Spark Plasma Sintering (SPS) ist ein fortschrittliches pulvermetallurgisches Verfahren, bei dem gepulster Gleichstrom (DC) eingesetzt wird, um Materialien bei niedrigeren Temperaturen und in kürzerer Zeit als bei herkömmlichen Sinterverfahren schnell zu verdichten.Bei diesem Verfahren wird ein gepulster Hochenergiestrom auf Pulverpartikel angewendet, der lokal hohe Temperaturen (bis zu 10.000 °C) und ein Plasma erzeugt, das Verunreinigungen entfernt und die Partikeloberflächen aktiviert.Dies führt zu einer raschen Erhitzung, zum Schmelzen und Verschmelzen der Partikelgrenzflächen, wodurch dichte Strukturen mit einer Feststoffdichte von über 99 % entstehen.SPS ist auch als feldunterstützte Sintertechnik (FAST) oder elektrisch feldunterstütztes Sintern (EFAS) bekannt und wird häufig für die Herstellung hochwertiger Metall-, Keramik- und Verbundwerkstoffe verwendet.
Die wichtigsten Punkte werden erklärt:
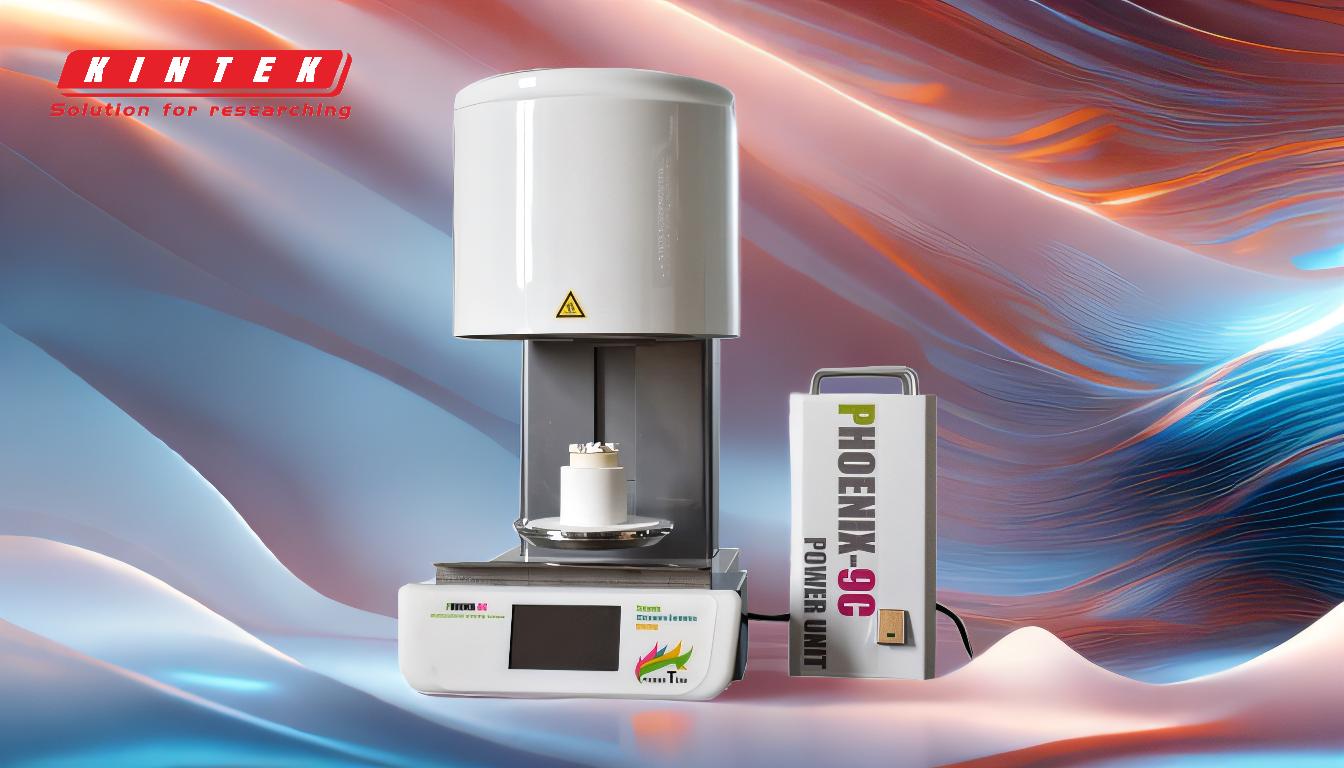
-
Prinzip des Spark-Plasma-Sinterns (SPS):
- Bei der SPS wird ein gepulster Gleichstrom direkt auf Pulverpartikel angewendet, wodurch elektrische Funkenentladungen und Plasma erzeugt werden.
- Die Hochenergieimpulse erzeugen örtlich begrenzte Temperaturen von bis zu 10.000 °C, wodurch Verunreinigungen entfernt und die Partikeloberflächen aktiviert werden.
- Dieser Prozess ermöglicht eine schnelle Verdichtung durch Schmelzen und Verschmelzen von Partikelgrenzflächen, wodurch dichte Strukturen, so genannte "Hälse", entstehen.
-
Mechanismus der Erwärmung:
- Der gepulste Strom fließt durch eine leitfähige Graphitmatrize und ggf. durch das Material selbst.
- Die Matrize dient als externe Wärmequelle, während das Material intern durch den elektrischen Strom erhitzt wird.
- Dieser doppelte Heizmechanismus ermöglicht extrem schnelle Aufheiz- und Abkühlraten, wodurch die Sinterzeiten erheblich verkürzt werden.
-
Vorteile von SPS:
- Niedrigere Sintertemperaturen:SPS erreicht die Verdichtung bei Temperaturen, die mehrere hundert Grad niedriger sind als bei herkömmlichen Sinterverfahren.
- Kürzere Verarbeitungszeiten:Schnelle Aufheiz- und Abkühlraten ermöglichen das Sintern in Minuten statt in Stunden.
- Hohe Dichte und Qualität:Das Verfahren erzeugt Materialien mit einer Feststoffdichte von über 99 % und minimalen Verunreinigungen.
- Vielseitigkeit:SPS kann für Metalle, Keramiken und Verbundwerkstoffe verwendet werden.
-
Anwendungen von SPS:
- Keramiken:SPS wird zur Herstellung von dichten keramischen Materialien wie Siliziumkarbid (SiC) mit Sinterhilfsmitteln wie Al2O3 und Y2O3 verwendet.
- Metalle:Es eignet sich für das Sintern von Metallpulvern zu Komponenten mit hoher Dichte.
- Verbundwerkstoffe:SPS ermöglicht die Herstellung von komplexen Verbundwerkstoffen mit verbesserten Eigenschaften.
-
Missverständnisse über SPS:
- Trotz des Namens hat die Forschung gezeigt, dass bei diesem Verfahren kein Plasma erzeugt wird.Alternative Bezeichnungen wie Field-Assisted Sintering Technique (FAST) oder Direct Current Sintering (DCS) sind zutreffender.
- Der Begriff "Funkenplasma" leitet sich von den lokalisierten hohen Temperaturen und den Effekten der Funkenentladung ab, nicht vom Vorhandensein eines Plasmas.
-
Prozesssteuerung und Parameter:
- Zu den wichtigsten Parametern gehören die Impulsstromstärke, die Heizrate, der angewandte Druck und die Haltezeit.
- Die präzise Steuerung dieser Parameter gewährleistet eine optimale Verdichtung und optimale Materialeigenschaften.
-
Vergleich mit konventionellem Sintern:
- Konventionelles Sintern erfordert externe Heizquellen und längere Verarbeitungszeiten, was häufig zu einer geringeren Dichte und höheren Verunreinigungsgraden führt.
- SPS bietet eine bessere Kontrolle über die Mikrostruktur und die Materialeigenschaften aufgrund des schnellen und lokalisierten Heizmechanismus.
-
Herausforderungen und Beschränkungen:
- Material Leitfähigkeit:Materialien mit geringer elektrischer Leitfähigkeit erfordern möglicherweise leitfähige Formen oder Zusätze, um den Prozess zu erleichtern.
- Ausrüstung Kosten:SPS-Systeme sind teurer als herkömmliche Sinteranlagen.
- Skalierbarkeit:Während SPS für die Produktion im Labormaßstab effektiv ist, bleibt die Ausweitung auf industrielle Anwendungen eine Herausforderung.
Zusammenfassend lässt sich sagen, dass das Spark-Plasma-Sintern eine hochmoderne Technik ist, die gepulste elektrische Ströme nutzt, um eine schnelle und hochwertige Verdichtung von Materialien zu erreichen.Seine Fähigkeit, bei niedrigeren Temperaturen und kürzeren Zeiten zu arbeiten, macht es zu einem wertvollen Werkzeug für die Herstellung fortschrittlicher Materialien mit hervorragenden Eigenschaften.Für eine breitere Anwendung in der Industrie müssen jedoch noch Herausforderungen in Bezug auf Kosten und Skalierbarkeit bewältigt werden.
Zusammenfassende Tabelle:
Aspekt | Einzelheiten |
---|---|
Prinzip | Gepulster Gleichstrom erzeugt lokal hohe Temperaturen (bis zu 10.000 °C), entfernt Verunreinigungen und aktiviert die Partikeloberflächen. |
Heizmechanismus | Zweifache Beheizung: extern (Graphitstempel) und intern (elektrischer Strom). |
Vorteile | Niedrigere Temperaturen, kürzere Zeiten, hohe Dichte (99%+) und Vielseitigkeit für Metalle, Keramik und Verbundwerkstoffe. |
Anwendungen | Keramiken (z. B. SiC), Metalle und Verbundwerkstoffe. |
Missverständnisse | Es wird kein echtes Plasma erzeugt; alternative Bezeichnungen sind FAST oder EFAS. |
Prozesssteuerung | Schlüsselparameter: Impulsstrom, Heizrate, Druck und Haltezeit. |
Herausforderungen | Leitfähigkeit des Materials, hohe Anlagenkosten und Einschränkungen bei der Skalierbarkeit. |
Erfahren Sie, wie Spark Plasma Sintering Ihre Materialproduktion verändern kann. Kontaktieren Sie uns noch heute !