Die Dünnschichtabscheidung im Vakuum ist ein spezielles Verfahren zum Aufbringen ultradünner Materialschichten auf ein Substrat in einer kontrollierten Vakuumumgebung.Diese Technik ist in Branchen wie der Halbleiter-, Optik- und Beschichtungsindustrie, in denen präzise Materialeigenschaften erforderlich sind, von entscheidender Bedeutung.Die Vakuumumgebung gewährleistet eine minimale Verunreinigung und ermöglicht die Abscheidung hochreiner Schichten.Die Abscheidung von Dünnschichten kann durch physikalische oder chemische Verfahren erfolgen, die je nach den gewünschten Schichteigenschaften und der Anwendung einzigartige Vorteile bieten.Das Verfahren verbessert die Leistung des Substrats durch Veränderung von Eigenschaften wie Leitfähigkeit, Verschleißfestigkeit, Korrosionsbeständigkeit und optische Eigenschaften.
Die wichtigsten Punkte werden erklärt:
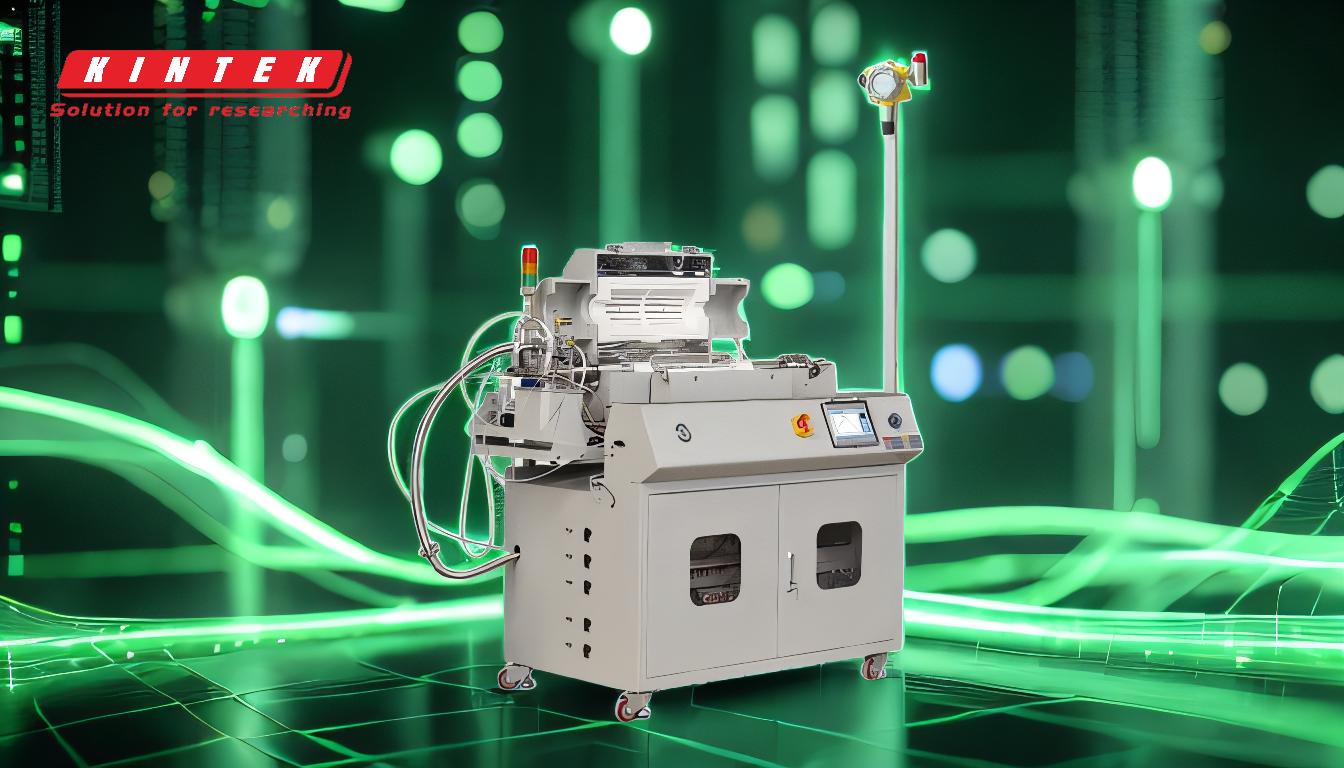
-
Definition und Zweck der Dünnschichtabscheidung im Vakuum:
- Bei der Dünnschichtabscheidung im Vakuum wird eine dünne Materialschicht (im Bereich von Nanometern bis Mikrometern) in einer Vakuumkammer auf ein Substrat aufgebracht.
- Der Hauptzweck besteht darin, die Oberflächeneigenschaften des Substrats zu verändern oder zu verbessern, wie z. B. Leitfähigkeit, Härte, Korrosionsbeständigkeit und optische oder elektrische Leistung.
- Die Vakuumumgebung ist von entscheidender Bedeutung, da sie die Verunreinigung durch Luft oder andere Gase minimiert und somit hochreine und hochwertige Schichten gewährleistet.
-
Arten der Dünnschichtabscheidung:
-
Physikalische Ablagerung:
- Mechanische, elektromechanische oder thermodynamische Verfahren zur Abscheidung von Materialien.
-
Zu den gängigen Techniken gehören:
- Thermische Verdampfung:Das Material wird in einem Vakuum bis zu seinem Verdampfungspunkt erhitzt, und der Dampf kondensiert auf dem Substrat.
- Sputtern:Ein Zielmaterial wird mit Ionen beschossen, wodurch Atome herausgeschleudert werden und sich auf dem Substrat ablagern.
- Ionenstrahlabscheidung:Ein fokussierter Ionenstrahl wird verwendet, um Material auf das Substrat zu sputtern.
-
Chemische Abscheidung:
- Chemische Reaktionen zur Abscheidung dünner Schichten.
-
Zu den gängigen Techniken gehören:
- Chemische Gasphasenabscheidung (CVD):An der Substratoberfläche findet eine chemische Reaktion in der Gasphase statt, die einen festen Film bildet.
- Atomlagenabscheidung (ALD):Ein sequenzielles, selbstbegrenzendes chemisches Verfahren sorgt für die Abscheidung einer Atomschicht nach der anderen und ermöglicht eine präzise Kontrolle.
-
Physikalische Ablagerung:
-
Schlüsselanwendungen der Dünnschichtabscheidung:
- Halbleiter:Wird zur Herstellung von leitenden, isolierenden oder halbleitenden Schichten in der Mikroelektronik verwendet.
- Optik:Verbessert die optischen Eigenschaften von Glas, wie z. B. Antireflexionsbeschichtungen oder Spiegeln.
- Korrosionsschutz:Ablagerung von Schutzschichten auf Metallen zur Verbesserung der Haltbarkeit.
- Abriebfestigkeit:Fügt Werkzeugen oder Bauteilen harte Beschichtungen hinzu, um ihre Lebensdauer zu verlängern.
- Energie:Einsatz in Solarzellen und Batterien zur Verbesserung der Effizienz und Leistung.
-
Vorteile der Dünnschichtabscheidung im Vakuum:
- Hohe Reinheit:Die Vakuumumgebung verhindert Verunreinigungen, was zu qualitativ hochwertigen Filmen führt.
- Präzise Kontrolle:Ermöglicht eine präzise Kontrolle der Dicke und Zusammensetzung, was für fortschrittliche Anwendungen entscheidend ist.
- Vielseitigkeit:Kann eine breite Palette von Materialien abscheiden, darunter Metalle, Oxide und Verbindungen.
- Verbesserte Eigenschaften:Verbessert die Leistung des Substrats durch Hinzufügen funktioneller Schichten mit maßgeschneiderten Eigenschaften.
-
Herausforderungen und Überlegungen:
- Kosten:Vakuumbeschichtungsanlagen und -verfahren können teuer sein.
- Komplexität:Erfordert spezielle Kenntnisse und Ausrüstung, um die gewünschten Ergebnisse zu erzielen.
- Skalierbarkeit:Einige Methoden sind möglicherweise nur begrenzt für die Produktion in großem Maßstab geeignet.
- Beschränkungen des Materials:Nicht alle Materialien eignen sich aufgrund ihrer Verdampfungs- oder Reaktionseigenschaften für die Vakuumabscheidung.
-
Vergleich von Abscheidungstechniken:
-
Thermische Verdampfung:
- Vorteile:Einfach, kostengünstig, hohe Abscheidungsraten.
- Nachteile: Begrenzt auf Materialien mit niedrigem Schmelzpunkt, weniger präzise.
-
Sputtern:
- Vorteile:Funktioniert mit einer breiten Palette von Materialien, gute Haftung.
- Nachteile: Langsamere Abscheidungsraten, komplexere Ausrüstung.
-
CVD:
- Vorteile:Hochwertige Filme, gute Stufenabdeckung für komplexe Geometrien.
- Nachteile: Erfordert hohe Temperaturen, kann gefährliche Nebenprodukte erzeugen.
-
ALD:
- Vorteile:Präzision auf atomarer Ebene, hervorragende Gleichmäßigkeit.
- Nachteile: Langsame Abscheidungsraten, begrenzte Materialoptionen.
-
Thermische Verdampfung:
-
Zukünftige Trends in der Dünnschichtabscheidung:
- Nanotechnologie:Zunehmende Verwendung dünner Schichten in nanoskaligen Geräten und Anwendungen.
- Grüne Technologien:Entwicklung von umweltfreundlichen Abscheidungsmethoden und Materialien.
- Automatisierung:Integration von KI und Automatisierung zur Verbesserung der Prozesssteuerung und Effizienz.
- Hybride Techniken:Kombination physikalischer und chemischer Verfahren zur Verbesserung der Schichteigenschaften.
Zusammenfassend lässt sich sagen, dass die Dünnschichtabscheidung im Vakuum ein vielseitiges und präzises Verfahren ist, mit dem funktionelle Beschichtungen auf Substrate aufgebracht werden können, um deren Leistung für eine Vielzahl von Anwendungen zu verbessern.Es bietet zwar erhebliche Vorteile in Bezug auf Reinheit und Kontrolle, birgt aber auch Herausforderungen, die einer sorgfältigen Prüfung bedürfen.Im Zuge des technologischen Fortschritts wird die Dünnschichtabscheidung in Branchen wie Elektronik, Optik und Energie voraussichtlich eine immer wichtigere Rolle spielen.
Zusammenfassende Tabelle:
Aspekt | Einzelheiten |
---|---|
Zweck | Verändert Substrateigenschaften wie Leitfähigkeit, Korrosionsbeständigkeit usw. |
Arten | Physikalisch (z. B. thermisches Verdampfen, Sputtern) und chemisch (z. B. CVD, ALD) |
Wichtigste Anwendungen | Halbleiter, Optik, Korrosionsschutz, Energie, Verschleißfestigkeit |
Vorteile | Hohe Reinheit, präzise Kontrolle, Vielseitigkeit, verbesserte Eigenschaften |
Herausforderungen | Hohe Kosten, Komplexität, Skalierbarkeitsprobleme, Materialbeschränkungen |
Erfahren Sie, wie die Dünnschichtabscheidung Ihre Anwendungen optimieren kann. Kontaktieren Sie unsere Experten noch heute !