Das Sintern ist ein wichtiges Verfahren in der Materialwissenschaft und der Fertigung, bei dem durch kontrolliertes Erhitzen und Abkühlen feste, dauerhafte Produkte aus pulverförmigen Materialien hergestellt werden.Es umfasst mehrere Stufen, darunter die Vorbereitung der Rohstoffe, die Verdichtung, die Erhitzung zur Förderung der Partikelbindung und die Abkühlung zur Verfestigung des Endprodukts.Dieses Verfahren gewährleistet die Bildung einer porenarmen, kohäsiven Struktur mit verbesserten mechanischen Eigenschaften.Im Folgenden werden die wichtigsten Schritte und Phasen des Sinterns im Detail erläutert, wobei der Schwerpunkt auf den chemischen Reaktionen und physikalischen Umwandlungen liegt, die während jeder Phase stattfinden.
Die wichtigsten Punkte werden erklärt:
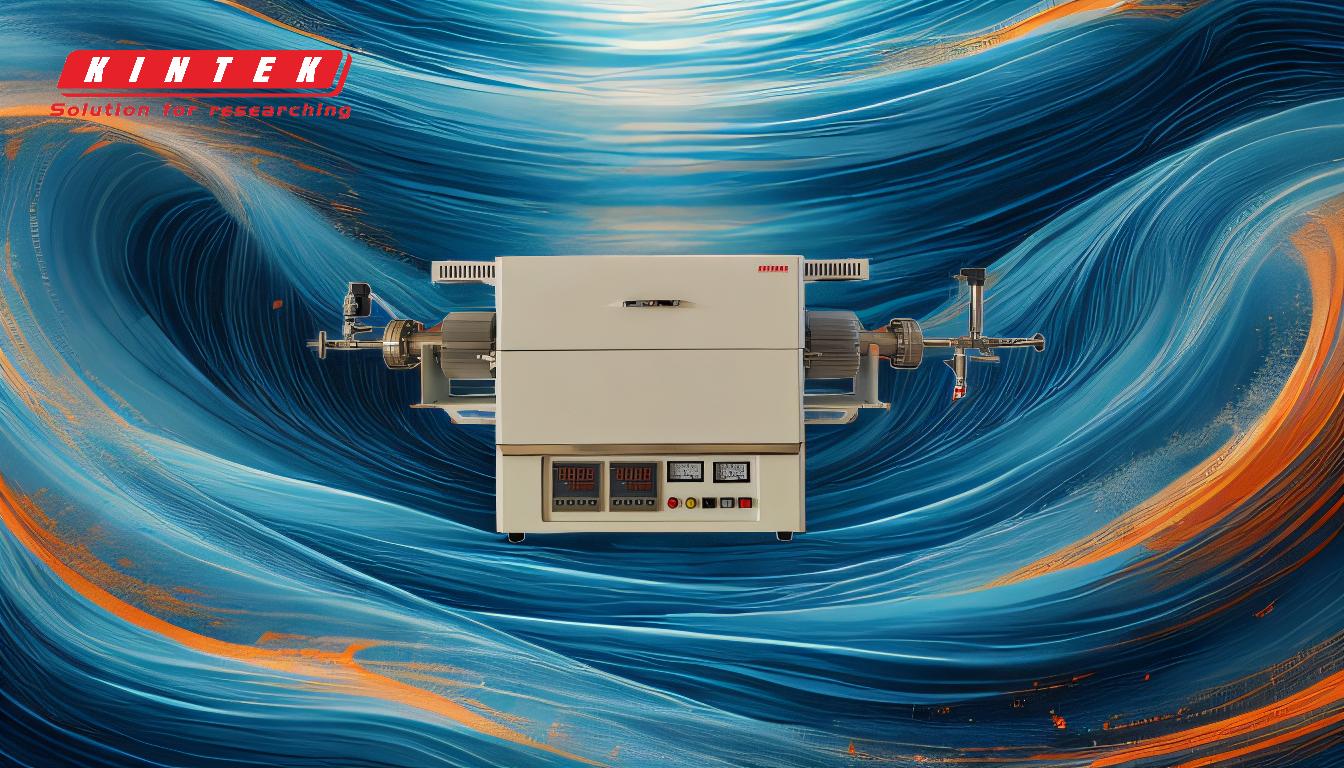
-
Aufbereitung von Rohstoffen
- Der Sinterprozess beginnt mit der Aufbereitung von Rohstoffen, die in der Regel in Pulverform vorliegen.
- Diese Pulver werden mit Zusatzstoffen wie Haftvermittlern, Bindemitteln oder Entflockungsmitteln gemischt, um die Einheitlichkeit zu verbessern und die Bindung zu erleichtern.
- Die Mischung wird häufig sprühgetrocknet, um eine Aufschlämmung zu erzeugen, die dann in die gewünschte Form gebracht wird.
- Chemische Reaktionen:In dieser Phase finden keine nennenswerten chemischen Reaktionen statt, aber die Gleichmäßigkeit der Mischung ist entscheidend für die spätere gleichmäßige Sinterung.
-
Verdichtung (Powder Compacting)
- Das gemischte Pulver wird mit mechanischem Druck verdichtet, z. B. durch Kalt- oder Warmformpressen, um ein "Grünteil" zu bilden.
- Durch die Verdichtung werden Hohlräume beseitigt und eine gleichmäßige Dichte des Materials gewährleistet, die für ein stabiles Endprodukt unerlässlich ist.
- Chemische Reaktionen:In diesem Stadium können die Partikel kalte Schweißnähte bilden, aber es treten keine größeren chemischen Veränderungen auf.
-
Erhitzen (Sintern oder Brennen)
- Das Rohteil wird in einer kontrollierten Umgebung, in der Regel in einem Sinterofen oder Brennofen, auf eine Temperatur knapp unter dem Schmelzpunkt des Materials erhitzt.
-
Während des Erhitzens kommt es zur Diffusion der Partikel, was zur Bildung von Einschnürungen und zur Verdichtung führt.Hier finden die wichtigsten chemischen Reaktionen und physikalischen Umwandlungen statt.
- Bildung des Halses:Die Partikel verbinden sich an ihren Berührungspunkten und bilden Hälse, die wachsen, wenn Atome über die Partikeloberflächen diffundieren.
- Verdichtung:Die Hohlräume zwischen den Partikeln schrumpfen, und das Material wird dichter und fester.
- Flüssigphasensintern (LPS):In einigen Fällen kann sich eine flüssige Phase bilden, um die Verschmelzung und Verdichtung der Partikel zu beschleunigen.
- Chemische Reaktionen:Je nach Material kann es zu Oxidation, Reduktion oder Phasenumwandlungen kommen.Beim Sintern von Keramik zum Beispiel kann sich das Bindemittel zersetzen und die Keramikpartikel können verschmelzen.
-
Abkühlung und Erstarrung
- Nach dem Sintern wird das Material allmählich abgekühlt, damit es zu einer festen, kohäsiven Struktur erstarren kann.
- Die kontrollierte Abkühlung verhindert thermische Spannungen und gewährleistet, dass das Material seine gewünschten Eigenschaften beibehält.
- Chemische Reaktionen:Während der Abkühlung kommt es zu keinen nennenswerten chemischen Reaktionen, aber das Gefüge des Materials stabilisiert sich.
-
Behandlung nach dem Sintern
- In einigen Fällen können zusätzliche Behandlungen wie Bearbeitung, Polieren oder Beschichtung durchgeführt werden, um die Spezifikationen des Endprodukts zu erreichen.
- Chemische Reaktionen:Die Behandlungen nach dem Sintern sind in erster Linie mechanisch oder auf der Oberfläche und beinhalten keine wesentlichen chemischen Veränderungen.
Bedeutung der kontrollierten Parameter:
- Temperatur:Die genaue Kontrolle der Temperatur ist entscheidend, um eine ordnungsgemäße Partikelbindung ohne vollständiges Schmelzen zu gewährleisten.
- Atmosphäre:Die Sinterumgebung (z. B. Vakuum, Inertgas oder reduzierende Atmosphäre) kann die chemischen Reaktionen und die endgültigen Eigenschaften des Materials beeinflussen.
- Zeit:Die Dauer der Erwärmung und Abkühlung beeinflusst das Ausmaß der Verdichtung und der Mikrostrukturentwicklung.
Anwendungen des Sinterns:
- Metalle:Zur Herstellung von Bauteilen mit hoher Festigkeit und Verschleißfestigkeit, z. B. Zahnräder und Lager.
- Keramiken:Zur Herstellung haltbarer, hitzebeständiger Produkte wie Fliesen und Dämmstoffe.
- Verbundwerkstoffe:Beim Sintern werden verschiedene Materialien wie Metalle und Keramiken miteinander kombiniert, um einzigartige Eigenschaften zu erzielen.
Wenn die Hersteller den Sinterprozess und seine Phasen verstehen, können sie die Herstellung hochwertiger Materialien mit maßgeschneiderten Eigenschaften für bestimmte Anwendungen optimieren.
Zusammenfassende Tabelle:
Stufe | Wichtige Aktionen | Chemische Reaktionen |
---|---|---|
Aufbereitung von Rohstoffen | Mischen von Pulvern mit Zusatzstoffen, Sprühtrocknung zu einem Schlamm, Formgebung. | Keine nennenswerten Reaktionen; Gleichmäßigkeit ist entscheidend. |
Verdichtung | Kalt- oder Warmformpressen zur Herstellung eines "grünen Teils". | Es können sich kalte Schweißnähte bilden; keine größeren chemischen Veränderungen. |
Erhitzen (Sintern) | Erhitzen bis knapp unter den Schmelzpunkt; Halsbildung, Verdichtung, LPS. | Oxidation, Reduktion oder Phasenumwandlung (z. B. Bindemittelzersetzung, Partikelschmelze). |
Abkühlung | Allmähliche Abkühlung zur Verfestigung des Materials. | Keine nennenswerten Reaktionen; das Gefüge stabilisiert sich. |
Behandlung nach der Sinterung | Bearbeitung, Polieren oder Beschichtung für die endgültigen Spezifikationen. | Hauptsächlich mechanische oder oberflächliche Bearbeitung; keine wesentlichen chemischen Veränderungen. |
Optimieren Sie Ihren Sinterprozess für hochwertige Materialien. Kontaktieren Sie noch heute unsere Experten !