Die Sputterbeschichtung ist ein Verfahren zur Abscheidung von Dünnschichten, das unter Niederdruckbedingungen, in der Regel in einer Vakuumkammer, stattfindet.Bei diesem Verfahren wird ein Plasma verwendet, das durch die Ionisierung eines Gases, in der Regel Argon, bei einem Druck von 1 bis 15 Millitorr (mTorr) erzeugt wird.Diese Niederdruckumgebung ist von entscheidender Bedeutung, da sie es den Argon-Ionen ermöglicht, zu beschleunigen und mit dem Zielmaterial zu kollidieren, wodurch Atome herausgeschleudert werden und sich auf einem Substrat ablagern.Der Druck wird sorgfältig kontrolliert, um eine effiziente Ionisierung und eine gleichmäßige Beschichtung zu gewährleisten.Üblich sind Techniken wie Magnetronsputtern, HF-Sputtern und Gleichstromsputtern, die jeweils spezifische Druckbedingungen zur Optimierung des Beschichtungsprozesses erfordern.Die Sputterbeschichtung ist in Anwendungen wie der Halbleiterherstellung, optischen Beschichtungen und der Probenvorbereitung für die Elektronenmikroskopie weit verbreitet.
Die wichtigsten Punkte erklärt:
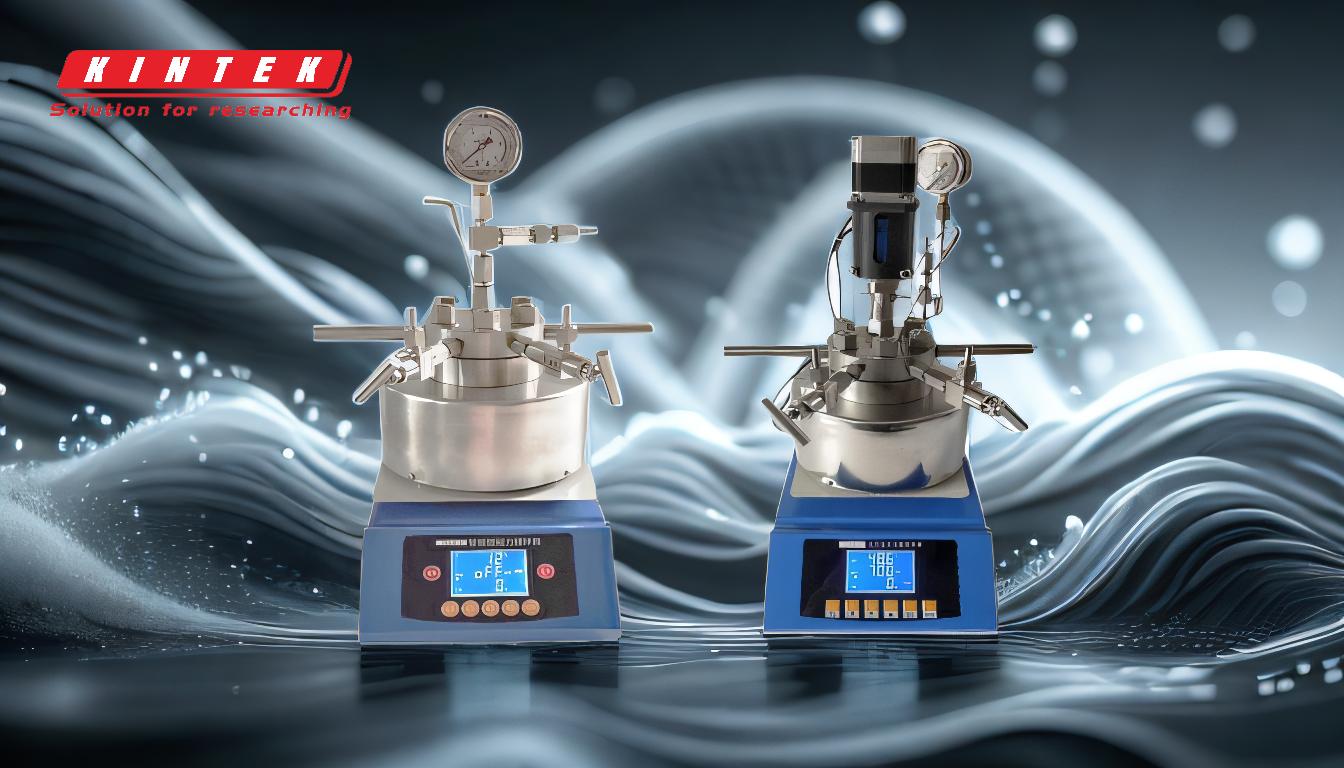
-
Niederdruck-Umgebung:
- Die Sputterbeschichtung erfolgt in einer Vakuumkammer, in der ein Druck von 1 bis 15 mTorr herrscht.Diese Niederdruckumgebung ist für die Ionisierung des Argongases und die Beschleunigung der Ionen auf das Zielmaterial unerlässlich.
- Das Vakuum sorgt für eine minimale Störung durch andere Gase und ermöglicht eine präzise Steuerung des Abscheidungsprozesses.
-
Ionisierung und Plasmabildung:
- Eine kleine Menge Argongas wird in die Vakuumkammer eingeleitet.Wenn eine Spannung (Gleichstrom, Hochfrequenz oder Mittelfrequenz) angelegt wird, wird das Argongas ionisiert und bildet ein Plasma.
- Das Plasma besteht aus freien Elektronen und positiv geladenen Argon-Ionen, die in Richtung des negativ geladenen Zielmaterials beschleunigt werden.
-
Erosion des Zielmaterials:
- Die beschleunigten Argon-Ionen stoßen mit dem Zielmaterial zusammen, wodurch Atome aus der Oberfläche herausgeschleudert werden (Sputtern).
- Die gesputterten Atome werden in die Gasphase geschleudert und wandern zum Substrat, wo sie sich ablagern und einen dünnen Film bilden.
-
Gleichmäßige Beschichtungsbildung:
- Die gesputterten Atome lagern sich auf allen Oberflächen innerhalb der Vakuumkammer ab, auch auf dem Substrat.Diese omnidirektionale Abscheidung führt zu einer einheitlichen und gleichmäßigen Beschichtung.
- Die Gleichmäßigkeit der Beschichtung ist entscheidend für Anwendungen wie die Elektronenmikroskopie, wo eine gleichmäßige Dicke erforderlich ist, um Aufladung zu verhindern und die Bildqualität zu verbessern.
-
Anwendungen der Sputter-Beschichtung:
- Halbleiterherstellung:Die Sputter-Beschichtung wird verwendet, um dünne Schichten aus Metallen und Dielektrika auf Silizium-Wafern aufzubringen.
- Optische Beschichtungen:Antireflexions- und hochemissive Schichten werden auf Glas und andere optische Komponenten aufgebracht.
- Elektronenmikroskopie:Die Sputterbeschichtung wird zur Vorbereitung von Proben verwendet, indem eine leitende Schicht, z. B. Gold, aufgebracht wird, um Aufladung zu verhindern und die Emission von Sekundärelektronen zu verbessern.
-
Techniken und Variationen:
- Magnetron-Sputtern:Nutzt Magnetfelder, um das Plasma in der Nähe des Targets einzuschließen, wodurch die Effizienz des Sputterprozesses erhöht wird.
- RF-Sputtern:Nutzt Hochfrequenzstrom zur Ionisierung des Gases, geeignet für isolierende Zielmaterialien.
- DC-Sputtern:Verwendet Gleichstrom, der in der Regel für leitfähige Zielmaterialien verwendet wird.
-
Druckkontrolle:
- Der Druck in der Vakuumkammer wird sorgfältig kontrolliert, um den Sputterprozess zu optimieren.Ein zu hoher Druck kann zu Kollisionen zwischen Gasmolekülen führen, wodurch die Energie der Ionen verringert wird.Ein zu niedriger Druck kann zu einer unzureichenden Ionisierung und schlechten Abscheidungsraten führen.
-
Vorteile der Sputter-Beschichtung:
- Präzision:Ermöglicht die Abscheidung von dünnen Schichten mit präziser Dicke und Zusammensetzung.
- Gleichmäßigkeit:Gewährleistet eine gleichmäßige Beschichtung über komplexe Geometrien und große Flächen.
- Vielseitigkeit:Geeignet für eine breite Palette von Materialien, darunter Metalle, Legierungen und Keramik.
Durch die Aufrechterhaltung des richtigen Drucks und den Einsatz fortschrittlicher Sputtertechniken bietet die Sputterbeschichtung eine zuverlässige und effiziente Methode zur Abscheidung hochwertiger Dünnschichten für verschiedene industrielle und wissenschaftliche Anwendungen.
Zusammenfassende Tabelle:
Hauptaspekt | Einzelheiten |
---|---|
Druckbereich | 1 bis 15 mTorr |
Zweck des Niederdrucks | Sorgt für effiziente Ionisierung und gleichmäßige Beschichtung |
Gängige Techniken | Magnetron-, RF- und DC-Sputtern |
Anwendungen | Halbleiterherstellung, optische Beschichtungen, Elektronenmikroskopie |
Vorteile | Präzision, Gleichmäßigkeit und Vielseitigkeit bei der Dünnschichtabscheidung |
Entdecken Sie, wie die Sputterbeschichtung Ihren Prozess verbessern kann. Kontaktieren Sie unsere Experten noch heute für maßgeschneiderte Lösungen!