Chemische Niederdruck-Gasphasenabscheidungssysteme (LPCVD) arbeiten normalerweise in einem Druckbereich von 0,1 bis 10 Torr was als mittleres Vakuum angesehen wird.Dieser Druckbereich ist wichtig, um eine gleichmäßige Schichtabscheidung zu erreichen, Gasphasenreaktionen zu minimieren und qualitativ hochwertige dünne Schichten zu gewährleisten.Die Betriebstemperatur für LPCVD-Anlagen liegt im Allgemeinen zwischen 425°C bis 900°C je nach dem abzuscheidenden Material.So wird beispielsweise Siliziumdioxid häufig bei etwa 650 °C abgeschieden.Die Druck- und Temperaturbereiche werden sorgfältig kontrolliert, um die Filmeigenschaften, wie Gleichmäßigkeit, Dichte und Haftung, zu optimieren und gleichzeitig Defekte und Verunreinigungen zu minimieren.
Die wichtigsten Punkte erklärt:
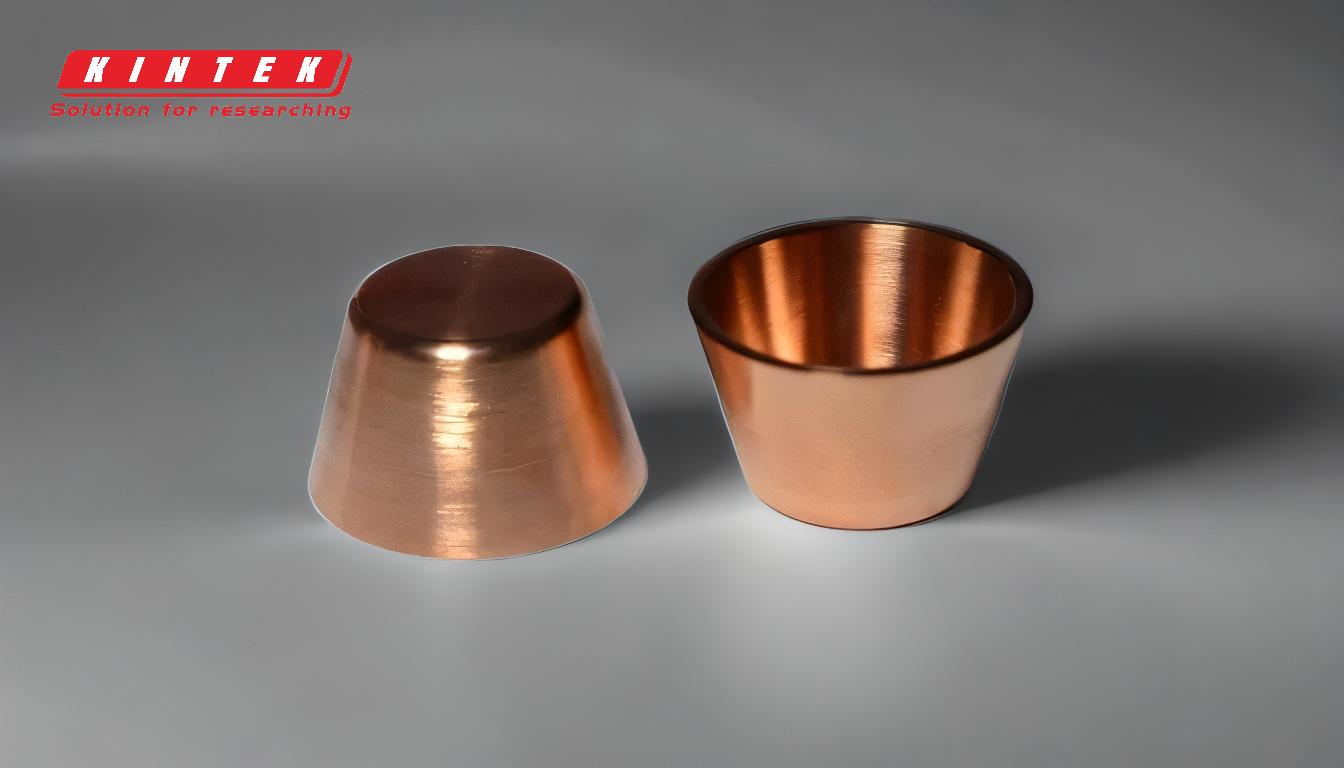
-
Druckbereich in LPCVD-Anlagen:
- LPCVD-Anlagen arbeiten in der Regel bei Drücken zwischen 0,1 bis 10 Torr .
- Dieser Bereich wird als mittleres Vakuum eingestuft, das niedriger als der Atmosphärendruck (760 Torr), aber höher als Hochvakuumsysteme ist.
- Die Niederdruckumgebung reduziert die Gasphasenreaktionen und fördert die gleichmäßige Schichtabscheidung, indem sie sicherstellt, dass die Reaktionsgase die Substratoberfläche ohne nennenswerte Streuung erreichen.
-
Die Bedeutung der Druckkontrolle:
- Die Aufrechterhaltung eines präzisen Druckbereichs ist entscheidend für eine gleichbleibende Filmqualität.
- Die Druckregelung wird durch Vakuumpumpen und Druckregelungssysteme erreicht, die dafür sorgen, dass der Druck während des gesamten Beschichtungsprozesses konstant bleibt.
- Abweichungen vom optimalen Druckbereich können zu Defekten, schlechter Schichtgleichmäßigkeit oder unvollständigen Reaktionen führen.
-
Temperaturbereich bei LPCVD:
- LPCVD-Prozesse erfordern in der Regel hohe Temperaturen, die zwischen 425°C bis 900°C .
-
Die spezifische Temperatur hängt von dem aufzubringenden Material ab.Zum Beispiel:
- Siliziumdioxid wird häufig bei etwa 650°C .
- Für andere Materialien wie Siliziumnitrid oder Polysilizium können höhere Temperaturen erforderlich sein.
- Hohe Temperaturen sind notwendig, um die chemischen Reaktionen zu aktivieren, die die dünnen Schichten auf dem Substrat bilden.
-
Vergleich mit anderen CVD-Techniken:
-
PECVD (Plasma-unterstützte chemische Gasphasenabscheidung):
- Funktioniert bei niedrigeren Drücken (typischerweise 0,1 bis 10 Torr ) und niedrigere Temperaturen ( 200°C bis 500°C ).
- Nutzt Plasma zur Verbesserung chemischer Reaktionen, was niedrigere Betriebstemperaturen ermöglicht.
-
APCVD (Atmospheric Pressure Chemical Vapor Deposition):
- Wird bei oder nahe Atmosphärendruck betrieben, was im Vergleich zur LPCVD zu stärkeren Gasphasenreaktionen und weniger gleichmäßigen Schichten führen kann.
- Die LPCVD schafft ein Gleichgewicht zwischen den hochwertigen Schichten der Niederdrucksysteme und dem höheren Durchsatz der Atmosphärensysteme.
-
PECVD (Plasma-unterstützte chemische Gasphasenabscheidung):
-
Vorteile der LPCVD:
- Uniform Film Deposition:Die Niederdruckumgebung sorgt dafür, dass die Reaktionsgase gleichmäßig über das Substrat verteilt werden, was zu sehr gleichmäßigen Schichten führt.
- Hochwertige Filme:Die Kombination aus niedrigem Druck und hoher Temperatur führt zu dichten, fehlerfreien Filmen mit ausgezeichneter Haftung.
- Vielseitigkeit:Mit LPCVD kann eine breite Palette von Materialien abgeschieden werden, darunter Siliziumdioxid, Siliziumnitrid und Polysilizium, wodurch es sich für verschiedene Halbleiter- und MEMS-Anwendungen eignet.
-
Anwendungen von LPCVD:
- Die LPCVD wird in der Halbleiterindustrie in großem Umfang für die Abscheidung dünner Schichten bei der Herstellung integrierter Schaltkreise (IC) eingesetzt.
- Sie wird auch bei der Herstellung von mikroelektromechanischen Systemen (MEMS) eingesetzt, bei denen eine präzise Kontrolle der Schichtdicke und der Gleichmäßigkeit entscheidend ist.
-
Zu den gängigen Materialien, die mit LPCVD abgeschieden werden, gehören:
- Siliziumdioxid (SiO₂):Wird als Isolierschicht in ICs verwendet.
- Siliziumnitrid (Si₃N₄):Wird als Passivierungsschicht oder Maske in der Lithografie verwendet.
- Polysilizium:Wird für Gate-Elektroden in Transistoren verwendet.
-
System-Konfigurationen:
-
LPCVD-Systeme gibt es in verschiedenen Konfigurationen, darunter:
- Röhrenförmige Heißwandreaktoren:Hierbei handelt es sich um Batch-Systeme, bei denen mehrere Wafer gleichzeitig in einem beheizten Rohr verarbeitet werden.
- Vertikale Durchfluss-Batch-Reaktoren:Diese Systeme ermöglichen eine bessere Kontrolle des Gasflusses und werden häufig für die Produktion großer Mengen eingesetzt.
- Single-Wafer-Reaktoren:Diese werden in modernen Fabriken zur besseren Prozesskontrolle und -integration eingesetzt, insbesondere in der fortgeschrittenen Halbleiterfertigung.
-
LPCVD-Systeme gibt es in verschiedenen Konfigurationen, darunter:
-
Herausforderungen und Überlegungen:
- Thermischer Haushalt:Die hohen Temperaturen, die für die LPCVD erforderlich sind, können den Einsatz in Verfahren einschränken, bei denen eine thermische Schädigung des Substrats zu befürchten ist.
- Durchsatz:Batch-Systeme bieten einen höheren Durchsatz, können aber im Vergleich zu Single-Wafer-Systemen eine gewisse Uniformität einbüßen.
- Kosten:Der Betrieb von LPCVD-Anlagen kann teuer sein, da sie eine präzise Temperatur- und Druckregelung sowie eine hochwertige Vakuumausrüstung erfordern.
Wenn man die Druck- und Temperaturbereiche von LPCVD-Anlagen sowie ihre Vorteile und Grenzen kennt, können die Käufer von Anlagen und Verbrauchsmaterialien fundierte Entscheidungen über die Eignung von LPCVD für ihre spezifischen Anwendungen treffen.
Zusammenfassende Tabelle:
Parameter | Bereich | Einzelheiten |
---|---|---|
Druckbereich | 0,1 bis 10 Torr | Mittleres Vakuum, unerlässlich für eine gleichmäßige Schichtabscheidung und minimale Gasphasenreaktionen. |
Temperaturbereich | 425°C bis 900°C | Abhängig vom Material (z. B. 650°C für SiO₂).Hohe Temperaturen aktivieren Reaktionen. |
Die wichtigsten Vorteile | Gleichmäßigkeit, Qualität, Vielseitigkeit | Sorgt für dichte, fehlerfreie Filme mit hervorragender Haftung. |
Anwendungen | Halbleiter, MEMS | Für die IC-Fertigung, MEMS-Produktion und die Abscheidung von SiO₂, Si₃N₄ und Polysilizium. |
System-Konfigurationen | Röhrenförmig, vertikal, Einzel-Wafer | Batch- oder Single-Wafer-Systeme für unterschiedlichen Durchsatz und Präzision. |
Benötigen Sie fachkundige Beratung zu LPCVD-Anlagen? Kontaktieren Sie uns noch heute um Ihre Dünnschichtprozesse zu optimieren!