Das traditionelle Sinterverfahren ist eine thermische Behandlungsmethode, mit der Materialien wie Zirkoniumdioxid zu einer festen Masse verschmolzen werden, ohne sie zu schmelzen.Bei diesem Verfahren wird das Material auf eine hohe Temperatur erhitzt, so dass sich die Partikel durch Verdichtung und intergranulares Halswachstum verbinden können, was die Porosität verringert und die Dichte erhöht.Das Ergebnis ist ein festes, dichtes Endprodukt mit verbesserten mechanischen Eigenschaften.A Sinterofen für Zirkoniumdioxid ist für diesen Prozess unerlässlich, da er eine präzise Temperaturkontrolle, eine gleichmäßige Wärmeverteilung und eine effiziente Luftzirkulation gewährleistet, um die gewünschten Eigenschaften des gesinterten Zirkoniums zu erreichen.Der Prozess umfasst in der Regel Erhitzungs-, Sinter- und Abkühlungsphasen, um sicherzustellen, dass das Material seine endgültige Härte und strukturelle Integrität erreicht.
Die wichtigsten Punkte erklärt:
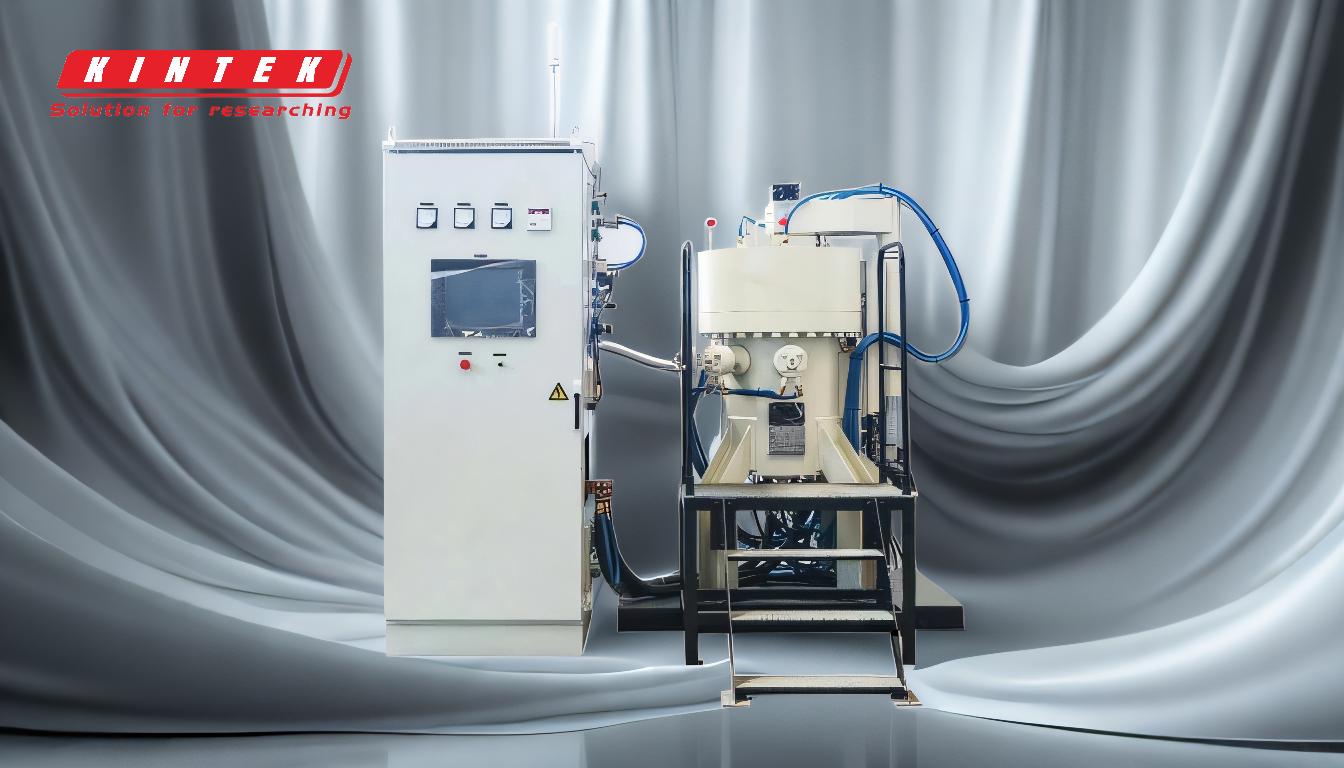
-
Definition des traditionellen Sinterns:
- Beim traditionellen Sintern werden Werkstoffe wie Zirkoniumdioxid durch Wärmeeinwirkung miteinander verschmolzen, ohne dabei einen flüssigen Zustand zu erreichen.Dieses Verfahren beruht auf einer thermischen Behandlung und manchmal auch auf Druckbeaufschlagung, um eine Verdichtung und intergranuläre Einschnürung zu erreichen, wodurch die strukturelle Integrität des Endprodukts verbessert wird.
-
Phasen des Sinterprozesses:
- Heizphase:Das Material wird allmählich auf eine hohe Temperatur erhitzt, wodurch die Wärme von der Oberfläche auf den Kern übertragen wird.
- Phase des Sinterns:Bei der Zieltemperatur verbinden sich die Partikel durch Verdichtung und intergranuläres Halswachstum, wodurch die Porosität verringert und die Dichte erhöht wird.
- Abkühlungsphase:Das Material wird langsam auf Raumtemperatur abgekühlt, so dass es seine Festigkeit und Dichte behält.
-
Die Rolle eines Zirkoniumdioxid-Sinterofens:
-
A
Sinterofen für Zirkoniumdioxid
ist speziell für den Sinterprozess von Zirkoniumdioxid ausgelegt.Die wichtigsten Merkmale sind:
- Hochpräzise Temperaturregelung (z. B. intelligentes PID-Temperaturregelsystem mit ±1℃ Genauigkeit).
- Moderne Heizelemente für eine gleichmäßige Wärmeverteilung.
- Effiziente Luftzirkulation zur Aufrechterhaltung eines optimalen Sauerstoffgehalts und zur Erzielung der gewünschten Farbe und Oberflächenbeschaffenheit.
-
A
Sinterofen für Zirkoniumdioxid
ist speziell für den Sinterprozess von Zirkoniumdioxid ausgelegt.Die wichtigsten Merkmale sind:
-
Vorteile des Sinterns von Zirkoniumdioxid:
- Verbesserte mechanische Festigkeit:Das Sintern verringert die Porosität und erhöht die Dichte, was zu einem Endprodukt mit überlegener Härte und Haltbarkeit führt.
- Verbesserte Oberflächengüte:Das Verfahren gewährleistet eine glatte und gleichmäßige Oberfläche, was für Anwendungen wie Zahnersatz von entscheidender Bedeutung ist.
- Wirkungsgrad:Moderne Sinteröfen, wie die für Zirkoniumdioxid, können den Prozess in nur 65 Minuten abschließen, einschließlich der Heiz-, Sinter- und Kühlphasen.
-
Fortschrittliche Merkmale moderner Sinteröfen:
- Schnelle Sinter-Programme:Einige Öfen bieten schnelle Sinterzyklen, die die Produktionszeit verkürzen.
- Hohe Kapazität:Die Öfen können mehrere Schichten von Tiegeln stapeln, so dass in einem einzigen Zyklus bis zu 150 Einheiten gesintert werden können.
- Umwelt- und Sicherheitsmerkmale:Verwendung umweltfreundlicher, schadstofffreier Materialien und Speicherfunktionen, die den Betrieb nach einer Stromunterbrechung wieder aufnehmen.
-
Anwendungen von gesintertem Zirkoniumdioxid:
- Gesintertes Zirkoniumdioxid ist in Branchen wie der Zahnmedizin weit verbreitet, wo seine Festigkeit, Haltbarkeit und ästhetischen Eigenschaften sehr geschätzt werden.Der Sinterprozess stellt sicher, dass Zirkoniumdioxid-Restaurationen die erforderlichen Standards für Passform, Funktion und Aussehen erfüllen.
Durch das Verständnis des traditionellen Sinterprozesses und der Rolle moderner Geräte wie dem Sinterofen für Zirkoniumdioxid können die Hersteller hochwertige Zirkoniumdioxidprodukte mit gleichbleibenden Eigenschaften und Leistungen herstellen.
Zusammenfassende Tabelle:
Aspekt | Einzelheiten |
---|---|
Definition | Verschmilzt Materialien wie Zirkoniumdioxid zu einer festen Masse, ohne zu schmelzen, und verbessert so die strukturelle Integrität. |
Phasen | Erhitzungs-, Sinter- und Abkühlphasen, um Festigkeit und Dichte zu gewährleisten. |
Wichtigste Ausrüstung | Zirkoniumdioxid-Sinterofen mit präziser Temperaturregelung und gleichmäßiger Wärmeverteilung. |
Vorteile | Verbesserte mechanische Festigkeit, verbesserte Oberflächengüte und hohe Effizienz. |
Anwendungen | Weit verbreitet in der Zahnmedizin für dauerhafte und ästhetisch ansprechende Zirkoniumdioxid-Restaurationen. |
Sind Sie bereit, Ihren Sinterprozess zu optimieren? Kontaktieren Sie uns noch heute um mehr über unsere fortschrittlichen Zirkoniumdioxid-Sinteröfen zu erfahren!