Die physikalische Gasphasenabscheidung (PVD) ist ein Verfahren zur Beschichtung von Dünnschichten, bei dem Materialien in einer Vakuumumgebung auf ein Substrat aufgebracht werden.Dabei wird ein festes Material physikalisch verdampft und kondensiert dann auf einer Zieloberfläche zu einer dünnen, gleichmäßigen Schicht.PVD wird in vielen Branchen eingesetzt, um die mechanischen, optischen, chemischen oder elektronischen Eigenschaften von Materialien zu verbessern.Besonders geschätzt wird es für seine Fähigkeit, die Verschleißfestigkeit zu verbessern, die Reibung zu verringern und dekorative Oberflächen zu erzeugen.Das Verfahren ist vielseitig und ermöglicht die Herstellung fortschrittlicher Werkstoffe und Beschichtungen für Anwendungen, die von Halbleitern und Solarzellen bis hin zu dekorativen Bauteilen und Komponenten für die Luftfahrt reichen.
Die wichtigsten Punkte werden erklärt:
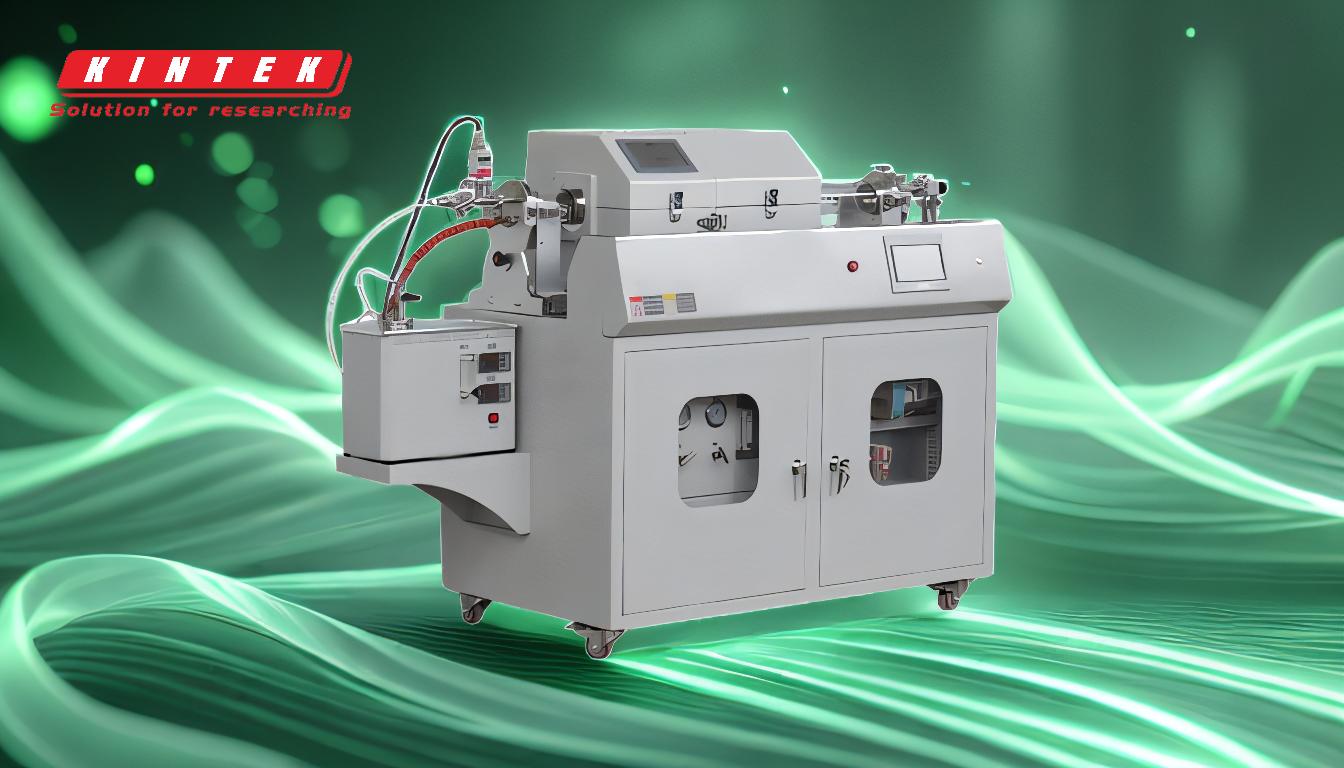
-
Definition und Verfahren von PVD:
- PVD ist ein vakuumbasiertes Beschichtungsverfahren, bei dem ein festes Material verdampft und dann auf ein Substrat aufgebracht wird, um einen dünnen Film zu bilden.
-
Der Prozess beinhaltet:
- Verdampfung:Das Ausgangsmaterial wird mit Methoden wie Verdampfung, Hochleistungselektrizität oder Laserablation vergast.
- Transport:Das verdampfte Material wandert durch ein Vakuum oder eine Niederdruckumgebung.
- Kondenswasser:Das Material kondensiert auf dem Substrat und bildet eine dünne, gleichmäßige Schicht.
- Beim PVD-Verfahren finden keine chemischen Reaktionen statt, es handelt sich also um einen rein physikalischen Prozess.
-
Anwendungen von PVD:
-
Industrielle Anwendungen:
- Zerspanung und Werkzeuge:PVD-Beschichtungen, wie z. B. Titannitrid, verbessern die Verschleißfestigkeit und verlängern die Lebensdauer von Schneidwerkzeugen.
- Mikroelektronik und Halbleiter:PVD wird zur Abscheidung dünner Schichten für Halbleiterbauelemente und integrierte Schaltkreise verwendet.
- Solarpaneele:Dünnschicht-Solarmodule nutzen PVD, um Effizienz und Haltbarkeit zu verbessern.
- Luft- und Raumfahrt:PVD-Beschichtungen verbessern die Beständigkeit gegen hohe Temperaturen und Ablation bei Komponenten für die Luft- und Raumfahrt.
-
Dekorative und funktionelle Beschichtungen:
- Architektonisches Glas:PVD-Beschichtungen bieten reflektierende und energieeffiziente Eigenschaften.
- Schmuck und Hardware:PVD wird für dekorative Oberflächen verwendet, die metallischen Glanz und Haltbarkeit bieten.
- Unterhaltungselektronik:PVD wird bei der Herstellung von Festplatten, CDs und DVDs verwendet.
-
Industrielle Anwendungen:
-
Vorteile von PVD:
-
Verbesserte Materialeigenschaften:
- Verbessert die Härte, Verschleißfestigkeit und Oxidationsbeständigkeit von Substraten.
- Verringert die Reibung und ist daher ideal für bewegliche Teile in Maschinen.
-
Vielseitigkeit:
- Kann eine breite Palette von Materialien abscheiden, darunter Metalle, Legierungen und Keramiken.
- Ermöglicht die Herstellung fortschrittlicher Materialien mit einzigartigen Eigenschaften, wie z. B. erweiterte Löslichkeiten und feine Korngrößen.
-
Ästhetische und funktionale Vorteile:
- Erzeugt ein hochwertiges metallisches Finish, ohne dass Polieren erforderlich ist.
- Geeignet sowohl für funktionelle als auch für dekorative Anwendungen.
-
Verbesserte Materialeigenschaften:
-
Materialien und Techniken in PVD:
-
Quellenmaterialien:
- Üblicherweise werden reine Metalle (z. B. Titan, Aluminium) und Legierungen (z. B. Ti-Mg) verwendet.
- Die Wahl des Materials hängt von den gewünschten Eigenschaften der Beschichtung ab.
-
Abscheidungstechniken:
- Verdampfung:Das Ausgangsmaterial wird erhitzt, bis es verdampft.
- Sputtern:Hochenergetische Ionen beschießen das Ausgangsmaterial, wodurch es Atome ausstößt.
- Laserablation:Ein Laser wird zur Verdampfung des Ausgangsmaterials verwendet.
-
Beschichtungsarten:
- Einschichtige Beschichtungen (z. B. Titannitrid für Verschleißfestigkeit).
- Mehrschichtige Beschichtungen zur Leistungssteigerung (z. B. abwechselnde Schichten aus verschiedenen Materialien).
-
Quellenmaterialien:
-
Branchen, die PVD nutzen:
-
Zerspanung und Fertigung:
- PVD-beschichtete Werkzeuge werden häufig beim Schneiden, Bohren und Umformen eingesetzt.
-
Elektronik:
- PVD ist von entscheidender Bedeutung für die Herstellung dünner Schichten in der Mikroelektronik und bei Halbleitergeräten.
-
Architektur und Design:
- PVD-beschichtetes Glas und Beschläge werden in modernen Gebäuden sowohl für funktionale als auch für ästhetische Zwecke verwendet.
-
Schmuck und dekorative Kunst:
- PVD bietet haltbare und attraktive Oberflächen für Schmuck, Lampen und Kunsthandwerk.
-
Zerspanung und Fertigung:
-
Zukünftige Trends bei PVD:
-
Fortschrittliche Legierungen und Verbundwerkstoffe:
- PVD ermöglicht die Herstellung von Versuchslegierungen mit einzigartigen Eigenschaften, wie z. B. Ti-Mg, die mit der herkömmlichen Metallurgie nicht hergestellt werden können.
-
Nachhaltigkeit:
- PVD ist ein umweltfreundliches Verfahren, da nur wenig Abfall anfällt und keine schädlichen Chemikalien verwendet werden.
-
Aufstrebende Anwendungen:
- PVD wird für den Einsatz in der Energiespeicherung (z. B. Batterien) und in biomedizinischen Geräten (z. B. Implantatbeschichtungen) erforscht.
-
Fortschrittliche Legierungen und Verbundwerkstoffe:
Zusammenfassend lässt sich sagen, dass PVD eine vielseitige und fortschrittliche Beschichtungstechnik ist, die in vielen Branchen Anwendung findet.Ihre Fähigkeit, die Materialeigenschaften zu verbessern, dekorative Oberflächen zu schaffen und die Entwicklung innovativer Materialien zu ermöglichen, macht sie zu einer wichtigen Technologie in der modernen Fertigung und im Design.
Zusammenfassende Tabelle:
Aspekt | Einzelheiten |
---|---|
Prozess | Verdampfung, Transport und Kondensation in einer Vakuumumgebung. |
Anwendungen | Bearbeitungswerkzeuge, Mikroelektronik, Solarzellen, Luft- und Raumfahrt und Schmuck. |
Vorteile | Verbessert die Verschleißfestigkeit, verringert die Reibung und bietet dekorative Oberflächen. |
Werkstoffe | Metalle (Titan, Aluminium), Legierungen (Ti-Mg) und Keramiken. |
Techniken | Aufdampfen, Sputtern und Laserablation. |
Branchen | Fertigung, Elektronik, Architektur und Kunstgewerbe. |
Zukünftige Trends | Moderne Legierungen, Nachhaltigkeit und neue biomedizinische Anwendungen. |
Erfahren Sie, wie PVD Ihre Produkte verändern kann. Kontaktieren Sie unsere Experten noch heute !