Die Frequenz des Wechselstroms (AC) bei der Induktionserwärmung spielt eine entscheidende Rolle bei der Bestimmung der Tiefe der Wärmeerzeugung, der Effizienz und der Anwendungseignung.Höhere Frequenzen führen aufgrund des Skineffekts zu einer geringeren Wärmedurchdringung und sind daher ideal für Oberflächenerwärmung und Härteanwendungen.Niedrigere Frequenzen hingegen ermöglichen eine tiefere Wärmedurchdringung und eignen sich besser für die Erwärmung von Schüttgut oder Schmelzprozesse.Die Wahl der Frequenz wirkt sich auch auf die Leistungskapazität, die Turbulenzen in geschmolzenen Materialien und die Gesamteffizienz des Induktionserwärmungssystems aus.Das Verständnis dieser Auswirkungen ist entscheidend für die Auswahl der geeigneten Frequenz für bestimmte industrielle Anwendungen.
Die wichtigsten Punkte werden erklärt:
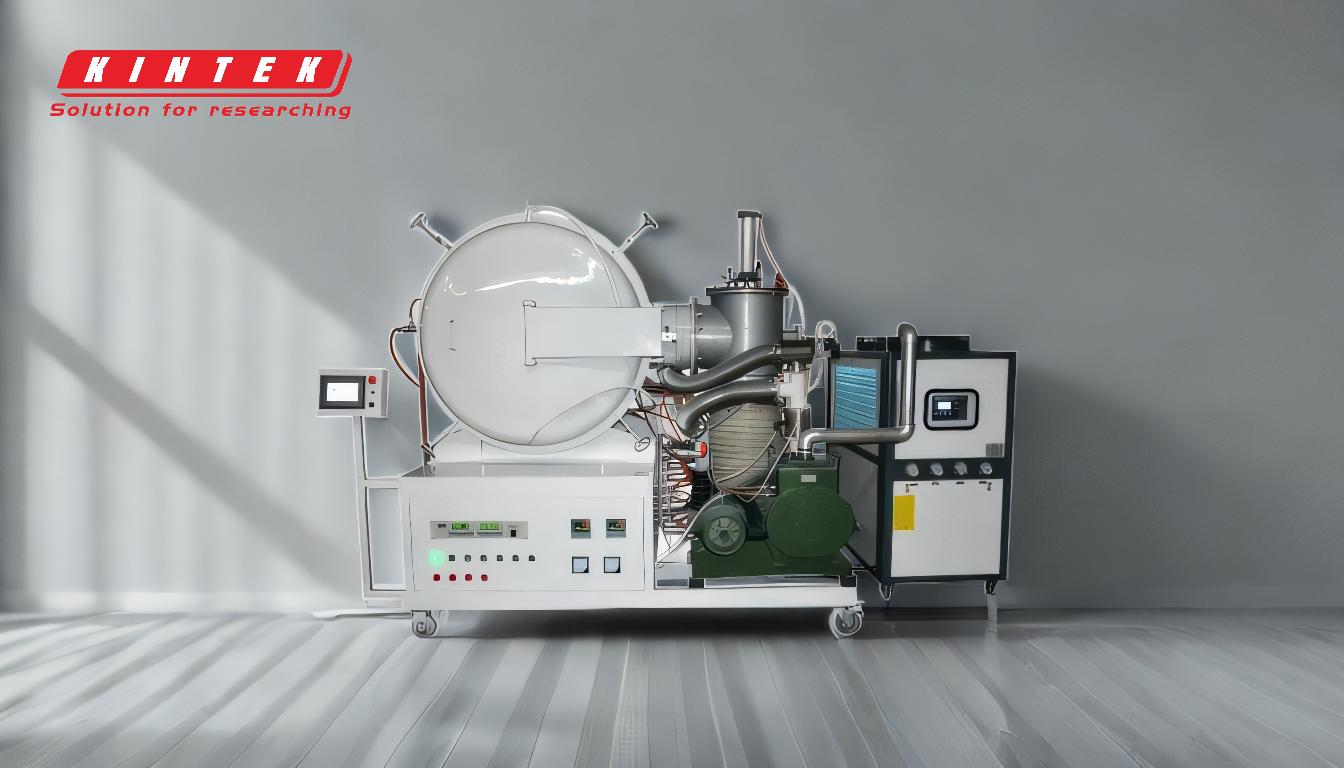
-
Frequenz und Magnetfelddynamik:
- Die Frequenz des Wechselstroms bestimmt, wie schnell das Magnetfeld seine Richtung ändert.Ein 60-Hz-Strom beispielsweise bewirkt, dass das Magnetfeld 60 Mal pro Sekunde die Richtung wechselt, während ein 400-kHz-Strom zu 400.000 Richtungswechseln pro Sekunde führt.
- Dieser schnelle Wechsel induziert Wirbelströme im Werkstück, die durch Widerstand Wärme erzeugen.Die Frequenz des Stroms in der Spule steuert direkt die Frequenz des induzierten Stroms im Werkstück.
-
Tiefe der Wärmeentwicklung (Skin-Effekt):
- Höhere Frequenzen (z. B. 400 kHz) erzeugen einen größeren Stromdichteunterschied zwischen der Oberfläche und dem Inneren des Werkstücks, was zu einer dünneren Heizschicht führt.Dieses Phänomen ist als Skin-Effekt bekannt.
- Niedrigere Frequenzen (z. B. 50-60 Hz) ermöglichen ein tieferes Eindringen des induzierten Stroms und eignen sich daher zur Erwärmung dickerer Materialien oder zur gleichmäßigen Erwärmung von Schüttgut.
-
Anwendungen basierend auf der Frequenz:
- Hohe Frequenzen:Ideal für die Oberflächenhärtung, bei der nur die äußere Schicht des Materials über seine kritische Temperatur erhitzt werden muss.Durch schnelles Abkühlen nach dem Erhitzen wird eine Oberflächenhärtung erreicht.
- Niedrige Frequenzen:Sie eignen sich zum Schmelzen oder Erhitzen großer Materialmengen, da sie tiefer eindringen und Rührungen oder Turbulenzen in geschmolzenen Metallen hervorrufen können.
-
Leistungskapazität und Wirkungsgrad:
- Höhere Frequenzen ermöglichen eine höhere Leistungszufuhr zu einem Ofen mit einer bestimmten Kapazität, was schnellere Erhitzungs- oder Schmelzprozesse ermöglicht.
- Niedrigere Frequenzen sind zwar für die Oberflächenerwärmung weniger leistungsfähig, für die Erwärmung von Schüttgut jedoch effizienter, da sie tiefer eindringen und den Energieverlust verringern.
-
Turbulenz und Rühren in geschmolzenen Materialien:
- Höhere Frequenzen führen zu weniger Turbulenzen in geschmolzenen Materialien, was für Anwendungen, die eine präzise Kontrolle der Schmelze erfordern, von Vorteil ist.
- Niedrigere Frequenzen können erhebliche Turbulenzen erzeugen, was beim Mischen oder Homogenisieren von Metallschmelzen von Vorteil sein kann.
-
Faktoren für die Frequenzauswahl:
- Materialeigenschaften:Die elektrische Leitfähigkeit und die magnetische Permeabilität des Materials beeinflussen die optimale Frequenz.
- Kapazität des Ofens:Kleinere Öfen oder Schmelzen erfordern aufgrund des Hauttiefeneffekts in der Regel höhere Frequenzen.
- Anforderungen an die Anwendung:Die gewünschte Erwärmungstiefe, Temperaturgleichmäßigkeit und Verarbeitungsgeschwindigkeit bestimmen die Wahl der Frequenz.
Durch das Verständnis dieser Schlüsselpunkte können Käufer von Geräten und Verbrauchsmaterialien fundierte Entscheidungen über die Frequenzeinstellungen für Induktionserwärmungssysteme treffen und so eine optimale Leistung und Effizienz für ihre spezifischen Anwendungen sicherstellen.
Zusammenfassende Tabelle:
Aspekt | Hochfrequenz (z. B. 400 kHz) | Niederfrequenz (z. B. 50-60 Hz) |
---|---|---|
Wärmedurchdringung | Oberflächlich (Hauteffekt) | Tief |
Anwendungen | Oberflächenhärtung, dünne Materialien | Massenerwärmung, Schmelzen, dicke Materialien |
Leistung | Höhere Leistung für schnellere Erwärmung | Geringere Leistung, effizient für Massenerwärmung |
Turbulenz in geschmolzenen Materialien | Minimale Turbulenz, präzise Kontrolle | Starke Verwirbelung, ideal zum Mischen |
Material Eignung | Dünne, leitfähige Materialien | Dickes, schüttfähiges Material |
Benötigen Sie Hilfe bei der Auswahl der richtigen Frequenz für Ihr Induktionserwärmungssystem? Kontaktieren Sie noch heute unsere Experten für maßgeschneiderte Lösungen!