Das Vapor-Transport-Deposition-Verfahren (VTD) ist ein spezielles Verfahren zur Abscheidung dünner Filme oder Beschichtungen auf Substraten, in der Regel in einer Vakuumumgebung.Dabei werden verdampfte Materialien (entweder durch physikalische oder chemische Mittel) auf ein Substrat transportiert, wo sie kondensieren und eine dünne, gleichmäßige Schicht bilden.Dieses Verfahren ist in Branchen wie der Halbleiterindustrie, der Optik und der Energiespeicherung aufgrund seiner Präzision und seiner Fähigkeit zur Herstellung hochwertiger Schichten weit verbreitet.VTD kann in physikalische Gasphasenabscheidung (PVD) und chemische Gasphasenabscheidung (CVD) unterteilt werden, die jeweils unterschiedliche Mechanismen und Anwendungen haben.PVD beruht auf physikalischen Verfahren wie Verdampfung oder Sputtern, während CVD chemische Reaktionen zur Bildung der gewünschten Schicht beinhaltet.Beide Verfahren erfordern kontrollierte Umgebungen, präzise Temperatur- und Druckbedingungen und spezielle Geräte, um optimale Ergebnisse zu erzielen.
Die wichtigsten Punkte werden erklärt:
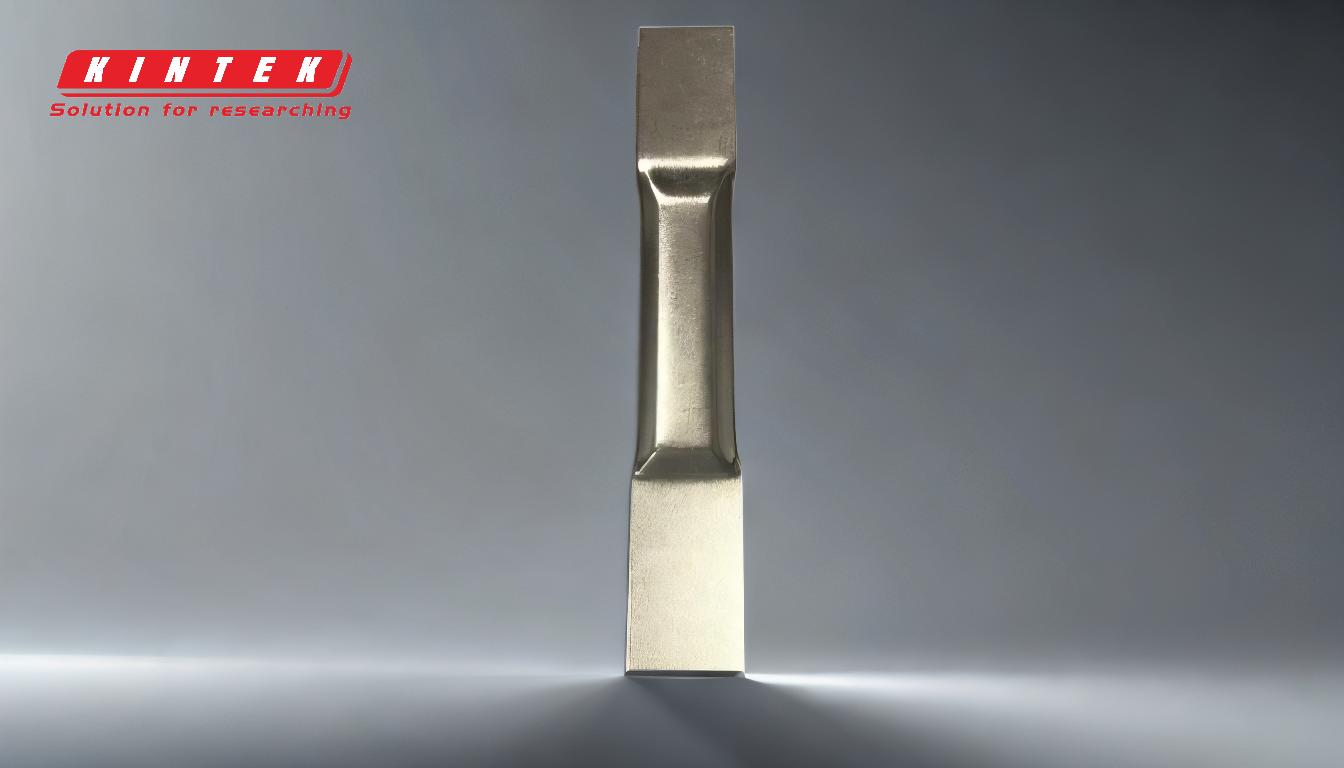
-
Definition und Zweck der Dampftransportabscheidung (VTD):
- VTD ist ein Verfahren zur Abscheidung dünner Filme oder Schichten auf Substraten in einer kontrollierten Umgebung.
- Es ist in Branchen wie der Halbleiterindustrie, der Optik und der Energiespeicherung weit verbreitet, um präzise, hochwertige Beschichtungen herzustellen.
-
Arten der Dampftransportabscheidung:
- Physikalische Gasphasenabscheidung (PVD): Physikalische Verfahren wie Verdampfen oder Sputtern, um das verdampfte Material auf das Substrat zu übertragen.Beispiele sind die thermische Verdampfung und das Magnetron-Sputtern.
- Chemische Gasphasenabscheidung (CVD): Basiert auf chemischen Reaktionen zwischen gasförmigen Vorläufern, um eine dünne Schicht auf dem Substrat zu bilden.Beispiele sind Niederdruck-CVD (LPCVD) und plasmaunterstütztes CVD (PECVD).
-
Die wichtigsten Schritte im VTD-Prozess:
- Schaffung einer Vakuumumgebung: Eine Vakuumkammer wird verwendet, um Luft und Gase zu eliminieren, die den Abscheidungsprozess stören könnten.
- Vorbereitung des Substrats: Das Substrat wird gereinigt oder behandelt, um eine gute Haftung des aufgebrachten Materials zu gewährleisten.
- Verdampfung des Materials: Bei der PVD wird das Material durch Erhitzen oder Sputtern verdampft.Bei der CVD werden gasförmige Ausgangsstoffe in die Kammer eingeleitet.
- Transport und Abscheidung: Das verdampfte Material oder die reaktiven Gase werden zum Substrat transportiert, wo sie kondensieren oder reagieren und einen dünnen Film bilden.
- Kühlung und Entlüftung: Nach der Abscheidung wird die Kammer gekühlt und entlüftet, damit das beschichtete Substrat entfernt werden kann.
-
Mechanismen der VTD:
- Physikalische Prozesse (PVD): Bei diesen Verfahren wird das Zielmaterial mit Hilfe von hochenergetischen Ionen oder Plasma verdampft, das sich dann auf dem Substrat niederschlägt.
- Chemische Verfahren (CVD): Chemische Reaktionen zwischen Vorläufern, die oft durch Hitze oder Plasma aktiviert werden, um die gewünschte Schicht auf dem Substrat zu bilden.
-
Anwendungen der VTD:
- Halbleiter: Zur Abscheidung dünner Schichten für integrierte Schaltungen und elektronische Geräte.
- Optik: Anwendung bei der Herstellung von Antireflexionsbeschichtungen und optischen Filtern.
- Energiespeicherung: Zur Herstellung von Beschichtungen für Batteriematerialien, wie z. B. die Kohlenstoffbeschichtung von LiFePO4 zur Verbesserung der Leistung.
-
Vorteile der VTD:
- Erzeugt hochwertige, gleichmäßige dünne Schichten mit präziser Kontrolle über Dicke und Zusammensetzung.
- Geeignet für eine Vielzahl von Materialien, darunter Metalle, Keramiken und Polymere.
- In einigen Fällen umweltfreundlich, z. B. bei der CVD mit festen Ausgangsstoffen wie Glukose.
-
Herausforderungen und Beschränkungen:
- Erfordert anspruchsvolle Ausrüstung und kontrollierte Umgebungen, was zu höheren Kosten führt.
- Längere Produktionszeiten, insbesondere bei CVD, aufgrund geringerer Zersetzungsraten der Ausgangsstoffe.
- Begrenzte Skalierbarkeit für die großtechnische Produktion im Vergleich zu anderen Beschichtungsmethoden.
-
Schlüsselfaktoren, die die VTD beeinflussen:
- Kammerdruck: Ein niedriger Druck ist häufig erforderlich, um einen ordnungsgemäßen Transport und die Ablagerung von Materialien zu gewährleisten.
- Temperatur des Substrats: Entscheidend für die Kontrolle der Abscheidungsgeschwindigkeit und der Qualität des Films.
- Vorläufermaterialien: Die Wahl der Vorläuferstoffe bei der CVD beeinflusst die chemischen Reaktionen und die Eigenschaften der fertigen Schicht.
Wenn ein Käufer von Geräten oder Verbrauchsmaterialien diese Schlüsselpunkte versteht, kann er fundierte Entscheidungen über die Eignung von VTD für seine spezifischen Anwendungen treffen und dabei Faktoren wie Materialanforderungen, gewünschte Filmeigenschaften und Produktionsumfang berücksichtigen.
Zusammenfassende Tabelle:
Aspekt | Einzelheiten |
---|---|
Arten von VTD | Physikalische Gasphasenabscheidung (PVD), Chemische Gasphasenabscheidung (CVD) |
Wichtige Schritte | Vakuumerzeugung, Substratvorbereitung, Verdampfung, Transport, Abscheidung |
Anwendungen | Halbleiter, Optik, Energiespeicherung |
Vorteile | Hochwertige Folien, präzise Kontrolle, Materialvielfalt |
Herausforderungen | Hohe Kosten, längere Produktionszeiten, begrenzte Skalierbarkeit |
Schlüsselfaktoren | Kammerdruck, Substrattemperatur, Vorläufermaterialien |
Entdecken Sie, wie VTD Ihren Produktionsprozess verbessern kann. Kontaktieren Sie unsere Experten noch heute !