Die maximale Betriebstemperatur beim Löten hängt von mehreren Faktoren ab, darunter der Art des verwendeten Zusatzmetalls, den zu verbindenden Grundmaterialien und den spezifischen Anwendungsanforderungen. Im Allgemeinen liegen die Löttemperaturen zwischen 450 °C und 1200 °C, die Betriebstemperatur der Lötverbindung nach dem Prozess ist jedoch typischerweise niedriger. Für Hochtemperaturanwendungen können spezielle Zusatzwerkstoffe wie Legierungen auf Nickel- oder Goldbasis verwendet werden, die Temperaturen von bis zu 1000 °C oder mehr standhalten. Aber auch die thermische Stabilität des Grundmaterials und die Verbindungsgestaltung spielen eine entscheidende Rolle bei der Bestimmung der maximalen Einsatztemperatur. Die richtige Auswahl von Zusatzwerkstoffen und Lötparametern gewährleistet die Integrität und Leistung der Verbindung unter Hochtemperaturbedingungen.
Wichtige Punkte erklärt:
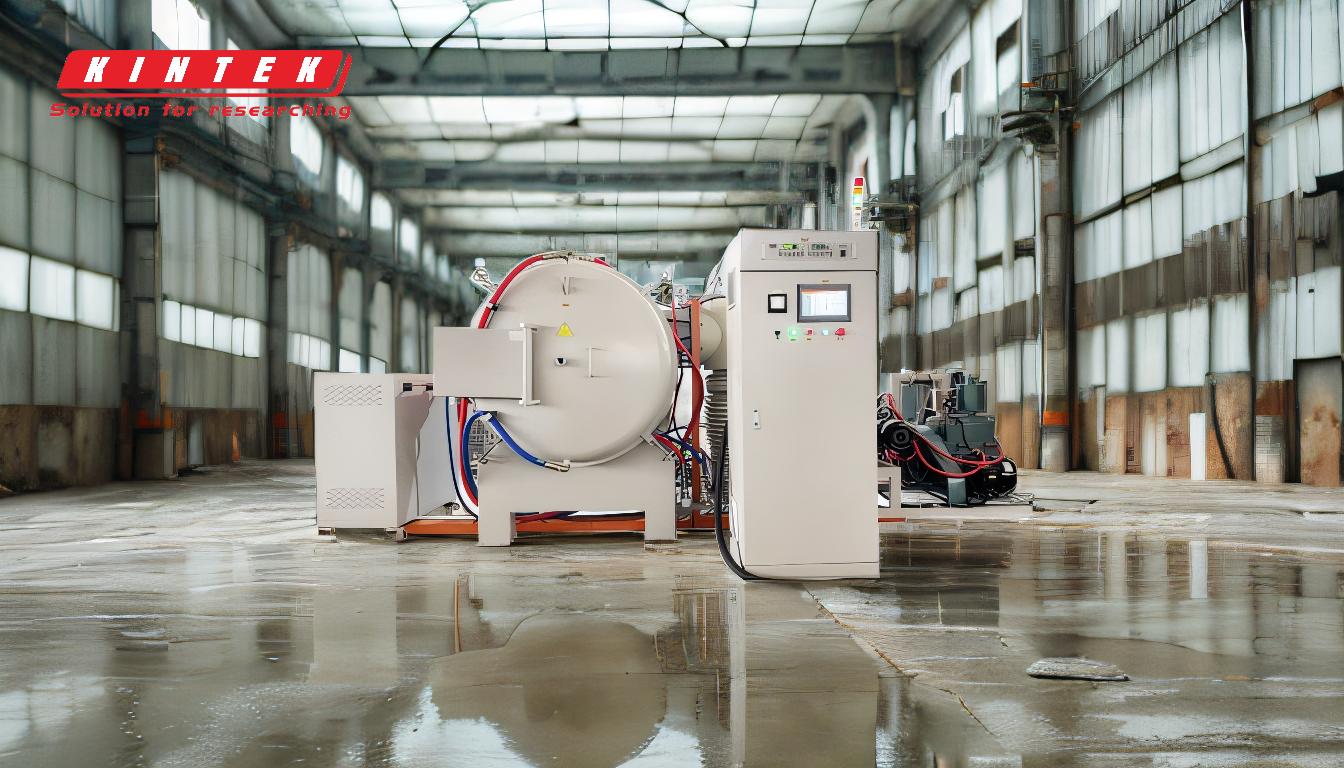
-
Löttemperaturbereich:
- Das Hartlöten erfolgt typischerweise bei Temperaturen zwischen 450 °C und 1200 °C, abhängig vom Zusatzwerkstoff und den Grundmaterialien.
- Die Löttemperatur wird so gewählt, dass das Zusatzmetall schmilzt, ohne dass die Grundmaterialien schmelzen, wodurch eine starke Verbindung gewährleistet wird.
-
Betriebstemperatur vs. Löttemperatur:
- Die Betriebstemperatur einer Lötverbindung ist die maximale Temperatur, der sie während des Betriebs standhalten kann. Sie liegt normalerweise unter der Löttemperatur.
- Beispielsweise könnte eine bei 800 °C gelötete Verbindung aufgrund von Materialbeschränkungen eine Betriebstemperatur von nur 600 °C haben.
-
Auswahl des Zusatzwerkstoffes:
-
Die Wahl des Zusatzwerkstoffs hat erheblichen Einfluss auf die maximale Betriebstemperatur. Zu den gängigen Zusatzmetallen gehören:
- Legierungen auf Silberbasis: Geeignet für Anwendungen bei niedrigeren Temperaturen, typischerweise bis zu 400 °C.
- Kupferbasierte Legierungen: Wird für Mitteltemperaturanwendungen bis 600 °C verwendet.
- Legierungen auf Nickelbasis: Ideal für Hochtemperaturanwendungen, beständig gegen Temperaturen von bis zu 1000 °C oder höher.
- Goldbasierte Legierungen: Wird in speziellen Anwendungen verwendet, die eine hohe thermische und chemische Stabilität erfordern.
-
Die Wahl des Zusatzwerkstoffs hat erheblichen Einfluss auf die maximale Betriebstemperatur. Zu den gängigen Zusatzmetallen gehören:
-
Überlegungen zum Grundmaterial:
- Die thermische Stabilität der Grundmaterialien begrenzt die maximale Einsatztemperatur. Beispielsweise weisen Aluminiumlegierungen im Vergleich zu Edelstahl oder Superlegierungen auf Nickelbasis eine geringere thermische Stabilität auf.
- Das Verbindungsdesign muss die Unterschiede in der Wärmeausdehnung zwischen den Grundmaterialien und dem Füllmetall berücksichtigen, um Risse oder Ausfälle bei hohen Temperaturen zu verhindern.
-
Anwendungsspezifische Anforderungen:
- In der Luft- und Raumfahrt- oder Energieerzeugungsindustrie müssen Hartlötverbindungen möglicherweise extremen Temperaturen und Belastungen standhalten. Um diesen Anforderungen gerecht zu werden, werden spezielle Legierungen und fortschrittliche Löttechniken eingesetzt.
- Nickelbasierte Zusatzmetalle werden beispielsweise aufgrund ihrer Hochtemperaturfestigkeit und Oxidationsbeständigkeit häufig in Gasturbinenkomponenten verwendet.
-
Faktoren, die die maximale Betriebstemperatur beeinflussen:
- Oxidationsbeständigkeit: Füllmetalle mit hoher Oxidationsbeständigkeit können die Verbindungsintegrität bei erhöhten Temperaturen aufrechterhalten.
- Kriechfestigkeit: Die Fähigkeit der Verbindung, Verformungen bei längerer Einwirkung hoher Temperaturen zu widerstehen.
- Temperaturwechsel: Wiederholtes Erhitzen und Abkühlen kann die Leistung der Verbindung beeinträchtigen. Daher müssen Materialien ausgewählt werden, die solchen Bedingungen standhalten.
-
Testen und Validieren:
- Hartgelötete Verbindungen, die für den Einsatz bei hohen Temperaturen vorgesehen sind, werden häufig strengen Tests unterzogen, darunter Temperaturwechsel-, Zugfestigkeitstests und metallurgische Analysen, um sicherzustellen, dass sie den Leistungsanforderungen entsprechen.
Durch die sorgfältige Auswahl des geeigneten Zusatzmetalls, der Grundmaterialien und der Lötparameter ist es möglich, Lötverbindungen zu schaffen, die auch bei anspruchsvollen Anwendungen bei hohen Temperaturen zuverlässig funktionieren.
Übersichtstabelle:
Faktor | Einzelheiten |
---|---|
Löttemperatur | 450°C bis 1200°C, abhängig vom Zusatzwerkstoff und Grundwerkstoff |
Betriebstemperatur | Typischerweise niedriger als die Löttemperatur (z. B. 600 °C für 800 °C-Löten) |
Zusatzmetalle | Silberbasis (bis 400°C), Kupferbasis (bis 600°C), Nickelbasis (1000°C+), Goldbasis (spezialisiert) |
Grundmaterialien | Die thermische Stabilität variiert (z. B. Aluminiumlegierungen vs. Edelstahl) |
Anwendungsanforderungen | Luft- und Raumfahrt, Energieerzeugung und andere Hochtemperaturumgebungen |
Wichtige Überlegungen | Oxidationsbeständigkeit, Kriechfestigkeit, Temperaturwechsel und Verbindungsdesign |
Benötigen Sie Hilfe bei der Auswahl der richtigen Lötlösung für Ihre Hochtemperaturanwendung? Kontaktieren Sie noch heute unsere Experten!