Die Oberflächenhärtung ist ein entscheidender Prozess in der Werkstofftechnik, der darauf abzielt, die Haltbarkeit und Leistung von Metallkomponenten zu verbessern. Dabei wird die Oberflächenschicht eines Metalls verändert, um dessen Härte zu verbessern und gleichzeitig die Zähigkeit des Kernmaterials beizubehalten. Dieser Prozess ist in Branchen von entscheidender Bedeutung, in denen Komponenten hohem Verschleiß, Ermüdung oder Stößen ausgesetzt sind, beispielsweise in der Automobilindustrie, in der Luft- und Raumfahrt sowie in der Fertigung. Durch die Oberflächenhärtung wird nicht nur die Lebensdauer der Teile verlängert, sondern auch die Wartungskosten gesenkt und die Gesamteffizienz verbessert. Die zur Oberflächenhärtung eingesetzten Techniken variieren je nach Material und Anwendung, haben jedoch alle das gemeinsame Ziel, eine harte, verschleißfeste Oberfläche zu schaffen, ohne die strukturelle Integrität des Bauteils zu beeinträchtigen.
Wichtige Punkte erklärt:
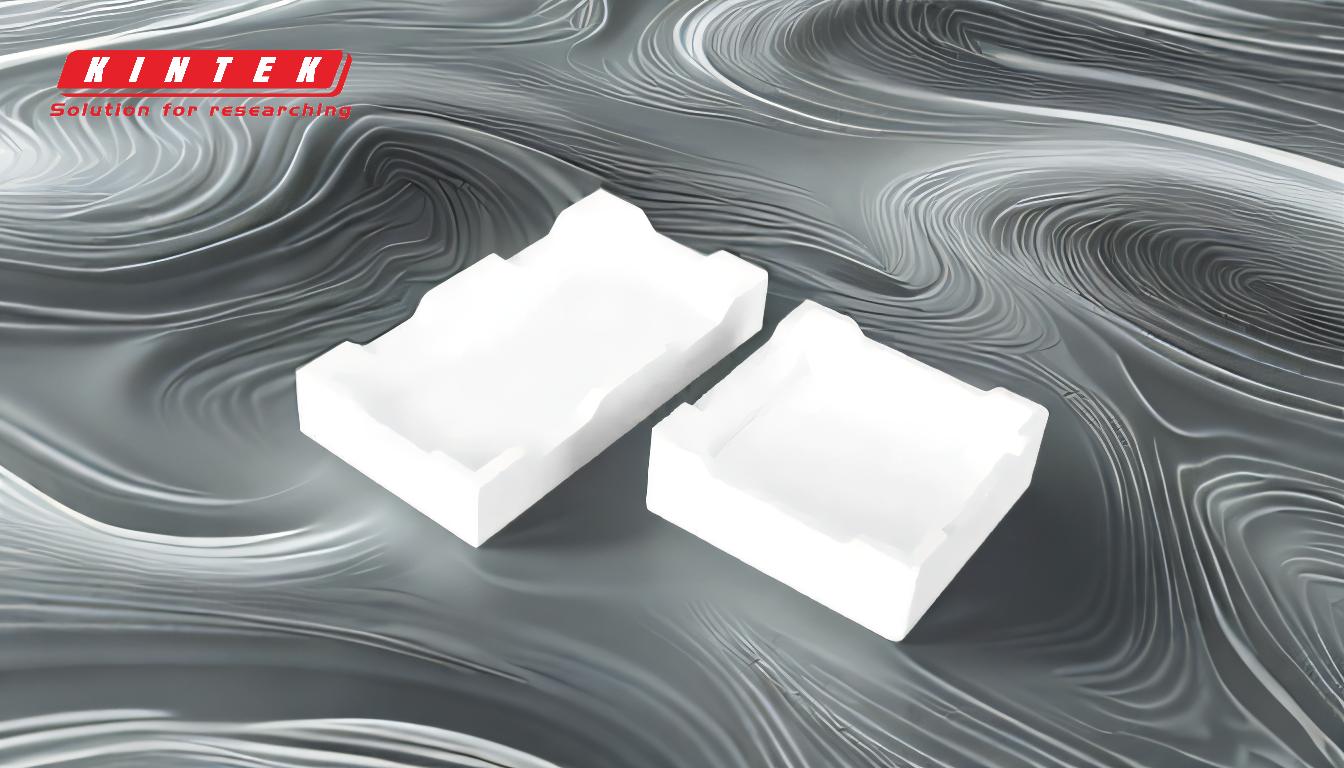
-
Verbesserte Verschleißfestigkeit:
- Durch die Oberflächenhärtung wird die Härte der äußeren Schicht eines Metallbauteils deutlich erhöht und dadurch widerstandsfähiger gegen Verschleiß und Abrieb. Dies ist besonders wichtig für Teile, die in ständigem Kontakt mit anderen Oberflächen stehen, wie z. B. Zahnräder, Lager und Schneidwerkzeuge. Durch die Härtung der Oberfläche hält das Bauteil den im Betrieb auftretenden mechanischen Belastungen und Reibungen stand, wodurch der Verschleiß verringert und die Lebensdauer verlängert wird.
-
Verbesserte Ermüdungsfestigkeit:
- Ermüdungsversagen tritt auf, wenn ein Material wiederholten zyklischen Belastungen ausgesetzt ist, was zur Bildung von Rissen und schließlich zum Versagen führt. Oberflächenhärteverfahren, wie z Einsatzhärten oder Nitrieren führen Druckeigenspannungen in die Oberfläche des Werkstoffs ein. Diese Spannungen wirken den Zugspannungen entgegen, die Ermüdungsrisse verursachen, und verbessern so die Dauerfestigkeit des Bauteils. Dies ist von entscheidender Bedeutung für Teile, die einer zyklischen Belastung ausgesetzt sind, wie z. B. Federn, Wellen und Strukturkomponenten.
-
Behielt die Kernfestigkeit bei:
- Einer der Hauptvorteile der Oberflächenhärtung besteht darin, dass der Kern des Materials seine ursprüngliche Zähigkeit und Duktilität behält. Während die Oberfläche hart und verschleißfest wird, bleibt der Kern zäh und kann Aufprallenergie absorbieren, ohne zu brechen. Diese Kombination aus harter Oberfläche und zähem Kern ist ideal für Komponenten, die sowohl Verschleiß als auch Stößen standhalten müssen, wie z. B. Zahnräder, Kurbelwellen und Nockenwellen.
-
Korrosionsbeständigkeit:
- Bestimmte Oberflächenhärtungstechniken, wie z Nitrieren und Aufkohlen kann auch die Korrosionsbeständigkeit von Metallkomponenten verbessern. Diese Prozesse erzeugen eine gehärtete Oberflächenschicht, die weniger anfällig für Korrosion ist, wodurch die Komponente in rauen Umgebungen langlebiger wird. Dies ist besonders vorteilhaft für Teile, die korrosiven Substanzen ausgesetzt sind, wie sie beispielsweise in der chemischen Verarbeitung oder bei Schiffsanwendungen verwendet werden.
-
Kosteneffizienz:
- Oberflächenhärtung ist eine kostengünstige Lösung zur Verbesserung der Leistung von Metallkomponenten. Anstatt teure hochlegierte Materialien im gesamten Bauteil zu verwenden, ermöglicht die Oberflächenhärtung den Herstellern die Verwendung kostengünstigerer Basismaterialien bei gleichzeitiger Erzielung der gewünschten Oberflächeneigenschaften. Dies reduziert die Materialkosten und macht den Produktionsprozess wirtschaftlicher.
-
Vielseitigkeit in den Anwendungen:
- Oberflächenhärtungstechniken sind vielseitig und können auf eine Vielzahl von Materialien und Komponenten angewendet werden. Ganz gleich, ob es sich um ein kleines Präzisionsteil oder ein großes Industriebauteil handelt, die Oberflächenhärtung kann individuell auf die jeweiligen Anforderungen zugeschnitten werden. Diese Vielseitigkeit macht es zu einem wertvollen Prozess in verschiedenen Branchen, darunter Automobil, Luft- und Raumfahrt, Werkzeugherstellung und mehr.
-
Vorteile für die Umwelt:
- Durch die Verlängerung der Lebensdauer von Komponenten und die Reduzierung der Notwendigkeit eines häufigen Austauschs trägt die Oberflächenhärtung zur Umweltverträglichkeit bei. Weniger Austausch bedeutet weniger Materialverschwendung und einen geringeren Energieverbrauch bei der Herstellung neuer Teile. Darüber hinaus sind einige Oberflächenhärtungsverfahren, wie z Induktionshärten , sind energieeffizient und produzieren nur wenig Abfall, was ihren Nutzen für die Umwelt noch weiter erhöht.
Zusammenfassend lässt sich sagen, dass die Oberflächenhärtung ein wichtiger Prozess ist, der die Leistung, Haltbarkeit und Kosteneffizienz von Metallkomponenten verbessert. Durch die Verbesserung der Verschleißfestigkeit, Ermüdungsfestigkeit und Korrosionsbeständigkeit bei gleichzeitiger Beibehaltung der Kernzähigkeit stellt die Oberflächenhärtung sicher, dass Komponenten den anspruchsvollen Bedingungen moderner Industrieanwendungen standhalten. Seine Vielseitigkeit und Umweltvorteile machen es zu einer unverzichtbaren Technik in der Werkstofftechnik.
Übersichtstabelle:
Hauptvorteil | Beschreibung |
---|---|
Verbesserte Verschleißfestigkeit | Erhöht die Oberflächenhärte, reduziert den Verschleiß und verlängert die Lebensdauer der Komponenten. |
Verbesserte Ermüdungsfestigkeit | Führt Druckspannungen ein, um Ermüdungsrisse bei zyklischer Belastung zu verhindern. |
Behielt die Kernfestigkeit bei | Hält den Kern zäh und duktil und härtet gleichzeitig die Oberfläche. |
Korrosionsbeständigkeit | Bestimmte Techniken verbessern die Korrosionsbeständigkeit in rauen Umgebungen. |
Kosteneffizienz | Reduziert die Materialkosten durch die Verwendung kostengünstigerer Grundmaterialien. |
Vielseitigkeit in den Anwendungen | Anwendbar auf eine breite Palette von Materialien und Komponenten in allen Branchen. |
Vorteile für die Umwelt | Verlängert die Lebensdauer der Komponenten und reduziert Abfall und Energieverbrauch. |
Optimieren Sie Ihre Metallkomponenten durch Oberflächenhärtung – Kontaktieren Sie noch heute unsere Experten um mehr zu erfahren!