Das Sintern ist ein wichtiges Verfahren in der Materialwissenschaft und der Fertigung, mit dem pulverförmige Materialien in feste, zusammenhängende Strukturen umgewandelt werden, ohne dass der Schmelzpunkt des Materials erreicht wird.Dieser Prozess umfasst mehrere Stufen, darunter die Vorbereitung des Pulvers, die Verdichtung, die kontrollierte Erhitzung und die Abkühlung.Das Sintern ist ein weit verbreitetes Verfahren zur Herstellung von Bauteilen mit hoher Präzision, Härte und Zähigkeit, das sich ideal für die Herstellung komplexer Formen und Geometrien eignet, die mit herkömmlichen Fertigungsmethoden nur schwer zu erreichen sind.Das Verfahren ist außerdem kosteneffizient und ermöglicht eine schnelle Massenproduktion bei gleichbleibender Präzision und Wiederholbarkeit.Im Folgenden werden die wichtigsten Schritte und Vorteile des Sinterns erläutert.
Die wichtigsten Punkte erklärt:
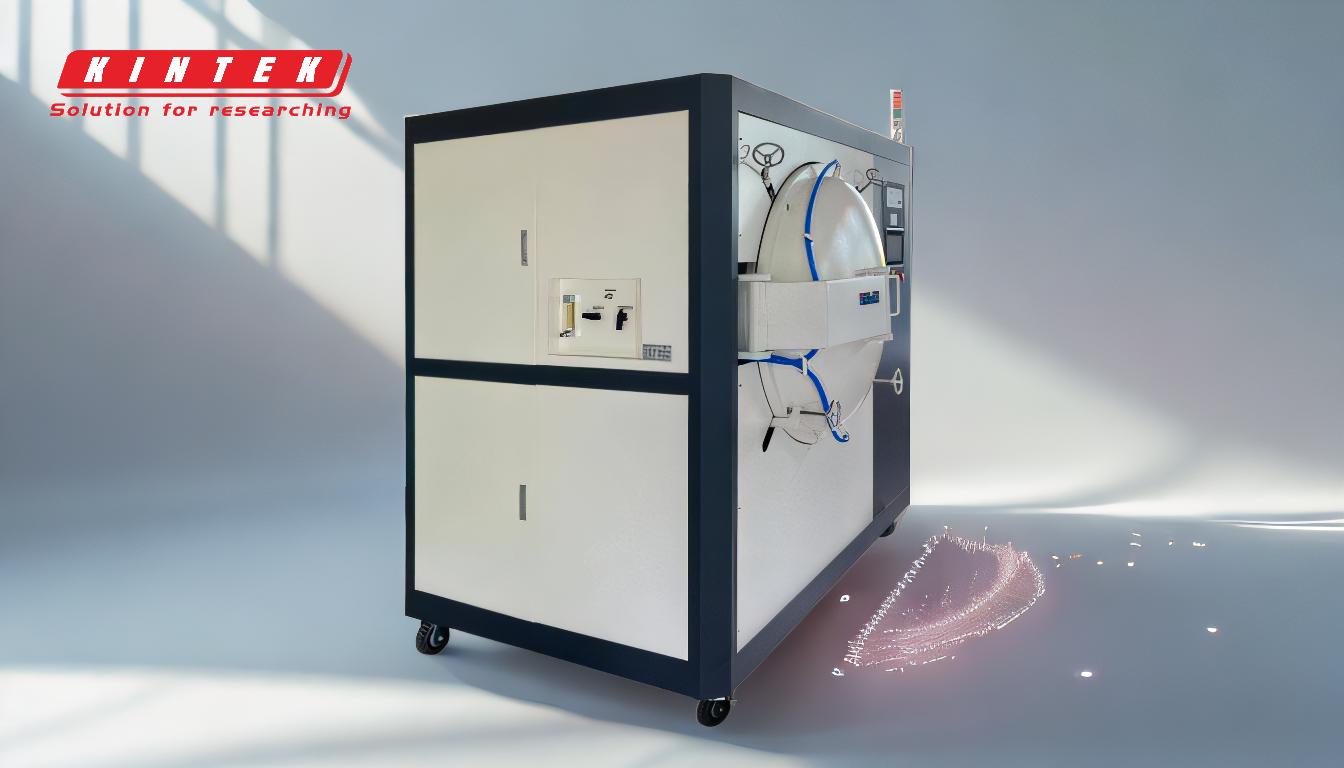
-
Vorbereitung des Kompaktpulvers
- Der Prozess beginnt mit der Vorbereitung von Rohstoffen, in der Regel in Pulverform.Das Pulver wird mit Bindemitteln wie Wasser, Wachs oder Polymeren gemischt, damit es zusammenhält.
- Das Pulver wird dann mit Methoden wie Kaltschweißen, Presswerkzeugen oder 3D-Laserdrucken verdichtet, um ein "grünes Teil" zu formen.Dieser Schritt gewährleistet Gleichmäßigkeit und eliminiert Hohlräume im Material.
-
Erhitzung und Konsolidierung
- Das verdichtete Pulver wird in einen Sinterofen gegeben, wo es auf eine Temperatur knapp unter seinem Schmelzpunkt erhitzt wird.Durch diese kontrollierte Erhitzung werden Diffusionsprozesse zwischen den Partikeln aktiviert, die zur Bildung von Einschnürungen und zur Verdichtung führen.
- In dieser Phase verdampft oder verbrennt das Bindemittel, und die Primärteilchen beginnen an ihren Oberflächen zu verschmelzen.In einigen Fällen schmelzen Zwischenbindemittel wie Bronze und verbinden sich zwischen den Partikeln, wobei das Primärmaterial unverändert bleibt.
-
Partikelverschmelzung und Verdichtung
- Mit steigender Temperatur kommt es zu einer Diffusion der Partikel, wodurch sie zusammenwachsen und sich verdichten.Diese Phase kann durch Techniken wie das Flüssigphasensintern (LPS) beschleunigt werden, bei dem sich eine flüssige Phase bildet und die Partikelbindung verbessert.
- Das Material geht von einer porösen Struktur in eine dichte, feste Masse über, die eine geringere Porosität und bessere mechanische Eigenschaften aufweist.
-
Abkühlung und Erstarrung
- Nach dem Erhitzen wird das Material allmählich abgekühlt.Durch diese Abkühlung verfestigt sich das gesinterte Produkt zu einer starren und kohäsiven Struktur.
- Das Endprodukt behält die gewünschte Form und weist verbesserte Eigenschaften wie Härte, Zähigkeit und Abriebfestigkeit auf.
-
Vorteile des Sinterns
- Komplexe Geometrien:Das Sintern ermöglicht die Herstellung komplizierter Formen und Geometrien, die mit herkömmlichen Fertigungsmethoden nur schwer zu erreichen sind.
- Materialeigenschaften:Es ermöglicht die Kombination mehrerer Materialien und vereint Eigenschaften wie Zähigkeit und Abriebfestigkeit.
- Kosten-Nutzen-Verhältnis:Das Sintern senkt die Werkzeugkosten und ermöglicht eine schnelle Massenproduktion bei gleichbleibender Präzision und Wiederholbarkeit.
- Materialien mit hohem Schmelzpunkt:Das Verfahren eignet sich besonders für Werkstoffe mit extrem hohen Schmelzpunkten, wie Wolfram und Molybdän, bei denen herkömmliche Schmelzverfahren unpraktisch sind.
-
Anwendungen des Sinterns
- Das Sintern ist in Branchen wie der Automobilindustrie, der Luft- und Raumfahrt und der Elektronik weit verbreitet, um Komponenten wie Zahnräder, Lager, Filter und Strukturteile herzustellen.
- Es wird auch bei der Herstellung von Keramik, Metallen und Verbundwerkstoffen eingesetzt, was es zu einer vielseitigen Fertigungstechnik macht.
Wenn die Hersteller den Sinterprozess verstehen, können sie seine Vorteile nutzen, um hochwertige, langlebige Komponenten effizient und kostengünstig herzustellen.Die Möglichkeit, komplexe Formen zu schaffen und Materialeigenschaften zu kombinieren, macht das Sintern zu einer unverzichtbaren Technik in der modernen Fertigung.
Zusammenfassende Tabelle:
Stufe | Beschreibung |
---|---|
Vorbereitung des Pulvers | Die Rohstoffe werden in Pulverform aufbereitet und mit Bindemitteln gemischt. |
Verdichtung | Das Pulver wird verdichtet, um ein "grünes Teil" zu bilden, das Gleichmäßigkeit gewährleistet und Hohlräume eliminiert. |
Erhitzung und Verfestigung | Das verdichtete Pulver wird unter den Schmelzpunkt erhitzt, wodurch Diffusion und Bindung aktiviert werden. |
Partikelverschmelzung | Die Partikel verschmelzen und verdichten sich und gehen von porösen in dichte feste Strukturen über. |
Abkühlung und Erstarrung | Durch allmähliches Abkühlen verfestigt sich das Material zu einem starren, kohäsiven Endprodukt. |
Vorteile | - Komplexe Geometrien |
- Verbesserte Materialeigenschaften
- Kostengünstige Massenproduktion
- Ideal für hochschmelzende Materialien | | Anwendungen
| Automobil, Luft- und Raumfahrt, Elektronik, Keramik, Metalle und Verbundwerkstoffe.| Entdecken Sie, wie das Sintern Ihren Fertigungsprozess revolutionieren kann. Kontaktieren Sie unsere Experten noch heute