften beeinflussen die Präzision. | Erfordert zusätzliche Bearbeitung, was die Kosten und die Komplexität erhöht. |
Ineffizienzen beim Betrieb von Öfen | Häufiges Kippen und Wechseln der Formen führen zu Materialverlusten und Produktionsverzögerungen. | Verlangsamt die Produktion, erhöht die Ausschussrate und verringert die Gesamtproduktivität. |
Benötigen Sie Hilfe bei der Optimierung Ihres Vakuumgießprozesses? Kontaktieren Sie unsere Experten noch heute um auf Ihre Bedürfnisse zugeschnittene Lösungen zu finden!