Die Induktionserwärmung ist eine hocheffiziente und schnelle Methode zur Erwärmung leitfähiger Materialien, vor allem Metalle, durch Erzeugung von Wärme im Material selbst durch elektromagnetische Induktion.Die Erwärmungsgeschwindigkeit bei der Induktionserwärmung hängt von mehreren Faktoren ab, unter anderem von den Materialeigenschaften, der Konstruktion der Induktionsspule, der Frequenz des Wechselstroms und der Stromversorgungskapazität.Materialien mit höherem Widerstand und kleineren Abmessungen erwärmen sich schneller, während höhere Frequenzen zu einer geringeren Erwärmungstiefe führen.Induktionserwärmungssysteme sind bekannt für ihre Schnelligkeit, ihre Effizienz und ihre Fähigkeit zur präzisen Temperaturregelung, wodurch sie sich für eine Vielzahl von industriellen Anwendungen eignen.
Die wichtigsten Punkte werden erklärt:
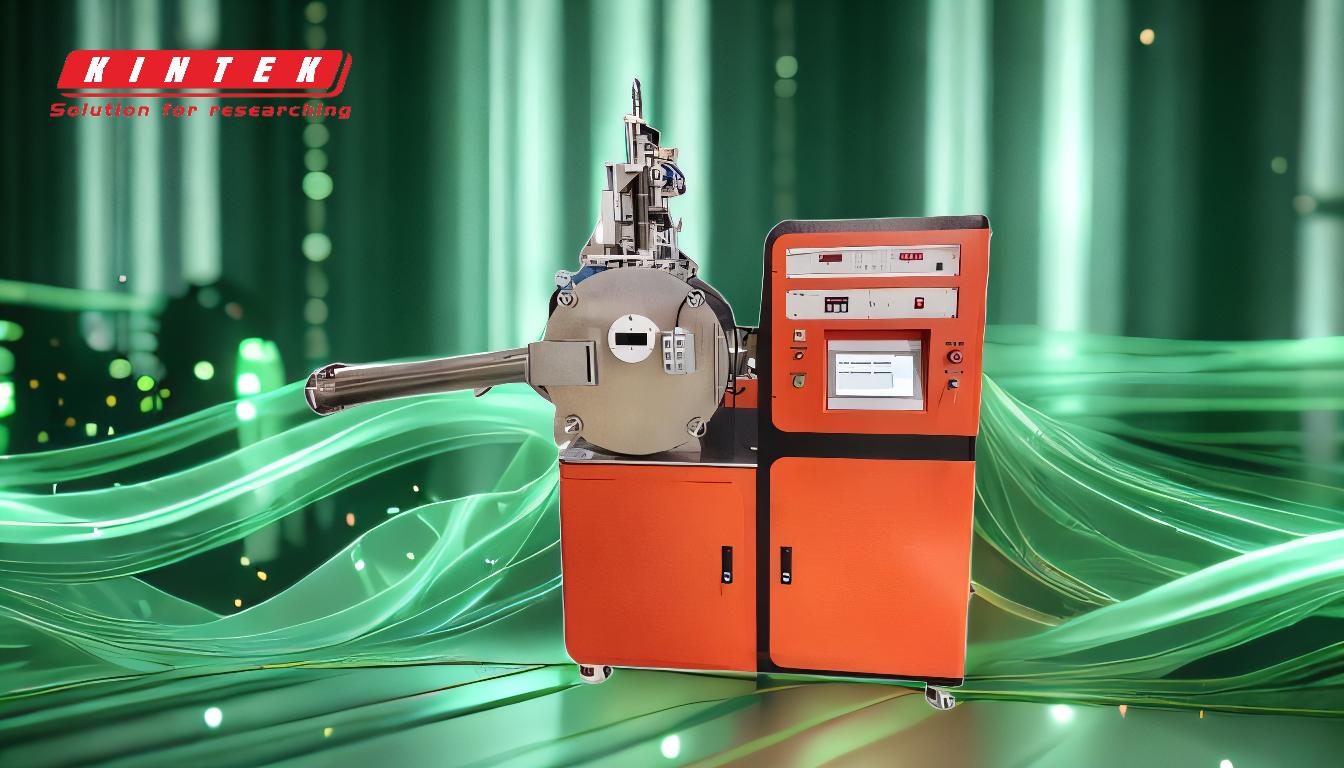
-
Erwärmungsmechanismus der Induktionserwärmung:
- Bei der Induktionserwärmung wird die Wärme durch elektromagnetische Induktion direkt im leitfähigen Material erzeugt.Dies wird erreicht, indem ein Wechselstrom durch eine Induktionsspule geleitet wird, die ein Magnetfeld erzeugt.Wenn sich ein leitfähiges Material in diesem Feld befindet, werden Wirbelströme induziert, die aufgrund des elektrischen Widerstands des Materials Wärme erzeugen.
- Diese Methode macht externe Wärmequellen überflüssig und ermöglicht eine schnelle und örtlich begrenzte Erwärmung ohne physischen Kontakt, was ideal für Anwendungen ist, die kontaminationsfreie Prozesse erfordern.
-
Faktoren, die die Erwärmungsrate beeinflussen:
-
Materialeigenschaften:
- Widerstandsfähigkeit:Materialien mit einem höheren spezifischen Widerstand erwärmen sich schneller, da sie mehr Wärme durch die induzierten Wirbelströme erzeugen.
- Spezifische Wärme und Masse:Materialien mit geringerer spezifischer Wärme und geringerer Masse erwärmen sich schneller, da weniger Energie benötigt wird, um den gewünschten Temperaturanstieg zu erreichen.
-
Größe und Dicke des Materials:
- Kleinere und dünnere Materialien erwärmen sich aufgrund ihrer geringeren thermischen Masse und kürzeren Wärmediffusionswege schneller.
-
Frequenz des Wechselstroms:
- Höhere Frequenzen führen zu einer geringeren Erwärmungstiefe (Skin-Effekt) und eignen sich daher für die Oberflächenerwärmung oder kleinere Bauteile.Niedrigere Frequenzen werden für eine tiefere Erwärmung größerer Materialien verwendet.
-
Design der Induktionsspule:
- Das Design der Induktionsspule spielt eine entscheidende Rolle bei der Bestimmung des Wirkungsgrads und der Heizleistung.Spezielle Spulenformen können die Heizleistung durch eine effektivere Fokussierung des Magnetfelds verbessern.
-
Materialeigenschaften:
-
Stromversorgung und Wirkungsgrad:
- Die Stromversorgungskapazität muss ausreichend sein, um den Energiebedarf der Anwendung zu decken, der von der spezifischen Wärme des Materials, der Masse, dem erforderlichen Temperaturanstieg und den Wärmeverlusten durch Leitung, Konvektion und Strahlung abhängt.
- Induktionserwärmungssysteme sind hocheffizient, wobei die Effizienz durch Fortschritte in der Halbleitertechnologie und optimierte Spulenkonstruktionen verbessert wurde.
-
Arten der Induktionserwärmung:
-
Hochfrequenz-Induktionserwärmung:
- Schnelle Heizraten, kompakte Größe und niedrige Kosten.Ideal für kleine Anwendungen oder Oberflächenerwärmung.
-
Induktionserwärmung mit mittlerer Frequenz:
- Bietet ein ausgewogenes Verhältnis zwischen Geschwindigkeit, Effizienz und Leistungsabgabe.Geeignet für größere Mengen und industrielle Anwendungen, die robuste und zuverlässige Systeme erfordern.
-
Hochfrequenz-Induktionserwärmung:
-
Anwendungen und Vorteile:
-
Die Induktionserwärmung ist in der Metallverarbeitung weit verbreitet, zum Beispiel beim Härten, Glühen, Löten und Schmelzen.Ihre Vorteile sind:
- Schnelle und präzise Erwärmung.
- Kein Außenkontakt, wodurch das Kontaminationsrisiko verringert wird.
- Hohe Energieeffizienz und Skalierbarkeit für verschiedene industrielle Anforderungen.
-
Die Induktionserwärmung ist in der Metallverarbeitung weit verbreitet, zum Beispiel beim Härten, Glühen, Löten und Schmelzen.Ihre Vorteile sind:
-
Zukünftige Entwicklungen:
- Es wird erwartet, dass die laufenden Fortschritte in der Halbleitertechnologie und bei der Konstruktion von Induktionsspulen die Effizienz, Leistung und Zuverlässigkeit von Induktionserwärmungssystemen weiter verbessern werden.Diese Entwicklungen werden ihre Einsatzmöglichkeiten erweitern und die Betriebskosten senken.
Zusammenfassend lässt sich sagen, dass die Erwärmungsgeschwindigkeit der Induktionserwärmung von einer Kombination aus Materialeigenschaften, Systemdesign und Betriebsparametern beeinflusst wird.Ihre Fähigkeit, eine schnelle, örtlich begrenzte und kontaminationsfreie Erwärmung zu ermöglichen, macht sie zu einer vielseitigen und effizienten Lösung für ein breites Spektrum industrieller Anwendungen.
Zusammenfassende Tabelle:
Faktor | Einfluss auf die Heizrate |
---|---|
Widerstandsfähigkeit des Materials | Materialien mit höherem Widerstand erwärmen sich schneller, da sie durch Wirbelströme mehr Wärme erzeugen. |
Spezifische Wärme und Masse | Materialien mit geringer spezifischer Wärme und geringer Masse erwärmen sich schneller. |
Größe und Dicke | Kleinere und dünnere Materialien erwärmen sich aufgrund der geringeren thermischen Masse schneller. |
Frequenz | Höhere Frequenzen führen zu einer flacheren Erwärmung, niedrigere Frequenzen sind besser für eine Tiefenerwärmung. |
Spulendesign | Optimierte Spulenkonstruktionen verbessern die Erwärmungseffizienz durch Fokussierung des Magnetfelds. |
Optimieren Sie Ihre industriellen Erwärmungsprozesse mit Induktionserwärmung - Kontaktieren Sie noch heute unsere Experten für maßgeschneiderte Lösungen!