Die Aufrechterhaltung eines Vakuums bei der Abscheidung von Dünnschichten ist entscheidend für die Erzielung hochwertiger, reiner und haftender Dünnschichten.Eine Vakuumumgebung minimiert das Vorhandensein von unerwünschten Substanzen wie Sauerstoff, Stickstoff und Kohlendioxid, die den Abscheidungsprozess stören, die Reinheit der Schichten verringern und die Haftung schwächen können.Durch die Verringerung der Partikeldichte und die Vergrößerung der mittleren freien Weglänge der Atome gewährleistet das Vakuum einen effizienten Materialtransport und minimiert die Verunreinigung.Außerdem ermöglicht es eine präzise Kontrolle der Gas- und Dampfzusammensetzung, erleichtert die Plasmabildung und unterstützt hohe thermische Verdampfungsraten.Diese Faktoren tragen gemeinsam zur Herstellung gleichmäßiger, leistungsstarker Dünnschichten mit verschiedenen Abscheidetechniken bei.
Die wichtigsten Punkte werden erklärt:
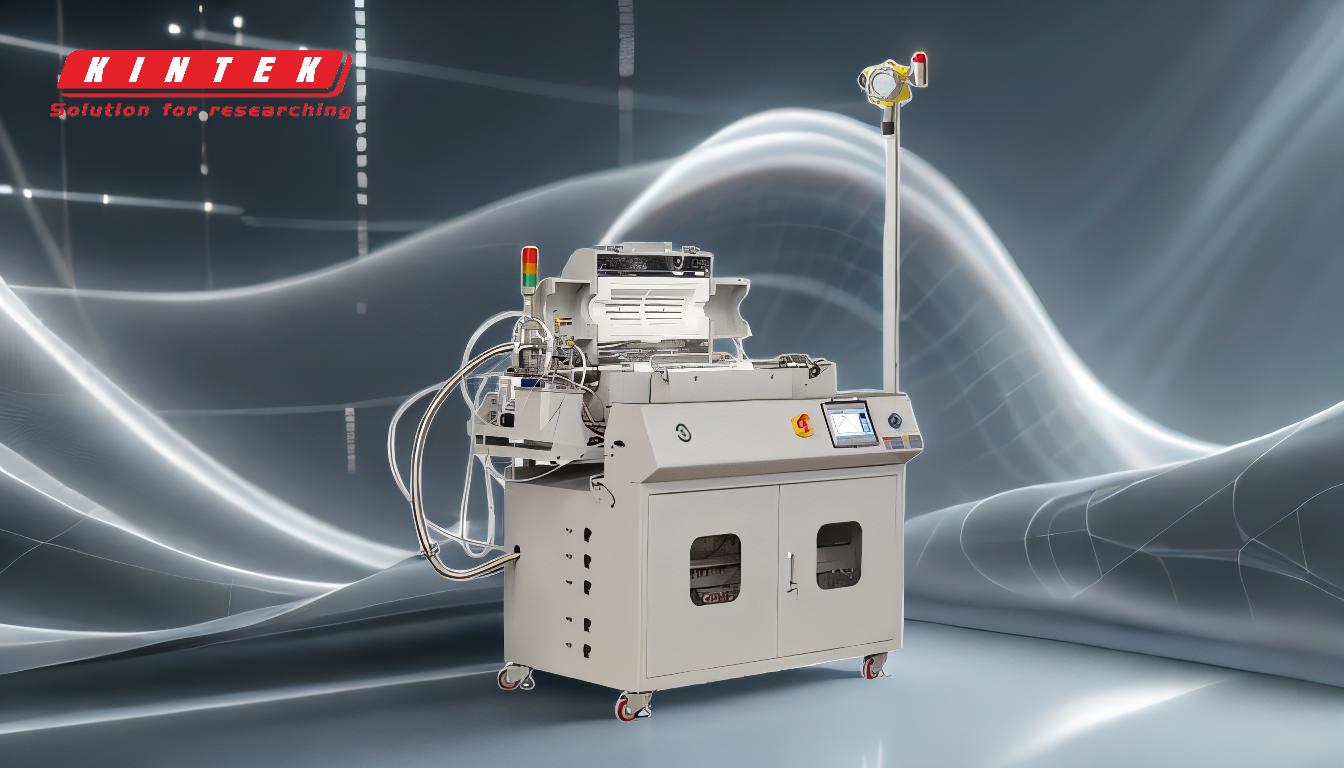
-
Reduktion unerwünschter Stoffe
- Eine Vakuumumgebung reduziert das Vorhandensein von Verunreinigungen wie Sauerstoff, Stickstoff, Kohlendioxid und Wasserdampf erheblich.
- Diese Stoffe können mit dem Filmmaterial reagieren, was zu Verunreinigungen oder unerwünschten chemischen Bindungen führt.
- So kann beispielsweise Sauerstoff das Folienmaterial oxidieren, wodurch sich seine Eigenschaften verändern und seine Funktionalität verringert wird.
-
Erhöhte Reinheit und Haftung
- Ein Hochvakuum sorgt dafür, dass das abgeschiedene Material rein bleibt, da es weniger Verunreinigungen gibt, die die Filmbildung stören könnten.
- Es wird eine stärkere Haftung erreicht, da sich die Filmpartikel direkt mit dem Substrat verbinden können, ohne mit Fremdpartikeln zu konkurrieren.
- Dies ist besonders wichtig für Anwendungen, bei denen die Integrität und Haltbarkeit des Films entscheidend ist, wie z. B. bei der Halbleiterherstellung oder bei optischen Beschichtungen.
-
Erhöhter mittlerer freier Weg
- Im Vakuum verringert sich die Dichte der Gasatome, wodurch sich die mittlere freie Weglänge der aufgedampften oder gesputterten Teilchen erhöht.
- Dadurch können die Teilchen längere Strecken ohne Zusammenstöße zurücklegen, was eine effiziente Abscheidung auf dem Substrat gewährleistet.
- Eine längere mittlere freie Weglänge ist für Verfahren wie die thermische Verdampfung und die Elektronenstrahlabscheidung, bei denen der Materialtransfer präzise und kontaminationsfrei erfolgen muss, von entscheidender Bedeutung.
-
Erleichterung der Plasmabildung
- Für die Bildung eines gasförmigen Plasmas bei Verfahren wie dem Sputtern ist eine Niederdruckumgebung erforderlich.
- Das Plasma ionisiert das Inertgas (z. B. Argon) und erzeugt ein Medium, das das Zielmaterial beschießt und Atome für die Abscheidung freisetzt.
- Ohne ein Vakuum wäre die Plasmabildung ineffizient und würde zu einer schlechten Schichtqualität führen.
-
Kontrolle über die Zusammensetzung von Gasen und Dämpfen
- Ein Vakuum ermöglicht die genaue Kontrolle über die Zusammensetzung der Gase und Dämpfe in der Beschichtungskammer.
- Dies ist entscheidend für Verfahren wie die chemische Gasphasenabscheidung (CVD) oder das reaktive Sputtern, bei denen spezifische Gasmischungen erforderlich sind, um die gewünschten Schichteigenschaften zu erzielen.
- Kontrollierte Umgebungen gewährleisten konsistente und wiederholbare Ergebnisse, die für industrielle Anwendungen unerlässlich sind.
-
Hohe thermische Verdampfungsraten
- Ein Vakuum ermöglicht hohe thermische Verdampfungsraten, indem es den Druck reduziert und es ermöglicht, dass Materialien mit relativ niedrigem Dampfdruck effizient verdampfen.
- Dies ist besonders wichtig für Materialien, die hohe Temperaturen zum Verdampfen benötigen, da ein Vakuum Wärmeverluste verhindert und eine gleichmäßige Verdampfung gewährleistet.
-
Minimierung von gasförmiger Kontamination
- Durch die Verringerung der Dichte unerwünschter Atome minimiert ein Vakuum das Risiko einer gasförmigen Verunreinigung während der Abscheidung.
- Verunreinigungen können die Eigenschaften der Folie beeinträchtigen, z. B. die elektrische Leitfähigkeit, die optische Transparenz oder die mechanische Festigkeit.
- Eine saubere Vakuumumgebung sorgt dafür, dass die Folie ihre vorgesehenen Eigenschaften behält.
-
Unterstützung für verschiedene Beschichtungstechniken
-
Vakuumumgebungen sind für eine breite Palette von Dünnschichtabscheidetechniken unerlässlich, darunter:
- Thermische Verdampfung:Sorgt für einen effizienten Materialtransfer und minimiert die Kontamination.
- Sputtern:Erleichtert die Plasmabildung und die präzise Steuerung der Abscheidungsparameter.
- Elektronenstrahl-Beschichtung:Ermöglicht eine hohe mittlere freie Weglänge für das aufgedampfte Material und sorgt für minimale Verluste.
- Chemische Gasphasenabscheidung (CVD):Ermöglicht kontrollierte Gasreaktionen zur Bildung hochwertiger Filme.
-
Vakuumumgebungen sind für eine breite Palette von Dünnschichtabscheidetechniken unerlässlich, darunter:
-
Gleichmäßige und hochleistungsfähige Schichten
- Die Kombination aus reduzierter Verunreinigung, erhöhter mittlerer freier Weglänge und kontrollierter Gaszusammensetzung führt zu gleichmäßigen und leistungsstarken Dünnschichten.
- Gleichmäßigkeit ist für Anwendungen wie die Mikroelektronik von entscheidender Bedeutung, wo selbst geringe Abweichungen in der Schichtdicke oder -zusammensetzung die Leistung der Geräte beeinträchtigen können.
- Hochleistungsfilme sind für fortschrittliche Technologien wie Solarzellen, Sensoren und Schutzbeschichtungen unerlässlich.
-
Anwendungen in Industrie und Forschung
- Die Bedeutung des Vakuums bei der Dünnschichtabscheidung erstreckt sich sowohl auf industrielle als auch auf Forschungsanwendungen.
- Bei industriellen Anwendungen ermöglichen Vakuumsysteme die Massenproduktion von hochwertigen Schichten mit gleichbleibenden Eigenschaften.
- In der Forschung ermöglichen Vakuumumgebungen Wissenschaftlern die Erforschung neuer Materialien und Abscheidetechniken, was Innovationen in Bereichen wie Nanotechnologie und erneuerbare Energien fördert.
Zusammenfassend lässt sich sagen, dass die Vakuumumgebung bei der Abscheidung von Dünnschichten unverzichtbar ist, da sie hohe Reinheit, starke Haftung und präzise Kontrolle über den Abscheidungsprozess gewährleistet.Durch die Minimierung von Verunreinigungen und die Ermöglichung eines effizienten Materialtransfers spielen Vakuumsysteme eine entscheidende Rolle bei der Herstellung hochwertiger Dünnschichten für ein breites Spektrum von Anwendungen.
Zusammenfassende Tabelle:
Hauptnutzen | Erläuterung |
---|---|
Reduktion von Verunreinigungen | Minimiert Sauerstoff, Stickstoff und Kohlendioxid und verhindert so Verunreinigungen. |
Erhöhte Reinheit und Adhäsion | Sorgt für einen reinen Materialauftrag und eine starke Bindung an das Substrat. |
Erhöhter mittlerer freier Weg | Ermöglicht es den Partikeln, längere Strecken ohne Kollisionen zurückzulegen, um eine effiziente Abscheidung zu erreichen. |
Plasmabildung | Erleichtert die Plasmabildung für Prozesse wie Sputtern. |
Kontrolle über die Gaszusammensetzung | Ermöglicht eine präzise Steuerung der Gase für konsistente und wiederholbare Ergebnisse. |
Hohe thermische Verdampfungsraten | Ermöglicht die effiziente Verdampfung von Materialien mit niedrigem Dampfdruck. |
Minimierte Verunreinigung | Reduziert gasförmige Verunreinigungen und bewahrt die Filmeigenschaften. |
Unterstützt mehrere Techniken | Unverzichtbar für thermisches Verdampfen, Sputtern, CVD und Elektronenstrahlabscheidung. |
Gleichmäßige, hochleistungsfähige Schichten | Produziert gleichmäßige Filme, die für die Mikroelektronik und fortschrittliche Technologien entscheidend sind. |
Industrie- und Forschungsanwendungen | Ermöglicht Massenproduktion und Innovation in den Bereichen Nanotechnologie und erneuerbare Energien. |
Erzielen Sie eine hervorragende Dünnschichtqualität mit unseren Vakuumlösungen. Kontaktieren Sie uns noch heute !