Ein Drehrohrofen ist ein zylindrischer, leicht geneigter Ofen, der sich langsam dreht, um Materialien bei extrem hohen Temperaturen zu verarbeiten.Er dient zur Durchführung verschiedener thermischer Prozesse wie Kalzinierung, Verbrennung, thermische Desorption und organische Verbrennung.Der Ofen funktioniert, indem die Materialien in das obere Ende eingeführt werden, wo sie durch die Schwerkraft und die Rotation nach unten wandern und sich vermischen.Heiße Gase, die entweder intern oder extern erzeugt werden, strömen durch den Ofen und erhitzen die Materialien gleichmäßig.Die Kombination aus Rotation, Neigung und hohen Temperaturen sorgt für eine gründliche Verarbeitung und ermöglicht chemische Reaktionen oder physikalische Veränderungen in den Materialien, bevor sie am unteren Ende des Ofens austreten.
Die wichtigsten Punkte erklärt:
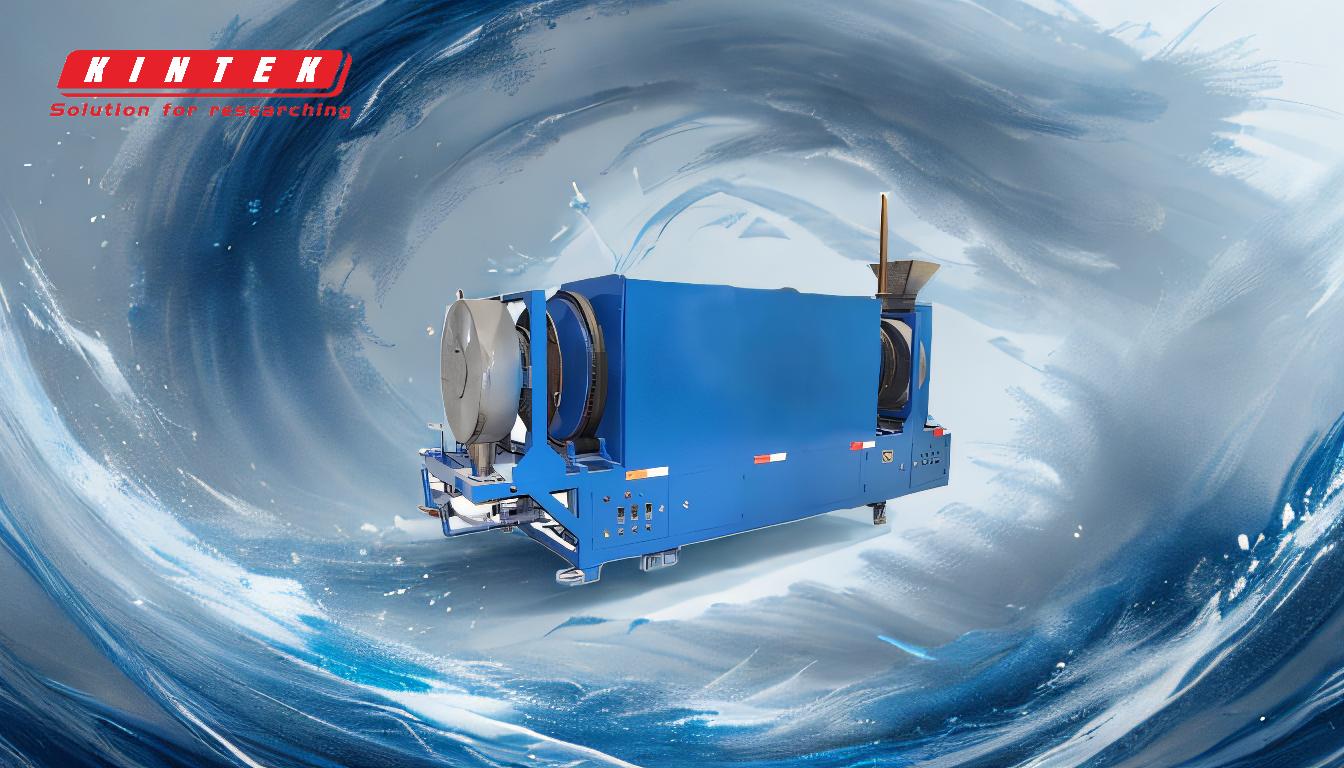
-
Aufbau und Konstruktion eines Drehrohrofens
- Ein Drehrohrofen ist ein großer, hohler, zylindrischer Behälter, der gegenüber der Horizontalen leicht geneigt ist.
- Durch die Neigung und die Drehung kann das Material vom oberen Ende (Zufuhr) zum unteren Ende (Abfuhr) bewegt werden.
- Die interne Konfiguration des Ofens kann angepasst werden, um die Materialtrommelung und die Wärmeeinwirkung zu optimieren.
-
Materialbewegung und Mischen
- Das Material wird durch das obere Ende des Ofens mit Hilfe einer Beschickungsvorrichtung, z. B. einer Förderschnecke, in den Ofen eingeführt.
- Während sich der Ofen dreht, werden die Materialien durcheinander gewirbelt und vermischt, so dass sie gleichmäßig der Hitze ausgesetzt sind.
- Die Drehung und die Neigung erleichtern die allmähliche Bewegung der Materialien in Richtung der Austrittsöffnung.
-
Wärmeerzeugung und -übertragung
- Im Inneren des Ofens werden hohe Temperaturen zwischen 800°F und 2.200°F erzeugt.
- Die Wärme wird durch heiße Gase bereitgestellt, die in die gleiche Richtung wie das Material (Gleichstrom) oder in die entgegengesetzte Richtung (Gegenstrom) strömen können.
- Die heißen Gase können durch einen externen Ofen oder durch eine Flamme im Inneren des Ofens erzeugt werden, die mit Gas, Öl, pulverisiertem Petrolkoks oder Kohle betrieben wird.
-
Thermische Prozesse in einem Drehrohrofen
- Kalzinierung:Erhitzen von Materialien auf hohe Temperaturen, um flüchtige Bestandteile zu zersetzen oder zu entfernen.
- Verbrennung:Verbrennung von Abfallstoffen zur Volumenreduzierung und Beseitigung von Schadstoffen.
- Thermische Desorption:Entfernung von Verunreinigungen aus Materialien durch Hitze.
- Organische Verbrennung:Verbrennung von organischen Materialien zur Energiegewinnung oder Abfallvermeidung.
- Sintern/Induration:Erhitzen von Materialien, um eine feste Masse zu bilden, ohne zu schmelzen.
- Wärmebehandlung:Anwendung von Wärme zum Aushärten von Materialien.
-
Betriebliche Anpassungen
- Die Drehgeschwindigkeit und die Neigung des Ofens können eingestellt werden, um die Verweilzeit des Materials im Ofen zu steuern.
- Die Strömung der heißen Gase kann optimiert werden, um eine gleichmäßige Erwärmung und effiziente Verarbeitung zu gewährleisten.
- Interne Konfigurationen wie Umlenkbleche oder Heber können eingesetzt werden, um die Materialdurchmischung und die Wärmeübertragung zu verbessern.
-
Anwendungen von Drehrohröfen
- Drehrohröfen sind in Branchen wie der Zementherstellung, der Metallurgie, der Abfallwirtschaft und der chemischen Verarbeitung weit verbreitet.
- Sie sind unverzichtbar für Prozesse, die eine Hochtemperaturbehandlung erfordern, wie die Herstellung von Kalk, Tonerde und Eisenerzpellets.
-
Vorteile von Drehrohröfen
- Die kontinuierliche Verarbeitung ermöglicht einen hohen Durchsatz und eine hohe Effizienz.
- Gleichmäßige Erwärmung gewährleistet gleichbleibende Produktqualität.
- Vielseitigkeit bei der Verarbeitung verschiedener Materialien und Prozesse.
Durch die Kombination dieser Elemente stellen Drehrohröfen eine robuste und effiziente Lösung für die thermische Verarbeitung bei hohen Temperaturen dar, was sie für viele industrielle Anwendungen unverzichtbar macht.
Zusammenfassende Tabelle:
Aspekt | Einzelheiten |
---|---|
Aufbau | Zylindrischer, leicht geneigter Behälter für Materialbewegung und Wärmeeinwirkung. |
Bewegung des Materials | Wird am oberen Ende zugeführt, taumelt und vermischt sich aufgrund von Rotation und Neigung. |
Wärmeerzeugung | Hohe Temperaturen (800°F-2.200°F) durch heiße Gase (Gleichstrom/Gegenstrom). |
Thermische Verfahren | Kalzinierung, Verbrennung, thermische Desorption, organische Verbrennung, Sinterung. |
Anwendungen | Zementherstellung, Metallurgie, Abfallwirtschaft, chemische Verarbeitung. |
Vorteile | Hoher Durchsatz, gleichmäßige Erwärmung, Vielseitigkeit bei Materialien und Prozessen. |
Benötigen Sie einen Drehrohrofen für Ihren industriellen Bedarf? Kontaktieren Sie noch heute unsere Experten um die perfekte Lösung zu finden!