Vakuumabschrecken ist ein spezielles Wärmebehandlungsverfahren zur Verbesserung der mechanischen Eigenschaften von Metallen, insbesondere von Stahl und Legierungen. Dabei wird das Werkstück in einer Vakuumumgebung auf eine bestimmte Temperatur erhitzt, es für eine vorgegebene Zeit auf dieser Temperatur gehalten und dann mit einem Kühlmedium wie Gas, Öl oder Wasser schnell abgekühlt. Dieser Prozess verändert die Mikrostruktur des Metalls und wandelt typischerweise Austenit in Martensit um, was die Härte und Festigkeit erhöht. Die Vakuumumgebung verhindert Oxidation und Kontamination und sorgt so für eine saubere und präzise Behandlung. Das Verfahren wird häufig in Branchen eingesetzt, die Hochleistungsmaterialien erfordern, beispielsweise in der Luft- und Raumfahrt, im Automobilbau und im Werkzeugbau.
Wichtige Punkte erklärt:
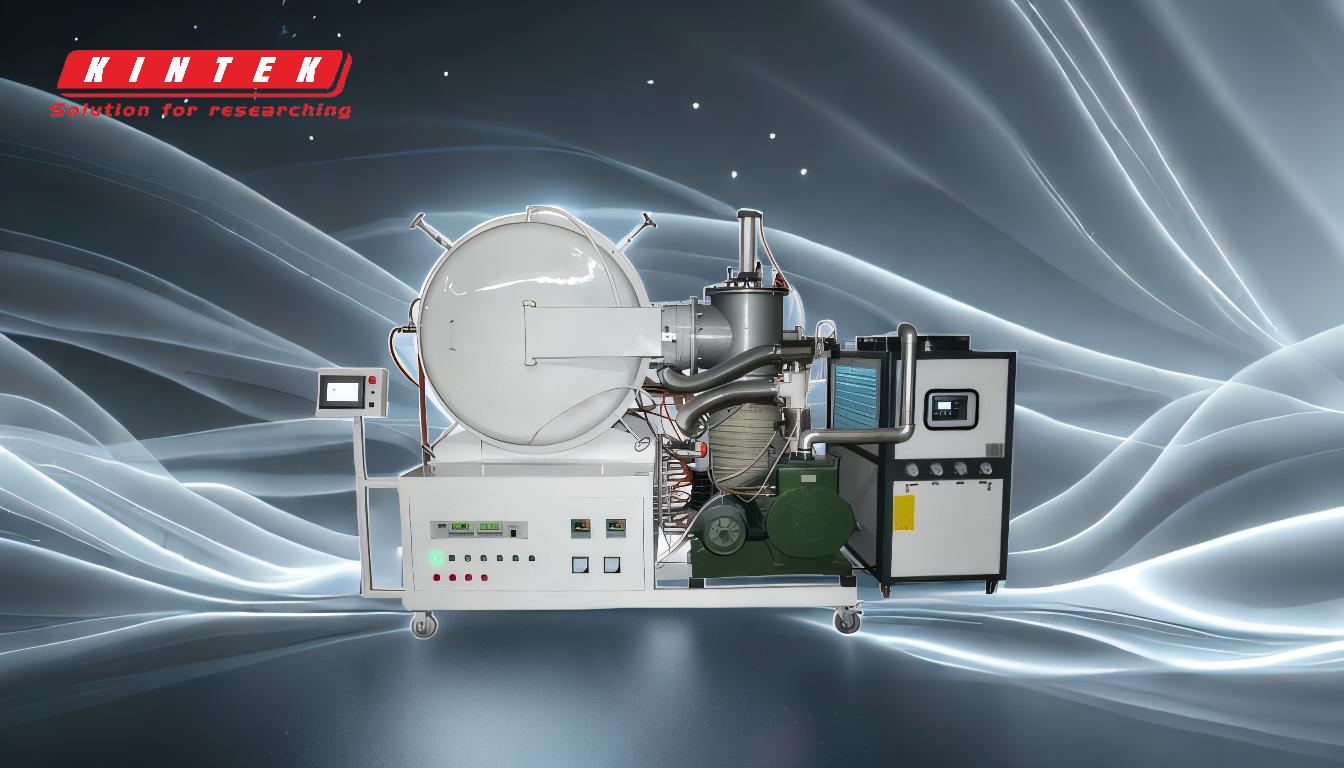
-
Beladung des Ofens:
- Der erste Schritt beim Vakuumabschrecken besteht darin, das Werkstück in die Vakuumkammer zu laden. Dabei werden die Teile, Werkzeuge oder Komponenten so in der Kammer platziert, dass eine gleichmäßige Erwärmung und Kühlung gewährleistet ist. Die richtige Belastung ist entscheidend, um gleichmäßige Eigenschaften am gesamten Werkstück zu erreichen.
-
Vakuum erzeugen:
- Sobald das Werkstück geladen ist, wird die Kammer verschlossen und ein Vakuum erzeugt, indem mithilfe einer Vakuumpumpe sämtlicher Sauerstoff und andere Gase entfernt werden. Dieser Schritt ist wichtig, um Oxidation und Kontamination des Werkstücks zu verhindern. Das Vakuumniveau wird während des gesamten Erhitzungs- und Abschreckprozesses aufrechterhalten, um eine saubere Umgebung zu gewährleisten.
-
Erhitzen des Werkstücks:
- Anschließend wird das Werkstück mithilfe präziser Temperaturkontrollen auf eine bestimmte Temperatur, die sogenannte Austenitisierungstemperatur, erhitzt. Diese Temperatur variiert je nach Metallart und den gewünschten Eigenschaften. Das Werkstück wird für einen festgelegten Zeitraum auf dieser Temperatur gehalten, damit sich die Mikrostruktur vollständig in Austenit umwandeln kann.
-
Abschrecken:
-
Nach der Aufheizphase wird das Werkstück mit einem Kühlmedium schnell abgekühlt. Die Wahl des Kühlmediums hängt vom Material und den gewünschten Eigenschaften ab. Zu den gängigen Kühlmedien gehören:
- Gasabschreckung: Zur Kühlung des Werkstücks werden hochreine Inertgase wie Stickstoff oder Argon verwendet. Diese Methode ist sauber und verhindert chemische Reaktionen, die die Eigenschaften des Metalls verändern könnten.
- Flüssigkeitsabschreckung: Das Werkstück wird in einem Abschreckölbad schnell abgekühlt. Diese Methode ist aggressiver und wird verwendet, wenn eine höhere Kühlrate erforderlich ist.
- Wasserabschreckung: In einigen Fällen wird Wasser als Kühlmedium verwendet, insbesondere bei Materialien, die eine sehr schnelle Abkühlung erfordern.
-
Nach der Aufheizphase wird das Werkstück mit einem Kühlmedium schnell abgekühlt. Die Wahl des Kühlmediums hängt vom Material und den gewünschten Eigenschaften ab. Zu den gängigen Kühlmedien gehören:
-
Abkühlen und Endbearbeitung:
- Nach dem Abschrecken wird das Werkstück weiter auf Raumtemperatur abgekühlt. In einigen Fällen können zusätzliche Wärmebehandlungsverfahren wie Anlassen angewendet werden, um die Sprödigkeit zu verringern und die Zähigkeit zu verbessern. Der letzte Schritt besteht darin, das Werkstück zu prüfen, um sicherzustellen, dass es den erforderlichen Spezifikationen entspricht.
-
Arten von Abschreckprozessen:
- Gasabschreckung: Dabei wird das Werkstück nach dem Erhitzen im Vakuum in einem hochreinen Neutralgas gekühlt. Es wird üblicherweise für Materialien verwendet, die eine saubere und kontrollierte Kühlumgebung erfordern.
- Flüssigkeitsabschreckung: Dabei erfolgt nach dem Erhitzen eine schnelle Abkühlung in einem Abschreckölbad. Das Werkstück wird in eine mit hochreinem Stickstoff gefüllte Kühlkammer bewegt, um eine Oxidation während des Abkühlvorgangs zu verhindern.
-
Ausrüstung und Komponenten:
- Das Vakuumsystem in einem Vakuumofen umfasst Komponenten wie Vakuumventile, mechanische Pumpen, Diffusionspumpen und Roots-Pumpen. Diese Komponenten arbeiten zusammen, um das gewünschte Vakuumniveau zu erreichen und aufrechtzuerhalten, das typischerweise bei etwa 7 × 10^-3 Pa liegt Vakuum-Reinigungsofen spielt eine entscheidende Rolle bei der Gewährleistung der Sauberkeit und Effizienz des Abschreckprozesses.
-
Anwendungen und Vorteile:
-
Das Vakuumabschrecken wird häufig in Branchen eingesetzt, die Hochleistungsmaterialien erfordern, beispielsweise in der Luft- und Raumfahrt, im Automobilbau und im Werkzeugbau. Zu den Vorteilen gehören:
- Verbesserte mechanische Eigenschaften: Erhöhte Härte, Festigkeit und Verschleißfestigkeit.
- Saubere und präzise Behandlung: Die Vakuumumgebung verhindert Oxidation und Kontamination und sorgt so für ein hochwertiges Finish.
- Vielseitigkeit: Das Verfahren kann auf unterschiedliche Materialien und Kühlanforderungen zugeschnitten werden und ist somit für ein breites Anwendungsspektrum geeignet.
-
Das Vakuumabschrecken wird häufig in Branchen eingesetzt, die Hochleistungsmaterialien erfordern, beispielsweise in der Luft- und Raumfahrt, im Automobilbau und im Werkzeugbau. Zu den Vorteilen gehören:
Zusammenfassend lässt sich sagen, dass das Vakuumabschrecken ein hochgradig kontrollierter und präziser Wärmebehandlungsprozess ist, der die mechanischen Eigenschaften von Metallen verbessert. Durch den Einsatz einer Vakuumumgebung und sorgfältig ausgewählter Kühlmedien gewährleistet es eine saubere und effiziente Behandlung und ist somit ideal für Hochleistungsanwendungen.
Übersichtstabelle:
Schritt | Beschreibung |
---|---|
Beladen des Ofens | Legen Sie das Werkstück in die Vakuumkammer, um es gleichmäßig zu erwärmen und abzukühlen. |
Ein Vakuum erzeugen | Entfernen Sie Sauerstoff und Gase, um Oxidation und Kontamination zu verhindern. |
Heizung | Zur Mikrostrukturumwandlung auf Austenitisierungstemperatur erhitzen. |
Abschrecken | Mit Gas, Öl oder Wasser schnell abkühlen, um die gewünschten Eigenschaften zu erreichen. |
Abkühlen und Endbearbeitung | Auf Raumtemperatur abkühlen lassen; Überprüfen Sie die Situation und wenden Sie bei Bedarf zusätzliche Behandlungen an. |
Anwendungen | Luft- und Raumfahrt, Automobilbau und Werkzeugbau für Hochleistungswerkstoffe. |
Entdecken Sie, wie Vakuumabschrecken Ihre Metallbehandlung optimieren kann – Kontaktieren Sie noch heute unsere Experten !